AutoForm ofrece una solución de software para fabricantes de matrices progresivas
AutoForm Engineering GmbH, especialista en soluciones de software para procesos de estampado y ensamblaje BiW, presenta su nuevo software AutoForm ProgDie, desarrollado específicamente para las necesidades de los usuarios que trabajan en el campo de las matrices progresivas. Con AutoForm ProgDie los fabricantes de matrices progresivas podrán diseñar, simular, validar y modificar eficientemente varios conceptos de diseño de banda y seleccionar el que mejor se adapte a sus necesidades.
La estampación con matrices progresivas es un proceso versátil y rentable para la producción de una amplia gama de piezas para diversas industrias. Aunque la estampación con matrices progresivas se basa en los principios de la estampación de chapa metálica, el diseño, la simulación y la validación de su proceso difieren significativamente de los de la estampación con matrices transfer y en línea. En consecuencia, este proceso de estampación tiene sus requisitos específicos de ingeniería y simulación. El flujo de trabajo de AutoForm ProgDie está diseñado para satisfacer las necesidades de los diseñadores e ingenieros de matrices progresivas. El software permite eldesarrollo rápido del diseño de la banda, el diseño de las herramientas y la validación del diseño de la banda.
AutoForm ProgDie permite a los usuarios calcular fácilmente el diseño de la chapa y después evaluar y comparar rápidamente las diferentes opciones de anidado. Con este software, pueden identificar eficientemente el diseño óptimo de la chapa, teniendo en cuenta la máxima utilización de material. El software también les permite crear un plan de banda con una interfaz de diseño 3D intuitiva de arrastrar y soltar que simplifica significativamente el proceso de diseño.
Los fabricantes y proveedores de automoción se esfuerzan por reducir los plazos de entrega y los costes de las herramientas, por lo que se centran en reducir el tiempo de desarrollo de estas, que es una de las fases que más tiempo consume de todo el proceso de desarrollo del producto. AutoForm ProgDie permite a los usuarios crear rápidamente un diseño de herramienta partiendo únicamente de la geometría CAD de la pieza, evaluar diseños de herramienta alternativos y seleccionar el mejor para el proceso de fabricación.
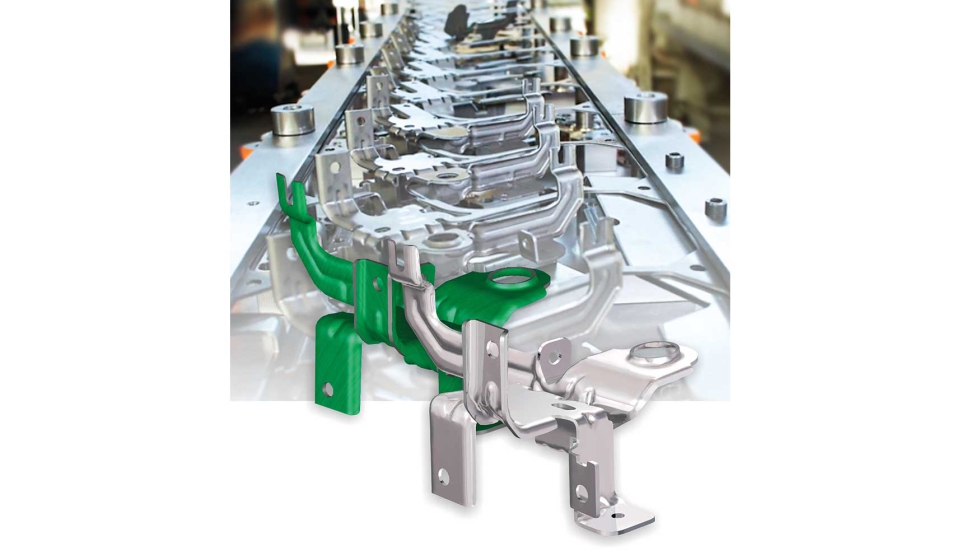
La validación del diseño de la banda es esencial para cualquier fabricante de matrices progresivas ya que evita costosos ajustes por prueba y error, así como el costoso diseño y creación de prototipos. AutoForm ProgDie permite a los ingenieros de matrices progresivas conseguir una simulación rápida y precisa de las matrices progresivas, incluyendo todas las operaciones de conformado y corte. La simulación de matrices progresivas se basa en el enfoque incremental integrado en AutoForm ProgDie. Con AutoForm ProgDie, los usuarios pueden obtener una visión profunda del proceso de estampado de la matriz progresiva y pueden identificar rápidamente las áreas problemáticas como arrugas, roturas, excesivo adelgazamiento o springback, que podrían ocurrir durante el proceso. El software permite a los usuarios diseñar las mejores soluciones alternativas posibles para corregir los problemas identificados.
Además, AutoForm ProgDie permite a los usuarios abordar los posibles problemas de robustez de la estampación de la matriz progresiva. Pueden alcanzar sus objetivos de capacidad de proceso deseados mediante el proceso de fabricación más eficiente y robusto posible. Con AutoForm ProgDie, los fabricantes de matrices progresivas pueden validar un proceso de forma rápida y precisa antes de que comience el proceso real de fabricación.
Markus Thomma, CMO del Grupo AutoForm, explica: “El lanzamiento al mercado de AutoForm ProgDie es un hito importante para AutoForm. Adaptado a las necesidades específicas de los usuarios que trabajan con matrices progresivas, el software les permite profundizar en el proceso de estampado de la matriz progresiva. El software les permite diseñar, simular y validar el proceso de forma fácil y precisa, minimizar los rechazos de pieza y maximizar la eficiencia de la producción”.