para un brazo medidor por coordenadas
Desarrollando un brazo de medida
Dpto. Ingeniería de Diseño y Fabricación. Centro Politécnico Superior.
Universidad de Zaragoza
01/09/2003
Introducción
Las ventajas principales de dicho brazo frente a otros sistemas son su facilidad de manejo, su gran flexibilidad de movimientos, su carácter portátil y su menor tamaño, lo que permite realizar mediciones rápidas sin apenas interferir en otros procesos que se estén llevando a cabo. Este sistema también permite la medición de piezas in situ sin necesidad de tener que trasladarlas al lugar donde se encuentre el instrumento de medición, como sí que ocurre, por ejemplo, con las máquinas de medición por coordenadas (MMC)
El brazo de medida puede poseer múltiples aplicaciones en sectores muy diversos y puede servir de base, mediante pequeñas modificaciones, a dispositivos similares de aplicación más específica. Así, mediante el diseño, la fabricación y el ensayo de una articulación, se pretende conocer la manera de modelar geométricamente este tipo de sistemas, así como determinar sus posibles mecanismos de error. Todo ello orientado a un posible desarrollo futuro de brazos de medida tanto de propósito general como para aplicaciones concretas.
Una parte fundamental del proceso es la implementación del modelo geométrico necesario para transformar las lecturas obtenidas por los sensores en las coordenadas cartesianas del punto medido. Para ello se ha utilizado el método de representación de Denavit-Hartenberg [1] que permite sistematizar el cálculo de las matrices de transformación necesarias.
Por otro lado, se ha desarrollado un procedimiento de optimización de parámetros geométricos orientado a la corrección de los posibles errores de fabricación, de montaje o debidos a otras magnitudes de influencia.
Diseño
Se decide que los grados de libertad permitirán un giro con respecto a un eje vertical y otro con respecto a un eje horizontal que se producirán mediante la actuación de rodamientos angulares. Se diseña un sistema de limitación del giro a 720º para no permitir a cada uno de los ejes girar más de dos vueltas completas. Los sensores utilizados para la medición de los giros son encoders angulares de gran número de pasos para obtener una buena resolución en el sistema. El paso de los cables a lo largo de toda la estructura también se tiene en cuenta en el diseño, sobre todo de las carcasas.
El aspecto externo de la articulación se puede observar en la figura 1. En ella se muestran los cuerpos vertical y horizontal con sus respectivas zonas de alojamiento de los encoders. En el diseño de la articulación se añadió un brazo con una esfera palpadora en su extremo que se utilizó en la fase de ensayo
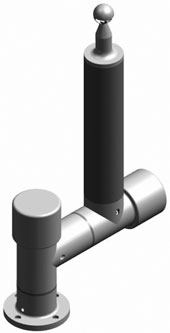
Modelo geométrico
En la figura 2 se muestra la ubicación de los distintos sistemas de referencia y los parámetros geométricos necesarios para las transformaciones. El sistema de referencia 0 es el que se considera la referencia fija. El sistema 1 gira solidario al eje vertical, por lo que los valores de q1 vendrán dados por las lecturas del encoder que mide ese giro. Del mismo modo, los valores de q2 vendrán dados por las lecturas del encoder que mide el giro con respecto al eje horizontal, eje al cual es solidario el sistema 2.
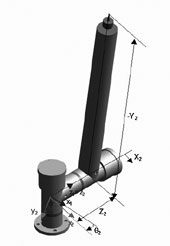
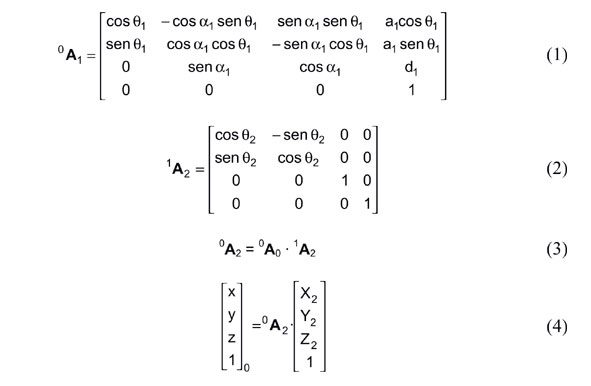
Ensayo
La captura de las lecturas de los encoders angulares y su transformación, mediante la implementación del modelo geométrico, a coordenadas cartesianas del punto medido se lleva a cabo mediante un software desarrollado también específicamente.
Optimización y resultados
Ix (mm) | Iy (mm) | Iz (mm) |
0.171 | 0.100 | 0.248 |
La determinación de los parámetros geométricos mediante medición es un aspecto crítico del proceso. Durante él mismo se comprueba que existe una gran variabilidad en los resultados de estos parámetros, principalmente debido a que resulta difícil restringir totalmente los movimientos del brazo durante su medición con la MMC.
Para obtener unos parámetros más ajustados se recurre a un proceso de optimización secuencial de los mismos. Su objetivo es minimizar el error medio de las coordenadas proporcionadas por el brazo con respecto a las de la MMC. Para ello se varía secuencialmente el valor de los parámetros en un número de puntos dentro de un intervalo establecido. Con cada combinación de los nuevos parámetros se vuelve a calcular el error medio. Si es menor que el de la etapa anterior se considera que los nuevos parámetros son mejores que los anteriores y se continúa el proceso de optimización con ellos. Tras llevar a cabo este proceso las nuevas incertidumbres obtenidas se muestran en la tabla 2.
Ix (mm) | Iy (mm) | Iz (mm) |
0.098 | 0.099 | 0.098 |
Conclusiones
Los resultados obtenidos y los procedimientos desarrollados para la confección del modelo geométrico y del algoritmo de optimización permiten pensar en la posibilidad de desarrollar procedimientos de calibración [2] destinados a la determinación de las correcciones e incertidumbres necesarias y a la mejora y optimización general de estos sistemas.
Referencias
[2] Hans Norgaard Hansen; Verification and calibration of co-ordinate measuring machines, Technical University of Denmark, (1997).