Soluciones avanzadas para procesos de electroerosión en seco
El mecanizado por electroerosión (EDM) requiere del uso de fluidos líquidos dieléctricos para garantizar la efectividad y limpieza del proceso. Sin embargo, este método genera residuos y acarrea gastos económicos elevados. Con la misión de avanzar en el desarrollo de procesos que no impliquen el uso de fluidos líquidos, el centro tecnológico vasco IK4-Tekniker ha participado en el proyecto Eleco, una iniciativa que ha permitido la fabricación de un dispositivo integrado en las máquinas de electroerosión para realizar procesos de fresado en seco. La solución desarrollada tiene aplicaciones en el mecanizado de piezas grandes como moldes y troqueles, así como en componentes de sectores de alto valor añadido como el aeronáutico o la generación de energía.
Los expertos del centro tecnológico, en colaboración con el resto de socios del consorcio y, especialmente, del fabricante vasco ONA, han logrado desarrollar un cabezal de fresado independiente y desmontable, de forma que se pueda emplear en distintos equipos que utilicen portaelectrodos estándar. Este dispositivo, que funciona con gas (aire) y dispone de una toma externa que hace posible que sea alimentado desde la propia máquina o desde una bombona, elimina la necesidad de un fluido dieléctrico líquido en el proceso de electroerosión. “Los principales objetivos del proyecto Eleco han sido desarrollar un nuevo concepto de mecanizado por electroerosión limpio, abrir un campo nuevo de aplicación del proceso de electroerosión para piezas grandes que no pueden procesarse en las máquinas actuales e impulsar el desarrollo tecnológico y la explotación del proceso de fresado EDM en gas”, asegura el responsable de la iniciativa en el centro tecnológico Manu Goiogana.
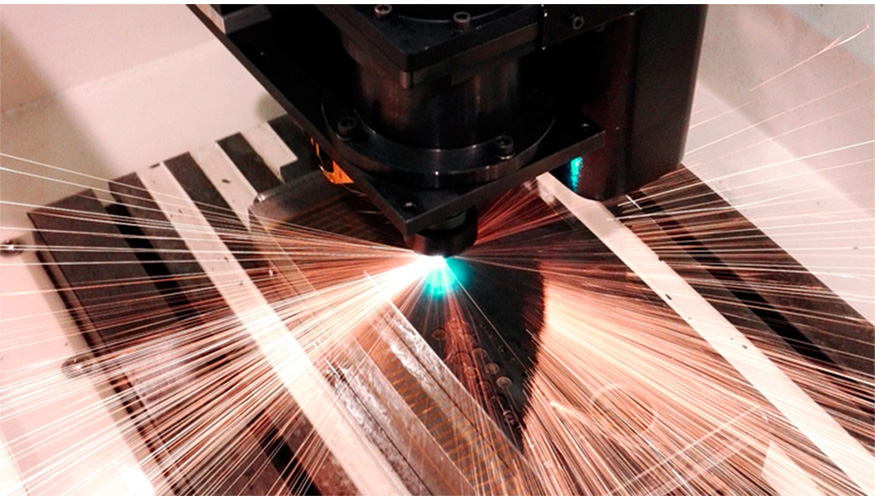
En concreto, la iniciativa ha permitido llevar a cabo el desarrollo íntegro del cabezal, desde la etapa de definición de los requisitos, hasta la validación del dispositivo en la máquina de EDM, pasando por todas las fases de diseño, fabricación, montaje y verificación. Además, se ha realizado un análisis para evaluar el comportamiento del proceso de EDM en gas respecto a los diferentes parámetros de proceso como la tensión de descarga, la intensidad, el tiempo, el diámetro, la geometría, el material del electrodo, la velocidad de giro del cabezal y el tipo de gas dieléctrico.
“Una de las principales ventajas que genera el dispositivo desarrollado en este proyecto es la reducción de los costes del proceso de EDM, gracias a la eliminación del medio dieléctrico líquido. También se disminuyen gastos por la menor gestión de residuos y la reducción de desgaste en herramienta”, asegura el experto. Además, la supresión de los tanques de dieléctrico líquido elimina la necesidad de sumergir todas las piezas y este fenómeno puede tener como consecuencia no limitar el tamaño de las piezas que se pueden electroerosionar. También resulta beneficioso el ahorro de espacio en el lay-out de los fabricantes de componentes que apliquen esta tecnología. “Para los fabricantes de máquinas de electroerosión como ONA, estos desarrollos facilitan la creación de un concepto de máquina EDM portable e inexplorado hasta ahora. Así como el refuerzo del perfil de estas empresas como proveedores globales de soluciones EDM especializadas de alto valor”, concluye Goiogana. Si el fabricante vasco ONA plantea la comercialización del cabezal, su capacidad de acoplamiento en portaelectrodos estándar (Erowa o Hirschmann) hará posible que cualquier desarrollador de componentes que en este momento disponga de una máquina de EDM pueda ser usuario de esta tecnología.