SP-MAG, el caso de éxito de Panasonic Welding System & co
Sergio Cherta, Country Manager de Roboteco en España (cherta@roboteco.com)
06/10/2020Cuando les pregunto las razones por las cuales utilizan un arco pulsado para bajos espesores, esto es lo que habitualmente me responden que para incrementar la velocidad de soldadura y para reducir la generación de proyecciones típicas de la soldadura de arco de cortocircuito (CC), que obliga a una limpieza posterior, tanto de las piezas como de los utillajes. Estas acciones de limpieza adicionales aumentan los costes de mano de obra directa y reducen los márgenes de beneficio. Estos son los motivos principales por los cuales las empresas argumentan la obligación de utilizar el arco pulsado como tecnología de unión, a pesar de sus inconvenientes.
¿Y cuáles son esos inconvenientes? Vuelvo a preguntar. Y la mayoría me responden, con buen conocimiento de causa, que el arco pulsado es un arco mucho más abierto que el de cortocircuito y por lo tanto no penetra en la raíz de la unión como lo hace el arco CC; que el arco pulsado tiende a crear incisiones marginales; y que el arco pulsado, a igualdad de corriente, trabaja con valores de tensión (voltios) mucho más elevados que el arco CC, calentando mucho más la pieza, deformándola por dilatación térmica y obligando a elaborar utillajes más complejos, con materiales caros para la disipación de calor, con más agarres e incluso con sistemas de recirculación y refrigeración líquida para reducir la temperatura del sistema y poder retirar la pieza.
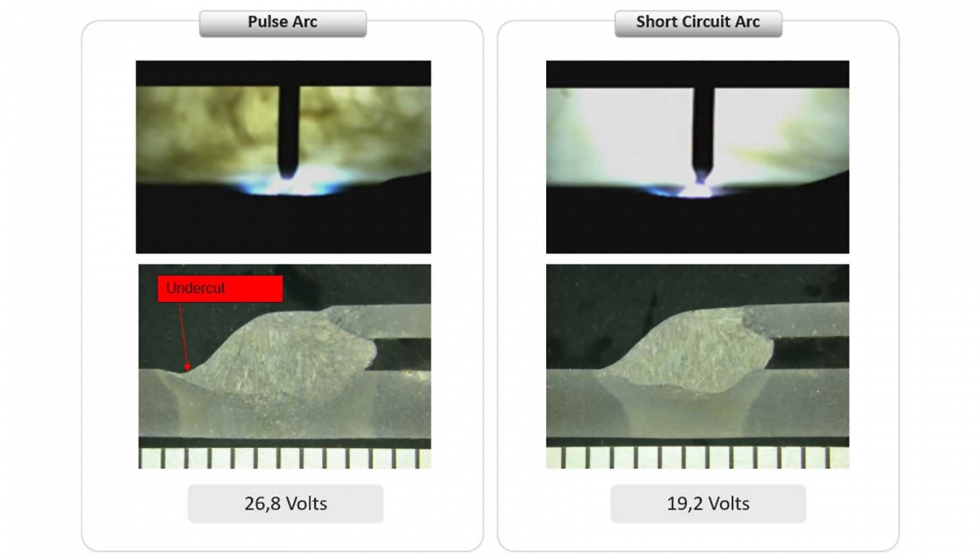
De nuevo, a la ‘japonesa’, respondo con otra pregunta: ¿Y estos inconvenientes no suponen también costes adicionales y reducción de vuestros márgenes de beneficio? “Sí, pero debemos escoger entre el menos gravoso. ¿Cómo si no?”, responden.
Mi última pregunta es obvia: ¿Por qué no utilizar un proceso que sea capaz de utilizar las ventajas de uno y de otro, y desechar los inconvenientes de ambos?
Llegados a este punto, les explico lo que cada vez más clientes en el mundo conocen como uno de los casos de éxito de Panasonic Welding System & Co: SP-MAG.
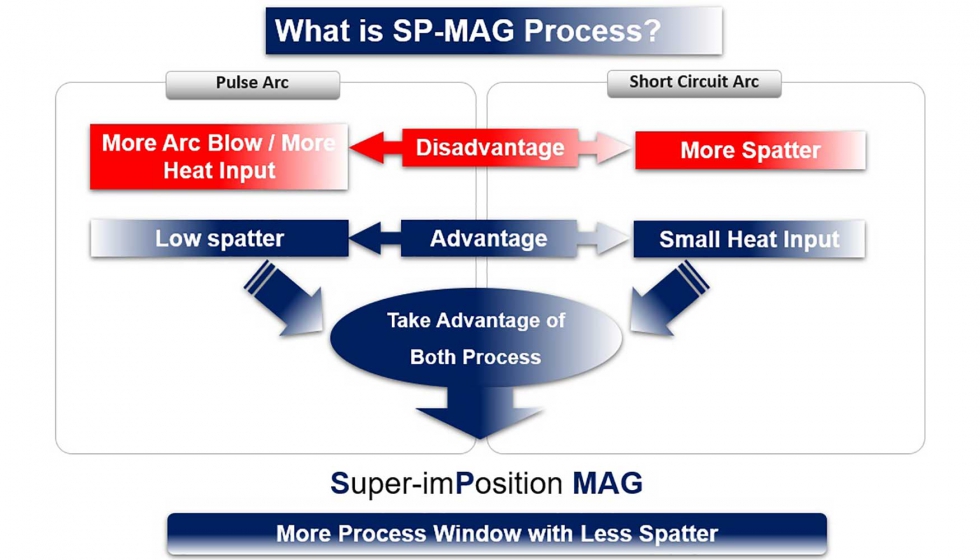
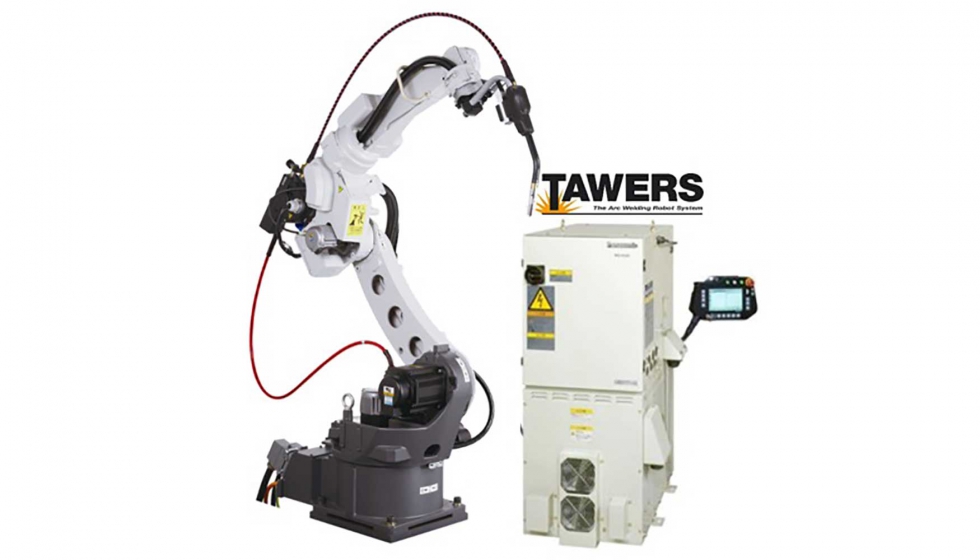
¿Y cómo Panasonic fue capaz de desarrollar este proceso?
Tres fueron las claves:
- Mediante la incorporación de su sistema TAWERS (The Arc WElding Robot System), donde, tanto el brazo antropomórfico como el generador de corriente están controlados por una única y potente CPU. Siendo así, que el sistema TAWERS es el único sistema de soldadura robotizada en el mundo donde el servo de avance y control del hilo de aporte es el séptimo eje del sistema.
- Mediante la incorporación de una forma de onda avanzada, diseñada específicamente para minimizar la volatilidad del arco voltaico gracias a un control y una monitorización precisa del comportamiento de la tensión y de la corriente y capaz de reaccionar en consecuencia en tiempo real a cualquier eventualidad.
- Dado que la soldadura de cortocircuito es un proceso volátil, donde los cambios de estado pueden producirse del orden de hasta 100 veces por segundo, fue necesaria la incorporación de un doble inverter con una velocidad de procesamiento de un primario de 100 kHz, capaz de controlar el ciclo cada 10 micro-segundos, es decir, ¡con capacidad de cambiar la forma de onda en ese lapso de tiempo! Y un inverter secundario capaz de cortar drásticamente la corriente antes y después de un cortocircuito, reduciendo la transición entre uno y otro, acortando el ciclo y estabilizando el baño de soldadura.
En definitiva, la tecnología SP-Mag es capaz de aportar valor, aumentar la eficiencia de los procesos de soldadura robotizada y mejorar la competitividad de la empresa.
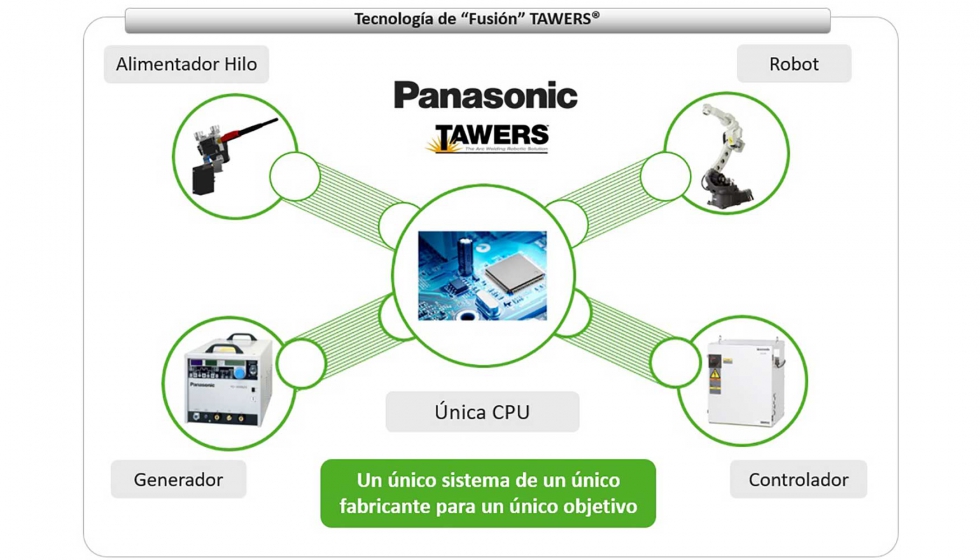