Optimización del proceso de electroerosión por hilo mediante técnicas y herramientas de la Industria 4.0
El proceso de corte mediante electroerosión por hilo (WEDM) siempre se ha caracterizado por conseguir tolerancias ajustadas en las piezas fabricadas de geometrías complejas. Sin embargo, los requerimientos cada vez más exigentes planteados por sectores como el aeronáutico han potenciado la investigación para la minimización de errores dimensionales. Un reto del proceso de WEDM es el corte de geometrías complejas o con cambios de espesor, que puede ser atacado desde este enfoque con excelentes resultados. En este trabajo, por tanto, se realiza el paso previo necesario para utilizar las técnicas características de esta cuarta revolución industrial y aplicarlas en el corte por electroerosión, por ser un proceso de naturaleza estocástica en el que se pueden adquirir una gran cantidad de datos. Se demuestra mediante este estudio que el análisis de una gran cantidad de datos es predecesor del uso de las redes neuronales (ANNs) como alternativa para resolver problemas históricamente analizados por expertos EDM, como es la detección de eventos durante el proceso de corte o el cambio de espesor.
1. Introducción
El proceso de corte mediante electroerosión por hilo (WEDM) siempre ha sido conocido por conseguir tolerancias ajustadas en sus piezas, caracterizándose por poder obtener geometrías complejas con cambios bruscos de dirección o radios pequeños, siendo esta mejora de la precisión una de las tareas más importantes a cumplir por los grandes fabricantes de este tipo de maquinaria [1-5]. Sin embargo, existen cada vez necesidades más exigentes por parte de sectores como el automovilístico o el aeronáutico [6] impulsadas, a su vez, por el cambio drástico en el paradigma industrial de esta nueva revolución que se caracteriza por la conectividad, la eliminación de defectos [2] y el tratamiento de grandes cantidades de datos.
Dicho cambio se refleja en la figura 1, donde se muestran las principales líneas de investigación sobre electroerosión por hilo durante el año 2016. La investigación del proceso y la mejora de las máquinas representan aproximadamente un 20 % de los trabajos publicados [7,8], y el análisis de los parámetros a utilizar en función de los nuevos materiales que pueden erosionarse y el estudio de las superficies y su resistencia a fatiga adquieren una importancia similar [9,10]. Asimismo, el estudio de la temperatura y la transferencia de calor durante el proceso y el análisis de las descargas apenas representan un 7 % del total [11,12]. Los artículos no clasificados y los que tienen relación con el láser, la soldadura y la Inteligencia Artificial (Artificial Intelligence, AI) [13] agrupan a la otra mitad de trabajos de este gráfico.
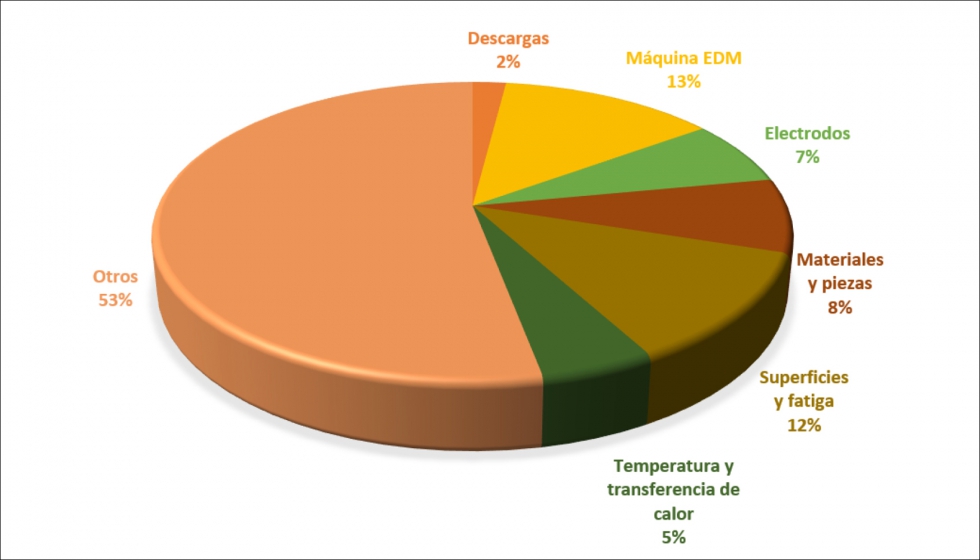
Figura. 1. Clasificación de artículos durante 2016 en función de las principales líneas de investigación en electroerosión por hilo (Fuente: ScienceDirect).
Históricamente, el primer grupo de la clasificación anteriormente mencionada ha tenido una gran relevancia, puesto que una de las necesidades a abordar por este proceso es la de caracterizar y disminuir la deformación y vibración del hilo. La importancia de minimizar este movimiento radica en que estos efectos provocan una pérdida de precisión, sobre todo en los cambios de dirección y en el corte de aristas vivas [14-16]. Por esta razón ha sido una de las tareas sobre las que más se ha investigado a lo largo de los años. Así, existen diferentes trabajos en los que se modelan y cuantifican las fuerzas [11] que toman parte dentro del proceso, modelos matemáticos [14,17] y modelos experimentales [18] que intentan representar el movimiento del hilo.
Sin embargo, a pesar de los numerosos esfuerzos y estudios realizados, todavía no ha sido explicado el comportamiento del hilo en su totalidad. Es por este motivo que, en un trabajo anterior [19,20], se presenta un estudio para la caracterización del error en círculos de diferente radio, con el fin de proponer una nueva metodología experimental para la medición directa del wire-lag o retraso del hilo.
Por otro lado, se ha contemplado que el uso de las redes neuronales se ha asociado tradicionalmente a aplicaciones de las Técnicas de la Información y Comunicación (Information and Communication Technologies, ICT) y el procesamiento de imágenes [21]. Sin embargo, dado el potencial de estas, pueden aplicarse a otros campos, como es el de la fabricación y el mecanizado. Precisamente es de lo que trata esta cuarta revolución industrial: aplicar técnicas de analítica de datos en fabricación, aprovechando la conectividad y las posibilidades de acceder a los mismos (Smart CNC., sensores …). Existen trabajos de aplicación de redes neuronales en procesos de torneado o rectificado a lo largo de los últimos años, incluso estudios en los que se propone su uso para predecir la vida de la herramienta [22-24].
Por lo tanto, una vez visto el buen resultado del empleo de las redes neuronales en el campo de fabricación y el mecanizado, se propone su uso para la mejora de la precisión en el proceso de la electroerosión por hilo e, incluso, para la detección de eventos durante el corte. Puesto que estas técnicas tienen una enorme capacidad para manejar y analizar gran cantidad de datos, el uso de las señales obtenidas del proceso de electroerosión para tal fin parece algo factible.
Se puede resumir el objetivo principal de este trabajo en demostrar la influencia de la Industria 4.0 y realizar el trabajo previo tan necesario para poder aplicar sus herramientas en los procesos industriales, más concretamente en WEDM, y la posibilidad de mejorar aspectos concretos de este mediante el uso de técnicas experimentales y de analítica de cantidades masivas de datos, planteándolas como
alternativa a los modelos teóricos ya estudiados a lo largo de los años, tal y como se ha podido ver en este apartado para otras aplicaciones.
2. Estimación del espesor de la pieza
A lo largo de este apartado se describirá la metodología experimental de los ensayos realizados y el cálculo de los parámetros necesarios para el establecimiento del espesor, con lo que se obtendrán unos resultados los cuales pueden analizarse para, finalmente, intentar predecir el cambio de espesor con antelación.
2.1. Metodología experimental
En los próximos párrafos se detallan los ensayos llevados a cabo para analizar el paso previo a la factibilidad del uso de las herramientas de inteligencia artificial en la mejora del proceso y la precisión de WEDM, mediante el uso de cantidades masivas de datos para la resolución de problemas típicos en este proceso de corte, comprobando si puede determinarse el espesor durante el proceso de corte.
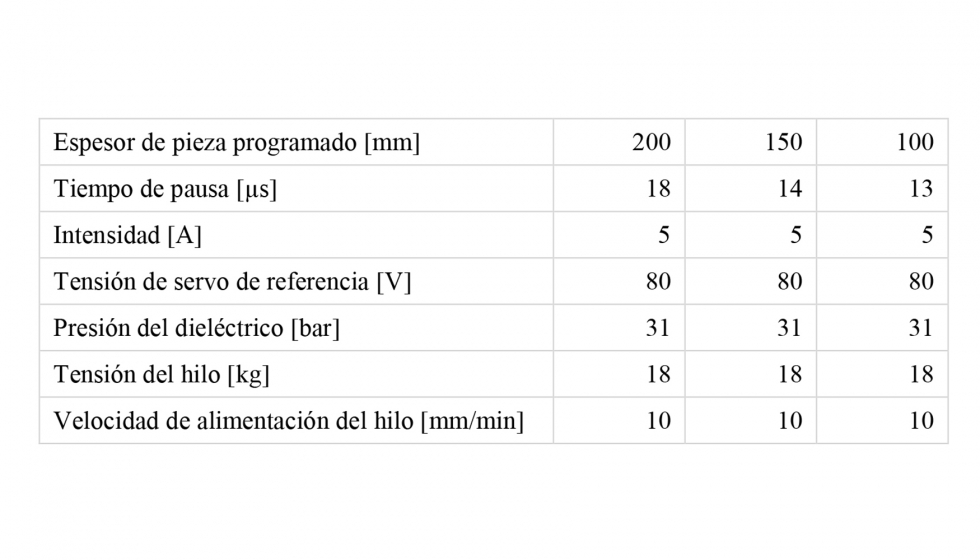
Se ha utilizado una máquina de electroerosión por hilo ONA AX3. El hilo empleado es el más habitual: latón sin recubrimiento (CuZn37) de 0,25 mm de diámetro, con una resistencia a rotura de 900 N/mm2 y un límite elástico del 1 %, y los parámetros eléctricos pueden verse en la tabla 1 para condiciones de desbaste. Asimismo, el material utilizado es un acero de herramientas AISI D2 (ISO 160CrMoV12) templado y revenido de 62 HRc. Por otra parte, la medición de las probetas se ha realizado con una máquina de medir por coordenadas (CMM) Zeiss 850.
Para la adquisición de las descargas del proceso de WEDM se ha utilizado osciloscopio de alta frecuencia (Tektronix DPO 5034B) y una sonda de tensión (Tektronix TMDP0200), con las condiciones mostradas en la tabla 2. Teniendo en cuenta la naturaleza del proceso WEDM, se han obtenido secuencias de descargas en periodos de tiempo que se consideran suficientemente largos como para poder registrar potenciales eventos que tuvieran lugar durante el corte.
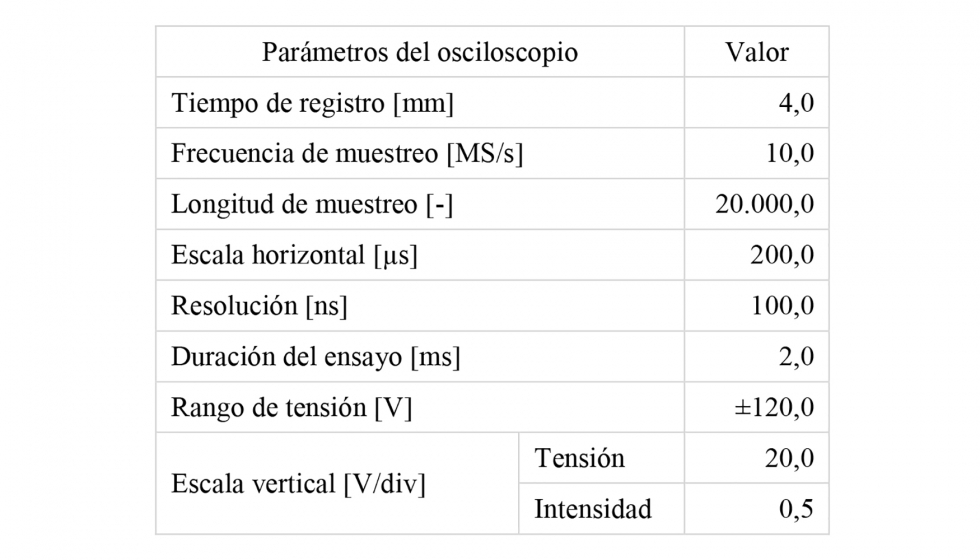
Una vez descritas las máquinas y herramientas de adquisición de datos que se han utilizado, se procede a detallar los ensayos llevados a cabo y, posteriormente, los resultados obtenidos de estos.
2.2. Cálculo de los parámetros para el establecimiento del espesor durante el corte
Derivado de un trabajo anterior [27] donde se ha demostrado que existe una degradación del proceso visible con el registro de las señales adquiridas mediante un osciloscopio [12], se ha planteado el estudio de otra solución que ya ha sido estudiada anteriormente por otros autores: la estimación del espesor de pieza [25]. La detección del espesor en el corte por WEDM parte de la hipótesis de que puede obtenerse mediante la aplicación de la Ecuación 1, que es una relación entre la tasa de arranque (U) del número total de descargas (N) con el espesor (h) y la velocidad de corte (v).

Los parámetros óptimos a emplear durante el proceso de corte se establecen desde la tecnología proporcionada por la compañía fabricante de este tipo de máquinas, teniendo en cuenta el binomio hilo-material y, además, el espesor de pieza, la cual se denominará a partir de ahora espesor programado. Obteniendo, para un corte de desbaste con condiciones de presión del fluido dieléctrico de 17 bar, el número de descargas en un determinado intervalo de tiempo, junto con la velocidad media del intervalo en el que se han registrado las mismas, puede despejarse de la ecuación anterior la tasa de arranque superficial por descarga (U) para dicho espesor.
Sin embargo, en piezas de espesor variable no siempre se realiza el corte en estas condiciones de presión (17 bar) y con un espesor real coincidente con el programado, por lo que la ecuación anterior se convierte en una ecuación matricial con la siguiente estructura, en la cual se han de diferenciar las descargas en función del tiempo de ionización, en lugar de utilizar el número total de las mismas (Ecuación 2):
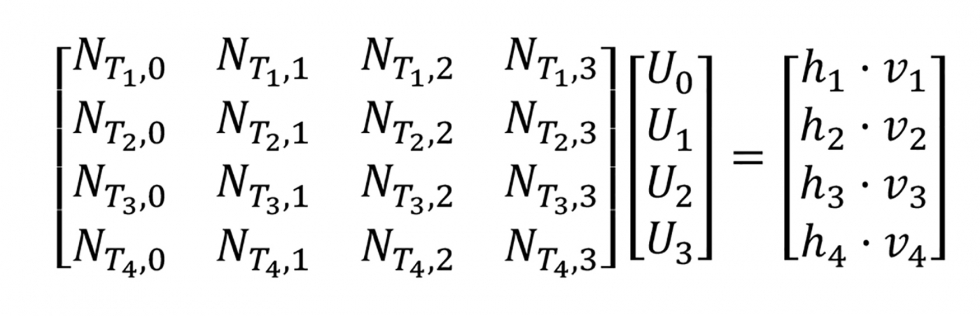
Donde 𝑁𝑇1, 𝑗 representa el número de descargas con un tiempo de ionización mayor a 10 μs, 𝑁𝑇2, 𝑗 las que cuyo tiempo de ionización es menor a 3 μs, para cada uno de los espesores ℎ𝑗 en los que se realizan los cortes.
Puesto que los valores de U no pueden ser negativos, es necesario establecer como condiciones de contorno que dichos valores deben ser mayores que cero. Una vez establecida esta relación, se puede realizar el cálculo de los valores de U (𝑈0, 𝑈1, 𝑈2 𝑦 𝑈3) para diferentes espesores programados, de forma que la metodología queda completamente definida.
Se lleva a la práctica este procedimiento teórico mediante el corte de una pieza de acero AISI D2 de geometría compleja, representada mediante la figura 2, cuyas dimensiones pueden observarse en la tabla 3.
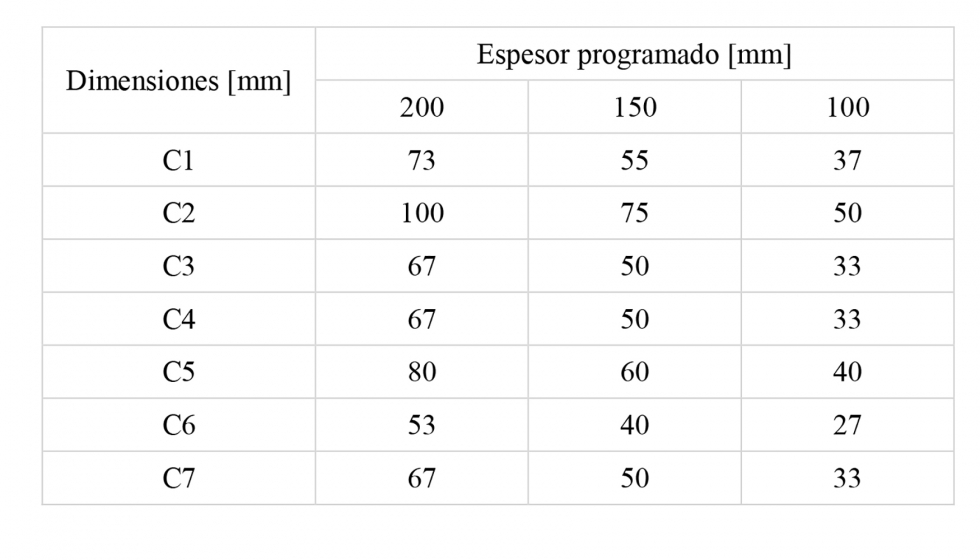
Se ha elegido una geometría compleja, con diferentes cambios instantáneos de espesor y de regiones invariantes del mismo de, al menos, 20 mm de longitud, para que puedan recogerse los datos (4 mm de longitud) en un rango estable y con diferentes condiciones de presión de dieléctrico.
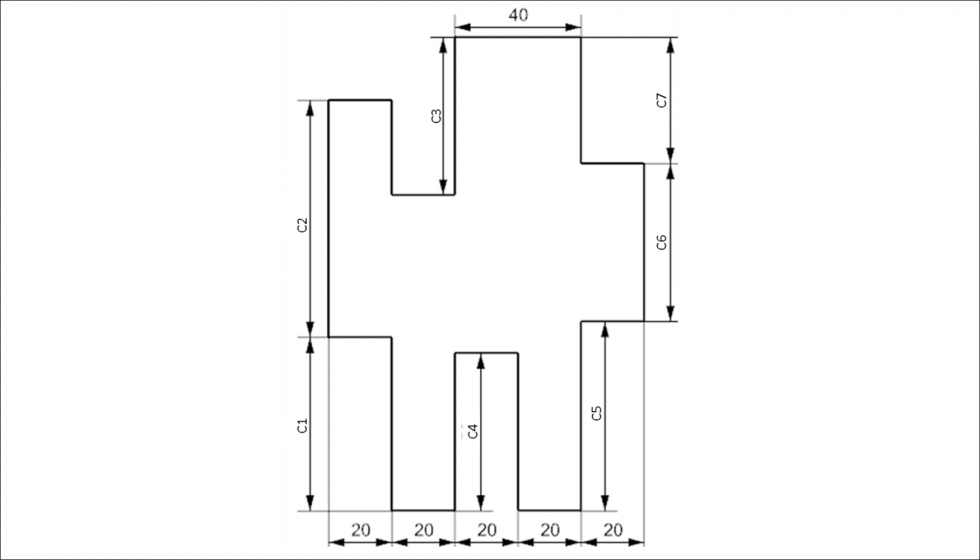
Con estos registros se han calculado la suma de cada tipo de descarga y los valores medios de velocidades para introducirlos en la Ecuación 2, de forma que se obtienen las constantes necesarias para la determinación del espesor para cada espesor programado (ver tabla 4).
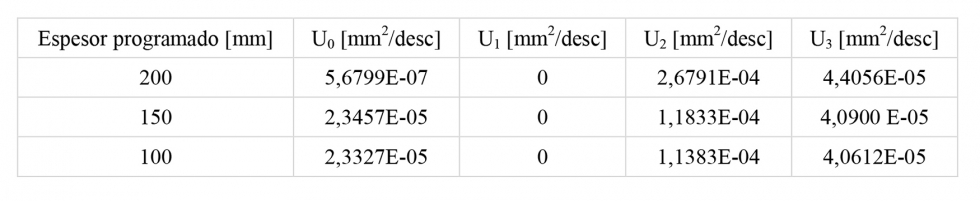
Una vez obtenidos los valores de U se puede calcular el espesor real de pieza mediante la misma ecuación, en la que ahora solo este valor es una incógnita (ver ecuación).

Con esta información se ha generado una aplicación en Matlab en la que, para que funcione correctamente, se debe proporcionar como dato de partida el espesor programado. Así, se representan las siguientes variables:
- espesor real de la pieza con respecto a la posición de las guías
- presión superior e inferior del fluido dieléctrico con respecto a la posición de las guías
- velocidad con respecto a la posición de las guías
- valor instantáneo de las variables anteriores
2.3. Análisis de los resultados
La comprobación de la teoría expuesta en el apartado anterior se corrobora mediante el siguiente ejemplo: se trata de una pieza cuya geometría se muestra en la figura 3, que consta, además de las regiones de 20 mm de longitud en diferentes espesores y condiciones de presión del dieléctrico, de un cambio de espesor progresivo.
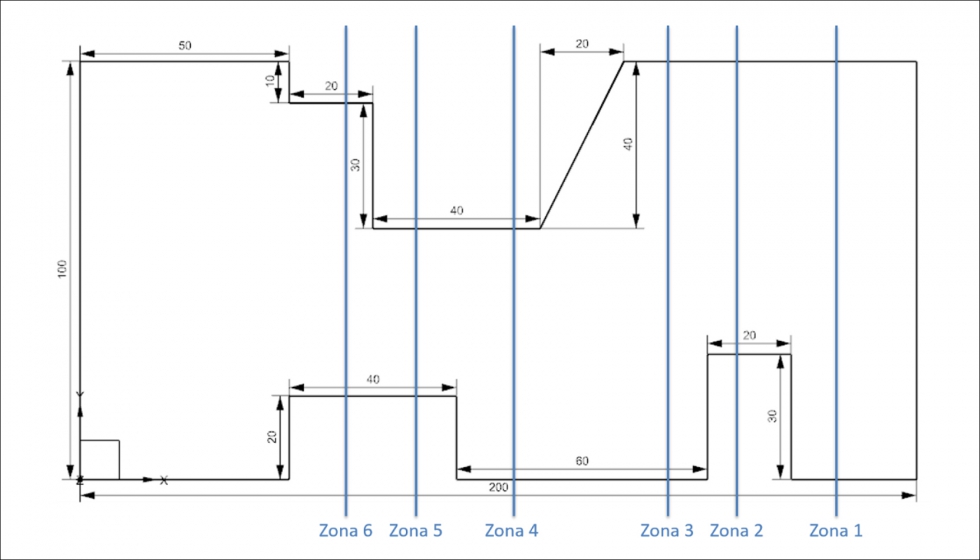
En la figura 4 se muestra la información proporcionada por la aplicación programada en Matlab, donde se puede observar la predicción del espesor (en azul) para este ejemplo con respecto al espesor teórico de la pieza (en rojo), con el fin de visualizar mejor esta comparativa.
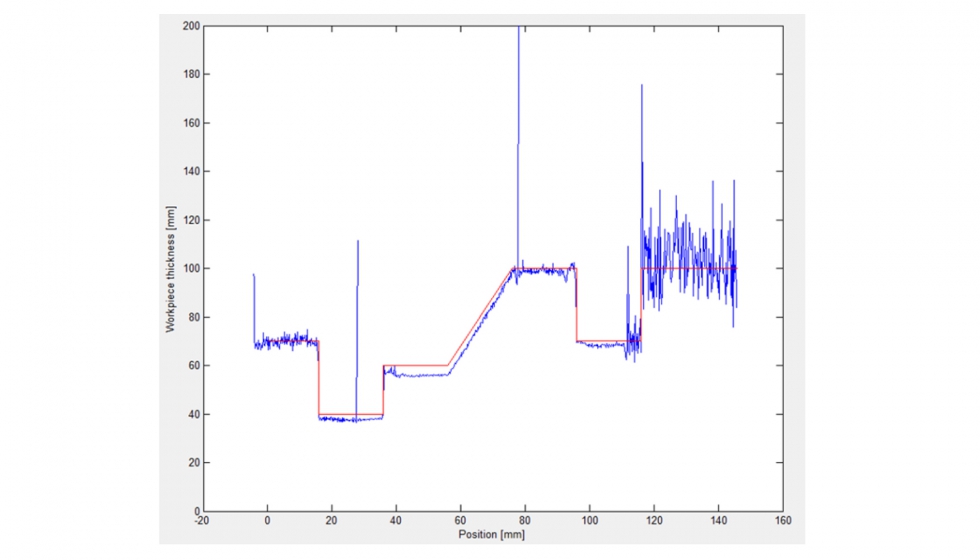
Para comprobar el grado de precisión de la estimación del espesor se comparan los valores medios de espesor de cada zona registrada con el valor teórico o de diseño de la pieza (ver tabla 5). De igual manera, se obtiene el porcentaje de error y se muestra la velocidad media real por zona registrada.
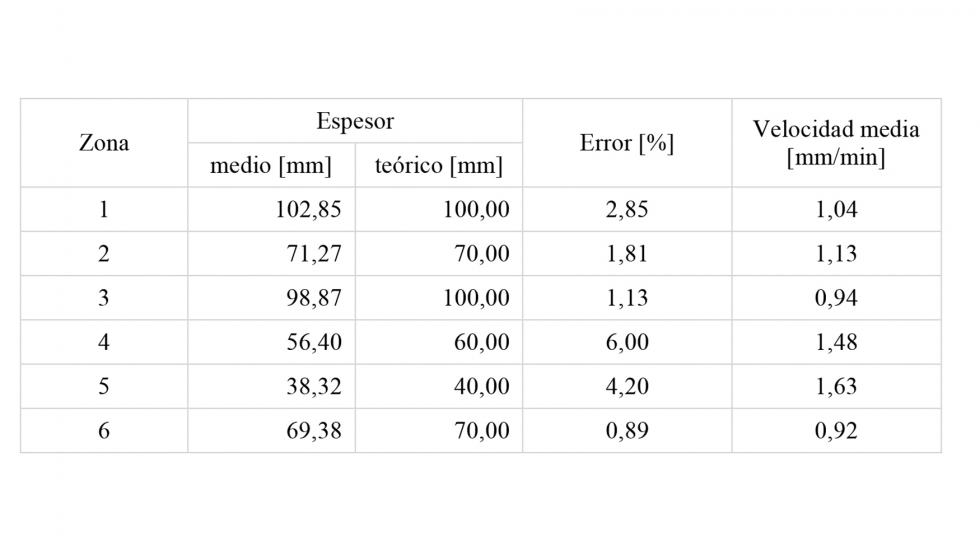
Se puede concluir, por tanto, que el espesor puede determinarse mediante la ecuación 1, con un error menor al 5 %.
2.4. Predicción con antelación del cambio de espesor
El siguiente paso es comprobar si esta estimación del espesor genera información suficiente para predecir su cambio con antelación. Si bien es cierto que la variación de presión del fluido dieléctrico no genera información válida para predecir dicho cambio, como se verá a continuación, el Coeficiente de Variación (CV) sí. Este parámetro se define de la siguiente forma: CV [%]= SD/h¯ · 100
En la figura 5 se muestra de forma conjunta el espesor de pieza predicho en cada momento (en color verde) junto con el CV (en color rojo). Además, redondeados en color azul, pueden observarse los puntos en los que este coeficiente tiene una fluctuación mayor del 10 %. La comparación de cotas entre estos puntos y el cambio de espesor mostrará la antelación con la que puede predecirse el cambio.
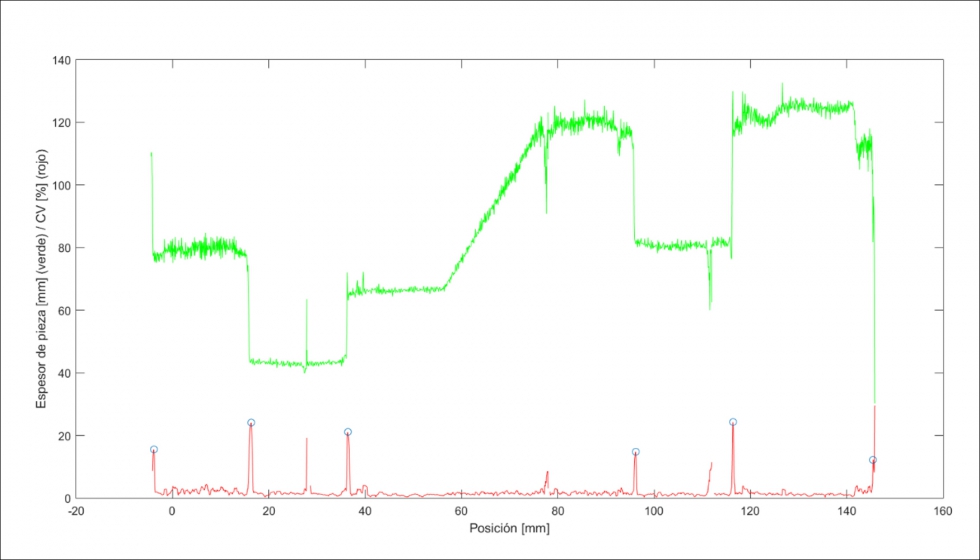
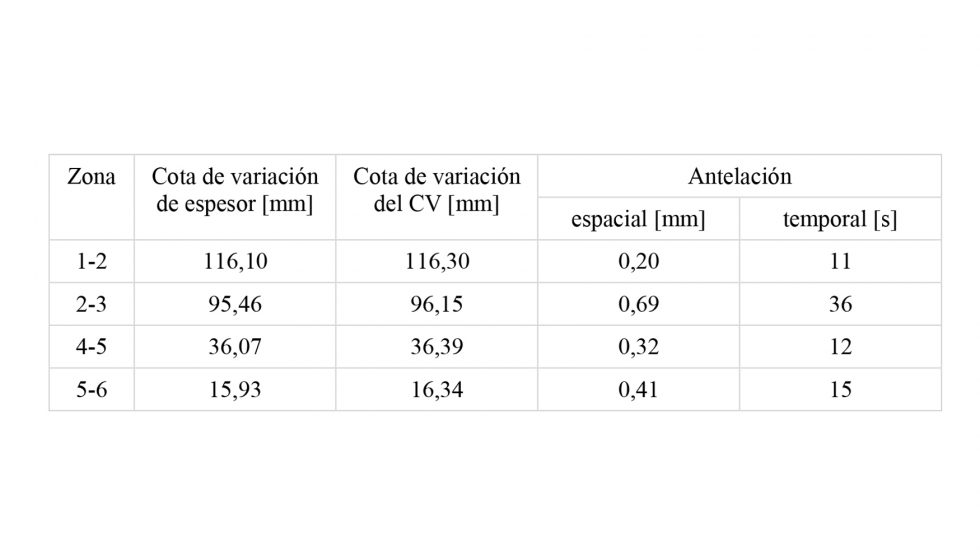
3. Conclusiones
A la vista de los resultados obtenidos, se pueden obtener las siguientes conclusiones:
- La revisión del estado del arte y la práctica industrial muestran la necesidad de avanzar en el desarrollo de la mejora de la precisión en el corte por electroerosión por hilo, puesto que cada vez requieren tolerancias más ajustadas. La Industria 4.0 y sus herramientas ponen de manifiesto que puede ser una alternativa para resolver algunos problemas del sector de la máquina-herramienta, después de haber obtenido un gran éxito en otros campos como es el de las comunicaciones.
- Se ha establecido una ecuación que relaciona la erosión de las descargas con la velocidad y el espesor de pieza, de forma que se puede establecer el espesor en cada punto de corte del proceso con el manejo de una gran cantidad de datos. Para ello únicamente es necesario saber el tiempo de ionización de las descargas.
- Mediante una aplicación programada en Matlab se ha visualizado que el error cometido en la predicción es menor al 5 %.
- Además, con los resultados obtenidos y mediante la misma aplicación, se han analizado diferentes parámetros que puedan predecir el cambio de espesor con antelación. El coeficiente de variación lo hace con una anticipación de, al menos, 7 s, en función del salto de espesor ante el que se enfrenta el proceso.
De este trabajo se deprende que existen nuevas posibilidades en el campo de la fabricación avanzada y las máquinas-herramienta de alto rendimiento, y que una línea futura es aplicar diferentes estructuras de ANNs para cada problema específico, de forma que realicen el trabajo del manejo de una cantidad masiva de datos. Esta línea de investigación será una realidad cuando se disponga de una mayor cantidad de datos, puesto que hoy en día es difícil recopilarlos en procesos de mecanizado.
Referencias
[1] Fanuc, Eeectroerosión por hilo con ROBOCUT http://www.fanuc.eu/es/es/robocut-ib
[2] GF Machining Solutions http://www.gfms.com
[3] ONA Electroerosión S.A. http://www.onaedm.com/
[4] Sodick https://www.sodick.com/products/wire-edm
[5] Mitsubishi Electric, EDM http://www.mitsubishi-edm.de/
[6] ADMAP-GAS project http://ec.europa.eu/research/transport/projects/items/admap_gas_en.htm
[7] Hsue WJ, Liao YS, Lu SS. ‘Fundamental geometry analysis of wire electrical discharge machining in corner cutting’. International Journal of Machine Tools and Manufacture. 1999. Vol. 39-4. p.651-667.
[8] Mori A, Kunieda M, Abeb K. ‘Clarification of Gap Phenomena in Wire EDM Using Transparent Electrodes’. Procedia CIRP. 2016. Vol. 42. p.601-605.
[9] Hinduja S, Kunieda, M. ‘Modelling of ECM and EDM processes’. CIRP Annals – Manufacturing Technology. 2013. Vol. 62. p.775-797.
[10] Klocke F, Klink A, Veselovac D, Aspinwall DK et al. ‘Turbomachinery Component Manufacture by Application of Electrochemical, Electro-Physical and Photonic Processes’. CIRP Annals-Manufacturing Technology. 2014. Vol. 63. p.703-726.
[11] Chen Z, Huang Y, Huang H, et al. ‘Three-dimensional characteristics analysis of the wire-tool vibration considering spatial temperature field and electromagnetic field in WEDM’. International Journal of Machine Tools and Manufacture. 2015. Vol. 92. p.85–96.
[12] Caggiano A, Teti R, Perez R, Xirouchakis P. ‘Wire EDM Monitoring for Zero-defect Manufacturing based on Advanced Sensor Signal Processing’. Procedia CIRP. 2015. Vol. 33. p.315-320.
[13] Shakeri S, Ghassemi A, Hassani M, et al. ‘Investigation of material removal rate and surface roughness in wire electrical discharge machining process for cementation alloy steel using artificial neural network’. The International Journal of Advanced Manufacturing Technology. 2016. Vol. 82-1. p.549–557.
[14] Chen Z, Huang Y, Zhang Z, et al. ‘An analysis and optimization of the geometrical inaccuracy in WEDM rough corner cutting’. International Journal of Advanced Manufacturing Technologies. 2014. Vol. 74. p.917–929.
[15] Sánchez JA, Rodil JL, Herrero A, et al. ‘On the influence of cutting speed limitation on the accuracy of wire-EDM corner-cutting’. Journal of Materials Processing Technology. 2007. Vol. 182-1-3. p.574-579.
[16] Firouzabadi HA, Parvizian J, Abdullah A. ‘Improving accuracy of curved corners in wire EDM successive cutting’. International Advanced Manufacturing Technologies. 2015. Vol. 76. p.447-459.
[17] Puri AB, Bhattacharyya B. ‘Modelling and analysis of the wire-tool vibration in wire-cut EDM’. Journal of Materials Processing Technology. 2013. p.295–301.
[18] Liang JF, Liao YS. ‘Methods to Measure Wire Deflection in Wire EDM Machining’. International Journal Automation Technology. 2014. Vol. 8-3. p.461-467.
[19] Conde A, Sánchez JA, Plaza S, et al. ‘On the Influence of Wire-lag on the WEDM of Low-radius Free-form Geometries’. Procedia CIRP. 2016. Vol. 42. p.274-279. DOI: https://doi.org/10.1016/j.procir.2016.02.285
[20] Conde A, Sanchez JA, Plaza S, et al. ‘Experimental Measurement of Wire-lag Effect and Its Relation with Signal Classification on Wire EDM’. Procedia CIRP. 2018. Vol. 68. p.132-137. DOI: https://doi.org/10.1016/j.procir.2017.12.035
[21] Krizhevsky A, Sutskever I, Hinton GE. ‘ImageNet classification with deep convolutional neural networks’. Proceedings NIPS. 2012. Vol. 25. p.1106–1114.
[22] Mikolajczyk T, Nowicki K, Klodowski A, et al. ‘Pimenov. Neural network approach for automatic image analysis of cutting edge wear’. Mechanical Systems and Signal Processing. 2017. Vol. 88. p.100-110.
[23] Mikolajczyk T, Nowicki K, Bustillo A, et al. ‘Predicting tool life in turning operations using neural networks and image processing’. Mechanical Systems and Signal Processing. 2018. Vol. 104. p.503-513.
[24] Arriandiaga A, Portillo E, Sánchez JA, et al. ‘Virtual sensors for on-line wheel wear and part roughness measurement in the grinding process’. Sensors. 2014. Vol. 14-5. p.8756–8778.
[25] Liao YS, Chuang TJ, Yu YP. ‘On-line workpiece height estimation and its application in servo feed control of WEDM process’. Procedia CIRP. 2016. Vol. 6. p.226–231.
[26] Ciresan DC, Giusti A, Gambardella LM, et al. ‘Mitosis detection in breast cancer histology images with deep neural networks’. Proceedings MICCAI. 2013. Vol. 2. p.411–418.
[27] Sanchez JA, Conde A, Arriandiaga A, Wang J, et al. ‘Unexpected Event Prediction in Wire Electrical Discharge Machining Using Deep Learning Techniques. Materials. 2018. DOI:10.3390/ma11071100
Agradecimientos
Los autores agradecen a Euskampus y a ONA Electroerosión S.A su apoyo en este proyecto.