La importancia de la gestión de cargas en maquinaria industrial
Fernando Vázquez González, Business Development Power Products en Schneider Electric
05/01/2021Todos estos problemas pueden abordarse fácilmente, contando con un control de cargas digitalizado, que permita monitorizar la energía, un mantenimiento predictivo y una conectividad en remoto.
¿Por qué se para una línea productiva?
Una de las principales causas de las paradas no planificadas es el desgaste de los equipos debido al mal funcionamiento. Un deterioro que suele acabar en avería y supone el 42% de las paradas de línea. Estaríamos hablando de fallos que se van gestando poco a poco, por desgaste, como, por ejemplo, por la pérdida de aislamiento por sobrecalentamiento continuo en el devanado de un motor. Aunque también, en muchas ocasiones, por el alcance del fin de vida de los dispositivos de control de potencia que actúan sobre dichos equipos activos, dado que, aun teniendo una vida predecible a partir de los datos dados por el fabricante, sus condiciones de trabajo reales terminan por alterar significativamente los plazos en los que debería haberse realizado una reposición o mantenimiento de estos.
Otro de los problemas más habituales son las sobrecargas eléctricas. Éstas pueden ser causadas por varios motivos como, por ejemplo, cortocircuitos, suministros de voltaje exagerados, o demasiado bajos, que producen corrientes excesivas en los devanados del motor.
Monitorizar los activos en tiempo real utilizando un sistema de control de cargas nos permite controlar la temperatura del motor, los datos de su ciclo de trabajo, su consumo de energía, o la vida útil restante del elemento de control y, así, detectar las tendencias anómalas que acaban en avería y adelantarnos a ellas.
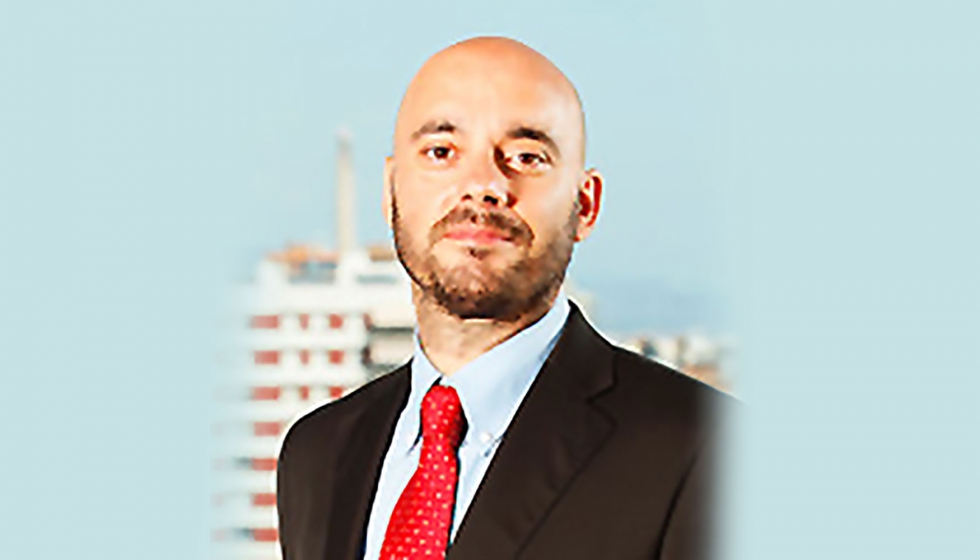
La digitalización nos permite ganar en eficiencia y competitividad
Actualmente, el 70% de las empresas sigue siendo incapaz de preparar sus equipos para evitar las paradas de línea. Solo el 26% utiliza el mantenimiento predictivo basado en datos y la monitorización de activos, capacidades que, como hemos visto, permiten identificar de forma más precisa los ciclos de mantenimiento necesarios para evitar las paradas no planificadas.
Hasta un 35% de los costes de producción se corresponden con el mantenimiento, donde el 62% es de tipo reactivo y correctivo. Dado que, el mantenimiento no ejecutado (13%) y el no planificado (11%) suman el 24% de las causas de fallo, resulta evidente que un mantenimiento predictivo de enfoque proactivo basado en datos y el estado real de cada activo, permitirá a las empresas mejorar sus operaciones y optimizar el uso que hacen de sus recursos.
Otro de los grandes problemas del sector industrial es un gasto energético excesivo que genera un importante sobrecoste productivo. La industria consume cerca del 42% de la electricidad mundial y dos terceras partes de ésta son utilizadas por los motores eléctricos. De éstos, el arranque directo sigue vigente en el 80%, estando el otro 20% equipado con Variadores de velocidad. En la mayoría casos, el conocimiento del consumo energético que se tiene de la línea productiva no es específico para cada carga en funcionamiento, sino general del conjunto de la misma, ya que no se reporta al sistema información específica en tiempo real de cada uno de los motores. Esto significa que la imputación que se haga de los costes energéticos a cada uno de los posibles y diversos bienes producidos podría estar muy alejada de la realidad específica de cada uno de ellos, con una afectación clara tanto en su rentabilidad como en su competitividad cuando éstos llegan al mercado.
Para optimizar los presupuestos es fundamental reducir el consumo eléctrico en general, pero también, y fundamentalmente, de modo pormenorizado conociendo el coste exacto de producción de cada pieza, máquina, línea, área o planta. Este objetivo no es alcanzable sin la capacidad de monitorizar todos los datos útiles y analizarlos de forma efectiva. Por ejemplo, contrastar los datos de consumo eléctrico con el coste de la electricidad o la productividad de los equipos para evaluar metodologías de actuación más rentables.
Tesys Island: control de cargas fácil y flexible
Como decíamos, digitalizar el control de cargas permite evitar las paradas de línea no planificadas y reducir el consumo de energía. En este sentido, Tesys Island de Schneider Electric permite hacerlo de forma sencilla y flexible, poniendo al alcance de las empresas del sector el mantenimiento predictivo de las cargas y los propios dispositivos, la monitorización de la energía y la conectividad remota.
Tesys Island es un sistema digital 4.0 abierto que permite controlar múltiples cargas de hasta 80 A, y que conecta sistemas de forma cibersegura con los principales protocolos de comunicación industriales, captura datos, los analiza y permite tomar mejores decisiones en tiempo real. Todo ello mejora de forma sustancial el mantenimiento, ya que la cantidad de información aportada hace posible anticiparse, incrementar la eficiencia y el ahorro de costes.
Por otro lado, la indicación predictiva del momento óptimo en el que hay que hacer el mantenimiento de los propios elementos de Tesys Island, basada en los datos aplicativos reales, proporciona una capacidad de anticipación a paradas de línea no deseadas que no es posible obtener con arrancadores basados en semiconductores. Es por eso por lo que Tesys Island es el sistema idóneo para la monitorización de procesos críticos.
Con todo ello, los técnicos pueden observar tendencias a largo plazo de los principales parámetros del proceso y aprender a detectar cambios de comportamiento que pudieran suponer la génesis de un problema, y los usuarios avanzados pueden desarrollar modelos estadísticos comparables con la realidad que permitan evoluciones productivas acertadas.
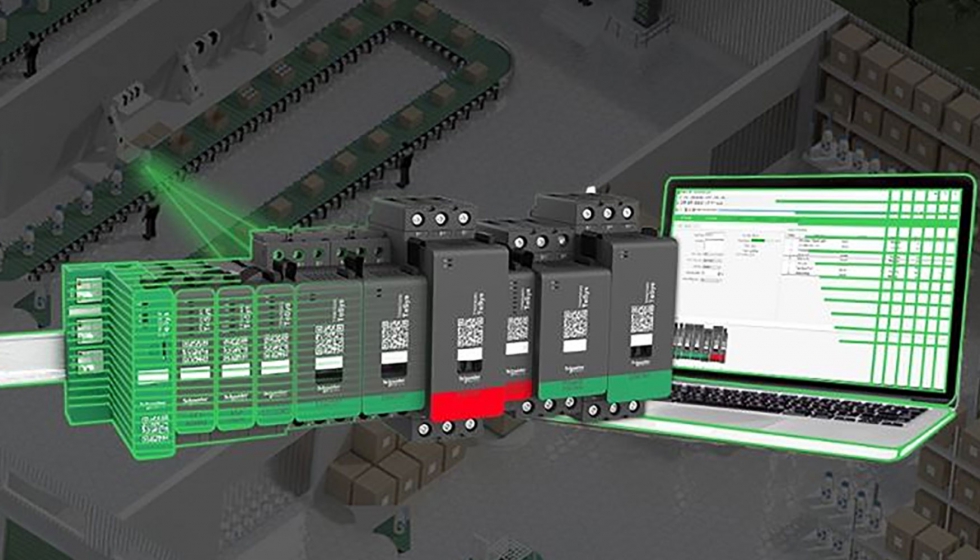
La interfaz de usuario basada en web que incorpora Tesys Island permite la supervisión remota y cibersegura a través de cualquier dispositivo móvil, reduce el número total de dispositivos en la arquitectura de control y adapta las mismas a los hábitos de una nueva generación de personas más digitales.
Estas capacidades digitales de Tesys Island resultan especialmente interesantes también para los OEM, no sólo porque el conocimiento total del coste de cada unidad producida por su máquina le permitiría ofrecer a su cliente la máquina como un servicio en lugar de como un producto, sino también porque pueden ofrecer servicios de intervención, mantenimiento, analítica etc, a sus clientes sin tener que desplazarse, ganando así claramente en velocidad, productividad, y, lo más importante, en satisfacción de su cliente final.