Stratasys y Worrell aceleran el desarrollo de dispositivos médicos gracias al uso de moldes de inyección impresos en 3D
10 de noviembre de 2014
Stratasys, proveedor mundial de soluciones de impresión 3D y fabricación aditiva, ha anunciado su colaboración con la empresa de diseño y desarrollo de producto Worrell, con el objetivo de acelerar el desarrollo de equipamiento médico a través de la utilización de moldes de inyección impresos en 3D (3D IM). Mediante el uso de moldes de inyección impresos en 3D para dispositivos médicos, la empresa produce piezas prototipo inyectadas con materiales de producción final en un 95% menos de tiempo y con unos costes 70% inferiores comparado al uso de moldes de aluminio tradicionales.
En una iniciativa por contribuir al inmenso ahorro de costes que 3D IM proporciona a los fabricantes de dispositivos médicos, así como a la reducción notable de sus ciclos de desarrollo de productos, Stratasys y Worrell participarán conjuntamente en ferias internacionales y ofrecerán una serie de talleres para formar a la industria médica en este innovador proceso y en su enorme impacto en fabricación.
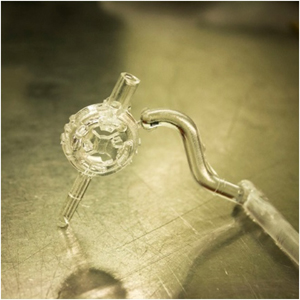
“Hemos constatado una utilización del moldes impresos en 3D para inyección durante el desarrollo de dispositivos médicos muy por debajo de sus posibilidades y queremos trabajar con Worrell para corregir esta tendencia“declara Nadav Sella, director senior de utillaje de fabricación en Stratasys.”Worrell es una empresa de diseño líder en el sector, con la experiencia y la infraestructura necesarias para integrar inyección de molde e impresión en 3D dentro de su ciclo de desarrollo de productos. En un sector cuyos productos tienen el potencial de salvar vidas, queremos que esta colaboración sirva para demostrar cómo los fabricantes de dispositivos médicos pueden introducir al mercado sus productos mucho más rápido que nunca”.
Tradicionalmente, los fabricantes de dispositivos médicos se enfrentan a dos principales obstáculos a la hora de lanzar sus productos al mercado: los costes del utillaje y los procesos de las agencias regulatorias. Hasta ahora, la producción de utillaje ha sido costosa en términos de inversión y de tiempo, dado que, antes de la fabricación, se debían crear moldes nuevos o hacer costosas modificaciones con cada revisión de los prototipos. En aras de reducir los potenciales riegos de iteración y los costes de las herramientas, Worrell emplea las impresoras 3D basadas en la tecnología PolyJet de Stratasys para crear moldes de inyección e inyectar los mismos materiales que se utilizarán en el dispositivo médico final, con lo que se crean prototipos mucho más fiables.
“Recientemente, MedTG, una empresa emergente dedicada a los dispositivos médicos, se ha interesado por nuestros métodos para el diseño y la ingeniería de un sistema de extracción de sangre de doble flujo sin aguja que reduce la necesidad de múltiples inyecciones y, por tanto, resulta mucho más cómodo para los pacientes y mucho más eficaz para el hospital. El uso de moldes de inyección impresos en 3D para la fabricación de los prototipos nos ha permitido reducir los costes asociados a utillaje tradicional en un 70% aproximadamente y, el tiempo, en un 95%”, explica Kai Worrell, CEO de Worrell.
Worrell concluye: “Gracias a los moldes de inyección impresos en 3D hemos podido crear prototipos por una fracción del coste en cuestión de días, frente a las ocho semanas que suelen tardar los procesos tradicionales. Este revolucionario proceso de fabricación, que debemos a la tecnología basada en PolyJet de Stratasys, forma ya parte integral de nuestro ciclo de desarrollo de productos, lo que nos permite presentar mejores prototipos y ahorrar a nuestros clientes una considerable cantidad de tiempo y de dinero”.