Un avance técnico permite fabricar un soporte de batería para vehículos híbridos
"Se precisa un acero de muy alta resistencia para sujetar unas baterías tan pesadas, y para actuar al mismo tiempo como protección en caso de choque," indica Kevin Bilkey, ingeniero de Trim Trends, al describir el soporte de batería. "En un impacto posterior, la energía se transmite del parachoques al soporte de batería; éste último se desplazará hacia delante y hacia arriba, pero sin penetrar en el habitáculo."
En las primeras etapas del proyecto, los diseñadores realizaron pruebas con un grado de acero convencional, pero el diseño no ofrecía suficiente resistencia y presentaba un peso excesivo.
"Decidimos entonces utilizar uno de los aceros de mayor resistencia disponibles en el mercado: un acero martensítico con una resistencia a la tracción mínima de 1200 N/mm2," prosigue Kevin Bilkey. "El problema que encontramos era que, hasta la fecha, nadie había utilizado este material para la conformación en prensa de componentes avanzados de dimensiones tan grandes. No sabíamos si sería posible producirlos."
El problema residía en encontrar un método de producción adecuado y económico que permitiese minimizar o eliminar el riesgo de agrietamiento.
"Se trata de un componente de gran tamaño, y sabíamos que existía un elevado riesgo de agrietamiento," explica Kevin Bilkey. "Finalmente, la solución consistió en permitir que la pieza de 7 kilogramos se mueva libremente en la matriz, para conformarla sin restricción en la prensa."
"Se precisa un acero de muy alta resistencia para sujetar unas baterías tan pesadas, y para actuar al mismo tiempo como protección en caso de choque," indica Kevin Bilkey, ingeniero de Trim Trends, al describir el soporte de batería. "En un impacto posterior, la energía se transmite del parachoques al soporte de batería; éste último se desplazará hacia delante y hacia arriba, pero sin penetrar en el habitáculo."
En las primeras etapas del proyecto, los diseñadores realizaron pruebas con un grado de acero convencional, pero el diseño no ofrecía suficiente resistencia y presentaba un peso excesivo.
"Decidimos entonces utilizar uno de los aceros de mayor resistencia disponibles en el mercado: un acero martensítico con una resistencia a la tracción mínima de 1200 N/mm2," prosigue Kevin Bilkey. "El problema que encontramos era que, hasta la fecha, nadie había utilizado este material para la conformación en prensa de componentes avanzados de dimensiones tan grandes. No sabíamos si sería posible producirlos."
El problema residía en encontrar un método de producción adecuado y económico que permitiese minimizar o eliminar el riesgo de agrietamiento.
"Se trata de un componente de gran tamaño, y sabíamos que existía un elevado riesgo de agrietamiento," explica Kevin Bilkey. "Finalmente, la solución consistió en permitir que la pieza de 7 kilogramos se mueva libremente en la matriz, para conformarla sin restricción en la prensa."
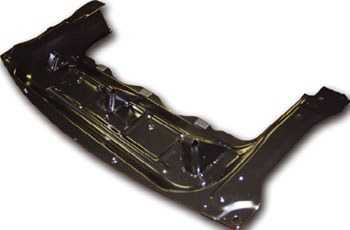
"Aunque llevamos muchos años suministrando componentes complejos a los grandes fabricantes de automóviles de Detroit, éste resultó el trabajo más difícil," afirma David A Crowe, especialista en la fabricación de herramientas en Trim Trends. "Tuvimos que olvidarnos de las teorías anteriores y de los conceptos preconcebidos, y comenzar de cero. Podemos realizar la soldadura, si nos aseguramos de que exista una adecuada disipación del calor durante el soldeo de la chapa. Tras resolver el problema, sólo nos quedaba un mes de plazo para comenzar con el suministro regular."
La fabricación de un soporte de batería es un proceso realizado en seis etapas – desde el troquelado de los agujeros y rebordeo del exceso de material hasta la soldadura de las cuñas para los carriles de deslizamiento. La conformación en prensa, mediante la cual se obtiene la forma del soporte de batería, se lleva a cabo en una sola operación. El material recortado se emplea para las cuñas. Por lo tanto, se consigue una utilización muy eficiente del material.
La producción ha alcanzado ahora su cadencia máxima. Las chapas para soportes de batería acabados se conforman a razón de 150 unidades diarias, que se envían a Sanyo, donde se instalan las baterías sobre los soportes. Así, Ford recibe unidades completas para su montaje en el vehículo.
Los pedidos de soportes de baterías efectuados por Ford ascienden a 30.000 unidades. Sin embargo, los automovilistas demuestran un gran interés por el nuevo vehículo, y las cifras de pedidos provisionales de vehículos indican que el número de soportes de batería que se necesitarán en el futuro aumentará sustancialmente.
"Prevemos suministrar soportes de baterías a Sanyo durante mucho tiempo, y estamos convencidos de que el Ford Escape Hybrid SUV será un éxito," concluye Kevin Bilkey. "Para dar respuesta a las demandas cada vez exigentes de la industria del automóvil, los proveedores deben ser innovadores y encontrar buenas soluciones a los problemas complicados."