La fabricación aditiva en la tecnología sanitaria
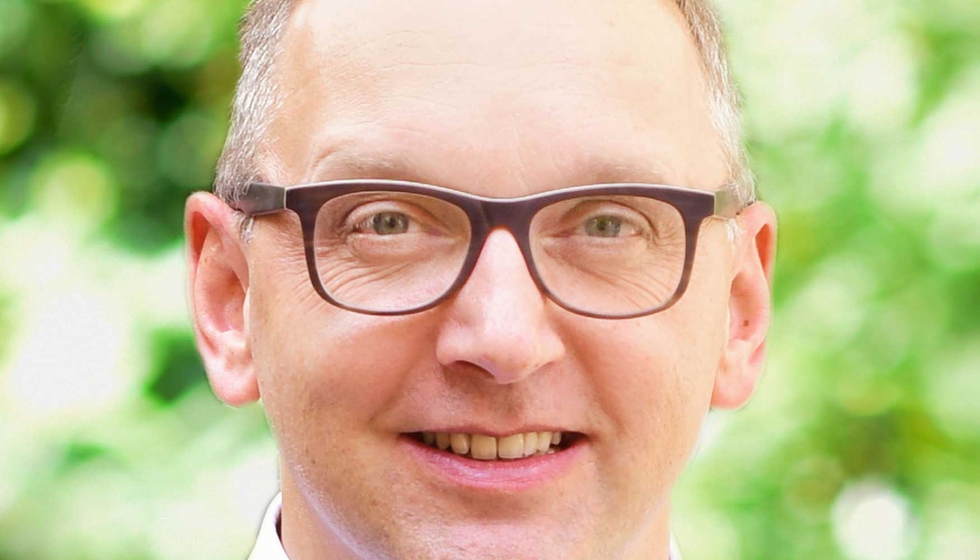
Frank Carsten Herzog: “Tenemos por delante una importante tarea: la formación y perfeccionamiento en impresión 3D como factor clave”. Foto: HZG Management GmbH & Co. KG.
La fabricación aditiva o additive manufacturing (AM) está presente en ámbitos de aplicación sumamente diversos. Como tecnología ecológica, la AM altera las anteriores estrategias de fabricación de manera cada vez más disruptiva. A menudo se trata de sustituir procesos clásicos como la fundición o el fresado. Este proceso sin molde expande la libertad geométrica, la reingeniería, la preservación de recursos, con grandes ventajas en economía y disponibilidad. Pero las ventajas esenciales no radican en copiar componentes convencionales, sino en nuevos diseños y aplicaciones constructivas biónicas. Entran en juego el tiempo de comercialización y la rápida disponibilidad, así como la reducción de tiempos de inactividad. Con el trasfondo de la discusión acerca de largas cadenas de suministros en el contexto de la globalización, la AM también se enfoca a la producción local. Y es que la producción in situ significa también que el valor añadido, el desarrollo y la fabricación del producto se acercan más a los consumidores. Una reducción del esfuerzo logístico contribuye al logro de los objetivos climáticos. En los siguientes ejemplos haré particular hincapié en la impresión 3D en metal.
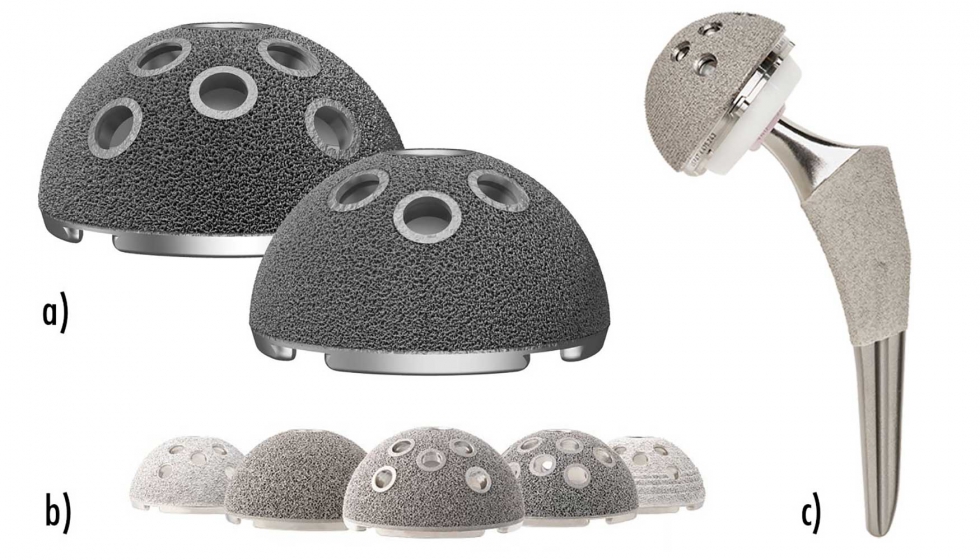
Panorama de la tecnología sanitaria
En la tecnología sanitaria, los materiales juegan un papel decisivo. Los clásicos grupos de materiales son metal, cerámica o plásticos. En los metales, y en el proceso LaserCusing desarrollado por mí, el proceso de fusión láser de lecho de polvo para metales (aproximadamente 80 % de la cuota de mercado global de todos los sistemas AM para metal), se produjo una adaptación muy temprana en la tecnología sanitaria, puesto que siempre pudimos utilizar materiales originales certificados en forma de polvo. Esto también es aplicable a las soluciones en cerámica. Debido a la diversidad y al comportamiento de los materiales, en los polímeros es un poco más complejo, por lo que, en comparación, las aplicaciones metálicas presentan un avance tecnológico de unos 5 a 10 años. Si se arroja luz sobre las disciplinas médicas, se aprecian varias áreas de aplicación de pequeñas piezas: implantes para caderas, articulaciones, columna vertebral, prótesis de cráneo o sustitución de piezas dentarias. Esto se complementa con instrumental médico, insumos para laboratorio o componentes para medicina de alta tecnología; en este aspecto la palabra clave en la actualidad son las válvulas para equipos de reanimación y respiradores artificiales. Incluso en la veterinaria existe actualmente una serie de ejemplos de tecnología de implantes, como veremos más adelante.
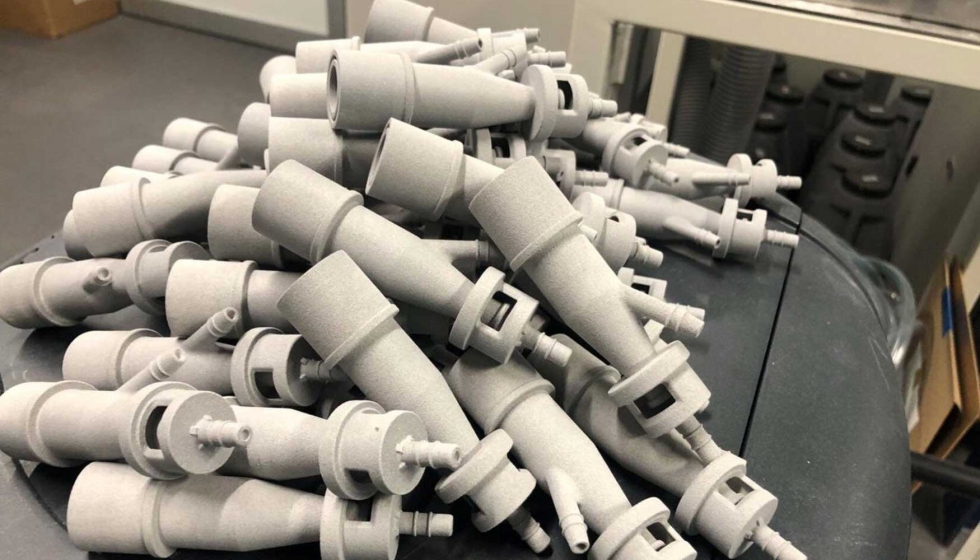
Válvulas de Venturi 3D en poliamida de Lonati, Italia. Foto: Lonati.
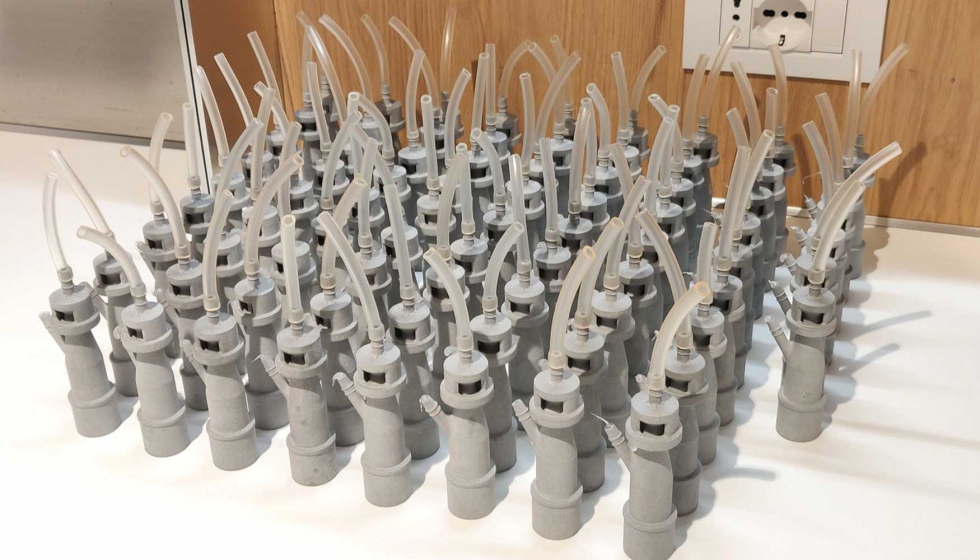
Válvulas de Venturi 3D en poliamida de Isinnova, Italia. Foto: Isinnova.
Situación actual de la tecnología dental
Ahora desearía llamar la atención acerca de la rentabilidad en base a un ejemplo de la tecnología dental. El trabajo convencional de los técnicos dentales es artesanal. Esto implica altos costes materiales y salariales. Para las prótesis dentales existen precios fijos. ¿Qué hacían entonces los técnicos dentales y los odontólogos para lograr rentabilidad? Apostaban por materiales económicos o adquirían implantes en el extranjero. O ambas cosas. Pero la AM tomó otro camino. Las prótesis dentales como coronas o puentes múltiples se obtienen con geometrías específicas para cada paciente en el espacio de construcción de un equipo de fusión por láser para metales. A veces, 80 o 100 implantes simultáneamente. Para los laboratorios de prótesis dentales que se reconvirtieron en centros de impresión, esto significó un gran salto en cuanto a rentabilidad. Se puede considerar que las prótesis dentales, contemplando todos los volúmenes, pueden llegar a ser de un 60 a un 70 % más económicas que las soluciones elaboradas a mano. Implante por implante.
Para un pleno aprovechamiento de capacidades, estos centros de impresión brindan sus servicios a un gran círculo de clientes de odontólogos, y así pueden proveer de prótesis dentales económicas, precisas y con rápida disponibilidad. Esta estrategia también logra ventajas para el paciente, y no solo por la rápida disponibilidad; también es posible utilizar materiales muy duraderos y de alta calidad, como el titanio, que es extremadamente resistente. Es muy bien tolerado por los alérgicos. Otra ventaja es su precisión; lo que es muy interesante en los puentes múltiples. Tradicionalmente, aquí aparecen tensiones en el implante. Con relación a un ciclo de vida largo, pueden darse ciertas limitaciones para el paciente. Gracias al tratamiento térmico del componente en el procesamiento posterior, un implante impreso en 3D tiene el grado de libertad de un módulo de elasticidad: se evitan las tensiones y se ayuda en el proceso de masticación. Así, el bienestar del paciente y las necesidades económicas no suponen una contradicción.
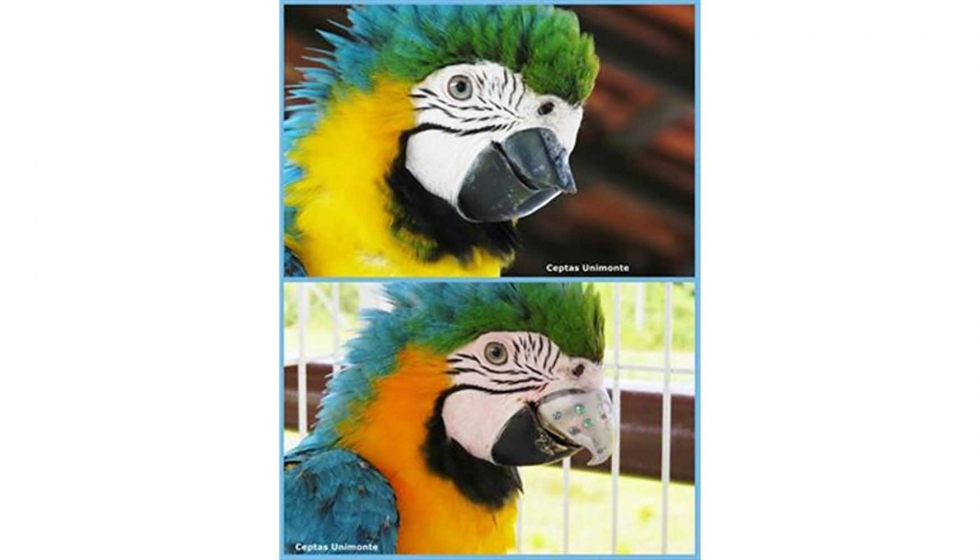
Guacamayo Gigi con pico 3D, antes y después de la operación. Foto: Cícero Moraes, Centro para el Cuidado de Animales en Sao Paulo, Brasil.
Datos de mercado y perspectivas de la fabricación aditiva
En 2018 (2019) el mercado de la fabricación aditiva ascendió a 9.300 (10.400) millones de dólares, según un informe de la empresa SmarTech Analysis de enero de 2020 (‘Additive Manufacturing Market Outlook 2020’). Esto significó un incremento del 18 % con respecto al año anterior. Para 2027 (2029) este instituto de investigación de mercado pronostica un mercado global de casi 41.000 (55.000) millones de dólares. Otros analistas más conservadores, como Hubs, dan tasas de crecimiento de un 18,2 a un 27,2 % anual. Pero, aun así, esto eclipsa a muchos otros sectores. La empresa inglesa de análisis de mercado Context pronostica para las impresoras 3D de metal un crecimiento superior al 49%. Para las impresoras de polímeros, Context indica un crecimiento superior al 20%. No obstante, los mayores incrementos de facturación en el sector de la fabricación aditiva recaen en la producción industrial en serie a mediana y gran escala. Esto incluye a la tecnología sanitaria solo en parte.
El mercado de impresoras 3D para ortopedia se estimó para 2018 en 691 millones de dólares. SmarTech Analysis pronostica que, hasta 2027, crecerá hasta alcanzar un mercado de 3.700 millones de dólares. El mercado de la impresión 3D sanitaria, incluidos materiales, servicios, software y hardware, según estimaciones de SmarTech Analysis asciende a 1.250 millones de dólares. SmarTech Analysis informa que la facturación de productos dentales en 3D crecerá hacia 2021 a 3.700 millones de dólares y que, hasta 2027, esta tecnología será el método de producción líder a nivel global para prótesis dentales y aparatos. Con referencia al mercado global, EY Research indica para 2019 que 722 empresas de AM proceden de Europa, 421 de las Américas y 168 de Asia.
O sea, Europa es un actor esencial en esta tecnología.
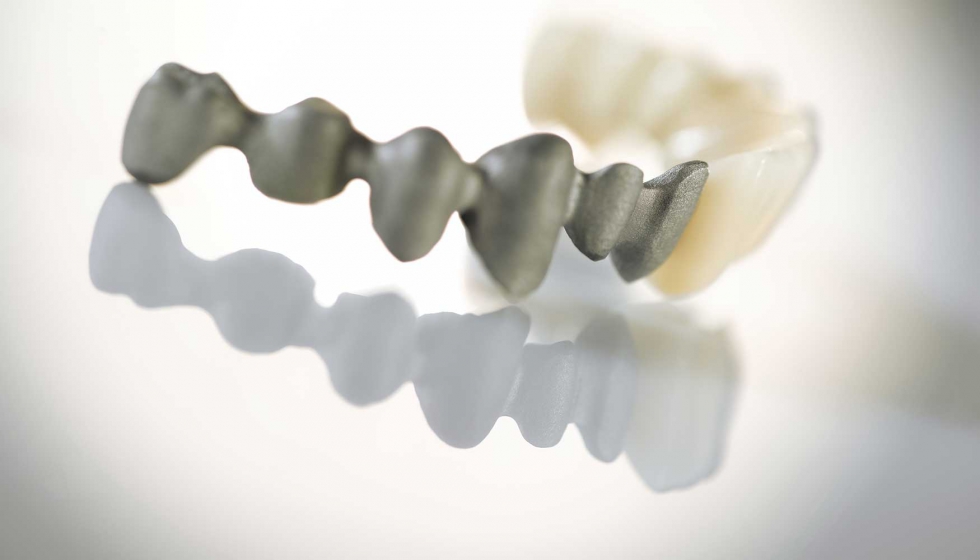
Los componentes dentales 3D en la placa de un equipo de fusión láser de metal. Foto: Concept Laser.
Evolución actual del mercado de proveedores y usuarios de la impresión 3D
Hay que aclarar que, en el sector de la fabricación aditiva, los proveedores se encuentran actualmente en una fase de consolidación. El enorme crecimiento, en particular en los últimos diez años, con numerosos saltos de innovación, y la consolidación de precios, surten efecto. Los grandes actores como Stratasys, 3D Systems, SLM Solutions, HP, EOS, GE Additive o MarkForged lo experimentan de forma más intensa. No obstante, hay nuevas pequeñas empresas que se abren camino, con soluciones creativas, en un mercado dinámico. Un mercado que todavía está lejos de una fase de saturación o de luchas por la supremacía. Por el contrario, los usuarios parecen subir una cuesta muy empinada. Esto se aprecia en las empresas del sector sanitario, al igual que en otros sectores. Pero esto también es así para los numerosos prestadores de servicios de impresión 3D que, con su experiencia y capacidades de AM, acompañan a numerosos sectores hacia el sector de la impresión 3D. Las posibilidades de la AM para mejorar los productos existentes son realmente tentadoras. Los conceptos clave son: diseño biónico, construcción ligera, componentes específicos para cada paciente, el enfoque one shot que reduce los componentes de un conjunto de manera drástica y sin complicaciones de montaje, fabricación descentralizada y rápida disponibilidad. Más tarde abordaré puntos en particular.
En primer término, mostraré algunos ejemplos actuales de la tecnología sanitaria.
Ejemplo de implante de acetábulo 3D de Stryker
Considerando la demografía de los baby boomers en el mundo occidental, los implantes ortopédicos juegan un papel cada vez más importante en el aparato locomotor de las personas. En la tecnología sanitaria se prevé un relevante mercado de futuro en aplicaciones para cadera, rodilla y columna vertebral. La empresa Stryker de Cork (Irlanda) desarrolló un nuevo implante de acetábulo 3D en titanio, fabricado con tecnología de fusión por haz de electrones (EBM, por su sigla en inglés). En 2016 obtuvo la certificación de la FDA (Food and Drug Administration) estadounidense. Stryker denominó Trident II Acetabular System a este producto, y destacó que se trata de una solución sin cemento que mejora de manera significativa la durabilidad en el cuerpo. La impresión 3D posibilita geometrías extremadamente complejas que no se podrían fabricar de modo convencional. El implante de acetábulo 3D en titanio presenta propiedades mecánicas duraderas de una cinemática consistente en un cabezal esférico y una esfera, opcionalmente en metal, cerámica, polietileno o un híbrido de aluminio y cerámica, así como un elemento de enclavamiento. Las superficies de poros abiertos del componente metálico 3D ayudan en la aceptación por parte del tejido. Además, el titanio es apto para alérgicos. Este implante viene en varias dimensiones, para adaptarlo según las necesidades específicas del paciente, reducir el riesgo de operación y mejorar la movilidad del paciente de manera óptima. En 2017, GE Additive y Stryker celebraron un acuerdo de colaboración para apoyar el crecimiento de Stryker en la fabricación aditiva. El acuerdo comprende nuevas máquinas aditivas, materiales y servicios para la cadena de suministros global de Stryker. A partir de esta alianza, en 2019 Stryker destinó 200 millones de dólares a la ampliación de sus unidades de investigación en 3D en Cork y, además, construyó una fábrica 3D completa para diversas aplicaciones de impresión 3D, con digitalización completa en todos los procesos. Naturalmente existen numerosos proveedores de tales soluciones en 3D. En aras del equilibro, mencionaré a B. Braun, Surgival, SurgTech, ImplanTech, Imeco, Medacta, Link, Go Eassdy y Rentec.
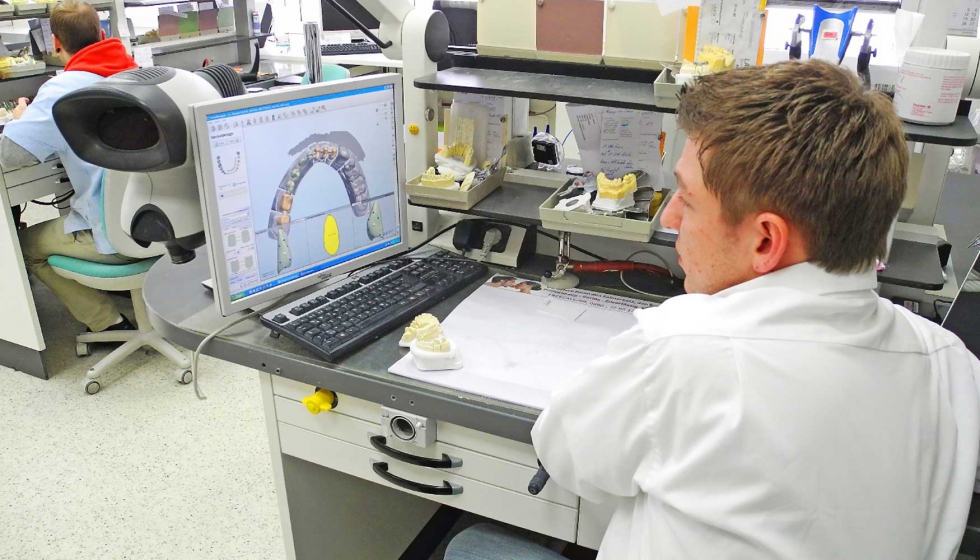
Preparación para el trabajo con datos STL en un laboratorio dental. Foto: Provvido.
Ejemplo de viseras protectoras de boca y nariz para los hospitales de Bamberg y Coburgo
Al desatarse la pandemia de SARS-CoV-2, los materiales de protección se convirtieron en una necesidad imperiosa a escala global. En primer lugar, las existencias para casos de emergencia apenas bastaban para 2 a 3 semanas; y en segundo lugar, muchos se fabricaban fuera de la UE. Las cadenas y tiempos de suministro eran demasiado largos. Además, había precios astronómicos para calidades dudosas. A nivel político y sanitario existía una alarma generalizada, puesto que las cifras de infectados crecían a nivel exponencial. Cualquier pérdida de disponibilidad de personal sanitario habría convertido una crisis en catástrofe, lo que de hecho ocurrió en algunos países. Desde la unidad de urgencias en el hospital de Bamberg me consultaron, en el contexto de esta difícil situación, si existía una solución de impresión 3D para viseras de protección facial. En principio, se trata de una construcción sencilla compuesta de lámina de plexiglás y aro para la cabeza. No podíamos imitar modelos certificados con tanta rapidez, pero sí máscaras improvisadas, consistentes en protección facial, bata protectora y mascarilla respiratoria. No obstante, yo también me di cuenta de que esto solo podía funcionar en red, porque la impresión 3D solo puede ser parte de la solución, y no la solución completa. En mi caso, la red fue el Centro de Investigación y Aplicación de Nuevas Tecnologías Digitales (FADZ) en plena construcción en Lichtenfels, que reúne a numerosas empresas de la región.
La empresa Innocept de Neuses desarrolló una novedosa mascarilla respiratoria. La idea era una mascarilla agradable al uso, que se pudiese utilizar varias veces, consistente en dos medias cáscaras de plástico entre las cuales se pueden colocar diversos elementos filtrantes. Las ventajas: el filtro de la mascarilla respiratoria no queda directamente sobre el rostro, con lo que es mucho más sencillo respirar, si se compara con las mascarillas provisionales de tela. Además, la mascarilla respiratoria fabricada en grandes cantidades permite costes de fabricación más económicos. Se colabora con el medio ambiente, ya que no se desecha la máscara completa. Para acelerar el proceso de desarrollo, en un abrir y cerrar de ojos elaboramos cinco prototipos con la tecnología HP Multi-Jet Fusion en la empresa Hofmann – Ihr Möglichmacher, de Lichtenfels. Dos semanas y media después, el producto estaba desarrollado. Innocept solicitó el registro de la patente. Además, la empresa Verpa de Weidhausen desarrolló una vestimenta protectora sencilla en película plástica. La empresa Hofmann – Ihr Möglichmacher produjo diversos objetos para equipamiento protector del rostro, o bien válvulas para la respiración asistida de pacientes en cuidados intensivos, y las puso a disposición de manera gratuita. La tecnología de HP Multi-Jet Fusion nos permitió una fabricación individualizada pero económica de productos que se necesitaban con urgencia en plazos ínfimos.
Ahora bien, un proceso digital presenta otra ventaja esencial: los datos de impresión STL se pueden utilizar como base integral en varias impresoras, independientemente del fabricante. Los ponemos a disposición de manera centralizada, a través de Bayern Innovativ. Como institución neutral del Estado Libre de Baviera, Bayern Innovativ concentra conocimiento relevante de expertos, en particular para pequeñas y medianas empresas, para que puedan implementar con éxito sus innovaciones. Al mismo tiempo, la Escuela Superior de Coburgo, socio del FADZ, produce más de 120 mascarillas protectoras de rostro para el hospital de Coburgo. En la actualidad, estos materiales de protección están a la venta. En el futuro se podrá crear una cadena de suministros just-in-time.
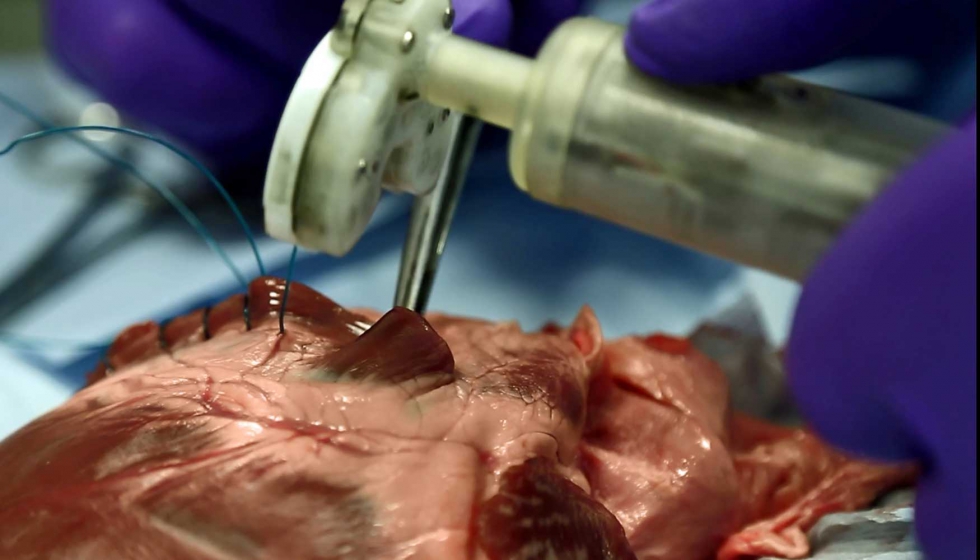
Automatismo para sutura de Sutrue (UK) en una operación cardiaca. Foto: Sutrue.
Ejemplo de válvulas de Venturi poliméricas impresas en 3D para equipos de reanimación en Italia
Ya en marzo de 2020, la UE reaccionó a la pandemia de SARS-CoV-2 con una solicitud a la industria europea de fabricación aditiva. La carencia de materiales de protección como mascarillas N95, máscaras, viseras o batas, así como equipos de reanimación y respiradores artificiales en el sistema sanitario, y la alta dependencia de las cadenas de suministro globales, debían combatirse con estrategias de impresión 3D. Se involucraron importantes proveedores como Draeger de Lübeck, y también muchos otros fabricantes de máquinas y equipos, al igual que numerosas empresas de procesamiento procedentes de los más diversos sectores. Muchas empresas jamás habían fabricado productos semejantes. Se improvisó mucho. Por ejemplo, era posible imprimir una protección facial transparente como el vidrio en unas 10 horas, pero en vista de las tecnologías convencionales casi no tenía sentido, por su ineficiencia de costes y falta de escalabilidad. La AM tiene mayor nivel de detalle. Un ejemplo son las válvulas de Venturi en los equipos de reanimación y respiradores artificiales. Aquí se trata de elaborar en impresión 3D una pieza de desgaste de fabricación convencional. Esto sucedió en el hospital de Brescia: la empresa Fab Lab de Milán instaló una impresora 3D de polímeros en el propio hospital. Se escanearon válvulas preexistentes y se imprimieron nuevas válvulas. Así, los equipos de reanimación continuaron funcionando. Posteriormente, la empresa italiana Lonati Spa asumió la producción en serie por proceso de fusión láser de lecho de polvo de polímeros, para imprimir las partes de poliamida y abastecer a los hospitales italianos. Estos son solo dos ejemplos: la empresa Isinnova, de Lombardía, suministró válvulas de Venturi impresas en 3D al hospital de Chiari. En nuestro sector, esto se denomina ‘repuestos a demanda’. Un elemento esencial, cuando ya no existen soluciones relativas a la forma o cuya adquisición necesita demasiado tiempo. Pero en este contexto, también es importante mencionar la reingeniería. Cuando se construye un repuesto de nuevo, entonces a partir de un componente de montaje de varias piezas se puede lograr de un solo golpe un componente impreso en 3D sin complicaciones de montaje.
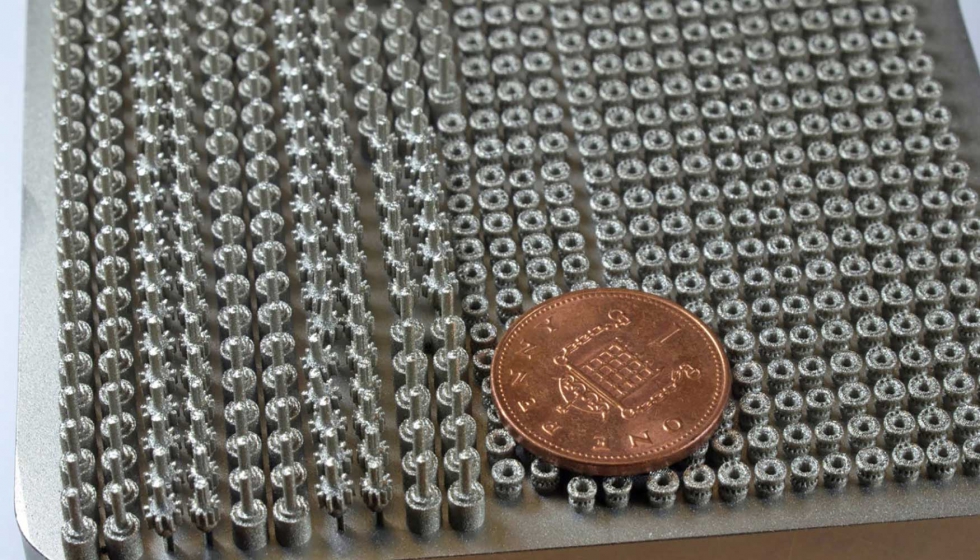
Diversos componentes 3D para el automatismo de sutura de Sutrue se generan en paralelo sobre una placa. Foto: Sutrue.
Conocimientos y factores de diseño
Las construcciones biónicas son posibles gracias a la impresión 3D en metal. Ofrecen una construcción ligera, densidades selectivas y superficies definidas. Esto constituye una ventaja esencial para los implantes. No obstante, se debe tener en cuenta: una geometría en 3D no debe ser idéntica a un componente convencional. Cuando elaboro una copia, muchas posibilidades quedan desaprovechadas. La geometría libre, la optimización de recursos o la reducción a muchos menos componentes en un conjunto en tecnología one shot. Naturalmente, las cadenas de procesos digitales y los valores empíricos de 3D son de importancia elemental para los usuarios. Tenemos por delante una importante tarea: la formación y perfeccionamiento en impresión 3D como factor clave. Solo cuando se difunda el ‘saber digital’, todavía muy reciente, y encuentre su lugar junto a las tecnologías de fabricación convencionales, entonces se acelerará su difusión en la industria. Es necesario ampliar este saber, puesto que los actuales expertos en 3D son autodidactas procedentes de diversos perfiles profesionales. Una piedra angular de la tarea educativa es el principio MINT, un acrónimo que alude a los contenidos educativos de las matemáticas, informática, ciencias naturales y tecnología. Además de la tecnología de procesos en 3D propiamente dicha, con este enfoque interdisciplinario MINT se transmite el saber integral y completo. Esto incluye además 5G, inteligencia artificial (AI), robótica o mecatrónica, por mencionar solo algunas palabras clave. Ya sea que lo encaremos como en el Centro de Investigación y Aplicación de Nuevas Tecnologías Digitales (FADZ) o en las escuelas superiores, además de la formación académica debe tener lugar una capacitación práctica, que conduzca a la formación en oficios. La temática también debe estar presente en las escuelas de artes y oficios, y además en los cursos de formación y especialización. Así, el FADZ también se orienta hacia las escuelas de oficios, pero no solo a ellas: talleres de industria con el apoyo de las cámaras de comercio e industria o de los gremios de oficios, e incluso las propias escuelas están en el foco, en lo que refiere a interesar a la ‘generación impresión 3D’ en estos perfiles profesionales.
Estado de la técnica en el ejemplo de los implantes craneales
La inteligencia artificial, la digitalización y la automatización son pilares de la estrategia de la Industria 4.0. Son temas que también dan alas a la fabricación aditiva. En el futuro influirán a la impresión 3D, la acelerarán y la desarrollarán de manera innovadora, ayudando a llevarla a la superficie. En la tecnología sanitaria, con sus soluciones a menudo específicas para el paciente, esto juega un papel secundario. No obstante, para un producto digital todavía hay mucho margen. Así, en un implante craneal el operador puede mandar elaborar un implante con máxima precisión sobre la base de la imagen de rayos X y de la utilización de los datos STL. Con una superficie porosa definida se procura que el implante sea aceptado de manera óptima por el tejido humano. La clave para los médicos experimentados es el diseño de los implantes en los lugares de transición con el cráneo. Con su diseño, el componente se puede colocar con mayor rapidez y se reducen los riesgos operatorios. Con los rápidos avances en la curación se beneficia el paciente, quien además gana en calidad de vida. La tecnología AM contribuye de manera esencial a la medicina con una mejora en la calidad de vida del paciente.
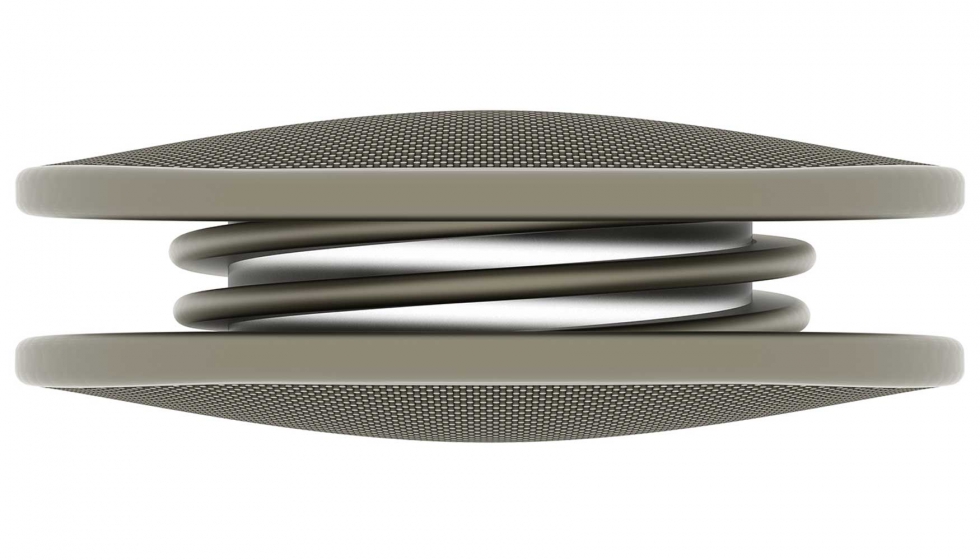
Las prótesis de discos 3D en la columna vertebral mejoran la movilidad; garantizan 360º de libertad de movimiento al paciente y, con su dimensionado, se adaptan exactamente a la anatomía de la columna vertebral de la persona. Foto: Tsunami.
Estado de la técnica en la interacción entre hardware y software
Las máquinas y equipos de AM consiguen aprovechar los potenciales de la construcción, cadena de procesos digitales y la interacción entre hardware y software. En lo que respecta al hardware, hasta ahora eran más importantes los espacios de construcción y las tasas de construcción (velocidades de impresión). En la actualidad, los espacios de construcción para el proceso de impresión de lecho de polvo de metal van de 1 cm³ a unos 800 cm³. Los espacios de construcción estándar son de 187 cm³, y en multiláser son de 125 cm³. Hoy en día, estas dimensiones de espacios de construcción son absolutamente suficientes para cada aplicación médica. También se han incrementado notablemente las velocidades de construcción, gracias al enfoque multiláser. Hoy en día, con varios rayos láser de 1.000 W las tasas de construcción son de hasta 40/50 cm³/h. En el futuro, esto se podrá incrementar gracias a las tecnologías de inyección aglutinante (Binder Jetting). Este proceso, desarrollado por el Instituto de Tecnología de Massachusetts (MIT), será importante para aplicaciones sencillas con determinados márgenes de tolerancia. En la impresión 3D de inyección aglutinante, las piezas se construirán por capas, a modo de ‘piezas en bruto’. A partir de datos 3D se calcula la geometría a generar para cada una de las capas. Al imprimir en 3D se aplica sobre una mesa de altura regulable una capa de polvo o granulado y se adhiere con aglutinantes a los puntos importantes para la pieza. Esto es parecido a lo que sucede en una impresora de chorro de tinta normal. Por regla general, se debe tener en cuenta: el desarrollo de los últimos 10 años resultó también en una gran expansión de los tamaños de lote. Cada vez más, el aseguramiento de la calidad y la automatización van ganando en importancia. El aseguramiento de la calidad es una función esencial del software. Y no solo eso. El software asume una función de dirección durante el montaje del componente en 3D. Controla la preparación de datos del componente, controla las tareas constructivas, propone una estrategia de iluminación y elección de parámetros, también para superficies y densidades. El software adapta de manera óptima la orientación del componente en el espacio de construcción, así como las necesarias estructuras de apoyo (estructuras de soporte). Para asegurar la calidad, posibilita también simulaciones de transferencia térmica (simulación térmica) y una simulación de retardo (simulación mecánica) en base a la densidad o espesores de un componente. Y por si esto fuera poco, el software permite un ‘gemelo digital’ (digital twin). Los parámetros de proceso optimizados para el componente y registrados se pueden almacenar 1:1. Así, resulta una máxima reproducibilidad, como sólo es posible con un componente digital.
Estado de la tecnología AM como estrategia integral de producción
Los temas de la automatización y cadena de procesos digitales completan el desarrollo. La automatización implica eliminar la mayor cantidad de perturbaciones, asegurar un proceso bajo atmósfera inerte, y concebirlo rápidamente automatizado. Esto comienza con la preparación en contenedores, pasando por el propio proceso de montaje del equipo de impresión en 3D, hasta el trabajo posterior automatizado, como eliminación de soportes, tratamiento térmico posterior o tratamiento superficial. El enfoque máximo de la automatización es continuo, desde el polvo hasta el componente terminado, sin ninguna actividad manual. Entretanto se ha ampliado la cadena de procesos digitales, desde el principio una exigencia, pero también una necesidad para lograr el aprovechamiento de los potenciales de la AM por parte de los fabricantes de máquinas y equipos. Un punto clave es la obtención directa de datos STL digitales. Así, hoy en día se pueden utilizar escáneres para lograr los datos de manera directa. Esto puede ser directamente en el paciente, o también con componentes convencionales que se deban fabricar por AM. Ya están disponibles escáneres dentales para uso de los odontólogos por menos de 10.000 €. Pero la cadena de procesos digitales también tiene lugar en otra dimensión. La palabra clave son las modernas fábricas AM con cadenas de procesos digitales continuos para el control de la producción y los procesos. Este moderno tipo requiere un flujo de datos en el suministro y preparación de materiales, en la producción de componentes, en el procesamiento posterior y en la logística interna de fábrica, hasta los sistemas de transporte sin conductor (tecnología FTS). Esta idea nos vino a la cabeza hace unos 5 o 6 años: el concepto ‘AM Factory of Tomorrow’. Va encontrando cada vez más cabida en el mundo de los usuarios de la AM, puesto que tiene importantes elementos que añaden valor y que determinan la competitividad.
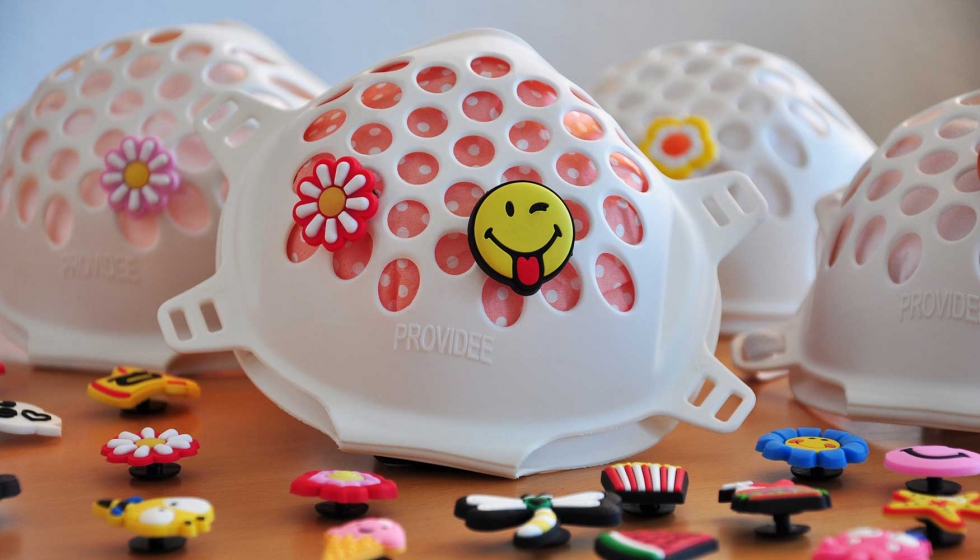
Mascarilla respiratoria para el hospital de Bamberg. Foto: Innocept.
Perspectivas de futuro de Pro Digital
Pro Digital significa: tendremos mayores tasas de construcción gracias a las tecnologías multiláser e inyección aglutinante, mayores tamaños de componentes, así como mejoras en la iluminación, aseguramiento de la calidad y nuevos materiales. Paso a paso, la tecnología evoluciona en efectividad y eficiencia, aun cuando las etapas del desarrollo resulten más moderadas que hace 10 o 20 años. Ante nosotros tenemos seguramente nuevos productos biónicos, nuevos diseños, nuevos materiales, productos más sostenibles y una ampliación de las aplicaciones. Desde hace años, en los Países Bajos se imprimen materiales de construcción, y una nueva tendencia es la impresión de calzado. Pero además de la tecnología, las personas son cada vez más un factor en el diseño. Mientras que muchas empresas fueron pioneras, la mayoría tiene sus reservas: en 2019, el 71% de las empresas indicaron que, al seleccionar métodos de fabricación alternativos, el mayor factor de impedimento para la impresión 3D era la falta de conocimiento especializado. Y como una contradicción, un 79 % de las empresas indicaron que, como mínimo, se habrán de duplicar las piezas que se obtengan por impresión 3D en los próximos 3 a 5 años (fuente: encuesta de Jabil en 2019). En la práctica, esta contradicción significa: no sabemos cómo, pero sabemos que será más importante. Las empresas reconocen que algo se está moviendo, pero son algo reticentes. Yo deduzco que en el futuro deberá haber un plus de «saber digital» para poder plasmar esta transformación de manera concreta. La formación y perfeccionamiento de la ‘generación impresión 3D’ será la clave decisiva para el futuro. La formación y perfeccionamiento en AM ofrecerá ventajas locales en todo el mundo, puesto que AM es una opción importante para desarrollar y fabricar productos a nivel local. Y esto lo afirmo con todo el trasfondo de la discusión acerca de las largas cadenas de suministro con China. La AM posibilita una fabricación local, cercana, a demanda. Se hacen innecesarios los largos recorridos de transporte y las dependencias. Las fábricas AM tienen estructuras de costes comparables a lo largo y ancho del planeta. La propia tecnología preserva recursos, pero, además, el enfoque local es más ecológico. Es por ello que necesitamos centros AM locales, ‘hot spots digitales’. Para ello, necesitamos enriquecer la tecnología con desarrolladores, montadores, diseñadores y usuarios que comprendan y puedan aplicar la impresión 3D. Solo así podremos superar las estrategias de fabricación heredadas para llevarlas a las nuevas posibilidades de la impresión 3D y aprovechar las futuras oportunidades de innovación. Para muchas empresas y sectores, el 3D se convertirá en factor de competitividad.
Una última reflexión a modo de conclusión
Para concluir mi mirada hacia el futuro de la AM, no quisiera olvidarme del sector de los consumidores de 3D: como en otros sectores del hardware, también aquí existe un mercado para impresoras 3D industriales y, además, para impresoras 3D para consumidores finales. La empresa inglesa de análisis de mercado Context da un comportamiento del volumen de mercado de 70:30 (%). El mercado nos muestra saltos cuantitativos: una moderna impresora 3D para consumidores finales cuesta hoy unos 1.000 €. Con una calidad comparable de componentes, quiero resaltar que, a modo de comparación, hace unos 15 años una impresora 3D industrial costaba de 100.000 a 200.000 €. Esto significa que hoy la impresión 3D está pasando de la cima al llano. Una impresora 3D local que actualmente funcione con el proceso HP Multi Jet Fusion, en el futuro será tan normal como una impresora láser de escritorio. Así, es imaginable que, en base a licencias de geometrías, numerosos productos plásticos sean producidos en casa por «personas como tú y yo». Son unas perspectivas de futuro positivas, pienso yo, si en una pandemia como la de SARS-CoV-2 se deben imprimir viseras o mascarillas protectoras. Sin salir de casa. Con datos de internet.
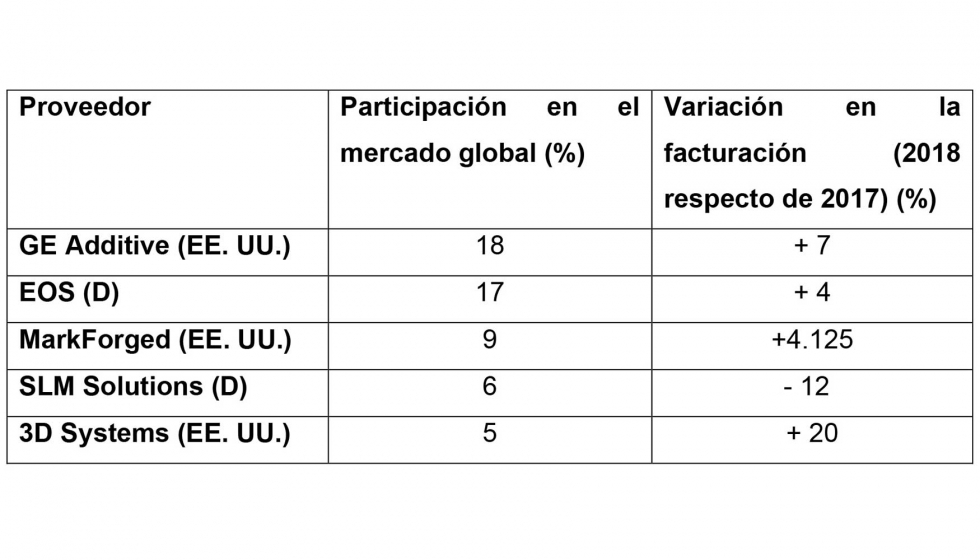
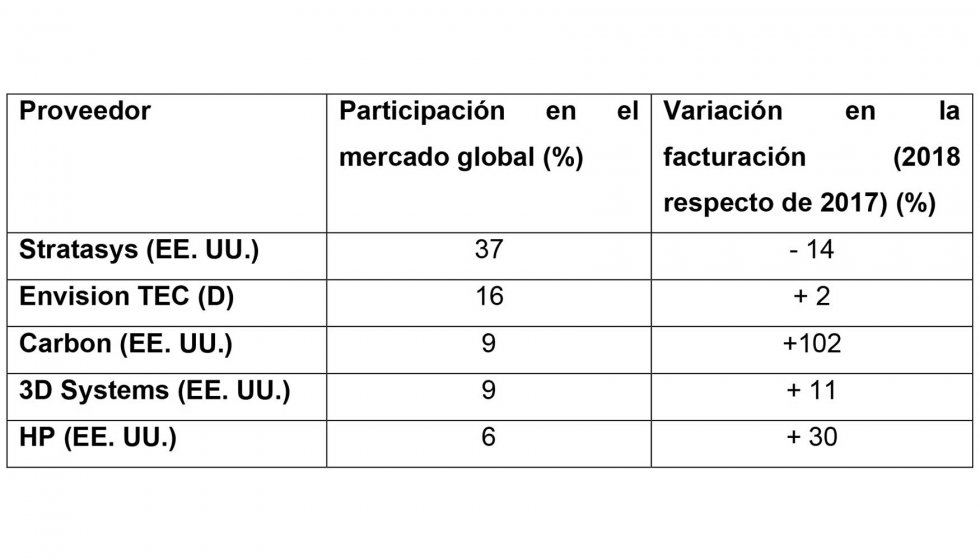
“Ante nosotros tenemos seguramente nuevos productos biónicos, nuevos diseños, nuevos materiales, productos sostenibles y una ampliación de las aplicaciones”
Frank Carsten Herzog
Frank Carsten Herzog (1971) aprobó sus estudios de Ingeniería Mecánica en la Escuela Superior de Ciencias Aplicadas de Coburgo y en 1999 se tituló como Dipl. Ing. (FH) siendo distinguido con el premio IHK (tema: ‘Introducción de nuevas tecnologías de sinterizado en el proceso de rapid tooling’). A partir de sus estudios, Frank Carsten Herzog desarrolló en 1997 la tecnología LaserCusing: la fusión láser de lecho de polvo para metales. Sobre la base de su tesis de grado pudo presentar dos solicitudes de patentes básicas del proceso de fusión por láser y, en el año 2000, fundó, junto con su esposa, la empresa Concept Laser GmbH. En su carácter de socio, presidente y director gerente de Concept Laser y miembro del consejo consultivo de GE Additive, Herzog trabajó de manera intensiva entre 2016 y 2019 en la transformación de Concept Laser GmbH con su tecnología LaserCusing hacia una empresa de escala global.
En 2019 fundó el Centro de Investigación y Aplicación de Nuevas Tecnologías Digitales (FADZ, por sus siglas en alemán) en Lichtenfels/Alemania. Como coautor de esta iniciativa y pionero de la tecnología aditiva, Herzog continúa con sus esfuerzos en pro de la consagración de la tecnología de la impresión 3D en la industria, los oficios y el comercio. En su condición de gerente del HZG Group, Coburgo, impulsa la creación en especial en el área de las nuevas tecnologías digitales.
Con más de 300 solicitudes de registro de patentes, Frank Carsten Herzog es uno de los precursores de la moderna impresión 3D en la industria del metal.