Fresado y taladrado de materiales duros
Para las operaciones de fresado y taladrado, los fabricantes del sector aeronáutico utilizan a menudo herramientas de metal duro o de acero rápido. Además, en las operaciones de mecanizado, los fabricantes deben alcanzar los máximos niveles de calidad posibles. Por lo general esta calidad se logra gracias al seguimiento y máximo control de la seguridad en los procesos. El coste por pieza suele representar algún que otro problema pero en la mayoría de los casos producir piezas perfectas es una prioridad mucho mayor y el aumento de la productividad tiende a ser secundario.
Los fabricantes del sector aeronáutico se esfuerzan por lograr seguridad y consistencia en el proceso mediante un rendimiento predecible de sus máquinas y herramientas. En el caso de las herramientas, los fabricantes deben disponer de fresas y brocas que ofrezcan siempre la misma duración de vida útil de las herramientas. Incluso sabiendo con exactitud cuánto tiempo durará una herramienta, en este sector, los fabricantes a menudo programan la sustitución de las herramientas de sus máquinas mucho antes de que se deterioren por completo.
Gracias a las tecnologías de las máquinas y herramientas de corte, los materiales como el titanio, Inconel o composites han pasado de ser casi imposibles de mecanizar a llegar a un punto en que los fabricantes del sector aeronáutico los mecanizan con precisión y eficacia, dando lugar a tecnologías de herramientas que ofrecen un mejor control de los procesos y una gran consistencia especializada en brocas y fresas de metal duro. Estas herramientas se han desarrollado específicamente para superar los retos de mecanizado presentados por estos materiales. A través de la incorporación de diversas geometrías y recubrimientos innovadores utilizados junto con avanzadas técnicas y estrategias de mecanizado, estas herramientas específicas no sólo ofrecerán seguridad en el proceso, sino que también aumentarán la producción y su rendimiento.
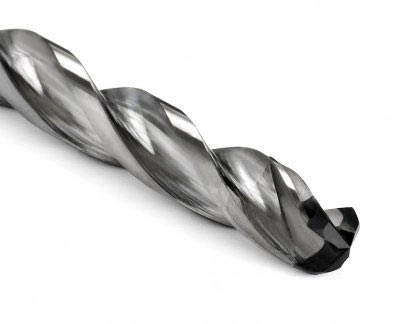
Fresado
Composites. El mercado de mecanizado de fibra de carbono reforzada con plásticos (CFRP) está aumentando en el sector aeronáutico. Sin embargo, los materiales son difíciles de mecanizar porque son muy abrasivos y duros para las herramientas de fresado. Además, se debe evitar el delaminado que se produce cuando se separan las hebras de la fibra de carbono durante el mecanizado. Estos problemas se pueden superar con el uso de fresas de metal duro con filos vivos y robustos, y con unos recubrimientos específicos.
Normalmente se utilizan dos tipos de procesos de recubrimiento, denominados PVD (deposición física de vapor) y CVD (deposición química de vapor), en combinación con un avanzado material de corte de PCD (diamante policristalino). Los recubrimientos PVD implican un proceso físico que incluye recubrimientos de nitruro de aluminio, nitruro de cromo y nitruro de titanio para dar lugar a una dureza de aproximadamente de 3.000 Vickers. Los recubrimientos de diamante que se realizan por el proceso químico CVD son aproximadamente tres veces más duros, lo que genera una dureza de unos 10.000 Vickers. El PCD viene soldado sobre el metal duro.
Desde el punto de vista de la geometría, las fresas más eficaces para los composites incorporan ángulos bajos de hélice para reducir las fuerzas axiales en las capas laminadas del material y evitar así la delaminación. Además, las fresas con hélice a derechas e izquierdas tienen también geometrías eficaces para los composites. Estos tipos de fresas, conocidas normalmente como de compresión, dirigen y comprimen las fuerzas de corte hacia los centros de espesor de la pieza y, en el caso del contorneado, mantienen las capas laminadas intactas. Además, estos tipos de geometrías mecanizan de forma mucho más suave estos materiales.
Existiendo fresas de compresión básicas, algunas empresas de herramientas de corte, como Seco, han desarrollado este tipo de diseño con nuevas y diferentes geometrías, como las de doble hélice. Seco, por ejemplo, diseño dos tipos de doble hélice. Uno de ellos es una herramienta de varios filos con corte muy suave. El otro tiene menos dientes, lo que proporciona más ángulo de incidencia en los filos de corte. Este último se utiliza más para operaciones de desbaste, mientras que la primera opción de varios dientes ofrece un rendimiento ideal para las operaciones de acabado.
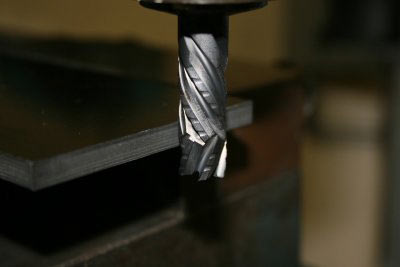
En cuanto a técnicas de mecanizado se refiere, los parámetros de corte para los composites dependen a menudo de los materiales que los componen. Las velocidades básicas de las fresas de metal duro para composites son aproximadamente de 150 m/min, y los avances son aproximadamente de 0,07 mm. Pero cabe señalar que esta variedad de materiales existen diferentes matrices, cada uno con sus propios requisitos de velocidad y avance. Los puntos de fusión de estos materiales de unión son a menudo los que determinan los datos de corte de los composites. Además, el contenido en fibras y su orientación también influyen de forma significativa en el proceso de mecanizado y en el control de las velocidades de corte y avances, así como en la trayectoria óptima de la herramienta.
Aleaciones de titanio. En el sector aeronáutico, las aleaciones de titanio se utilizan a menudo en tres áreas de aplicación: componentes estructurales de los aviones, piezas de la sección de refrigeración de los motores y sistemas del tren de aterrizaje. Se suele utilizar el titanio 5553, que es una aleación casi beta que se usa normalmente para las piezas del tren de aterrizaje. El TiAl6-4 es una aleación alfa-beta y uno de los tipos de titanio más utilizados, especialmente para componentes estructurales.
Los factores que hacen que las aleaciones de titanio sean un desafío para el mecanizado y que contribuyan a su baja potencia de maquinabilidad son su conductividad térmica, alta adherencia y tensión, y su alta tensión en temple. Las aleaciones de titanio tienen una baja conductividad térmica, lo que significa que en el proceso de mecanizado, el calor generado por el proceso se transfiere a la fresa en lugar de alejarse de la zona de corte con las virutas.
La alta adherencia del titanio comporta que las virutas tienden a pegarse a los filos, así que se generan virutas muy largas, más incómodas que las más cortas que se pueden extraer fácilmente. La tensión en temple por deformación del material que entra en juego durante el proceso de mecanizado provoca que una pequeña capa fina de material se temple debido a los efectos de presión generados durante el proceso de mecanizado.
A pesar de que el titanio se puede mecanizar con fresas de metal duro de uso general para diversos materiales, las fresas diseñadas específicamente para las características de maquinabilidad del titanio casi siempre proporcionarán resultados superiores. Estas fresas específicas proporcionan unos niveles de rendimiento elevados pero pueden resultar menos versátiles en lo que se refiere a los diferentes materiales con los que se pueden utilizar.
Por ejemplo, Seco dispone de una fresa de acero rápido (HSS) en programa diseñada tanto para titanio como para acero inoxidable. Las fresas que forman parte de la serie HPM (mecanizado de alto rendimiento) de Jabro están diseñadas específicamente para determinadas designaciones de material como el titanio. Estas fresas incorporan geometrías específicas y cualidades de diseño que se han optimizado para el titanio.
Estas geometrías y cualidades de diseño incluyen hélices de entre 40 y 50 grados, y conductos de refrigeración internos para evitar que las virutas se peguen a los dientes de la fresa, para evacuarlas rápidamente y enfriar la zona de corte. También cuentan con paso diferencial para eliminar las vibraciones con gran profundidad de corte, y una combinación de metal duro con recubrimiento de nitruro de cromo y de aluminio. No se utiliza nitruro de titanio para evitar la reacción química entre la fresa y el material.
Hay ciertos factores que determinan cuándo se debe usar una herramienta de metal duro o una herramienta de acero rápido. El factor principal es el diámetro de corte. Las herramientas de metal duro deben utilizarse cuando las aplicaciones requieren fresas de menor diámetro y cuando las geometrías de la pieza son extremadamente complejas, o si se busca una gran profundidad de corte (ap).
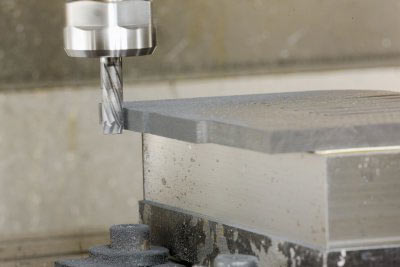
Se recomiendan las fresas de acero rápido para piezas menos complejas en aplicaciones de gran volumen y cuando se busca obtener grandes anchos de corte (ae) como grandes ap. También hay que usarlas cuando se utilizan máquinas antiguas y convencionales con par y potencia elevados.
Inconel. Como es habitual en el sector aeronáutico, las piezas de Inconel tienden a ser muy caras, no sólo en el coste del material, sino también en la inversión de tiempo para producirlas antes incluso de la etapa de mecanizado. Se producen unas enormes pérdidas cuando las piezas se dañan después de horas o incluso días de mecanizado.
Hay ciertas similitudes entre el Inconel y el titanio. Pero en términos de mecanizado, el Inconel (una superaleación con base de níquel) es el material más difícil de mecanizar. Tiene muy baja conductividad térmica y unos niveles muy elevados de temple por deformación, incluso más altos que los del titanio. El Inconel también tiene una alta adherencia, de manera que las velocidades de corte rara vez pueden superar los 25 o 30 m/min con el método de mecanizado convencional.
Las geometrías de la herramienta para el mecanizado en Inconel difieren considerablemente de las que se utilizan para el titanio. Las geometrías para el Inconel tienen desahogos muy pronunciados. Esa geometría reduce, en la medida de lo posible, el contacto entre la fresa y el material. Esto es muy importante porque el Inconel es flexible y dispone de una gran capacidad de memoria, lo que significa que ‘cederá’ algo cuando se someta a las fuerzas de una herramienta de corte. Por lo tanto, cuanto más tiempo de contacto haya entre la herramienta y el material, más alto será el desgaste abrasivo de la herramienta y menor su vida útil. Para reducir aún más la fricción entre la fresa y el Inconel, Seco incorpora una capa de nitruro de titanio y aluminio pulido con un acabado superficial extremadamente suave.
Cuatro estrategias de mecanizado para titanio e Inconel
Básicamente, existen cuatro técnicas de mecanizado o estrategias, para titanio e Inconel. La primera es el mecanizado tradicional, que implica un equilibrio entre el ae y el ap de 1 a 1. Esto significa que el mecanizado se realiza con todo el ancho de la fresa (1xDc) y una profundidad de corte de hasta 1 vez el diámetro de corte, con un avance medio.
La segunda estrategia es el HPM (mecanizado de alto rendimiento), el cual incluye fresas diseñadas específicamente para titanio e Inconel, como la gama de fresas HPM de Seco. Estas fresas funcionan con un gran ap (hasta de 1,5xDc) y con un ancho de corte (ae) total. Se eliminan grandes volúmenes de viruta en un corto intervalo de tiempo para aumentar la productividad.
La tercera estrategia es el HFM (mecanizado de altos avances) que utiliza un ap muy pequeño y un ae total, con lo que el ancho de corte es 1xDc. Las geometrías específicas de las fresas que se usan para esta estrategia dirigen las fuerzas de corte al husillo de la máquina, por lo que resulta especialmente útil en condiciones de mecanizado inestables debidas a los grandes voladizos de la herramienta y a aplicaciones complejas, como cajeras con profundidades de 5xDc o más.
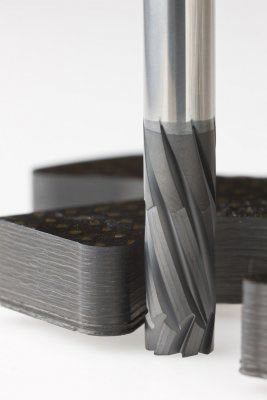
La cuarta estrategia de mecanizado es el HSM (mecanizado de alta velocidad) que utiliza uno ae bastante bajo y profundidades de corte ap muy grandes. Debido a que la profundidad de corte es relativamente baja, hay un pequeño arco en contacto que contribuye a reducir el calor en las zonas de corte debido al menor tiempo de contacto y, por lo tanto, permite obtener una mayor velocidad de corte para compensar y aumentar la productividad.
Los avances tanto de las herramientas de mecanizado como las máquinas han hecho posible estas estrategias. Por ejemplo, las geometrías de fresa HPM de Seco tienen características especiales, tales como el paso diferencial y hélices con ángulo variable, que proporcionan la estabilidad necesaria para el mecanizado de alto rendimiento. En el caso de los mecanizados de alta velocidad y alto avance, estas estrategias tienden a depender más de la herramienta de mecanizado, así como de las geometrías de la fresa.
En la mayoría de los casos, las herramientas de mecanizado y las máquinas trabajan al unísono para satisfacer las exigencias de mecanizado de los materiales específicos de los fabricantes del sector aeronáutico. Se necesitan tanto las herramientas de mecanizado como las fresas adecuadas. Esto es especialmente cierto en el caso del mecanizado con una gran capacidad de altos avances, pero también con controles CNC que puedan manejar programas más amplios y archivos NC relacionados con las operaciones de fresado de alta velocidad y altos avances.
Taladrado
Composites. Para las aplicaciones aeronáuticas, los agujeros taladrados en composites deben estar perfectamente limpios y sin fibras rasgadas o deshilachadas que puedan interferir o comprometer las operaciones de montaje posteriores.
Dos problemas comunes del taladrado de los composites son la delaminación y la presencia de fibras sin cortar, especialmente en la parte posterior o en la parte de salida de la broca en las piezas. Al taladrar, las fuerzas de la herramienta empujan hacia abajo al material y, a medida que el taladro se aproxima a la parte de salida, una fuerza excesiva puede provocar que la broca tan solo pase por la última parte del agujero, en vez de cortarla. El resultado son fibras de composite que están rasgadas en lugar de cortadas limpiamente, y que finalmente causan la delaminación.
Para superar estos retos, las empresas de herramientas se esfuerzan por disminuir las fuerzas de avance de la broca respecto al material a través del uso de diferentes ángulos de punta y ángulos de hélice en las brocas. Hay que tener en cuenta que algunas de las geometrías generan menores fuerzas de avance y funcionan mejor que otras.
Por ejemplo, un ángulo de punta de 140 grados, el más común para las brocas de metal duro, funciona bastante bien para varios agujeros al taladrar composites. Desafortunadamente, tan pronto como la herramienta se desgasta, pierde su efectividad. Con una broca de metal duro con recubrimiento de diamante C1 para composites, Seco emplea una geometría con dos ángulos de punta: uno de 130 grados en el centro y otro de 60 en el exterior de la punta de la broca. En la operación, el punto central de la broca sale primero de la parte final del agujero cortando el material que pudiera sobresalir de éste. Por lo tanto, cuando la parte de 60 grados sale, las fuerzas de avance de la broca a través del material se reducen drásticamente. Por lo tanto, hay una menor delaminación y también menos fibras sin cortar, si es que las hay.
Además de las brocas recubiertas de diamante con dos dientes, Seco ha desarrollado una única geometría de broca con punta de PCD y 3 dientes para composites. En las mismas condiciones de corte que las brocas para composites estándar, esta nueva geometría de broca de PCD proporciona unos resultados mucho mejores porque hay tres filos en vez de sólo dos. Las brocas tienen filos más vivos y generan menos fuerzas en el avance por revolución, especialmente al salir de un agujero. Además, la broca con punta de PCD completa, en contraposición a la recubierta de diamante, puede tener, en muchos casos, hasta cuatro veces más de vida útil.
Titanio. En el sector aeronáutico, la mayoría de los diámetros de los agujeros son pequeños. Para los diámetros inferiores a 1 mm y hasta 20 mm, las brocas de metal duro se utilizan ampliamente en el taladrado de titanio así como de Inconel.
Como ocurre con el fresado del titanio, el calor en el taladrado tiende a ir a la herramienta en lugar de ser arrastrado con las virutas. Para combatir esta situación, por lo general, se utilizan geometrías de brocas con filos de corte muy vivos. Normalmente, las brocas para titanio no están recubiertas debido a esta exigencia del filo. Además, los recubrimientos pueden aumentar un poco la fricción, al añadir generación de calor. Una parte importante es la contracción del material después del mecanizado. Por eso es necesaria una mayor conicidad trasera en la broca.
Inconel. Como el Inconel es muy abrasivo y se endurece al trabajarlo, las geometrías de brocas eficaces para taladrar ente material son básicamente las mismas que las del titanio. Sin embargo, se añaden recubrimientos para aumentar la resistencia al desgaste y reducir la fricción. Seco, por ejemplo, utiliza recubrimientos de nitruro de aluminio y titanio para proteger las brocas para Inconel y prolongar su vida útil.
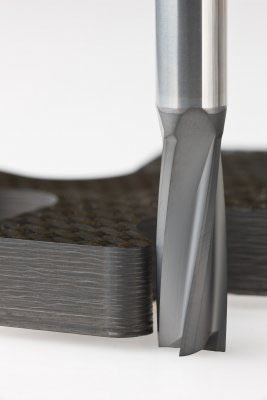
Al taladrar el Inconel, se utilizan velocidades y avances inferiores, sobre todo porque el material es más duro y difícil de cortar. La maquinabilidad del material entra en juego durante el taladrado, igual que lo hace durante el fresado. En aplicaciones aeronáuticas, las profundidades de los agujeros de los componentes de Inconel, por lo general, son sólo de 3xD.
Los recubrimientos han desempeñado un papel clave en el aumento de la productividad y seguridad en el proceso del taladrado en el sector aeronáutico, y las empresas de herramientas como Seco siguen intentando conseguir un mejor control y dominar los tratamientos en el filo de corte. A través de efectivas variaciones de los recubrimientos, como el nitruro de aluminio y titanio, y el control de los filos de corte, Seco ha sido capaz de desarrollar brocas que permiten obtener el doble de velocidad de corte y avances en el taladrado.
En el futuro, habrá más cambios en las geometrías existentes para mejorar aún más el rendimiento de la broca. Muchos de estos pequeños cambios sólo se podrán realizar gracias a las avanzadas tecnologías de las herramientas de mecanizado de hoy en día. Diferentes fabricantes del sector aeronáutico que ya han realizado millones de agujeros ya han puesto sus miras en estas brocas específicas.
Conclusión
Para mecanizar de manera efectiva los difíciles materiales del sector aeronáutico actual, la clave está en lograr una solución de mecanizado completa, no sólo un producto. Una solución de herramienta de corte completa incluye no sólo la geometría y el diseño necesarios, sino también soporte de ingeniería para las aplicaciones. El conocimiento y la experiencia del recurso humano combinado con el producto avanzado para formar una solución completa y conseguir mejores resultados.
La calidad de la pieza y la seguridad en el proceso requieren tener a mano la herramienta con el mejor diseño posible para la aplicación específica, ya se trate de composites, titanio o Inconel. Pero esas herramientas deben adquirirse de un proveedor capaz y dispuesto a proporcionar orientación en cuanto a la forma correcta de hacerla funcionar para obtener un rendimiento óptimo. La educación y la formación son la clave para sacar el mayor provecho de las avanzadas herramientas diseñadas hoy en día para los duros materiales aeronáuticos.