Entrevista a José Antonio Ocaña, director de fábrica de Symaga
Symaga es una empresa preparada para ofrecer un servicio global a los clientes partir de sus cuatro divisiones: Silos, para la fabricación y comercialización de silos industriales para almacenamiento de grano; Livestock para proyectos integrados para ganadería, para avicultura, porcino, ovino y bovino; Agriculture, para fabricación de poste de viña y depósitos de almacenamiento de agua; y Steel Works para tratamientos y procesos de aceros e inyección de plástico. Conscientes de la alta calidad que demandan sus clientes, en Symaga y las especificidades de sus productos, encontraron en Geka un proveedor “capaz de adaptarse a nuestras necesidades de automatización”, como explica José Antonio Ocaña, director de fábrica de Symaga.
Actualmente, Symaga presume de exportar un 95% de su producción. ¿Qué aconseja a las empresas que quieran salir al exterior tras su favorable experiencia?
La internacionalización de una empresa es un proceso que requiere un equipo de exportación, que estudie los mercados previamente para determinar si el producto puede tener éxito o si requiere alguna adaptación y que afiance relaciones con cliente y/o distribuidores, garantizando la correcta introducción del producto. Es determinante tener una producción con calidad estandarizada y una red comercial potente.
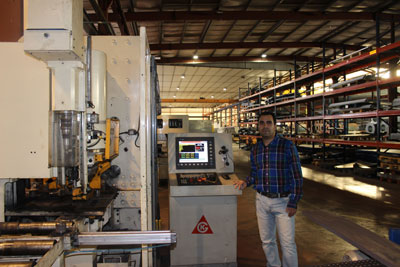
¿Considera la inversión en I+D+i como uno de los motores de crecimiento para Symaga?
El presupuesto de inversión en I+D+i en Symaga es un 9% de su facturación, para este 2014 es de 4 millones de euros y en 2007 alcanzó los 6 millones de €. Symaga considera que para mantener un producto en el mercado hay que tenerlo actualizado. Además, nuestro equipo de ingenieros colabora con la universidad Politécnica de Madrid y con equipos de investigación internacional, como el Bipree.
Symaga factura cerca de 50 millones de euros al año. ¿En que consideran que es fundamental invertir?
Como hemos comentado en I+D+i, pero tambien en la estandarización de la calidad a través una fabricación automatizada y fiable, a finales del año pasado fuimos los primeros en obtener el certificado CE para la fabricación de silos, esto confirma que tenemos un control de fabricación homologado externamente, y no podemos olvidar el servicio al cliente, como valor añadido de Symaga, ya que el departamento comercial siempre esta apoyado en la venta con un equipo de ingenieros.
¿Qué nuevos materiales han venido introduciendo en sus productos?
La materia prima es fundamental en nuestra actividad porque garantiza la durabilidad el producto, este año hemos introducido el Z600 como estándar de fabricación, incrementando un 33% el recubrimiento y la protección.
Symaga tiene capacidad para transformar unos 2 millones de quilos de acero semanales gracias a la fabricación automatizada. ¿En qué maquinaría confían para cumplir con las exigencias de sus clientes?
Sin duda, son las últimas tecnologías del sector las que ponemos a nuestra disposición.
¿Desde cuándo cuentan con las soluciones de Geka? ¿Qué les ha hecho decantarse por este proveedor?
La máquina Geka más antigua que tenemos es de 1991. Uno de los puntos más importantes para decantarnos por Geka es la fabricación a medida de las máquinas cumpliendo con todos nuestros requisitos y adaptándose a nuestras necesidades. Además Geka siempre ha tenido una respuesta a nuestras necesidades de automatización, lo cual nos hace ser más competitivos, esto unido al servicio técnico de calidad que ofrecen con asistencia técnica inmediata y técnicos cualificados, hacen de Geka un proveedor importante en nuestra organización.
¿Qué modelos Geka podemos encontrar en su parte de maquinaria y cuál ha sido la última incorporación?
Disponemos de 2 máquinas manuales Geka, y convienen destacar los modelos automáticos que tenemos concretamente:
- Geka Alfa 500: con posibilidad del corte y taladrado de productos planos y angulares.
- Geka Automática para llantas.
- Geka Automática para tubos.
- Y la última incorporación la Geka Alfa 500-220T: Un sistema completo de procesado para el punzonado, taladro, marcado y corte de llantas controlado numéricamente y programable mediante CNC basado en PC. Para procesar llantas de 50 a 500 mm de ancho y hasta 35 mm de espesor y Longitud del material 6 o 12 metros, de alta resistencia.
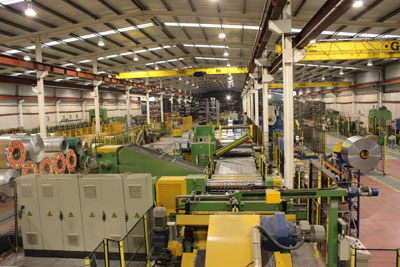
Colaboran estrechamente con el proveedor Geka. ¿Qué ventajas aportan las herramientas de su proveedor?
En cuanto a las herramientas cabe destacar la flexibilidad del diseño y fabricación de herramientas especiales, así como la relación calidad-precio, tanto de estas herramientas especiales como de las herramientas más comunes.
Para finalizar, ¿Pueden destacar algún proyecto innovador que provenga del presupuesto destinado a I+D+i?
Ademas de una revisión constante del silo industrial, el presupuesto de I+D+i de estos ultimo años está destinado a la definición de proyectos completos de ganadería.