El proyecto faro futureAM de Fraunhofer obtiene impresiones en 3D metálicas ‘en forma’ para uso industrial
Acelerar la producción aditiva de los componentes metálicos por lo menos en un factor de 10: con este objetivo en mente, la Fraunhofer-Gesellschaft lanzó el proyecto faro ‘futureAM - Next Generation Additive Manufacturing’ en 2017. Al finalizar el proyecto en noviembre de 2020, seis institutos Fraunhofer han dado saltos tecnológicos en ingeniería de sistemas, materiales y control de procesos, así como en la digitalización de extremo a extremo, aumentando así el rendimiento y la rentabilidad de la fabricación aditiva basada en el metal a lo largo de toda la cadena de procesos.
Por un lado, los socios de futureAM se han centrado en la integración de la cadena de valor digital y física desde los pedidos entrantes hasta el componente metálico acabado e impreso en 3D y, por otro, en dar un salto hacia una nueva generación tecnológica de fabricación aditiva. La plataforma digital Virtual Lab desempeña un papel importante en esto, ya que reúne las competencias de forma digital y hace que todo el proceso de fabricación aditiva sea transparente para todos los socios implicados. “Estamos ahora en el umbral de la implementación industrial”, dice Christian Tenbrock, jefe de grupo del Instituto Fraunhofer de Tecnología Láser ILT y director del proyecto futureAM. “La experiencia que hemos adquirido juntos debe ser ahora transferida a la aplicación industrial”.
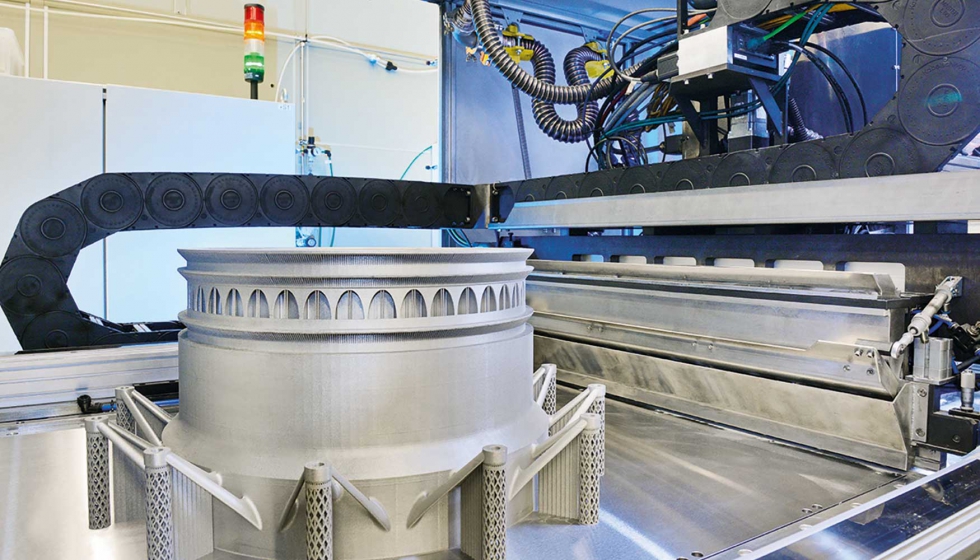
El laboratorio virtual reúne la experiencia
Un importante desafío para futureAM fue la interacción entre todos los participantes, algunos de los cuales cubren áreas muy diferentes de toda la cadena de procesos. El Virtual Lab, una plataforma digital que asegura el intercambio de información a través de todas las áreas de tareas y actores de la fabricación, ha demostrado su valor. En este contexto, el Instituto Fraunhofer de Tecnologías de Producción Aditiva IAPT ha desarrollado varias herramientas de software para el diseño de componentes aditivos. De esta manera, ha creado herramientas de simulación basadas en la web para la fabricación aditiva de metales, herramientas que también pueden ser utilizadas por los principiantes.
Componentes multimateriales sin unión posterior
En el ámbito de la actividad ‘Materiales’, el Instituto Fraunhofer de Tecnología de Materiales IWS, de Dresde, ha investigado qué materiales pueden combinarse entre sí en un componente y qué problemas surgen en el proceso. Entre otras cosas, los investigadores de Dresde se han ocupado de ampliar el espectro aplicable de materiales de alta temperatura procesables adicionalmente e investigado cómo pueden combinarse en un diseño multimaterial. La interacción de la deposición de material por láser (LMD) y la inteligencia artificial (AI) dio un resultado emocionante: gracias al análisis de procesos apoyado por la IA, el instituto pudo analizar una amplia gama de factores de influencia y optimizar el proceso de fabricación. El Fraunhofer IWS demuestra lo bien que funciona ya el proceso utilizando componentes multimateriales de níquel y aluminio. Según los requisitos de los componentes, los investigadores añaden un tercer o cuarto elemento para adaptar las propiedades exactamente a la aplicación respectiva.
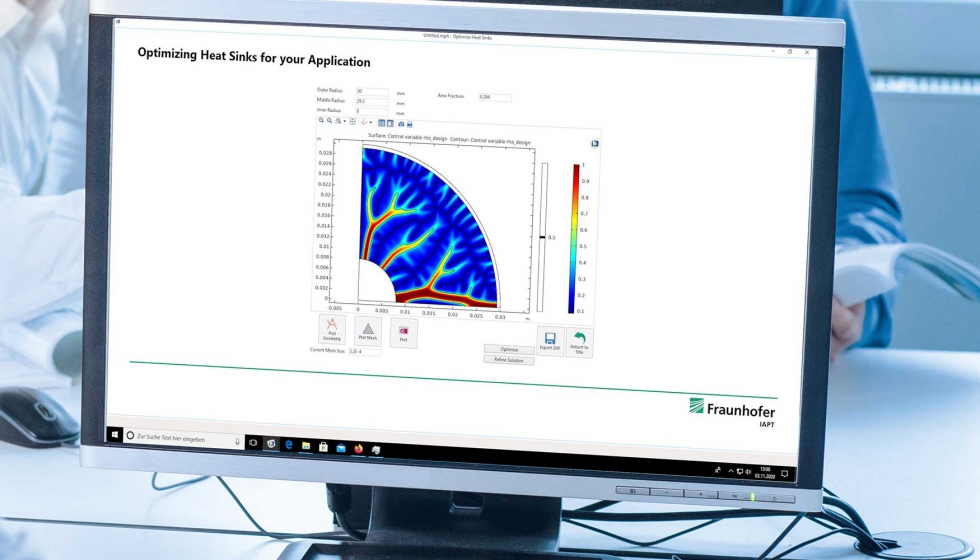
Componentes en formato XXL: despegue 10 veces más rápido
Los científicos del Instituto Fraunhofer de Aquisgrán han desarrollado un sistema de demostración construido por un fabricante de máquinas. Se trata de un sistema para la impresión en 3D de componentes a escala XXL. Por ejemplo, un componente de demostración para las futuras generaciones de motores Rolls-Royce podría ser fabricado con fusión de lecho de polvo láser (LPBF) gracias al gran volumen de construcción (1000 mm x 800 mm x 400 mm) y un nuevo sistema de máquina con un sistema óptico móvil. Se han logrado éxitos similares con la deposición de material láser de extrema velocidad (EHLA), que ahora también puede utilizarse para producir componentes 3D. El nuevo proceso desarrollado permite velocidades de deposición extremadamente rápidas con alta resolución de detalles.
El posprocesamiento automatizado ahorra recursos
Los investigadores también identificaron un gran potencial de optimización en el posprocesamiento. Por ello, el Instituto Fraunhofer de Máquinas Herramientas y Tecnología de Conformado IWU de Chemnitz desarrolló una solución automatizada para ello como parte del proyecto. Para permitir que el proceso identifique y rastree el componente físico más allá de toda duda y de manera continua, se incorpora un código durante la fabricación y se lee en voz alta posteriormente. Este código también asegura una protección de copia eficiente y sin problemas. En el siguiente paso, la geometría real del componente sujetado se registra mediante escáneres láser y la estrategia de procesamiento óptima se deriva de la comparación entre la geometría objetivo y la real. El procesamiento se realiza entonces automáticamente por un robot y se verifica en el proceso mediante escaneos 3D renovados. También tendrá la oportunidad de hablar con los expertos del equipo de futureAM en el formnext virtual 2020 del 10 al 12 de noviembre. Registros aquí: https://formnext.mesago.com/frankfurt/en.html
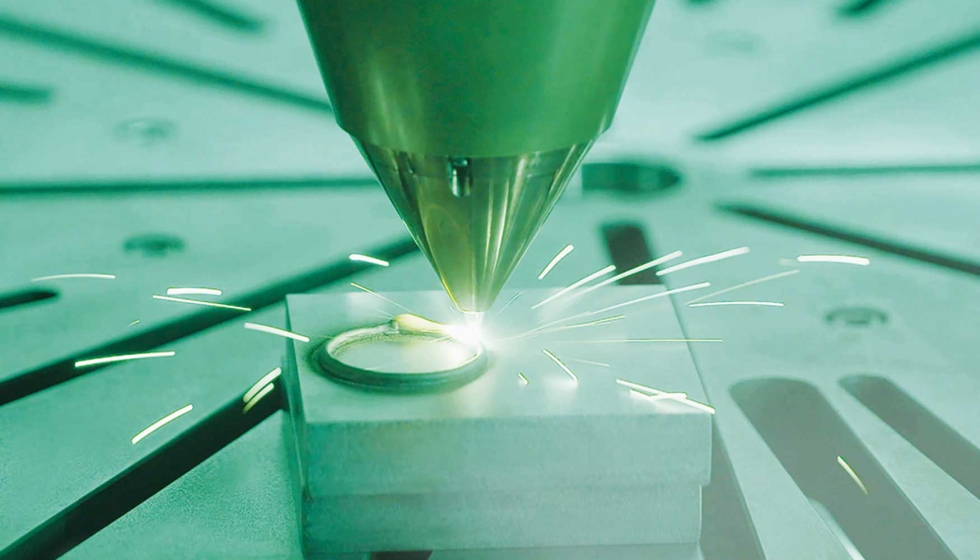
Proyecto Faro Fraunhofer ‘futureAM - Next Generation Additive Manufacturing’
Con la fundación de futureAM, la Fraunhofer-Gesellschaft está avanzando sistemáticamente en el desarrollo de la fabricación aditiva de componentes metálicos. Los siguientes institutos han entrado en una asociación estratégica de proyectos en el campo de la fabricación aditiva:
- Instituto Fraunhofer de Tecnología Láser ILT, Aachen (coordinación del proyecto),
- Instituto Fraunhofer de Tecnologías de Producción Aditivas IAPT, (Hamburgo)
- Instituto Fraunhofer de Tecnología de Fabricación y Materiales Aplicados-Investigación IFAM, Bremen
- Instituto Fraunhofer de Investigación de Gráficos por Ordenador IGD, Darmstadt
- Instituto Fraunhofer de Tecnología de Materiales IWS, Dresden
- Instituto Fraunhofer de Máquina-Herramienta y Tecnología de Conformado IWU, Chemnitz, Dresden
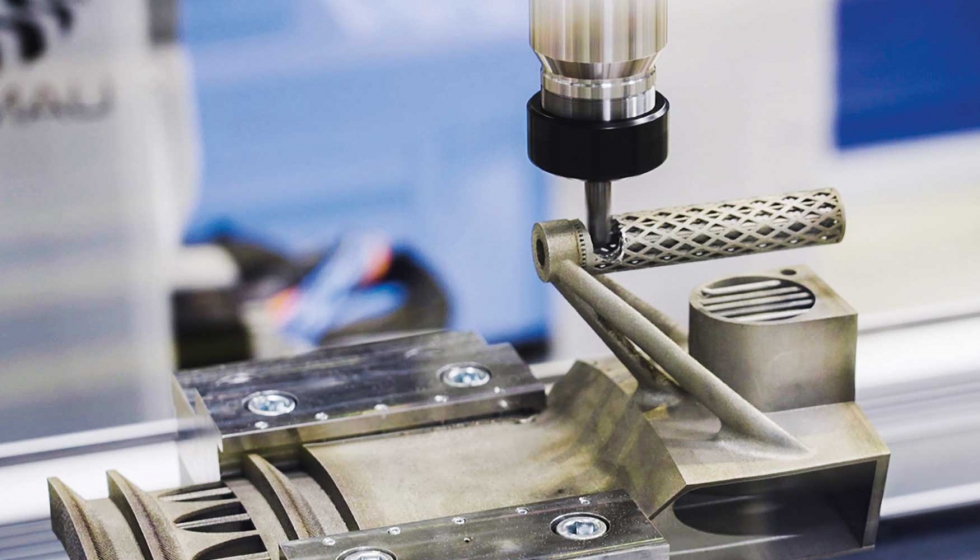