Mejora del roscado. El portaherramientas es la clave
Los procesos de roscado están presentes desde el ámbito doméstico hasta en piezas de alto valor añadido. En este último caso, el roscado se vuelve una operación crítica dado que generalmente se hace una vez la pieza está prácticamente terminada lo que implica que un fallo puede tener consecuencias desastrosas hasta el punto de llegar a invalidar la pieza en cuestión [2]. Los factores que influyen en el fallo del roscado se encuentran no sólo al gran número de filos de corte involucrados en el corte sino también en la complicada sincronización entre el movimiento axial y rotativo de la herramienta, sobre todo a altas velocidades de corte [3]. Este último concepto es el que toma gran relevancia ya que se estima que el tiempo de operación de roscado está alrededor del 30% del tiempo total de fabricación de una pieza [4]. Por tanto, seguir mejorando el propio proceso de fabricación de roscas se muestra como un objetivo interesante desde el punto de vista del sector del mecanizado con el fin de aumentar la productividad.
Para ejecutar los actuales procesos de roscado existen diversos portaherramientas diseñados para esta tarea con los que se busca optimizar la rigidez del giro del macho de roscar, así como aumentar la precisión del roscado y solventar la problemática de la sincronización de los movimientos axial y radial de la de la herramienta. Concretamente, los portaherramientas de roscar más extendidos tradicionalmente en la industria eran aquellos conocidos como flotantes que están provistos de un muelle interno a modo de embrague que absorben el cambio de sentido de giro del husillo. De este modo se lograba evitar cualquier problemática derivada de las sincronizaciones y holguras entre ejes. Sin embargo, la necesidad de mayores precisiones y rigideces, sobre todo en materiales que conllevan una dificultad de mecanizar, ha llevado a la industria a buscar nuevas soluciones como portaherramientas semirrígidos, los cuales tienen una gran aceptación por parte de las empresas de mecanizado. Este tipo de portaherramientas se caracterizan por llevar un embrague intermedio flexible que absorbe el desfase axial sin apenas pérdida de par. En la figura 1 se muestran dos ejemplos de estos portaherramientas para roscado.
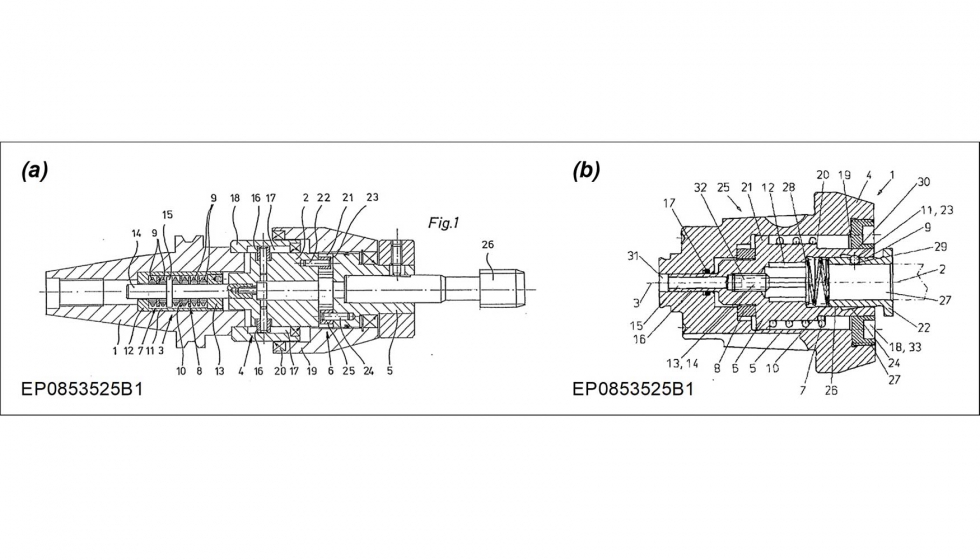
Cabe destacar, que los portaherramientas semirrígidos resultan la opción más eficaz a la hora de realizar roscados en condiciones difíciles de mecanizado. No obstante, con el fin de obtener procesos más robustos y fiables en este tipo de condiciones, los fabricantes de portaherramientas no dejan de presentar mejoras en los embragues que aporten más rigidez a éstos y así lograr dicho objetivo. Es aquí donde los últimos desarrollos de portaherramientas semirrígidos con embragues rígidos marcan la diferencia no sólo en vida de herramienta sino también en tiempos de mecanizado y costes de los propios portaherramientas.
Estos portaherramientas se caracterizan por sustituir el embrague basado en muelles por embragues rígidos que se aprovechan de la elasticidad de los materiales metálicos para absorber el cambio de giro de la herramienta sin afectar prácticamente a la calidad de la rosca y por tanto pueden posibilitar la obtención un proceso de un roscado más eficiente además de rebajar su costo ya que su fabricación es más sencilla.
Por tanto, en línea con todo esto, en este artículo se realiza un estudio de dos tipos de portaherramientas semirrígidos, uno con embrague flexible y otro rígido, en los que se busca verificar si los avances realizados en esta materia implican un salto cualitativo en cuanto al proceso de roscado.
Montaje experimental
Los ensayos de roscado han sido realizados en un centro de mecanizado Ibarmia ZV25/U600. El tipo de roscados realizados han sido roscas ciegas de métrica 8mm. Durante estos se han obtenido datos de consumo de potencia en el husillo mediante un medidor Vydas. Por otra parte, se ha procedido a la medida del desgaste de las caras de incidencia de los machos de roscar con la ayuda de un microscopio PCE-200. El material utilizado durante los ensayos ha sido un acero 42CrMo4 templado y revenido caracterizado por poseer gran porcentaje de aleantes abrasivos/endurecedores como el silicio y el cromo y durezas cercanas a los 35HRc. Las planchas utilizadas tenían un diámetro de 500 mm en las que se han realizado pasadas de planeado previas a su taladrado y posterior roscado. La profundidad de las roscas ha sido de 16 mm. El método de sujeción de las placas se ha llevado a cabo con 4 calzos realizados de 32 mm. El montaje experimental realizado se muestra en la figura 2.
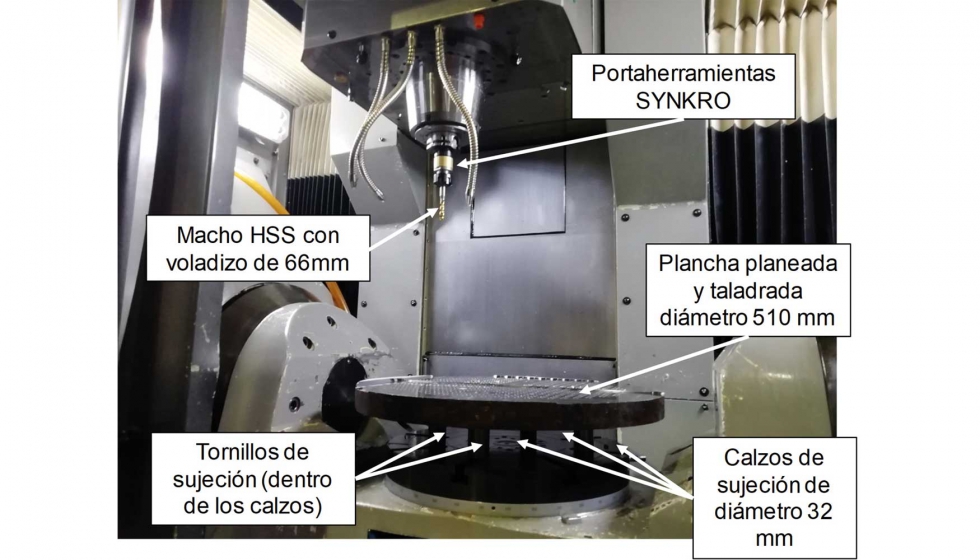
En cuanto a los portaherramientas utilizados se optó por utilizar dos portaherramientas de la empresa Laip. Específicamente, se utilizó un portaherramientas semirrígido tradicional, el cual consta de un embrague flexible y otro portaherramientas semirrígido denominado Synkrotapping el cual se caracteriza por utilizar un embrague rígido que se caracteriza por absorber mejor el cambio de sentido de giro del macho de roscar. Los machos de roscar que se utilizaron unos machos HSS recubiertos de TiN. En la figura 3 se muestran los portaherramientas utilizados.
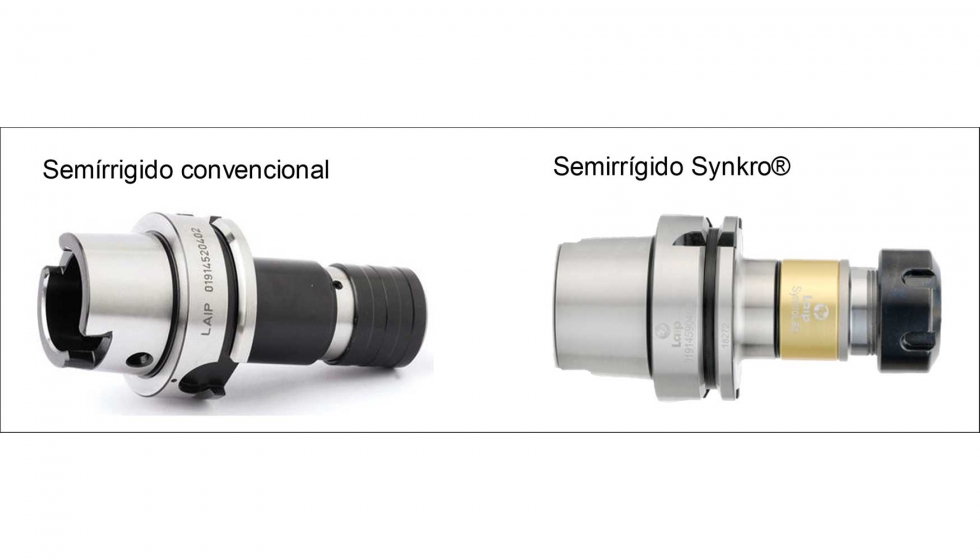
Finalmente, el diseño de ensayos realizado se caracterizó por comparar inicialmente el comportamiento de ambos portaherramientas con una velocidad de corte convencional para F1252 en roscados ciegos (15 m/min) con el fin de discernir si la mejora propuesta de utilizar embragues rígidos en lugar de flexibles implica una mejora sustancial en los procesos de roscado. Posteriormente, una vez verificada esta premisa, se procedió a evaluar la variación de la velocidad de corte en el portaherramientas Synkrotapping con 10, 15 y 20 m/min, respectivamente con el fin de comprobar si además es posible el aumento de productividad en este tipo de materiales.
Resultados y discusión
En la figura 4 se muestran los resultados obtenidos al roscar agujeros ciegos con cada uno de los portaherramientas ensayados en cuanto a potencia consumida y desgaste en cara de incidencia se refiere. Concretamente en cada una de las figuras se refleja el desgaste medio en cara de incidencia de los machos y la potencia de corte consumida por el husillo de la máquina durante el roscado.
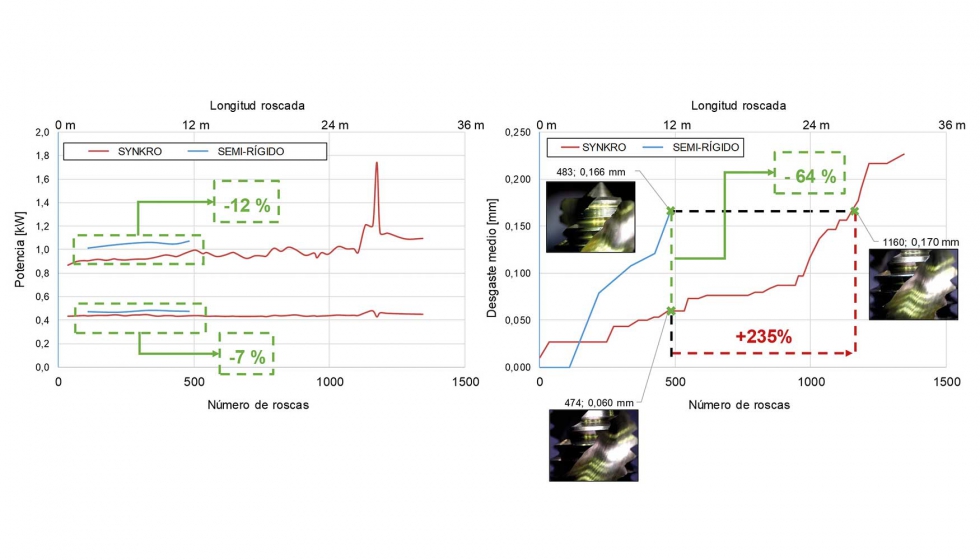
En ella se puede observar como la potencia media consumida es reducida un 7% y la potencia máxima —coincidente con el giro a izquierdas del macho de roscar en el fondo de la rosca— un 12%. Esto se traduce en menores esfuerzos de corte que se reflejan en un menor desgaste de herramienta como se detalla en la gráfica del desgaste en la cara de incidencia. En ella se aprecia que una vez realizados ≈500 roscados con ambos portaherramientas, el desgaste que presenta el macho de roscar al utilizar el portaherramientas Synkrotapping es un 64% menor. De hecho, ese valor (≈0,15 mm) no es alcanzado hasta roscar 650 taladros más, es decir, la vida de herramienta aumenta un 235%.
Una vez observado que el portaherramientas Synkrotapping ofrece una mayor durabilidad además de un menor consumo de potencia se pasó a la optimización de la velocidad de corte. En este caso, se tomó como referencia la velocidad de corte convencional (15 m/min) y se aumentó y redujo 5 m/min, respectivamente. Los resultados se muestran en la figura 5.
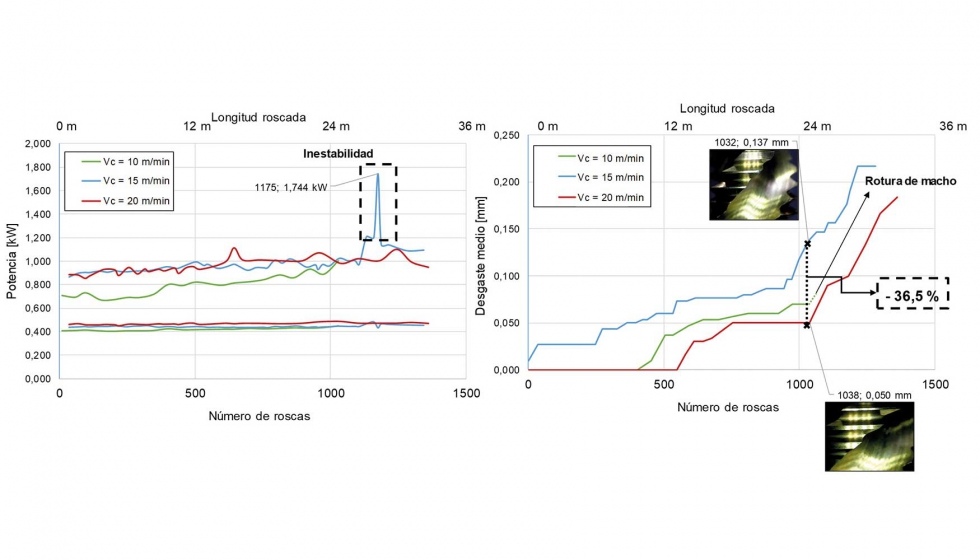
En ellos se observa como las potencias consumidas medias son prácticamente análogas para las tres velocidades de corte, reduciéndose la potencia máxima cuando la velocidad de corte es reducida a 10 m/min. Sin embargo, la vida de herramienta es reducida drásticamente ya que el macho se rompe en el roscado número 1.028, lo que invalida el uso de esta velocidad de corte en un entorno industrial. Por otra parte, cabe destacar que al roscar con una velocidad de corte de 15 m/min, a partir de la rosca ˜1.133 el proceso se vuelve inestable, lo que implica que el proceso industrialmente puede no ser viable. Sin embargo, al aumentar la velocidad de corte a 20 m/min esta inestabilidad es eliminada, haciendo el proceso más fiable y robusto. Esta afirmación se refleja en la gráfica de desgastes donde se observa que al roscar con 20 m/min el desgaste se reduce un 36,5% en comparación con la velocidad de corte tomada como referencia (15 m/min), tendencia que se mantiene como puede observarse en la figura 5. Por tanto, con el portaherramientas Synkrotapping, no sólo se consigue reducir consumos de potencia frente al portaherramientas semirrígido convencional, sino que permite un aumento de la velocidad del corte a la vez que se reduce el desgaste.
Conclusiones
En este artículo se ha analizado la diferencia existente entre el uso de dos portaherramientas semirrígidos que presentan sistemas de embrague diferentes. En concreto se ha estudiado el comportamiento del uso de un embrague flexible y otro rígido durante el roscado de un acero 42CrMo4 templado y revenido con una dureza de 35HRc.
Según los resultados obtenidos se puede concluir que la utilización de portaherramientas semirrígidos con embrague rígido implica:
- Reducción del consumo de potencia del cabezal sobre un 15%.
- Posibilidad de aumentar un 33% la velocidad de corte.
- A igual velocidad de corte un aumento de vida de herramienta del 235%.
Referencias
[1] http://www.fastener-world.com.tw/0_magazine/ebook/pdf_download/FW_152_E_182.pdf visitado el 16/05/2018 a las 11:57.
[2] P. Monka, K. Monkova, W. Modrak, S. Hric, P. Pastucha. Study of tap failure at the internal threads machining. Engineering Failure Analysis. 2019. Vol 100, pp. 25-36.
[3] K. Gawdzinska, Application of the Pareto chart and Ishikawa diagram for the identification of major defects in metal composite castings. Archives Foundry Engineering. 2019. Vol. 11, pp. 290-299.
[4] I. Elósegui. Una metodología para la mejora del proceso de roscado con macho en fundiciones de alta resistencia. Tesis. 2017. Universidad del País Vasco.