Sandvik Coromant e Intermaher muestran cómo convertir las operaciones de taladrado en un éxito
La presentación del evento 'See the Whole Picture' la realizó Roberto Hernando, director general de Intermaher – Mazak, quien hizo una breve descripción de las máquinas Mazak y de los servicios que Intermaher proporciona como distribuidor de Mazak en España. En Europa la firma nipona cuenta con unas 50.000 máquinas instaladas.
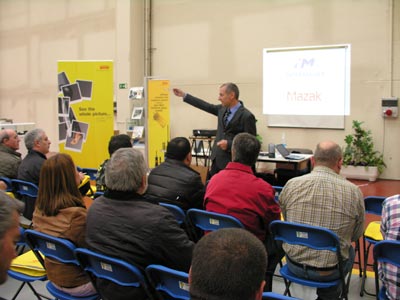
A lo largo de las jornadas se presentó un centro de mecanizado de 5 ejes Variaxis i-600, una máquina de pórtico con base muy rígida y mesa de doble apoyo de cuna para una mayor rigidez, que trabajó con las herramientas Sandvik Coromant y dio lugar a numerosas conversaciones técnicas entre público y especialistas de Sandvik Coromant y de Intermaher. La máquina destaca también por ser muy rápida y precisa por su construcción, cabezal y husillos refrigerados y servos de alta resolución. Es un modelo instalado en muchas empresas que trabajan para el sector aeronáutico.
Se presentó una ISO 40, una de las más pequeñas con volteos hasta un metro aproximadamente. Incorpora guías de rodillos cruzados en todos los ejes y el control Mazatrol Matric de última generación, un control muy rápido para que la maquina pueda dar muy buenos acabados de pieza. La máquina está diseñada para reducir las vibraciones en la punta de la herramienta y compensa los cambios en la temperatura ambiente. Puede simular los mecanizados con control de colisiones que, entre otros, dota a la máquina de inteligencia.
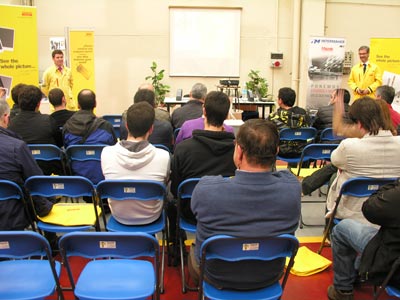
La parte correspondiente a Sandvik fue presentada por especialistas líderes del mercado en taladrado y roscado con macho y proporcionó las claves que impulsan la rentabilidad en el proceso de taladrado, Hubo de todo: consejos, trucos y técnicas resolutivas de problemas, que pueden impactar positivamente en el negocio de cualquiera que se dedique al mecanizado de piezas.
Según pudo escuchar el público asistente, la pobre calidad de agujero, demasiado desgaste, y en definitiva, el alto coste por componente son situaciones habituales entre los mecanizadores.
Alberto Pérez, responsable de Machine Investment de Coromant, realizó una breve descripción de la empresa “la primera del sector de la fabricación de herramientas, que cuenta con 8.000 personas y unos 2.500 productos nuevos al año. Con una gran apuesta por el I+D. Actualmente contamos con más de 2.000 patentes activas”. Su intervención y todos los temas tratados lo dejaron claro: su objetivo es mejorar la productividad, y precisamente en ese marco se celebró el evento.
Hechas las descripciones más generales se pasó directamente al taladrado.
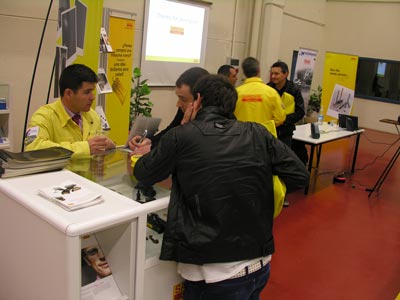
Tomás Borrell, Round Tools Specialist, comenzó hablando del proceso de taladrado, un proceso que a priori parece sencillo pero que no lo es. El taladrado, en comparación con el torneado y el fresado tiene la dificultad de que no vemos el trabajo que se está realizando. La vibración de la máquina o la viruta pueden ser indicadores a tener en cuenta pero no son suficientes. Es importante tener una imagen global del proceso, de los parámetros que influyen en el taladrado para hacer de todo ello un proceso rentable. Es decir, son factores clave el diámetro, la tolerancia, la versatilidad y el coste por agujero.
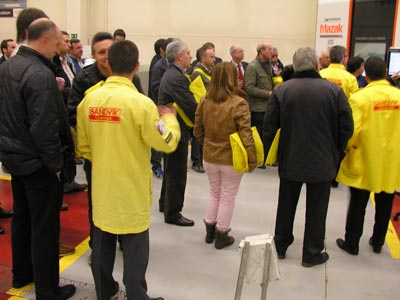
Hay muchos tipos de agujeros, unos con más y otras con menos dificultad. Cada uno de ellos requiere un método ideal de taladrado. Lo importante es tener en cuenta la relación entre el diámetro y la profundidad del taladrado.
Andrés García, Drilling Driver, a través de ejemplos prácticos, mostró diferentes tipos de agujeros, de diferentes métricas y pasos, que pueden ser taladrados con metal duro integral, punta intercambiable y placa intercambiable, cada una de ellas pensadas para situaciones de taladrado diferentes. Una placa intercambiable, explicó, tiene la ventaja de que cambiando la placa se pueden taladrar todo tipo de materiales. La ventaja de la punta intercambiable, por su parte, es que tiene una gran y que su cuerpo de acero da más seguridad en el taladrado. Y las brocas metal duro integral pueden trabajar con materiales muy complejos. Permiten tener geometrías en la punta de la broca adecuadas para diversos materiales: geometrías de punta invertida, de ‘corner radius’, geometrías específicas para aceros y para composites. Una buena elección de la geometría y de la calidad adecuada de broca influye directamente en la productividad del taladrado.
Asimismo, un condicionante a la hora de elegir la broca es el número de agujeros que se van a hacer y si el proceso que vamos a afrontar requiere versatilidad.
En un formato ameno para los asistentes, Andrés García y Tomás Borrell continuaron repasando las variables que hacen que un proceso de taladrado sea rentable.
Así por ejemplo, se detuvieron en la importancia del acoplamiento, que tiene que tener la calidad suficiente para obtener todo el rendimiento que la herramienta proporciona. Andrés García recomendó que la excentricidad se sitúe en torno a las dos centésimas. Las brocas de metal duro integral pueden utilizar acoplamientos térmicos e hidráulicos, al igual que los de punta intercambiable, que también pueden recurrir a CoroGrip o pinzas de gran apriete mientras que las de placa intercambiable pueden utilizar portas más convencionales.
También es importante elegir siempre la broca más corta, así como comprobar la formación de viruta y ajustar el avance en función de la viruta. Esto último es una buena pista de cómo se está realizando el taladrado. Pero ¿cuál es la viruta más adecuada? Una viruta corta y uniforme que se cierra sobre sí misma, es más fácil de evacuar, y es la que se recomendó. Aunque esto también depende de los materiales.
Otro momento interesante de la jornada fue el dedicado a la refrigeración. La refrigeración interior de alta presión ayuda a evacuar la viruta del interior, algo muy importante en taladrado profundo. La refrigeración exterior es útil cuando el taladrado es corto. En el caso de MQL, cada vez más utilizado en taladrado,
Se mostró la relevancia de la presión de la bomba, el caudal que tiene que suministrar la bomba para que la presión del líquido sea la adecuada y la calidad no se vea afectada.
Otros factores importantes
Tal y como explicaron los especialistas de Sandvik Coromant, cada vez más se demanda el taladrado en Plunge en sustitución del proceso de interpolación. Para ello la herramienta debe poder desbastar, soportar la fuerza axial y garantizar un proceso fiable. Con la herramienta adecuada se puede también taladrar en Plunge en superficies irregulares.
El proceso de trepanado, también citado, puede conducir a un taladrado más productivo. Se trata de procesos que pueden ser más productivos que los procesos convencionales.
En taladrado profundo se requiere una preparación y una programación específicas, siempre teniendo en cuenta el coste por agujero. La fijación de la pieza es crítica para evitar la rotura de la herramienta. También el acoplamiento debe ser absolutamente preciso y la refrigeración interna debe superar los 20 bares. Es obligatorio además un primer paso en el que una broca piloto hace de guía para que en el segundo paso la broca, situada en el agujero piloto, taladre sin problemas y centre de forma correcta.
En la explicación de las variables en un proceso de taladrado se hizo asimismo un repaso especial por los composites, un material cada vez más extendido que empezó en aeronáutica y siguió en renovables, automoción, yates y barcos o coches y motocicletas de competición. Una problemática al taladrar composites es la delaminación. La calidad del filo y la broca adecuada son indispensables para evitarlo. La geometría y el recubrimiento son los aspectos determinantes, así como realizar el taladrado por medio de picotes para extraer la viruta.
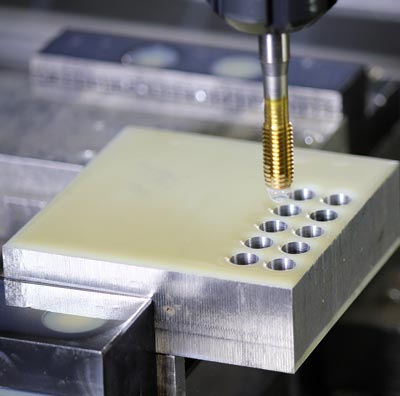
Otro de los temas destacados fue el roscado: en este tipo de trabajos es importante seleccionar el tamaño adecuado de broca, la tolerancia, el proceso que se va a utilizar para realizar la rosca y, por supuesto, el coste por agujero. En cuanto al proceso, hay diversos métodos. Puede girar la herramienta o la pieza, o puede realizarse el roscado con macho. Pero ¿cuál es el más adecuado? El roscado con macho es un proceso muy productivo pero menos versátil que el de roscado fresado/torneado. Requiere una programación sencilla y la laminación es posible. El roscado fresado requiere un control del paso y diámetro y permite trabajar con un alto valor de la materia prima, por lo que es más indicado que el anterior. La longitud de la rosca, el tipo de tolerancia y el porcentaje de altura del hilo de la rosca son fundamentales para elegir a broca adecuada.
En este apartado los especialistas de Sandvik hicieron una recomendación: según aumenta la dureza del material la dimensión del agujero previo toma una influencia decisiva. Además, el portamachos que se elija es de vital importancia en la calidad del roscado. Su diseño condiciona la vida del macho, la calidad de la rosca, la profundidad de la rosca y la vida de los rodamientos del cabezal de la máquina.
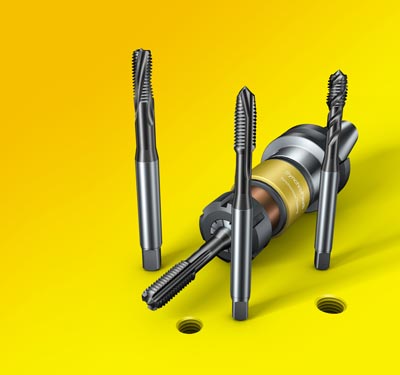