O papel da digitalização na indústria metalomecânica
Com bits e bytes contra a crise
A indústria está consciente desde há algum tempo do potencial da digitalização. As expetativas e as finalidades são diversas e incluem o desenvolvimento mais ágil de máquinas mais flexíveis, uma maior fiabilidade e uma manutenção (à distância) eficiente, uma melhor documentação, um maior grau de automatização, efeitos de aprendizagem por comparabilidade em massa e capacidade de autoaprendizagem: a lista de possibilidades é infinita. Não são poucas as pessoas que, perante os atuais desafios, gostariam que os processos de digitalização e de ampliação das redes necessárias, como o novo padrão de comunicações móveis 5G, estivessem muito mais avançados: “O 5G Industrial é a porta de entrada para uma rede sem fios integral para produção, manutenção e logística. A alta velocidade de dados, a transmissão ultrafiável e os tempos de espera extremamente baixos, permitirão aumentar significativamente a eficiência e a flexibilidade do valor acrescentado industrial”, afirma Eckard Eberle, CEO da Siemens Business Unit Process Automation. Eberle é responsável pelo centro de testes 5G da Siemens. É certo que não se vê aqui (ainda) qualquer máquina-ferramenta, mas o caminho para a interligação sem fios da fábrica do futuro já está claramente traçado. A Siemens está a testar desde há alguns meses, em Nuremberga, a banda de frequência de 3,7 - 3,8 GHz num contexto industrial real com componentes logísticos, por exemplo, com sistemas de controlo Simatic e dispositivos IO.
Ainda que sem 5G, já é possível observar interessantes aplicações para o suporte digital das empresas de automatização: por exemplo, para detetar a origem dos problemas de qualidade das peças com forma livre, a Siemens aposta num software que recolhe todos os pontos nevrálgicos da cadeia de processos e verifica as estações entre o sistema CAD e as ferramentas utilizadas.
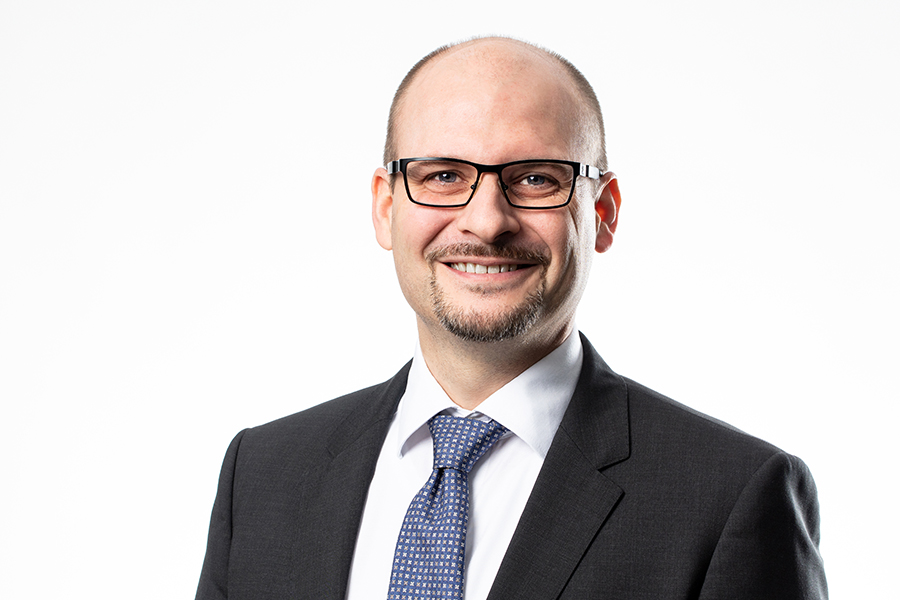
A origem dos erros pode ser muito diversa: a própria edição do sistema CAD, o rendimento do sistema CAM ou do pós-processador, a parametrização dos CNC e os reguladores de acionamento, o sistema mecânico da máquina, as ferramentas e, inclusivamente, o material da peça. Por isso, o programa Analyze MyWorkpiece/Toolpath verifica os dados de saída das diferentes partes do sistema, como o ficheiro STL do sistema CAD, o ficheiro MPF do sistema CAM ou do pós-processador, o registo dos valores nominais de posição e, por fim, a forma como o regulador de acionamento e o sistema mecânico da máquina e da ferramenta implementaram estes dados.
Desta forma, a garantia da qualidade dos dados CAD/CAM, por exemplo, de peças de grande formato, pode ser realizada num passo prévio ao fabrico. Estes sistemas de otimização próximos da máquina-ferramenta estarão em destaque na AMB 2020. A estrela de Estugarda poderá ser as denominadas soluções de edge computing. Estas soluções oferecem capacidade de computação adicional para o suporte digital do fabrico e servem-se, em muitos casos, de algoritmos baseados em inteligência artificial para apoiar o utilizador da maquinaria na realização do seu trabalho.
Em setembro, o tema principal será encontrar caminhos viáveis para sair da crise e preparar o crescimento do volume de negócios e a poupança de custos, em especial, elevando a produtividade e a eficiência de equipamentos e instalações, para o momento em que a carteira de encomendas esteja novamente completa.
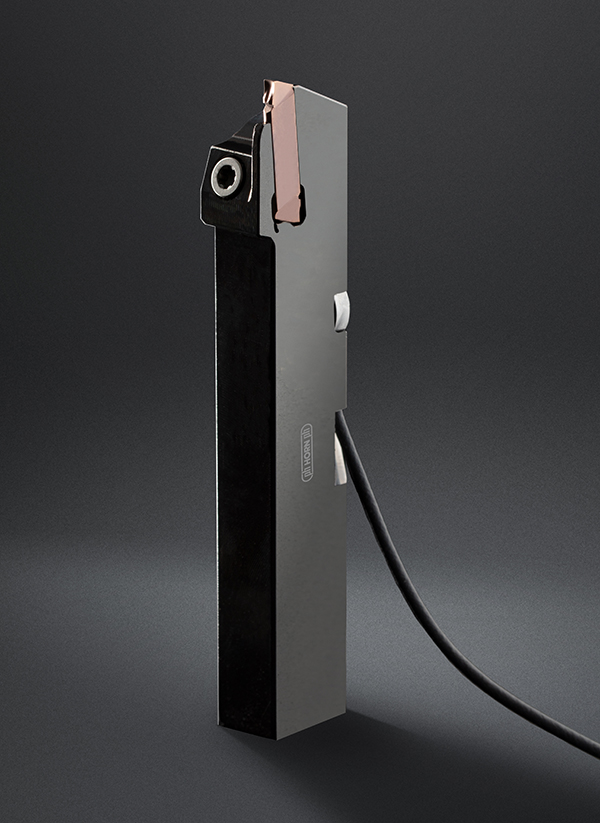
Entre a oportunidade e o desafio
Com soluções novas como o edge computing, a digitalização abre um amplo leque de possibilidades nos heterogéneos contextos de produção do setor da maquinação de metais. Mas também traz consigo inúmeros desafios. Para que a digitalização seja útil numa frente extensa é preciso dispor de padrões, segundo explica Markus Horn, diretor-geral da empresa Paul Horn GmbH: “A VDMA promove este tema no âmbito da GTDE. Saúdo-o com grande satisfação e, como empresa, damos o nosso contributo para este tema disponibilizando os dados necessários”, afirma. GTDE é a abreviatura da associação ‘Graphical Tool Data Exchange-Standard Open Base e.V.’, que atua como centro de competências, representante de interesses e fornecedor de serviços no âmbito do intercâmbio de dados de ferramentas. Os membros e os parceiros da associação são conhecidos fabricantes e utilizadores de ferramentas, empresas de software e a associação profissional VDMA, especializada em ferramentas de precisão. O objetivo consiste em planear o intercâmbio de dados de ferramentas de forma inovadora, utilizando padrões reconhecidos internacionalmente, e em prestar assistência às empresas abrangidas neste âmbito. Para a colocação em prática do intercâmbio de dados de ferramentas e, portanto, do fornecimento unificado dos dados de ferramentas, a associação dispõe de um servidor próprio que permite aos fabricantes participantes solicitar verificações de dados de ferramentas, tais como características das ferramentas, gráficos em 2D e 3D, segundo as normas DIN e ISO, e a sua disponibilização gratuita.
Mas Markus Horn também deixa claro: “O dinheiro ganha-se graças às ferramentas. O digital complementa, mas não substitui. Para nós, enquanto fabricantes de ferramentas, a mensagem é clara: se a ferramenta não oferece a qualidade e a precisão suficientes, a digitalização não serve de nada”, refere. Atualmente existem muitos intervenientes no mercado que disponibilizam serviços digitais: fabricantes de software, fabricantes de maquinaria ou fabricantes de ferramentas, segundo comenta Markus Horn. No entanto, na sua opinião, caso não se disponha de padrões, a implementação destes serviços é normalmente dispendiosa para os clientes e, portanto, a sua utilização é inflexível. “Os produtos adicionais ou serviços digitais apenas só deveriam ser utilizados nos casos em que geram realmente um benefício. Nós também nos centrámos, em relação ao futuro, na própria ferramenta, disponibilizamos os dados correspondentes e oferecemos soluções digitais para os casos individuais nos quais sejam eficazes”, afirma Markus Horn.
Uma vez que a AMB também abrangerá este ano a cadeia completa do processo de maquinação de metais, os visitantes poderão desfrutar de um amplo espetro de técnica clássica em combinação com valor acrescentado digital.
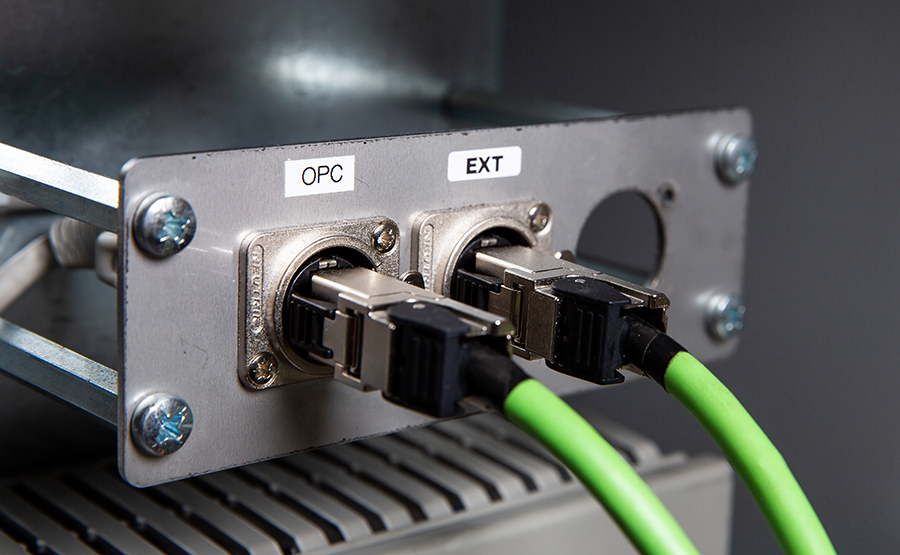
A rede da empresa Paul Horn GmbH utiliza, por exemplo, no âmbito do revestimento, o padrão de comunicação OPC-UA como um importante padrão internacional para a indústria 4.0. Foto: Paul Horn GmbH.
Sensores sensíveis
Um objetivo destacado para o qual as soluções digitais podem contribuir é o de minimizar as rejeições de peças. Assim, a empresa Paul Horn GmbH e o grupo Kistler estão a trabalhar em conjunto na deteção de problemas de maquinação que se manifestam em materiais defeituosos, materiais de corte desgastados ou rutura de ferramentas.
Os especialistas em tecnologia de medição dinâmica registam a pressão, a força, o binário de rotação e a aceleração e desenvolveram uma solução, em estreita colaboração com os engenheiros da Horn, para a supervisão de ferramentas em tempo real em processos de microtorneamento. O sistema Piezo Tool System (PTS) é constituído por um sensor de força que se insere na ferramenta de torneamento e que proporciona informação sobre o estado da ferramenta durante a maquinação. O diminuto sensor piezoelétrico mede com alta resolução inclusivamente as forças de corte mais baixas. O sistema é adequado para utilização em trabalhos de torneamento, especialmente no âmbito micro. Neste caso, como os desvios são menores, outros métodos de medição alternativos, como a vigilância da potência de acionamento do motor do fuso principal, são menos eficazes.
A medição do ruído estrutural também não proporciona resultados satisfatórios constantes com as peças de tamanho reduzido. A supervisão visual também fica excluída devido à utilização de lubrificantes de refrigeração e à elevada velocidade de rotação durante o processo de maquinação. A nova solução não requer intervenção no controlo CNC e a sua utilização é independente da equipa. Consequentemente, o PTS reduz os custos de produção e amplia as capacidades de fabrico.
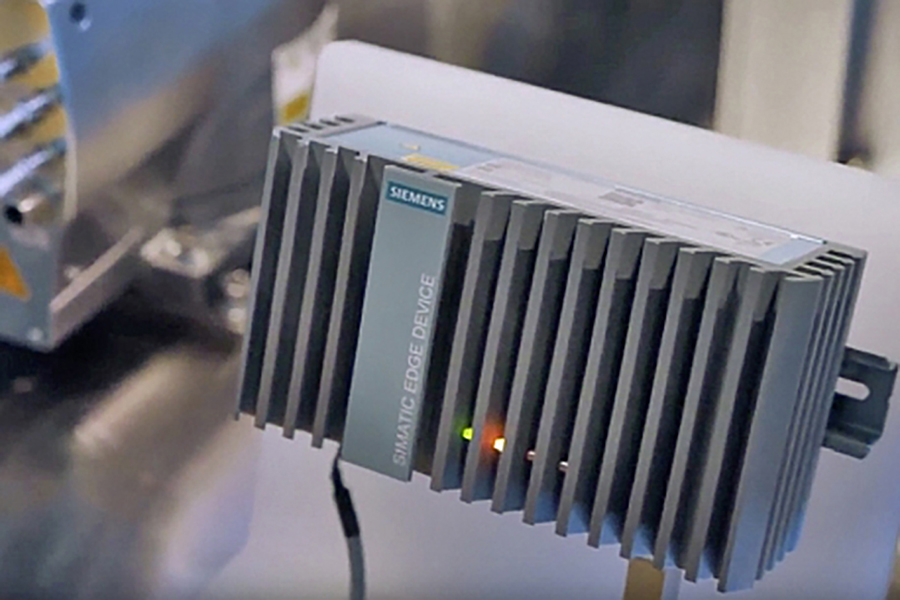
Canal curto até ao cliente
O controlo de custos e a eficiência preocupam também os fabricantes de maquinaria. “A necessidade de produtos digitais está sempre ligada à enorme importância que os nossos clientes dão à obtenção de processos eficientes. As soluções de base digital contribuem para melhorar a estrutura organizativa dos nossos clientes. A redução dos prazos de correção de falhas constitui um tema tão importante como o da maior disponibilidade da máquina”, afirma o diretor-geral da empresa Burkhardt und Weber, Olaf Furtmeier. Na opinião deste, a vantagem de uma empresa média é desfrutar de um canal curto e abordar os projetos de desenvolvimento com equipas ágeis para incluir o maior número de perspetivas no processo de desenvolvimento. “Não obstante, é indispensável contar com a ajuda de parceiros qualificados. Só desta forma é possível garantir a aplicação de conhecimentos técnicos globais sobre produtos para criar um produto final que proporcione realmente valor acrescentado e, portanto, seja adquirido pelos clientes”, reflete Olaf Furtmeier. Uma comunicação eficaz entre os diferentes elementos da produção é também, no caso da Zoller, o ponto central da digitalização e da indústria 4.0 quando falamos de ajuste, medição e gestão de ferramentas. Especialmente no trajeto de transferência dos dados, desde o equipamento de ajuste até à máquina, existem atualmente muitos caminhos seguros para o processo e rápidos. Os dados reais da ferramenta são processados de forma adequada para o respetivo controlo da máquina e transferidos diretamente desde o equipamento de ajuste e medição para o controlo CNC. O software transforma os valores de medição definidos num formato adequado para o controlo, em função da máquina, e emite-os. O software contém uma biblioteca com mais de 230 formatos de edição padrão para diferentes máquinas. A AMB 2020 também é a plataforma adequada para estas questões e para debates sobre possíveis modificações resultantes de exigências específicas dos clientes, que são sempre possíveis na Zoller, conforme se afirma.

Transferência de conhecimentos e formação
O motivo para que a digitalização tenha feito a sua entrada relativamente tarde no setor do fabrico de máquinas-ferramentas e da maquinação de metais comparativamente a outros setores não reside nos custos de implementação, mas sim no facto de exigir dos funcionários, em grande medida, novos modelos e lógicas de pensamento. A importância do tema da transferência de conhecimentos e da formação para abordar o tema da digitalização a partir dos fundamentos foi evidenciada pela empresa Trumpf, participante na AMB, no início do presente ano de formação: para dar resposta à transformação digital, a Trumpf aposta na interligação e qualifica os seus jovens talentos pela primeira vez com a ajuda de um “Formador de indústria 4.0”. O programa coordena todos os conteúdos digitais dos diferentes âmbitos de estudo e acompanha os jovens estagiários e os estudantes de formação dual. “Na nossa empresa, a digitalização torna-se numa pedra angular da formação. Quem estuda tecnologia informática ou tira um curso neste âmbito deve entender o que o fabricante de maquinaria faz. Por sua vez, o fabricante de maquinaria deve saber que software precisa para a sua máquina. Isto conflui também com os estudos empresariais, em que, por exemplo para a conceção de uma máquina, devem incluir-se peças de chapa e software”, comenta Katja Tiltscher, diretora de formação da Trumpf. Encaixa aqui na perfeição um novo elemento do programa-quadro da AMB 2020, o espaço sobre tendências Trend-Lounge, que oferece aos visitantes um fórum gratuito para a transferência de conhecimentos e para o intercâmbio com especialistas. Nos cinco dias do fórum, o programa incluirá diferentes temas centrais, tal como o fabrico aditivo, a construção leve e, naturalmente, a digitalização.
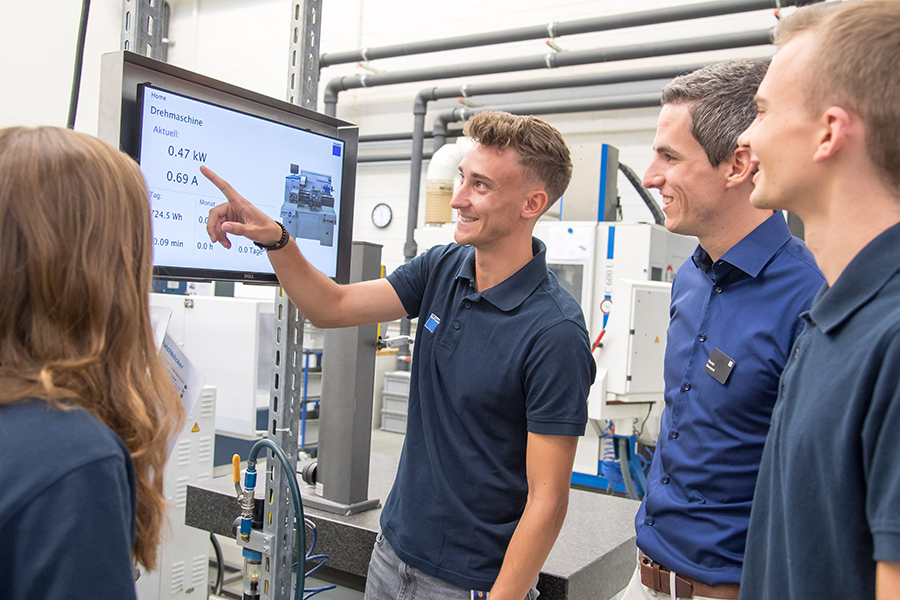
Na oficina de formação da Trumpf, os estagiários aprendem como melhorar o fabrico com as soluções digitais. Foto: Trumpf Group.
Com soluções novas como o edge computing, a digitalização abre um amplo leque de possibilidades nos heterogéneos contextos de produção do setor da maquinação de metais
As soluções digitais podem contribuir para minimizar as rejeições de peças
A formação é um fator crucial na transformação digital