Kennametal imprime en 3D una herramienta ligera para el sector de la movilidad eléctrica
Kennametal ha desarrollado una herramienta ligera para el taladrado del estator impresa en 3D diseñada expresamente para cubrir la creciente demanda, por parte de los clientes, de soluciones de herramientas más ligeras para mecanizar componentes de vehículos híbridos y eléctricos.
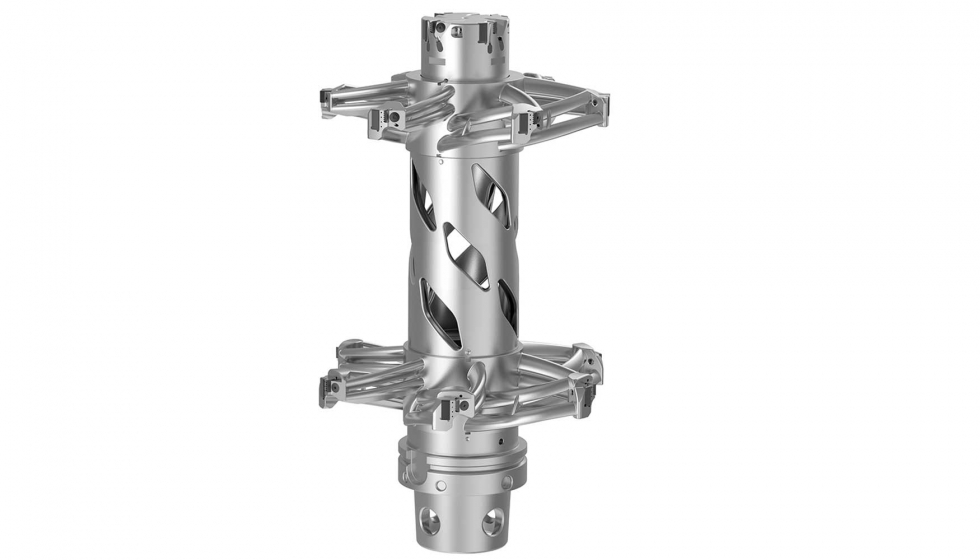
Los componentes de movilidad eléctrica se mecanizan generalmente en centros de mecanizado CNC más pequeños y de poca potencia que precisan soluciones de herramientas de peso más ligero. La herramienta para el taladrado del estator impresa en 3D de Kennametal pesa la mitad que la versión fabricada de manera convencional, y aun así cumple los requisitos de precisión, redondez y acabado superficial del taladrado del bloque de motor de aluminio. “El taladrado principal que alberga el estator de un motor eléctrico mide aproximadamente 250 mm de diámetro (9,84”) y unos 400 mm (15,74”) de largo, con un taladro menor en el fondo para el rodamiento”, explica Harald Bruetting, director de Ingeniería de Programas. “Si se fabricara con medios convencionales el escariador necesario para este tipo de aplicación pesaría más de 25 kilogramos (55 libras), demasiado pesado para la máquina herramienta existente o para el operario que la maneje”.
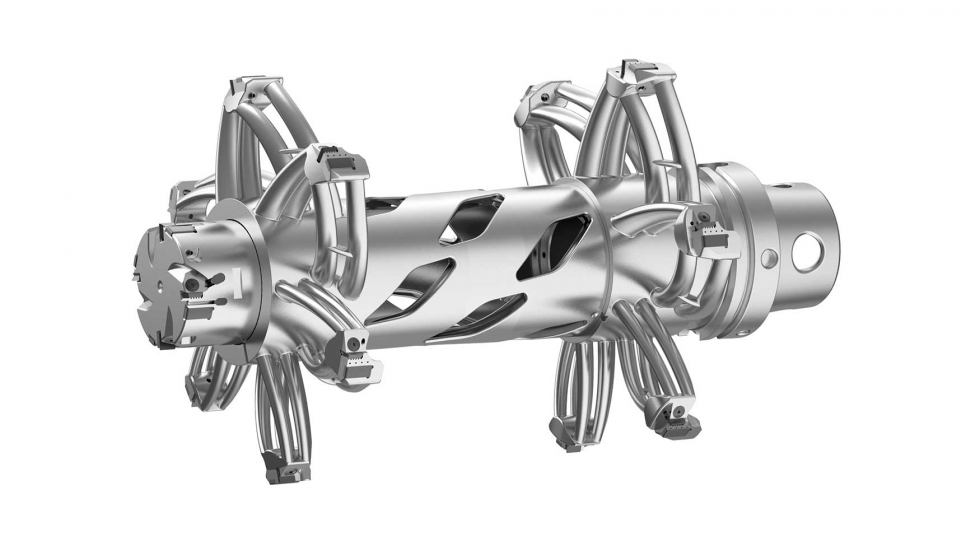
Bruetting y el grupo de soluciones de ingeniería de Kennametal echaron mano de las capacidades de fabricación aditiva internas de la compañía para imprimir en 3D una herramienta intercambiable robusta y a la vez ligera que estuviera equipada con tecnologías probadas de Kennametal, que incluyera las plaquitas de escariado fino RIQ ajustables para el acabado de alta precisión y un adaptador KM4X para obtener la máxima rigidez. La herramienta tiene además canales internos de refrigeración impresos en 3D que ayudan a maximizar la productividad y vida útil de la misma.
“Al utilizar la impresión en 3D de lecho de polvo metálico en combinación con software de análisis de elementos finitos, hemos podido diseñar y construir una herramienta que llevó el momento de inercia muy próximo a la cara del husillo aumentando así la rigidez y cumpliendo al mismo tiempo las restricciones de peso del cliente”, dice Werner Penkert, director de la sección de Soluciones Futuras. “Es un ejemplo excelente de cómo Kennametal utiliza la tecnología de fabricación avanzada para contribuir a superar los desafíos extraordinarios de nuestros clientes”.
Se construyeron dos versiones de la herramienta, una con un tubo de fibra de carbono y la otra con un tubo metálico impreso en 3D, y los resultados obtenidos fueron impresionantes. La herramienta con el tubo impreso en 3D pesaba 10,7 kg y la versión en fibra de carbono pesaba 9,5 kg, menos de la mitad de las versiones habituales de la herramienta.
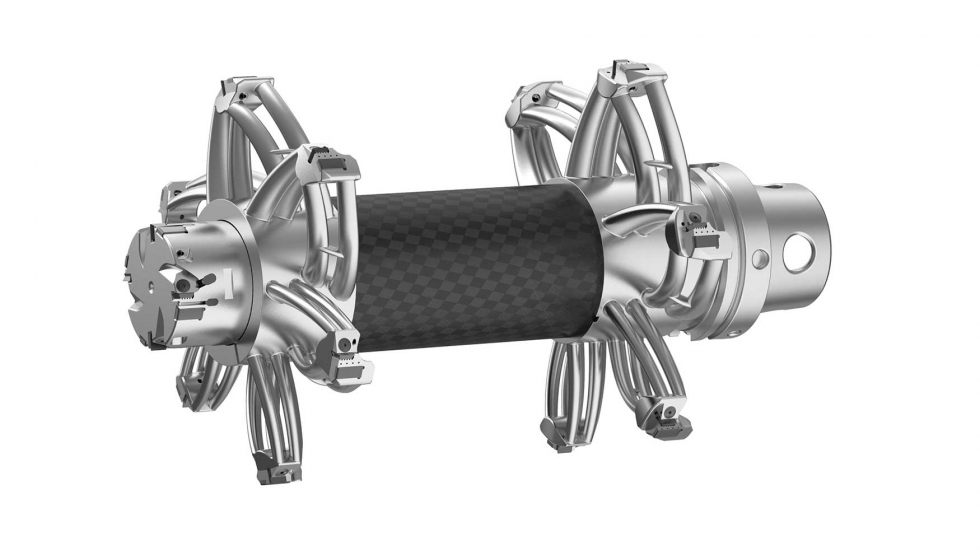