Entrevista a Clemente Cárdenas, investigador del proyecto Revamp en el centro de investigación Cartif
Para situarnos, ¿pueden explicaros en qué consiste el proyecto Revamp exactamente?
El objetivo principal del proyecto es desarrollar, adaptar y aplicar nuevas tecnologías para mejorar la eficiencia en el uso de materias primas y energía de los equipos y procesos que tienen lugar en las empresas metalúrgicas. La gran variabilidad de la materia prima en este tipo de empresas hace que sus procesos sean especialmente complejos y necesiten ser modernizados.
Las nuevas tecnologías están relacionadas con la implantación de nuevos sensores para una mejor caracterización de la materia prima, la mejora de la monitorización y control de los procesos y el uso de nuevos combustibles a partir de residuos, permitirán optimizan los procesos de carga y fusión en los hornos de fundición en los diferentes casos de uso.
Estas tecnologías serán validadas en tres casos de uso que van desde la producción de acero hasta el refino de aluminio y el reciclado del plomo.
El proyecto está financiado por el programa europeo Horizonte 2020 y liderado por el Centro Alemán de Tecnología BFI, participando 16 socios de tres países diferentes.
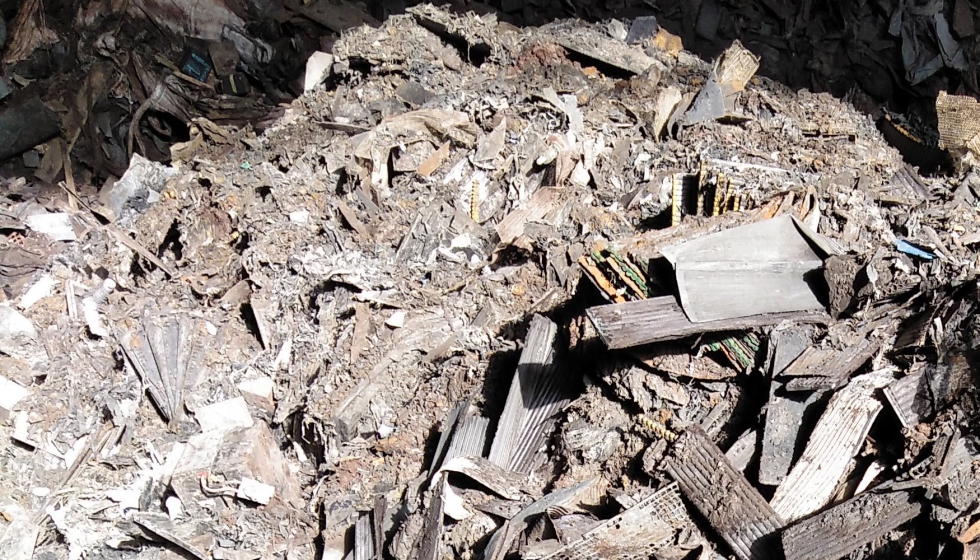
¿La procedencia de las materias primas es una de las preocupaciones en la industria de fabricación de metal?
Es evidente que el origen de la materia prima es importante para este tipo de industrias ya que si existe una gran variabilidad de materia prima tiene como consecuencia que los procesos no siempre se realicen de la misma forma y haya que estar haciendo ajustes en los sistemas de producción. Esto requiere un mayor control de la materia prima y una planificación continua de la producción con el aumento de los costes de producción.
Habitualmente ¿de dónde proceden estas materias?
La materia prima básica procede principalmente de chatarras metálicas que son suministradas por proveedores externos. Su importancia hace que en este tipo de empresas se centren en la calidad de la materia prima, porque tiene mucha incidencia en la calidad del producto final.
¿Qué garantías o certificados existen hoy en día?
La certificación ISO 9001 asegura el control a todo el proceso de fabricación en la industria del metal, desde la calidad de las materias primas hasta su formato final, que la realizan agentes externos apoyados en las normas, con pruebas de ensayos químicos, análisis de laboratorio, etc.
También las certificaciones ISO 50001 y 14001 tienen en cuenta el desarrollo sostenido de todos los impactos medioambientales y energéticos que tienen gran calado en el sector de las empresas metalúrgicas. Garantizan el impacto de todos estos aspectos en el proceso de producción de fabricación del metal ya que es una industria que necesita grandes recursos.
En este sentido, ¿cuáles son los más exigentes en cuanto a calidad del metal producido? ¿Por qué?
El sistema de gestión de calidad está centrado en la mejora continua de todos los procesos, de ahí que la calidad del producto final radique en los controles exhaustivos que se realizan en las instalaciones y en garantizar la trazabilidad y control de las materias primas.
Además de la implantación de acciones que mejoren las operaciones diarias se dispone de la capacidad y la tecnología necesaria para llevar a cabo análisis de composición química y calidad del producto final. Como resultado de estas medidas, en los procesos se cumplen con los estándares más exigentes de calidad, lo que pone de relieve su alta fiabilidad.
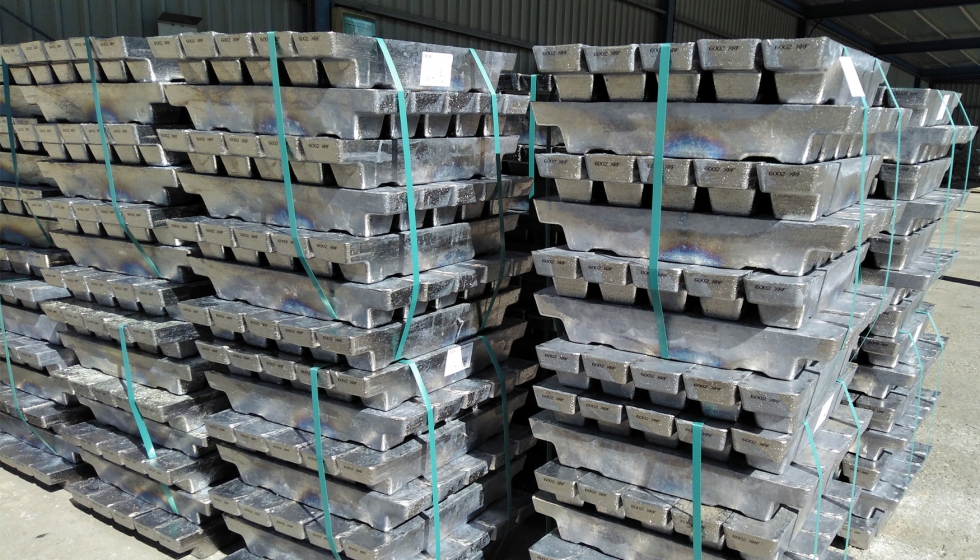
Y finalmente ¿qué aporta el Centro Cartif en este proyecto?
Cartif participa en este proyecto como coordinador del piloto de plomo junto con la empresa Exide Technologies aplicando técnicas de inteligencia artificial para el modelado, control y desarrollo de herramientas de decisión en los procesos de fundición y refinado del plomo.
Cartif como centro tecnológico con sede en Boecillo (Valladolid), cuenta con amplia experiencia en la gestión y desarrollo de proyectos en el ámbito de la Industria 4.0 en sectores diversos, como la industria agroalimentaria y de automoción que aplicará al proyecto Revamp.
Para ello, primero se ha realizado una actualización de los sistemas de monitorización y recogida de datos en los hornos de la planta. Posteriormente el tratamiento de la información recogida dará paso al desarrollo de modelos de predicción, lo que va a permitir implementar herramientas de decisión para la carga y el buen funcionamiento de los hornos de fundición.
Otra de las herramientas a desarrollar, permitirá la optimización en el proceso de refinado del plomo, mediante la búsqueda de la mejor combinación de bloques obtenidos en los procesos de fusión del plomo para la carga en los crisoles.
La aplicación de todas estas tecnologías en la planta de Exide, miembro del proyecto, situada en San Esteban de Gormaz (Soria), tiene como objetivo final la reducción del consumo energético y los tiempos de producción, consiguiendo una disminución del impacto ambiental en este tipo de industrias.