Aumento de la fiabilidad de las máquinas de corte por agua y abrasivo a través de la monitorización
La tecnología de corte por chorro de agua y abrasivo es un proceso de mecanizado flexible, barato y rápido que puede mecanizar cualquier tipo de material, incluso los de baja maquinabilidad como pueden ser el Inconel y el Titanio. Sin embargo, debido sobre todo a la falta de integración de sistemas de monitorización y control del proceso, la fiabilidad que ofrece este tipo de máquinas industriales es baja en comparación con otras tecnologías.
Durante las operaciones de mecanizado que utilizan la tecnología de corte por agua y abrasivo pueden existir múltiples desviaciones de parámetros respecto a sus valores de consigna que provocan que las máquinas trabajen pero sin conseguir piezas buenas. Ésto además de producir un alto desperdicio de tiempo y de recursos energéticos supone un alto riesgo económico para cortar piezas de alto valor añadido en las que el coste de la materia prima es elevado, y por lo tanto, asegurar una alta fiabilidad del proceso es crucial.
1. Introducción
La tecnología de corte por agua y abrasivo (AWJ) se basa en un chorro de agua a alta presión al cual se le añaden partículas de abrasivo que son dirigidas por una boquilla focalizadora. En el cabezal se forma entonces un chorro compuesto por agua presurizada, aire y abrasivo a velocidades en torno a 300 y 1000m/s que es capaz de eliminar el material deseado mediante la erosión del mismo. Es decir, la tecnología de corte por agua y abrasivo (abrasive water jet) consiste en hacer incidir el chorro sobre un material el tiempo suficiente para que el chorro atraviese el mismo [1].
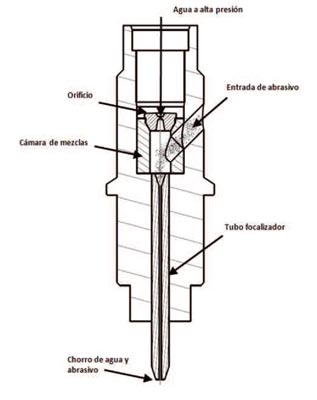
Es un proceso de mecanizado flexible, barato y rápido que puede mecanizar cualquier tipo de material. Sin embargo, el proceso de corte por AWJ presenta algunas limitaciones prácticas que condicionan su productividad, la evolución en las máquinas de agua se ha centrado en el aumento de ésta, incrementando para ello la presión hidráulica. Es cierto que a mayor presión, se obtiene una mayor potencia de corte, pero este aumento en la potencia de corte lleva asociados otros daños colaterales, como por ejemplo, un aumento del desgaste de los componentes del sistema de alta presión o un mayor desgaste de la herramienta de corte. Ésta evolución en los sistemas de alta presión ha dejado en evidencia otros problemas concernientes a la tecnología, como la baja incorporación de sensores para llegar a una automatización completa de estas máquinas comerciales.
Existen múltiples fallos o desviaciones del proceso respecto a sus valores de consigna que provocan que la calidad de las piezas obtenidas no sea la requerida. Estos fallos pueden deberse al desgaste de la boquilla, al atasco de abrasivo en la boquilla o en el conducto de abrasivo, a la rotura de la boquilla o a la fuga de agua en el conducto de agua a alta presión. Estas limitaciones dificultan la producción desatendida de las máquinas de AWJ, por lo que es necesario desarrollar un sistema para la detección de fallos asociados a estas causas.
En la bibliografía se pueden encontrar varias técnicas para la monitorización de los posibles fallos que pueden ocurrir en las máquinas de corte por agua. Annoni et al [2] estudiaron la posibilidad de controlar simultáneamente el caudal de abrasivo y la velocidad transversal, para lo que desarrollaron un aparato capaz de controlar continuamente el caudal de abrasivo. Louis y Meier [4] relacionan el diámetro de la boquilla con el flujo de aire succionado por la boquilla a través del tubo de alimentación de abrasivo, así como las pérdidas de presión en el tubo de alimentación de abrasivo. Si el tubo focalizador cambia su forma de manera significativa durante la fabricación de una pieza es imposible llevar a cabo un corte preciso [5], de aquí la necesidad de monitorizar el desgaste de estas piezas para asegurar la calidad de corte. La detección de desgastes y roturas es también posible con sensores de emisiones acústicas y con la medición del nivel de vacío en la cámara de mezclas [7].Con el objetivo de controlar la distancia de trabajof, Jurisevic et al. [8] realizaron un estudio relacionando esta distancia de trabajo con el nivel sonoro que se genera en el proceso, . Los resultados alcanzados mostraron que es posible filtrar esta señal y relacionar con la distancia de trabajo pero siempre bajo condiciones de trabajo controlados, pero mostraron dificultades para ser implementadas en condiciones de trabajo reales donde factores externos generan niveles de ruido que perturban la señal original del proceso. Axinte y Kong [9] miden las fuerzas remanentes del chorro tras el corte utilizando para ello una mesa Kistler, el objetivo que persiguen es relacionar esta fuerza con las estriacionesde las piezas cortadas.
Ha quedado patente la importancia de tratar de controlar el máximo número de parámetros que afectan a este proceso, pero todo Es importante controlar el máximo de parámetros posibles para poder detectar además de los posibles fallos debidos al suministro de abrasivo y al desgaste de las piezas, cualquier otro problema (como puede ser un fallo en la presión suministrada por la bomba) que pueda influir en la calidad de las piezas cortadas.
2. Control de suministro de abrasivo
Los fallos por atascos de abrasivo son muy comunes y pueden dar lugar a un atasco de la boquilla o a un atasco en el conducto de abrasivo. En los casos en los que se obstruye el conducto de abrasivo la máquina sigue funcionando, al no disponer de abrasivo en el chorro se pierde la capacidad de corte de materiales duros o de elevado espesor, por lo que aunque la máquina sigue funcionando, únicamente se consigue marcar las chapas y no cortarlas, malgastando tanto tiempo como materia prima y energía.
Se plantea un sistema para la monitorización de las condiciones instantáneas del proceso, resultando un sistema capaz de detectar de forma eficaz las situaciones de atasco en el conducto de abrasivo y de la boquilla.
Para desarrollar este sistema previamente se llevaron a cabo varios ensayos para llegar al sistema final. Se pueden utilizar diferentes metodologías para la detección de un atasco en el suministro de abrasivo. Una de las opciones es mediante la detección del sonido (LAT) aislando las diferentes fuentes de ruido. Jurisevic y Junkar [3] han conseguido un sistema basado en este principio que se puede integrar en la máquina. Sin embargo en los ensayos llevados a cabo en Tecnalia R&I la medida del ruido no resulta ser un método muy robusto, dado que existen múltiples fuentes que provocan niveles de ruido elevados (aunque en su mayor parte instantáneos) que nada tienen que ver con el consumo o no de abrasivo: movimientos en vacío de la máquina, cambios de dirección, perforaciones, entrada o salida del chorro de la chapa a cortar y otros.
Otra de las opciones estudiadas consiste en la medición de la resistencia eléctrica entre entrada y salida así como la temperatura en el conducto de suministro de abrasivo, ya que teniendo en cuenta que el agua es conductora y se calienta se puede detectar la presencia de agua en el conducto de abrasivo. En el interior del tubo el agua provoca un cambio brusco de temperatura de al menos 30°C. La temperatura registrada en funcionamiento normal no es constante, se han medido oscilaciones lentas entre 28°C y 10°C, en función principalmente de los rebotes y salpicaduras de agua sobre el sistema de detección. El flujo de aire (o aire y abrasivo) por el interior del tubo enfría el sensor de temperatura y si las salpicaduras son bajas, la temperatura resultante es menor a la ambiente. Si ocurren salpicaduras, la temperatura puede alcanzar los casi 30°C. En cualquier caso, las variaciones debidas a estos motivos son lentas. Cuando ocurre un atasco de boquilla, la subida de temperatura es repentina, casi instantánea y de temperatura muy superior a los 30°C.
Por último, la opción más fiable se basa en la monitorización de la depresión generada en el tubo de abrasivo debido al efecto Venturi que provoca el chorro de agua en la cámara de mezclas. Ésta depresión depende de la velocidad del chorro y de la oposición generada en el tubo. Se deduce que existirá un valor de depresión para condiciones normales de corte, que si el tubo de abrasivo se atasca en un punto entre el punto de medida y la cámara de mezclas no existirá depresión y que si se atascara en un punto entre el punto de medida y la toma de abrasivo la depresión será máxima. Sin embargo, esta depresión en condiciones habituales es muy pequeña, por tanto se opta por introducir un estrechamiento en el conducto de abrasivo para generar una depresión suficiente para ser diferenciada, pero que a su vez permita circular los caudales de abrasivo originales. Se han llevado a cabo ensayos con diferentes estrangulamientos comerciales de la marca FESTO, llegando a la conclusión de que para que la medición de la caída de depresión sea fiable es recomendable el uso de un estrangulamiento con una geometría interior diferente a la utilizada en los estrangulamientos comerciales. Por tanto se ha diseñado un estrangulamiento propio para poder obtener una señal óptima a la hora de detectar cualquier posible fallo sin que su inserción en la máquina suponga ninguna variación en el proceso.
En la Figura 2 se muestra un gráfico de la depresión generada en el tubo de abrasivo cuando se fuerza un atasco en el mismo con el estrangulamiento diseñado en Tecnalia. Se puede ver que la caída de presión es suficientemente estable y diferenciable, lo que permite que éste sea un sistema fiable para la detección de atascos en el tubo de abrasivo.
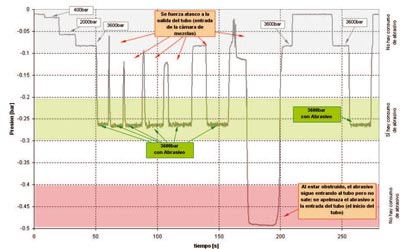
Se ha desarrollado un sistema para su instalación en máquina, que gracias a la utilización del estrangulamiento diseñado y a un sensor de presión instalado en el conducto de abrasivo, es capaz de detener la máquina cuando se produce un atasco en el mismo (Figura 3). El sistema funcionará de manera que cuando exista una demanda de abrasivo y no esté llegando al cabezal de corte, éste lo detecte y pare la máquina. Cuando no exista demanda y no haya tampoco consumo, la máquina continuará funcionando normalmente al igual que cuando exista demanda y haya consumo.
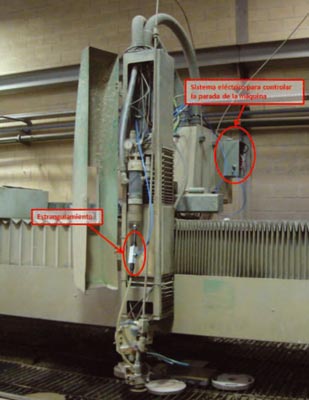
3. Control del corte
3.1 Medición Desgaste Boquilla y Zafiro
Tanto la boquilla como el zafiro sufren desgaste en el cabezal de corte debido a que a través de ellos pasa el agua a alta presión constantemente, si las partículas de abrasivo llegasen hasta el zafiro puede incluso producirse la rotura del mismo de manera que el chorro no llega a formarse correctamente (Figura 4).
![Figura 4. Expansión del chorro con diferentes desgastes de zafiro y boquilla [6] Figura 4. Expansión del chorro con diferentes desgastes de zafiro y boquilla [6]](https://img.interempresas.net/fotos/914411.jpeg)
La monitorización del desgaste de estas piezas se puede llevar a cabo de distintas maneras. El mismo sistema de control para el suministro de abrasivo consistente en la medición de la depresión creada en el tubo de abrasivo sirve también para detectar una rotura o desgaste de boquilla y zafiro. En las pruebas realizadas se ha detectado que el valor de la depresión varía en función de si estas piezas se encuentran en buen estado o no. En la Figura 5 se puede apreciar la señal recogida de depresión en el tubo de abrasivo utilizando abrasivos en diferente estado (nuevo, desgastado y roto), se ve que según la salud del empeora la depresión generada es mayor.
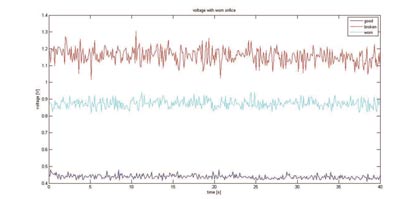
La detección del ruido es otra de las opciones a la hora de detectar un desgaste de las piezas del cabezal de corte. Se sitúa un micrófono junto al cabezal de corte y se mide el ruido generado durante el proceso relacionando las variaciones en las señales recogidas con desgastes o roturas de las distintas piezas. En este caso, debido al ruido que conlleva el proceso es complicado detectar señales de ruido claras que puedan indicar un desgaste con fiabilidad. En la Figura 6 se puede ver como en la señal de ruido, aunque se aprecia que existe un cambio, no es fácilmente identificable ya que es una variación pequeña y además se trata de una señal poco estable.
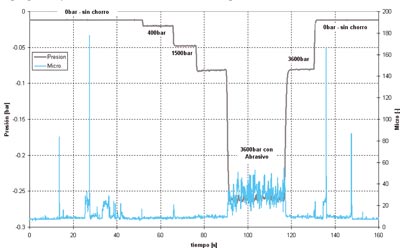
La detección de desgastes y roturas es también posible con sensores de emisiones acústicas y con la medición del nivel de vacío en la cámara de mezclas [7]. Se sitúa un sensor en la boquilla sujeto mediante una pieza metálica y otro sobre el material en el que se está trabajando (se puede ver esta configuración en la Figura 9). Con este método se podrá detectar si el zafiro está en buen estado y si se produce desgaste en la boquilla.
Se han llevado a cabo ensayos con un sensor de emisiones acústicas instalado en la boquilla del cabezal de corte cambiando los parámetros del chorro (presión y caudal de abrasivo) con el fin de conocer si las variaciones en el chorro son detectables mediante este tipo de sensores. Como puede verse en la Figura 7 se observa que mediante la obtención de esta señal se pueden llegar a detectar variaciones pequeñas en el chorro, como es el caso de una variación de abrasivo de tan solo 50g/min.
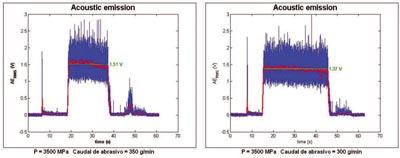
Este hecho abre las puertas a una experimentación más amplia con el fin de establecer los rangos en los que se encontrará ésta señal según se van desgastando zafiro y boquilla.
3.2 Energía del chorro
El proceso de formación AWJ consiste en acelerar las partículas abrasivas con un chorro de agua a alta velocidad. Una vez el chorro de agua a alta presión pasa por el orificio situado en lo alto de la cámara de mezclas se convierte en un chorro a alta velocidad en el que se inyectan las partículas de abrasivo, éstas se aceleran en su trascurso por la boquilla generando un chorro con una gran potencia de corte que choca contra el material erosionándolo. Según el tamaño del zafiro y la boquilla, la fuerza que tendrá el chorro será distinta, por lo que controlando la fuerza de impacto del chorro sobre el material se podrán detectar posibles desgastes en orificio y boquilla. Es posible relacionar también las marcas que existen en el material cortado con posibles variaciones en la potencia del chorro, lo que permite conocer la calidad del corte en función de las señales de las fuerzas de impacto.
![Figura 8. Parámetros del proceso. [8] Figura 8. Parámetros del proceso. [8]](https://img.interempresas.net/fotos/914415.jpeg)
Una de las posibles maneras de medir la fuerza del chorro es utilizando una mesa dinamométrica para medir la energía sobrante del chorro tras cortar el material y relacionarlo con las calidades de corte (Figura 9). Se mide el impacto del chorro en la mesa a la salida del corte, en el que quedan pequeñas estriaciones cuyo tamaño y frecuencia dependerán de la energía del chorro en ese momento. Cuanto peor sea la calidad del corte menor será la fuerza que ejercerá el chorro sobre la mesa.
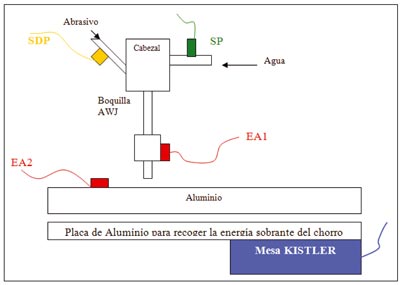
En los ensayos correspondientes además de la obtención de las fuerzas con la mesa Kistler, se colocan también sensores de emisiones acústicas para detectar si existe alguna relación entre las estriaciones que se producen en la pieza y las señales recogidas de fuerza y emisiones acústicas.
Se llega a la conclusión de que las fuerzas medidas con la mesa Kistler no guardan mucha relación con las estriaciones medidas sobre la pieza. Sin embargo, en el estudio de las señales de emisiones acústicas se puede apreciar que realizando un análisis en frecuencia los valores obtenidos se corresponden con aquellos medidos sobre la pieza (Figura 10).
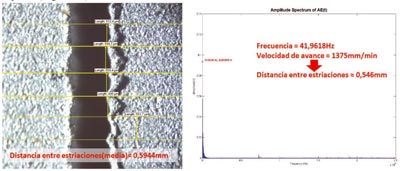
Por tanto, se deduce que mediante el análisis de las señales de emisiones acústicas se puede llegar a conocer las estriaciones que se obtendrán en la pieza final.
3.3 Presión y fugas
La base fundamental del proceso es el agua a alta presión, una variación en la presión puede ser señal de desgate de algún componente de la bomba o de una fuga en las tuberías de alta presión. Se conoce gracias a la experimentación realizada que monitorizar la presión puede ayudar a conocer la salud del zafiro, se han obtenido datos con diferentes tamaños de zafiro que indican que la presión que llega al cabezal es diferente según el diámetro del zafiro. En la Figura 11 se puede ver la diferencia que existe en la señal de presión cuando cambia el tamaño del zafiro.
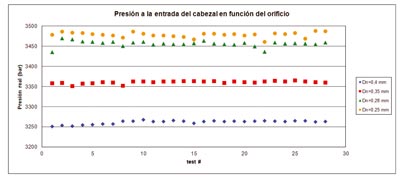
Disponiendo de dos sensores de presión se puede llegar a detectar las fugas o los desgastes de los componentes monitorizando en todo momento la diferencia de presión entre un sensor y otro.
Con la medición de la presión en el cabezal de corte se ha visto que la presión que llega al mismo no es la misma que la que proporciona la bomba e indica la máquina, sino que siempre existen unas pérdidas de presión debidas al número de codos, longitud de la tubería, etc. Controlando el valor de la presión en cabezal se controla que la presión de corte es la adecuada y se conoce para el tratamiento de las señales y los posteriores cálculos el valor real de la presión que se está utilizando durante los ensayos [10].
Lo que se pretende con la introducción de un segundo sensor a la salida de la bomba es conocer realmente si el valor de la presión en el cabezal es debido a las pérdidas propias de la distribución de la máquina o porque el agua no sale de la bomba con el valor de presión comandado desde el control.
4. Conclusiones
En este artículo se muestran los principales problemas que se producen durante el mecanizado mediante chorro de agua y abrasivo además de algunas de las técnicas de monitorización que pueden ser utilizadas. Se ha mostrado que son muchos los parámetros que intervienen y tienen efecto en el corte con esta tecnología. Cada uno de estos parámetros del proceso tiene un efecto distinto en las piezas cortadas. El control y monitorización de los distintos parámetros puede ayudar a hacer de este proceso, que en estos momentos está poco monitorizado, un proceso más fiable y preciso de manera que sea fácil tanto predecir un desgaste en la boquilla o el zafiro como detectar un error en la pieza por falta de presión o de abrasivo, pudiendo así parar la máquina y evitando de esta forma grandes cantidades de material y tiempo desperdiciados.
Aunque las técnicas mostradas son fiables a nivel de laboratorio, el principal problema se encuentra en cómo incorporar todos estos sensores dentro de un ambiente tan agresivo como el agua, el polvo y el abrasivo.
5. Agradecimientos
Los autores quieren agradecer el apoyo y la implicación durante este proyecto a la empresa MTorres, además de agradecer el apoyo recibido desde el Gobierno Vasco a través de programas de apoyo a proyectos de investigación industrial y desarrollo experimental de carácter estratégico.
Referencias
[1]. M.Hashish, Inside AWJ nozzles; 2003 WJTA American Waterjet Conference
[2]. M. Annoni, M.Monno y A. Henning, The continuous control of the abrasive mass flow rate and feed rate as a new opportunity in the AWJ precision machining, presented at he 16th International Conference on Water Jetting, Aix en Provence, France, 2002
[3]. B.Jurisevic y M.Junkar, Adaptative Control Constraint (ACC) of Abrasive Water Jet Cutting, presented at the International Conference on Water Jetting Machining WJM, Cracow, 2001, pp.71-76.
[4]. H.Louis y G.Meier, Methods of Process Control for Abrasive Water Jets, presented at the 6th American Water Jet Conference, Houston, Texas, 1991.
[5]. J.J Rozario Jegaraj y N.Ramesh Badu, A soft computing approach for controlling the quality of cut with abrasive waterjet cutting system experiencing orifice and focuing tube wear, Journal of Materials Processing Technology, vol. 185, nº.1-3, pp.217-227, abr.2007
[6]. T.Liu, Omax Corporation USA, Evaluation of nozzle health states for AWJ machining, 19th International Conference on Water Jetting.
[7]. M. Hashish, D.O. Monserud, y P.D. Bondurat, A new abrasive wáter jet nozzle for automated and intelligent machining, in 7th American Water Jet Conference, Seattle, Washington, 1993.
[8]. B. Jurisevic, D.Brissaud y M. Junkar, Monitoring of abrasive water jet (AWJ) cutting using sound detection, AMT, vol.24, nº9-10, pp.733-737, may 2004
[9]. D.A.Axinte y M.C.Kong, An integrated monitoring method to supervise waterjet machining, CIRP Annals – Manufacturing Technology, vol.58, nº.1, pp.303-306,2009.
[10]. A.Lebar, B. Jurisevic y M. Junkar, Monitoring of the AWJ cutting in the submerged conditions, in 2003 WJTA American Waterjet Conference, August 17-19, 2003, Houston, Texas.