Los láseres de Coherent proporcionan una visión exclusiva de la realidad
Wolfgang Illich y Thomas Schreiner, de Coherent
10/01/2020Siguiendo su afán por innovar, Silhouette Internation no ha dudado en adoptar nuevas tecnologías de fabricación para alcanzar sus objetivos. Y los sistemas de soldadura láser de Coherent permiten a la empresa producir algunos de sus diseños más avanzados.
Diseño único y duradero de gafas
“El diseño de las gafas personales es nuestra principal prioridad, porque queremos crear unas gafas únicas que se ajusten armoniosamente al rostro del usuario”. Así resume el CEO de Silhouette, Thomas Windischbauer, su filosofía de diseño. Este enfoque, a su vez, requiere varios imperativos de diseño. Entre ellos se encuentra la exigencia de una fácil adaptabilidad a las necesidades individuales del usuario, así como el uso de materiales que garanticen la ligereza y la flexibilidad, pero también la estabilidad.
Utilizado en el espacio
En 1999, Silhouette tuvo un año decisivo. La Silhouette ‘Titan Minimal Art’ (TMA) de 1,8 gramos, la primera gafa sin tornillos ni bisagras fabricada en titanio, revolucionó el mercado de las gafas y fue un éxito inmediato. Hasta la fecha, se han vendido más de 12 millones de unidades en todo el mundo.
El Titan Minimal Art fue aprobado para vuelos espaciales en el año 2000. La ausencia de tornillos y bisagras garantiza la seguridad al minimizar el riesgo de objetos que flotan libremente dentro de los cascos espaciales, los aparatos de respiración y dentro de la nave espacial. Hasta la fecha, la TMA ha sido la fiel compañera de los astronautas en más de 30 vuelos espaciales.
Desde 2017, Silhouette International también fabrica sus propias gafas en el llamado Lens Lab, un edificio especialmente construido en las instalaciones de la fábrica. Las monturas y las lentes se fabrican en la sede de la empresa en Linz con los más altos estándares técnicos y están hechas a medida para las colecciones de gafas de Silhouette.
Desde la introducción de la TMA, Silhouette ha aplicado este mismo enfoque sin bisagras a muchos otros diseños. En cuanto a la tecnología de fabricación, esto conlleva varios requisitos. En primer lugar, la capacidad de unir una variedad de materiales, incluyendo el titanio y las aleaciones especializadas. A continuación, la capacidad de producir juntas que sean estéticamente agradables; en concreto, esto significa que sean prácticamente invisibles y que no se puedan sentir. Por último, también se necesitan juntas que ofrezcan una excelente flexibilidad y una alta resistencia, además de la capacidad de ser ciclado (doblado y abierto) numerosas veces sin un cambio de forma o degradación de la resistencia mecánica.
Asociarse para una solución total
Teniendo en cuenta estos requisitos técnicos, además de las exigencias del mercado de apoyar la producción de varias colecciones nuevas cada año, Silhouette buscó un proveedor que apoyara tanto el desarrollo de los procesos de fabricación como que proporcionara el equipo de producción real. Desde el principio, se determinó que Silhouette pasaría de la soldadura por resistencia tradicional a la soldadura por láser para cumplir con sus estrictos requisitos de calidad y rendimiento.
Durante esta búsqueda, Coherent surgió como favorito entre los proveedores potenciales por varias razones. En primer lugar, Coherent era una de las pocas empresas que podía suministrar fácilmente el paquete completo, es decir, el láser, toda la optomecánica asociada, la manipulación de piezas y el software. Además, Coherent era capaz y estaba dispuesta desde el principio a participar en el desarrollo del proceso, prestando su considerable experiencia en láser a una empresa que no tenía mucha experiencia con la tecnología.
Los primeros sistemas de soldadura láser Coherent adquiridos por Silhouette fueron modelos manuales utilizados para la construcción de prototipos y trabajos de reparación; el éxito de los mismos condujo a la compra del Coherent MPS Rotary (Modular Processing System) para la soldadura láser, adaptado específicamente a las necesidades de Silhouette. La voluntad de Coherent de realizar esta personalización fue otro factor clave en su selección por parte de Silhouette.
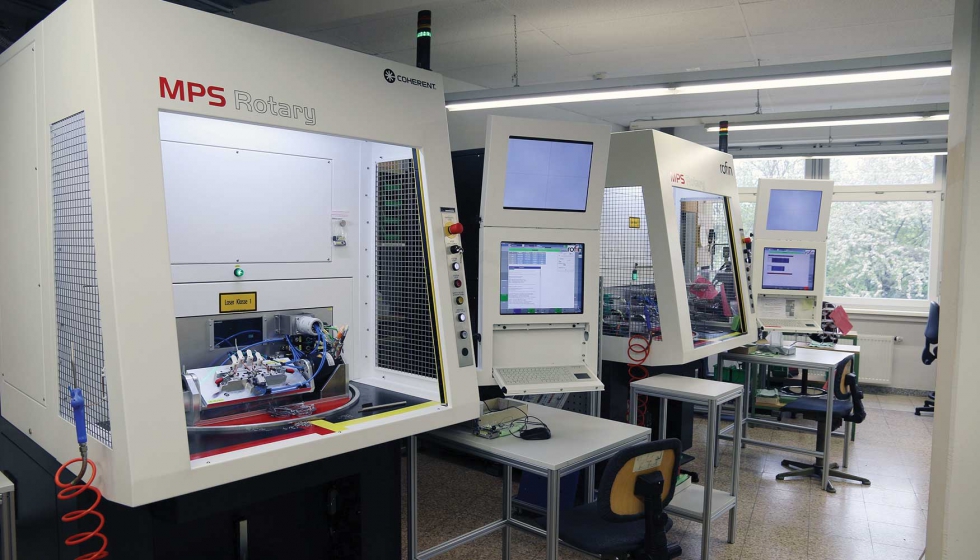
Beneficios de MPS Rotary
El MPS Rotary es un sistema automatizado, llave en mano, para la soldadura, corte y perforación de metales, en este caso, incorporando un láser de fibra Coherent de 200 W (StarFiber 200). La combinación de la óptica del escáner y el desplazamiento permite un campo de trabajo variable. El sistema es completamente cerrado (láser de clase I) para la seguridad del operador. Están disponibles varias opciones, incluyendo la visión artificial integrada. El sistema también utiliza una mesa giratoria para permitir la carga/descarga de piezas mientras se realiza el procesamiento.
El software, de fácil manejo, permite el uso por parte de los operarios con un mínimo de habilidad y formación. Por ejemplo, el sistema detecta automáticamente el tipo de pieza que se ha cargado y luego llama al programa de procesamiento correcto. Los ingenieros de Silhouette suelen cambiar diariamente los parámetros de los trabajos para cumplir con sus requisitos de producción específicos, y el software de MPS Rotary ha demostrado tener la suficiente capacidad de respuesta para cumplir con este programa. Silhouette utiliza el sistema cinco días a la semana, dos turnos al día, y ha comprobado que la disponibilidad y el tiempo de funcionamiento de la máquina son excelentes.
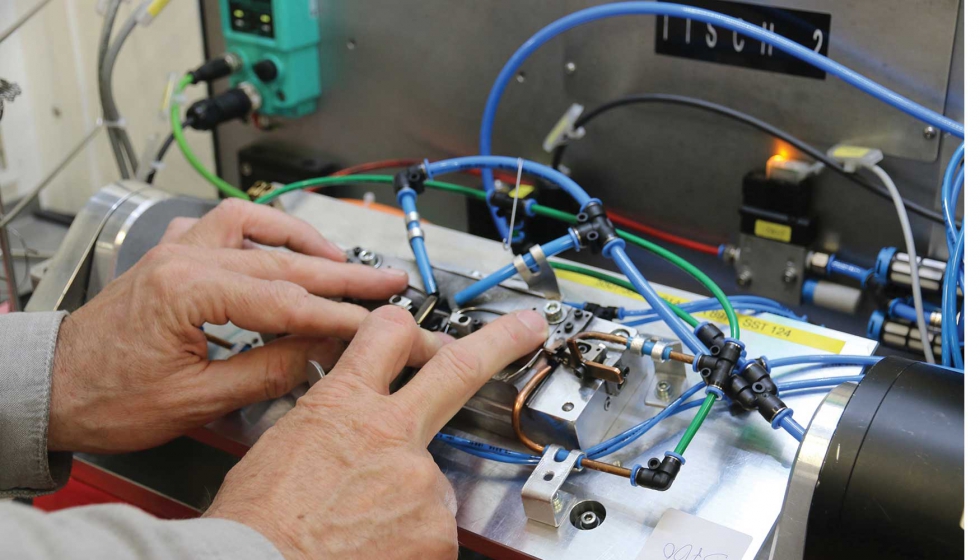
Producción más flexible y rentable
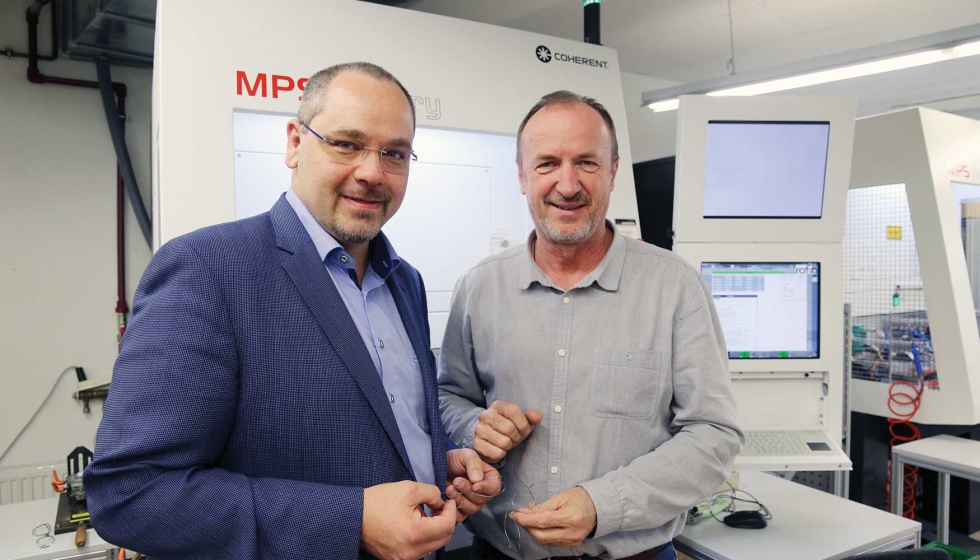
SmartWeld
Otra ventaja clave del MPS Rotary es que incluye la tecnología SmartWeldTM de Coherent. SmartWeld incorpora una implementación avanzada de ‘oscilación del haz, es decir, el movimiento rápido del haz de luz durante el proceso de soldadura. Específicamente, en lugar de moverse simplemente a lo largo de un cordón de soldadura, el haz puede trazar patrones circulares, elípticos o incluso en zigzag, ejecutando el movimiento tanto a lo largo como perpendicular al cordón de soldadura. Estos patrones se programan fácilmente en el MPS Rotary utilizando el software integrado.
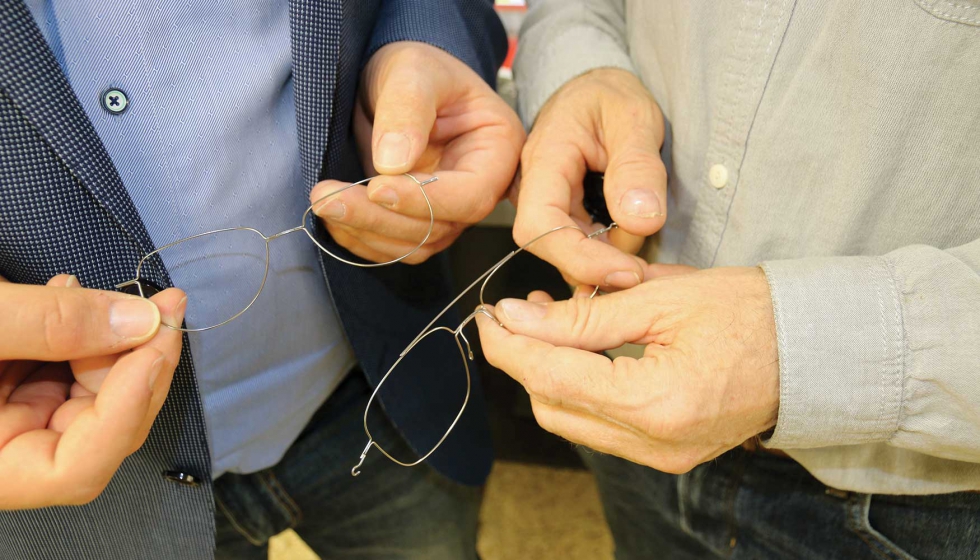
Un beneficio clave de SmartWeld es que produce una soldadura de mayor calidad y más reproducible. Esto se debe a que el movimiento del rayo permite un control más flexible y preciso de la distribución de calor producida por el láser. Por ejemplo, un patrón SmartWeld relativamente grande puede ser usado para precalentar el material antes de que sea completamente licuado, o para enfriarlo lentamente después de fundirlo. El primero puede prevenir burbujas y turbulencias en el baño de fusión, que producen salpicaduras y resultados inconsistentes, mientras que el segundo puede eliminar el agrietamiento a medida que el material se enfría. SmartWeld también puede ser usado para alterar la distribución Gaussiana normal (altamente pico en el centro) de la energía láser aplicada. Reduciendo la intensidad efectiva en el centro del patrón láser puede reducir la turbulencia del baño de fusión permitiendo que la expansión del vapor ocurra de una manera más controlada, conduciendo nuevamente a una mejor consistencia del proceso. En este caso, Silhouette puede recurrir a la experiencia de Coherent en la optimización de SmartWeld para diferentes materiales y geometrías de soldadura.
Otro beneficio de SmartWeld es que permite la construcción de puentes de mayor anchura en las piezas soldadas. Esto reduce la tolerancia de montaje, lo que acelera la producción y reduce los costos. “Silhouette produce actualmente unos 2,2 millones de vidrios al año”, informa Illitz. “Necesitamos equipos de producción que soporten este volumen y que ofrezcan la calidad que necesitamos de forma que aún podamos ser competitivos en cuanto a costes”. Además, nuestros métodos de producción deben ser lo suficientemente flexibles para apoyar nuestro rápido e implacable ciclo de diseño, que es un requisito previo para mantener el éxito en el mercado en cualquier tipo de moda vestible”. MPS Rotary ha demostrado su capacidad en todos estos frentes. Y, lo que es igual de importante, Coherent se ha asociado sistemáticamente con nosotros para proporcionar los conocimientos de aplicación y proceso necesarios para aprovechar al máximo las capacidades de su máquina”.