Soldadura de aceros inoxidables dúplex. No es difícil, sólo diferente
El acero inoxidable dúplex es un material especial desde el punto de vista metalúrgico. El término dúplex lo define bien: consiste en dos estructuras, una estructura ferrítica (como un acero al carbono) y una estructura austenítica (como la del inoxidable tipo 304L y 316L) (figura 1). Los aceros inoxidables dúplex son populares porque combinan las mejores propiedades de ambas estructuras, es decir, alta resistencia mecánica y excelente resistencia a la corrosión.
El fabricante de este tipo de aceros (por ejemplo Outokumpu) tiene como objetivo la obtención de un producto con un contenido austenita/ferrita en porcentaje 50/50%. Además de una composición química adecuada, el fabricante debe poner especial atención en la temperatura durante el proceso de fabricación, ya que hace falta un tratamiento térmico de recocido seguido de un enfriamiento rápido y controlado para finalmente obtener una estructura correcta compuesta de 50% de ferrita y 50% de austenita. El nitrógeno es un elemento de aleación especialmente importante para ‘congelar’ la estructura, en particular, la fase austenita.
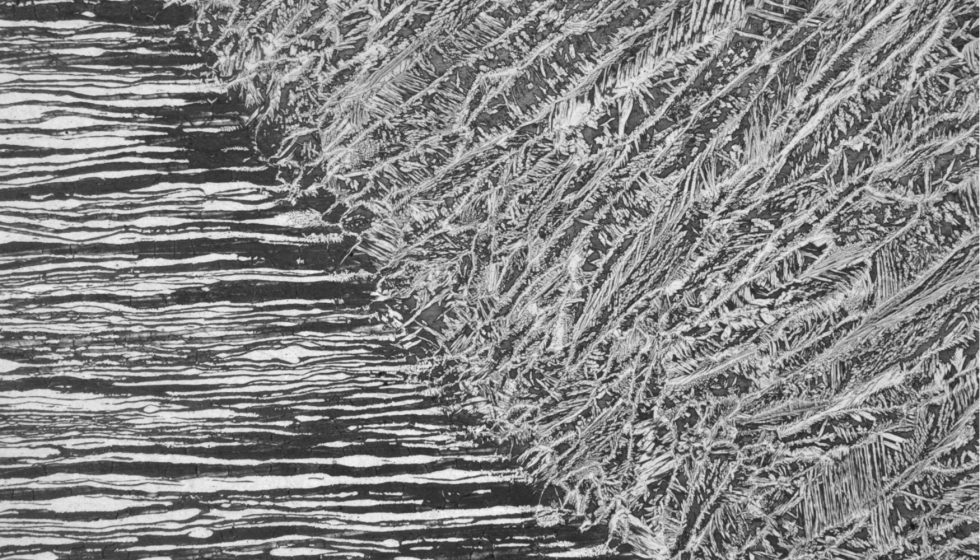
El desarrollo del acero inoxidable dúplex
Las primeras descripciones de aceros inoxidables dúplex datan de 1930, de acuerdo con Avesta Research Centre Outokumpu. Debido a su elevado contenido en carbono y a los problemas encontrados durante su soldadura, sus aplicaciones fueron muy limitadas (aceros inoxidables dúplex de primera generación). Hasta 1970 no fue posible fabricar aceros inoxidables dúplex con un contenido controlado en carbono, aleados con nitrógeno, naciendo así los aceros inoxidables dúplex de segunda generación. A día de hoy existen los aceros inoxidables dúplex de tercera generación, por ejemplo los lean dúplex, que son aceros desarrollados a partir del 1.4462 pero con un contenido más reducido en níquel y superior de manganeso y nitrógeno. Este grupo de lean dúplex tiene una resistencia a la corrosión similar a los grados austeníticos 304L/316L/317 L pero con la resistencia mecánica del acero inoxidable dúplex.
Existen otros aceros dúplex, denominados aceros inoxidables superduplex e hiperduplex, que debido a su mayor cantidad de cromo, molibdeno y nitrógeno (en otros casos también tungsteno y cobre) incrementan su resistencia a la corrosión. Finalmente también mencionar los nuevos aceros dúplex con mayor facilidad de conformación debido a un mecanismo denominado técnicamente como TRIP (Transformation Induced Plasticity). Las figuras 2 y 3 muestran el posicionamiento de diferentes calidades de aceros inoxidables.
Se desarrollan constantemente nuevas aplicaciones para estos aceros inoxidables dúplex, no tan solo como substitutos al acero inoxidable convencional por su resistencia a la corrosión, sino también en aplicaciones decorativas, donde se requiera resistencia mecánica elevada, etc.
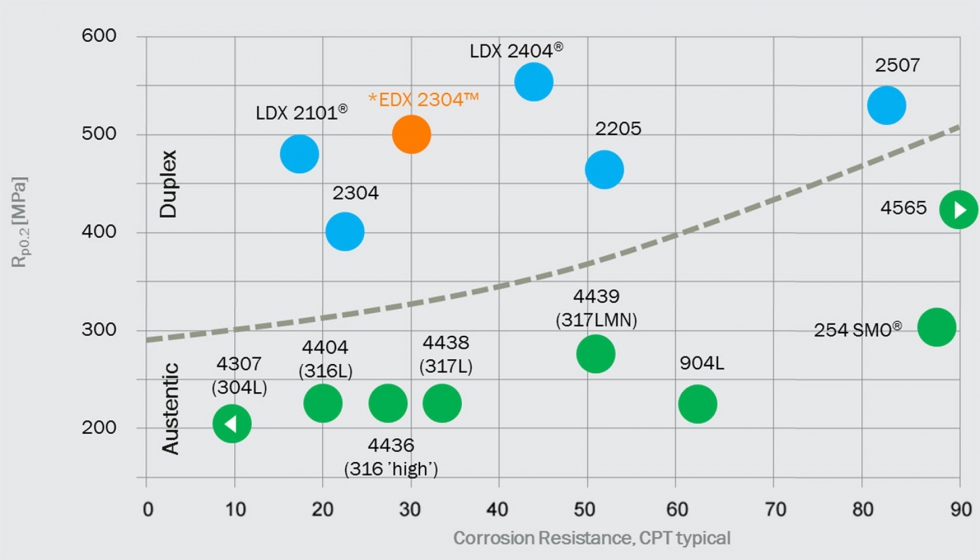
Medición de ferrita
El material base, por ejemplo chapa o tubo suministrado por el fabricante, contiene habitualmente una proporción de austenita/ferrita del 50%/50%. Cuando este material debe soldarse, sin embargo, podría cambiar a proporciones del 10%/90% en algunos casos (por ejemplo, si no se utiliza material de aportación para realizar la unión por soldadura). Si no se respeta una correcta proporción de ferrita y austenita, las propiedades del material (resistencia mecánica y a la corrosión) podrían cambiar significativamente. Es por ello que el contenido de ferrita debe medirse adecuadamente, mediante métodos basados en el magnetismo del acero analizado (por ejemplo, mediante Ferritoscopio), análisis micrográfico (mediante probeta previamente atacada) o mediante análisis químico del material y a través del diagrama WRC. Cada método tiene sus pros y contras, por ejemplo, el efecto de la rugosidad superficial, la calibración del equipo, etc. Es necesario que todas las partes (ingeniería, cliente final, contrata, proveedor de los consumibles de soldadura) tengan claro qué método debe utilizarse para su medición ya que existen ligeras diferencias entre los resultados obtenidos por cada método (figura 4).
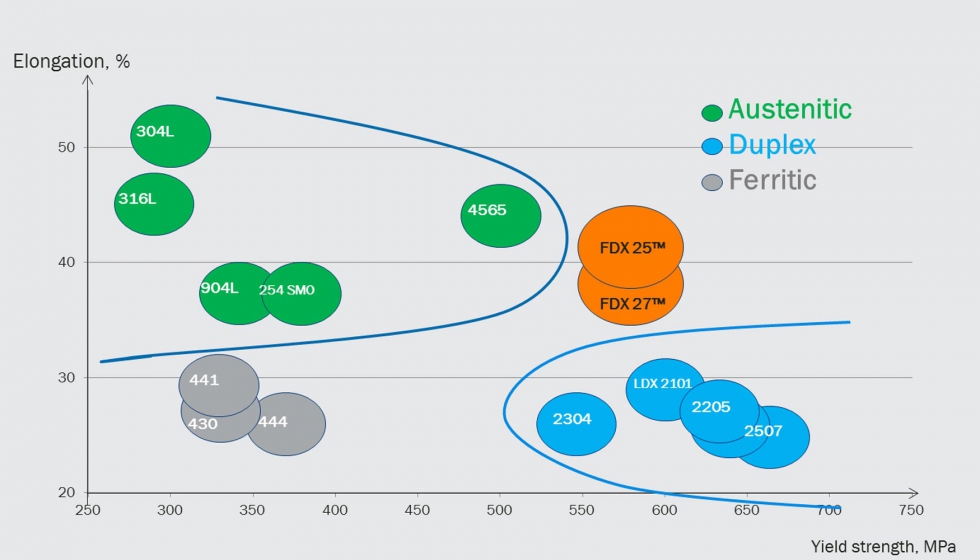
Cualificación de uniones de acero inoxidable dúplex
Los requisitos de las especificaciones para las uniones soldadas son en muchos casos difíciles de obtener o no son posibles de alcanzar, ya que se exigen valores mecánicos y de corrosión solamente alcanzables en el metal base. Y en otros casos, estos requisitos son difícilmente obtenibles en la cualificación de procedimiento de la unión soldada, pero de más dudable obtención en las soldaduras reales durante la fabricación. Hace falta exigir unos requisitos que sean reales y posibles para una cierta unión, sino se deben buscar alternativas, como la selección de materiales de soldadura sobrealedos respecto al material base; este es el caso de utilizar un consumible de soldadura de acero inoxidable superduplex para unir materiales base de acero inoxidable dúplex con el fin de otorgar a la unión soldada una resistencia a la corrosión superior. En otros casos, los valores mecánicos (valores de impacto a baja temperatura) requeridos para las uniones soldadas son tan elevados que solamente es posible tener resultados adecuados para las uniones soldadas con procesos de soldadura de menor productividad (por ejemplo TIG).
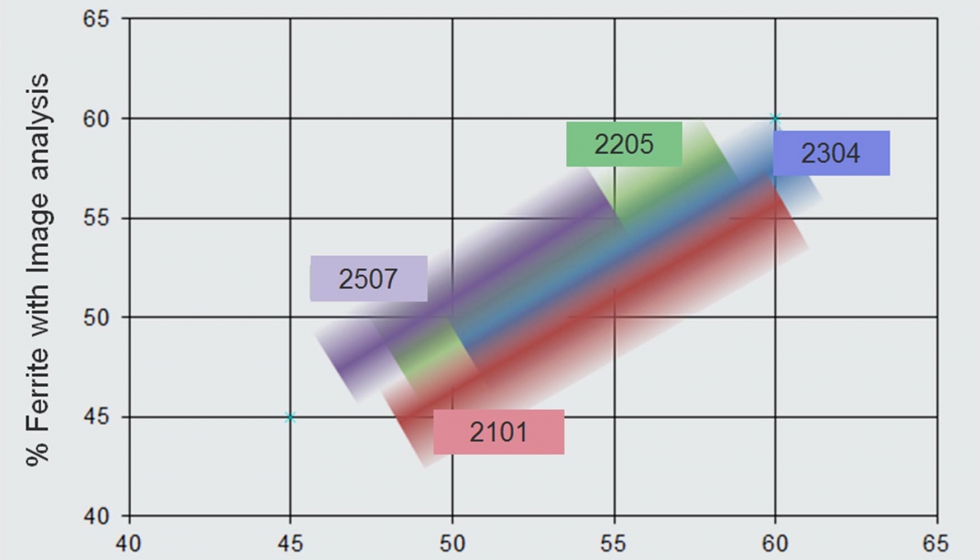
Tratamiento superficial y mantenimiento
Los aceros inoxidables también necesitan, en muchos casos, mantenimiento. La presencia de cromo produce en el acero inoxidable su capa de óxido protectora pasiva. Esta capa de óxido de cromo tarda aproximadamente 21 días en crecer hasta su espesor máximo. Un proceso de decapado y pasivado químico acelera este proceso de manera significativa, pudiendo alcanzar los resultados óptimos en unas pocas horas. Es importante destacar que el procedimiento de decapado y pasivado del acero dúplex, aunque es similar al de los aceros austeníticos tipo 316 L y 304 L, puede diferir en el tiempo de actuación, por lo que se aconseja seguir las instrucciones del proveedor de los productos decapantes y pasivantes (tabla 1). Hay estándares a seguir en los procesos de limpieza, decapado y pasivado químico (incluyendo los aceros inoxidables dúplex) tales como ASTM A380, ASTM A967 y BS 7773. En dichos procesos debe tenerse en cuenta su tiempo de actuación, la temperatura ambiente y el producto aplicado. El mantenimiento regular mediante productos de limpieza química del acero inoxidable dúplex es muy recomendable para mantener su bella apariencia y asegurar una vida en servicio adecuada.
Líquido desengrasante |
Pasta decapante |
Spray decapante |
Líquido por inmersión |
Líquido pasivante |
Avesta 402 |
Avesta 140 |
Avesta 204 |
Avesta 302 |
Avesta 630 |
Soldadura de aceros inoxidables superduplex
La elección del consumible de soldadura adecuado para los aceros dúplex y superduplex depende de variables como el material base utilizado, valores de impacto y mecánicos requeridos, etc. La tabla 2 muestra el consumible de voestalpine Böhler Welding adecuado para diferentes materiales base del tipo dúplex y superdúplex
Material Base (EN) |
Electrodo Revestido |
Hilo tubular |
Hilo MIG / Varilla TIG |
LDX 2101 (1.4161) |
Avesta LDX 2101 |
Avesta LDX 2101-PW |
Avesta LDX 2101 |
2205 (1.4462) |
Avesta 2205 |
Avesta 2205-PW |
Avesta 2205 |
2304 (1.4362) |
Avesta 2304 |
Avesta 2304-PW |
Avesta 2304 |
SAF 2507 (1.4410) |
Avesta 2507/P100 |
Avesta 2507/P100 |
Avesta 2507/P100 |
El acero superduplex es una variante mejorada del acero inoxidable dúplex. Debido al mayor contenido en cromo, molibdeno y, en particular, nitrógeno, el material es más resistente a la corrosión y es por ello muy popular. Sin embargo, el acero inoxidable superdúplex tiene más dificultades a la hora de soldarse que el dúplex normal. Un problema habitual es la porosidad del material resultante del proceso de soldadura. Esta porosidad proviene del elevado contenido de nitrógeno del material base y de los consumibles de soldadura y puede limitarse durante la soldadura MIG/MAG del acero inoxidable superduplex mediante la selección correcta del gas de protección, por ejemplo, Argón +20-30% Helio + 0,5% CO2. Un equipo de soldadura adecuado, con una curva sinérgica y programa de pulsado especial para estos aceros, facilitará mucho el trabajo. Otra posibilidad para limitar el riesgo de porosidad e incrementar la velocidad de deposición es la utilización de los hilos tubulares. Estos consumibles de soldadura, utilizando tanto gas 100% CO2 como 80%Ar+20% CO2, originan depósitos libres de defectos tales como faltas de fusión y porosidad. Dan lugar también a superficies más suaves (menos rugosas).
La velocidad de enfriamiento tiene un gran impacto sobre los resultados finales. Esto significa que son especialmente importantes unos parámetros de soldadura correctos, preparación de junta adecuada, aporte térmico y temperatura entre pasada.
La soldadura TIG sin metal de aportación no es adecuada, debido al contenido excesivo de ferrita en el depósito de soldadura. Al utilizar material de aportación, el contenido de las fases austenita y ferrita es adecuado para la obtención de soldaduras resistentes a la corrosión y con buenas propiedades mecánicas. El empleo de gases de protección y respaldo conteniendo nitrógeno es beneficioso para compensar la disminución de nitrógeno del material base durante el proceso de soldadura. Hemos de recordar que el nitrógeno es un elemento fundamental para proporcionar una resistencia a la corrosión adecuada a la unión. El aporte térmico de la pasada de raíz y de la segunda pasada afectará en la presencia de precipitados metálicos indeseados y podrá alcanzarse un porcentaje de fases adecuado en la estructura. De esta manera, la primera pasada (pasada de raíz) es relativamente gruesa, mientras que la segunda pasada es más fina (con menor aporte térmico) (figura 5).
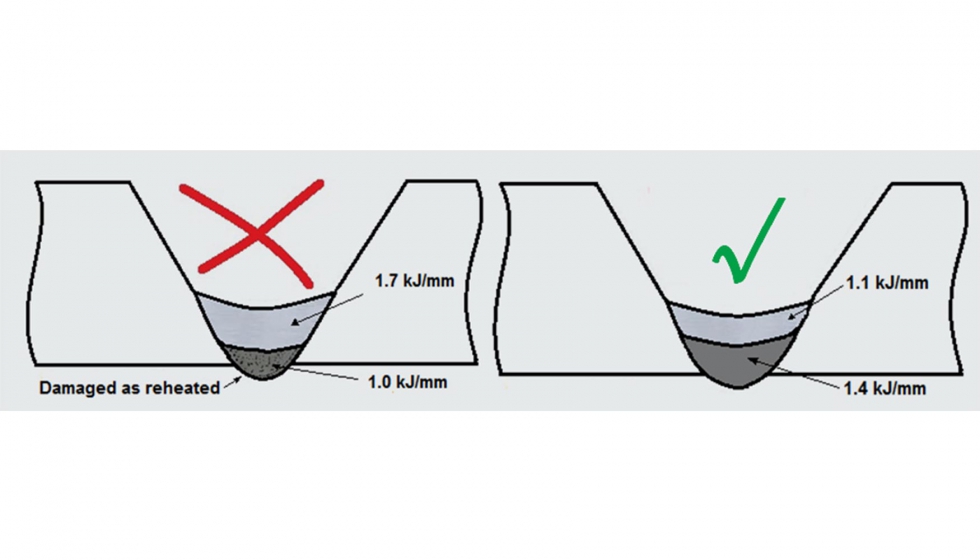
También es posible unir acero inoxidable dúplex con acero al carbono. En este caso, existen dos opciones, la utilización del mismo aporte de acero inoxidable dúplex o el consumible 309 LMo (o 309 L). La utilización de 309 LMo (o 309 L) es ideal para realizar uniones con mayor tenacidad en la zona donde exista una dilución significativa con el acero al carbono.
Ejemplo real: Construcción de tanque de almacenamiento
Cuando Damm, uno de los mayores fabricantes de cerveza en España, necesitó reemplazar un viejo depósito, se decidieron por Outokumpu Forta DX 2205 debido la resistencia mecánica y a la corrosión del acero inoxidable.
El viejo tanque, realizado en acero al carbono, se utilizó como tanque intermedio que contuvo 3 millones de litros de aguas residuales. Solo duró 3 o 4 años, debido a la corrosión producida por los agentes químicos utilizados para tratar el residuo.
Parcitank, uno de los fabricantes de depósitos más grandes en Europa, aconsejó a Damm que utilizara el acero dúplex para construir el nuevo tanque (figura 6).
“La gran ventaja es que resiste a la corrosión mucho mejor que el acero al carbono o un acero inoxidable austenítico estándar, es por ello que decidimos que el acero dúplex Forta DX 2205 era el más adecuado”, explica Antonio Parra, director de Producción de Parcitank.
Para Parcitank, otra gran ventaja de la utilización de este dúplex es la reducción de espesor. “Una reducción de 2 ó 3 milímetros da lugar a un gran descenso del peso”, explica Parra. De esta manera, un tanque de peso típico de 80 toneladas pesaría 60 t con la utilización del dúplex. Para este proyecto, Parcitank utilizó material base en bobinas de 2.000 milímetros de anchura y espesor de 5 ó 6 mm, así como bobinas de 1.500 mm y espesores de 6 a 8 mm.
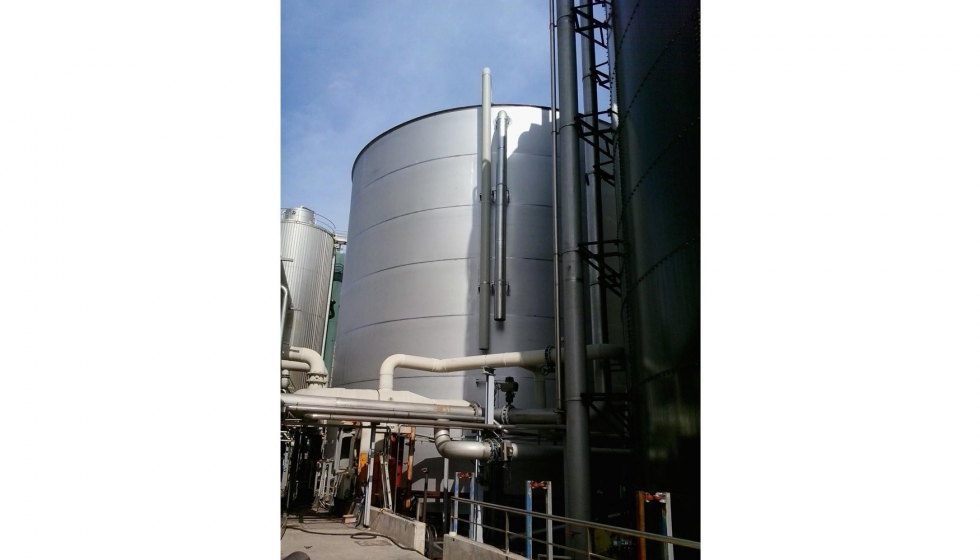
Figura 6: Tanque de acero dúplex realizado por Parcitank.
Agradecimientos
Muchas gracias a Geri van Krieken y Johan Cobben de voestalpine Böhler Welding Nederland, por su importante contribución en el artículo. También a los miembros de Outokumpu S.A. por su colaboración.