Aidimme investiga la fabricación 3D con una aleación mejorada de titanio para reducir el peso de los aviones
El Instituto Tecnológico Metalmecánico, Mueble, Madera, Embalaje y Afines, Aidimme, está desarrollando una nueva aleación de base de titanio modificada con nanopartículas cerámicas para la fabricación aditiva de piezas metálicas que permita fortalecer la estructura entre un 15 y un 40% y reducir sustancialmente el peso de los componentes, con un ahorro estimado de materiales entre un 40 y un 50%, frente a las fabricadas mediante procesos tradicionales. Características especialmente atractivas para un sector como el aeroespacial, según indican los promotores del proyecto europeo de investigación Nanotun3D.
El nuevo material en desarrollo, Nanotun3D, coge la denominación del proyecto europeo con el mismo nombre en el que participan 9 socios de Bélgica, Gran Bretaña, Alemania, Italia y España, incluido el propio Instituto Tecnológico Aidimme, coordinador de la investigación.
Menos peso, ahorro de combustible, menos CO2
La ambiciosa iniciativa Nanotun3D ‘Desarrollo del flujo de trabajo completo para producir y usar una novedosa aleación basada en Titanio nanomodificada mediante fabricación aditiva para aplicaciones especiales’ propone un gran beneficio para el sector aéreo, con un ahorro estimado de entre 0,02 y 0,04 litros de combustible por hora por cada kilo de peso reducido en las piezas, así como una sustancial reducción de las emisiones de CO2, del mismo modo que para el sector espacial, y donde el rendimiento de las propiedades estructurales de los materiales es un aspecto crítico para ambos.
Otro aspecto de capital importancia para transferir los resultados a la industria aeroespacial, es la cualificación del nuevo material y proceso de fabricación. Se trata de verificar que los resultados obtenidos alcanzan los estándares establecidos y se constatan a lo largo del tiempo y en diferentes lotes de fabricación. Durante el proyecto se están sentando las bases para llevar a cabo la citada cualificación, de manera que facilite a los fabricantes de componentes aeronáuticos la certificación de los productos fabricados con esta nueva aleación procesada mediante tecnología aditiva.
De esta forma, el proyecto ha asumido el reto de proporcionar al sector aeroespacial soluciones con el material y sistemas indicados bajo el estricto cumplimiento del Sistema de Gestión de la Seguridad Operacional (SMS) de servicios y productos para las aeronaves.
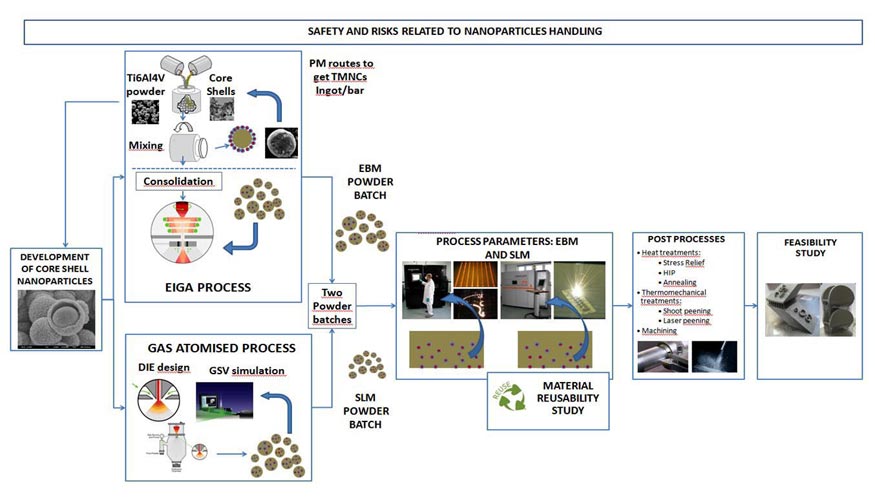
Flujo de trabajo Nanotund3D: desarrollo de materiales nano modificados para fabricación aditiva y caracterización de su ciclo de vida operativo, desde la síntesis de nanopartículas y la fabricación de polvo metálico hasta la pieza final.
Fabricación aditiva
Igualmente aporta ventajas directas a otros sectores como la automoción, implantes articulares y odontológicos, y bienes de equipo, por ejemplo, y las numerosas inherentes a la propia fabricación aditiva, como el diseño y fabricación de geometrías complejas; la fabricación bajo demanda; la reducción de tiempos de puesta en el mercado; la ausencia de herramientas de producción, el procesado de materiales a medida; el ahorro de costes por reducción de material; la reducción de la cadena de suministro; y la fabricación de piezas de recambio y reparación de piezas dañadas, entre otras ventajas.
La dispersión eficiente de las nanopartículas de carburo de silicio (SiC) es fundamental para mejorar las aleaciones de Ti6Al4V, y para ello es necesario garantizar su presencia a lo largo de toda la cadena de fabricación, inclusive, después del proceso de fabricación aditiva. La configuración novedosa ‘core-shell’ adoptada en esta investigación, protege a la nanoparticula durante el proceso de transformación, y refuerza la matriz metálica.
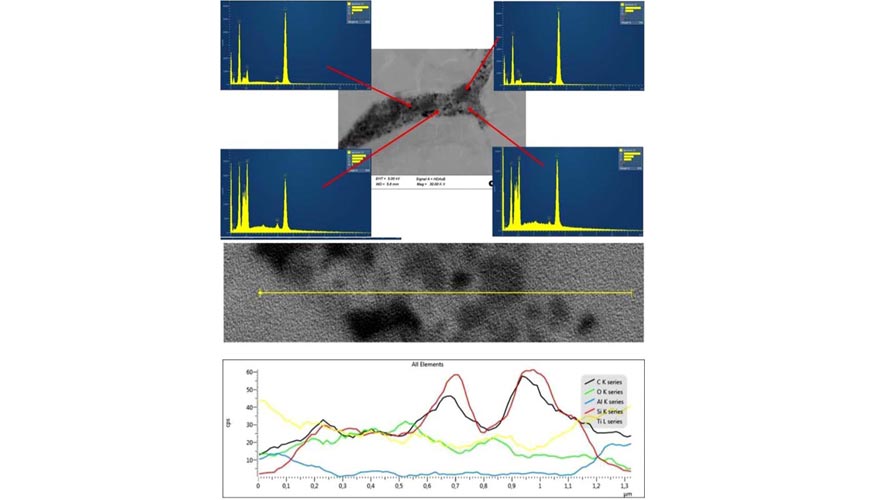
Matriz de Ti6Al4V consolidado con nanopartículas de carburo de silício (SiC) y recubrimiento de dióxido de titanio (TiO2) por HIP, para producir electrodos para el proceso EIGA.
Innovación mediante ‘core-shell’
En esta línea de trabajo, Nanotun3D proporciona un concepto innovador basado en estructuras ‘core-shell’ (núcleo-envoltura) para resolver esta limitación y mejorar así la dispersión y garantizar presencia de nanopartículas SiC, donde el núcleo es de carburo de silicio y el material exterior es un óxido de metal, bien óxido férrico (Fe2O3) bien dióxido de titanio (TiO2). En este sentido, la investigación aborda actualmente una serie de ensayos para la correcta síntesis y fabricación de la encapsulación ‘core-shell’ a escala piloto industrial que posibilite una adecuada incrustación de las nanopartículas de cerámica en la matriz de Ti6Al4V y mejorar así la interacción en todo el proceso, desde la obtención del polvo metálico, hasta el procesado de dicho polvo mediante tecnología de fabricación aditiva para obtener la pieza final.
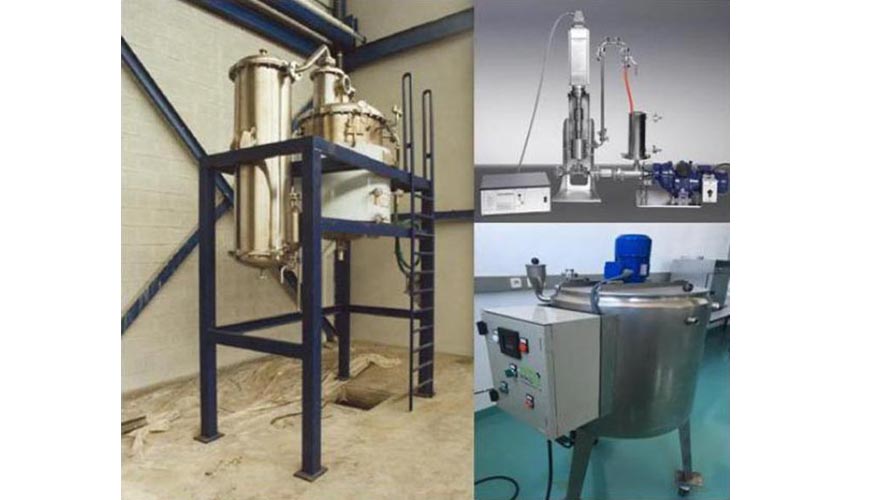
Equipos para la producción de nanopartículas ‘core-shell’ a escala industrial.
HSE
El proyecto considera también una parte fundamental del desarrollo de la investigación la incorporación de las políticas y estándares HSE (salud, seguridad y medio ambiente en inglés) para controlar los riesgos de seguridad asociados con el uso de nanopartículas a lo largo de la cadena de valor de la industria, y definirá procesos de trabajo seguros en la fabricación, manipulación y procesamiento del polvo metálico.
Fabricación del polvo, procesado FA y post-procesado
Además, el proyecto aborda nuevas líneas de investigación para la fabricación de polvo industrial a partir de las técnicas habituales de atomización tras la fundición, como pueden ser mediante gas (GA) y su variante por inducción de electrodos (EIGA), método este último más económico con aleaciones reactivas como el titanio. Del mismo modo, se trabaja simultáneamente en un rediseño del sistema de fundición por inyección (DIE) para atomización por gas, que permita insertar las nanopartículas durante el proceso de atomización para la fabricación del polvo metálico con una dispersión adecuada.
Al mismo tiempo, se están estudiando los ajustes de los parámetros necesarios para procesar el nuevo material nanomodificado mediante los sistemas SLM (sinterizado selectivo por láser) y EBM (fusión por haz de electrones) y las modificaciones que pueda requerir la maquinaria para el procesado del polvo, así como la reutilización del polvo residual.
La investigación contempla una exhaustiva evaluación de postprocesado en cuanto a los tratamientos térmicos y superficiales, entre otros factores como la facilidad del mecanizado, con objeto de mejorar la rugosidad, el comportamiento ante la fatiga, la reducción de las tensiones residuales y las distorsiones de las piezas fabricadas.
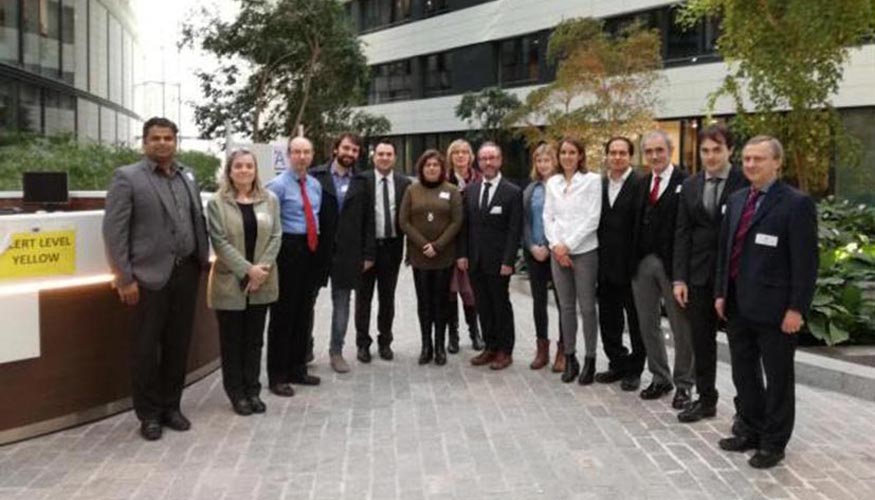
Los socios del Consorcio Nanotund3D en la reunión del proyecto celebrada en el Covent Garden de la Comisión Europea el pasado día 2 de febrero.
Propiedades del nuevo material Nanotun3D
En este sentido, el nuevo material nanomodificado Ti6Al4V, Nanotun3D, proporcionará piezas con una estructura reforzada frente a la aleación estándar, con un incremento del 30 al 40% de las propiedades de tracción, y entre un 20 y un 30% de mejora en el comportamiento mecánico de dureza, fatiga y desgaste, a mayores temperaturas, en torno al 15-25% superiores y con una determinante reducción del peso de las piezas.
Nanotund3D proyecta nuevos horizontes para la FA
Estos procesos o flujos de trabajo que están perfectamente definidos para la cadena de valor mediante el uso de SLM y EBM y la aleación Nanotun3D, pueden ser utilizados para otros materiales siguiendo idéntico proceso productivo, de tal modo, que la investigación prevé una cadena de suministro para la nueva aleación que también se podría trasladar a otros materiales metálicos nano-mejorados que incrementarían la gama de productos disponibles para la fabricación aditiva de metales de alto valor añadido.
El Instituto Tecnológico Aidimme se implica así en un escenario de presente y de futuro con un proyecto en pleno desarrollo y con altas expectativas para un entorno en constante evolución como las tecnologías aditivas para los metales. Un proyecto, Nanotun3D, que está financiado por el H2020 de la Unión Europea dentro del Programa de Investigación e Innovación bajo el acuerdo nº 685952, y que concluirá en 2019.
Socios del proyecto
- Universitat Politècnica de València (UPV)
- Laurentia Technologies SLL
- Vlaamse Instelling Voor Technologisch Onderzoek N.V. (VITO)
- TLS Technik GMBH & CO. Spezialpulver KG (TLS TECHNIK)
- Zoz GMBH (ZOZ)
- Asociación Centro de Estudios e Investigaciones Técnicas (IK4-Ceit)
- TWI Limited
- APR SRL
- Metal-Processing, Furniture, Wood and Packaging Technology Institute (Aidimme)