Ensayos de caracterización y validación de máquinas herramienta
Fundación Tekniker
01/09/2003
Introducción
Hay abundante literatura sobre ensayos de máquinas-herramienta. Probablemente uno de los textos “modernos” más antiguos fue escrito por Koenigsberger y J. Tlusty [1]. M. Weck [2] es el autor de otro libro clásico que considera varios aspectos de las máquinas, incluyendo los procedimientos de ensayo.
Un libro muy completo sobre mecanizado de alta velocidad fue escrito por Arnone [6]. Entre otros aspectos, incluye propuestas muy interesantes y prácticas para medir diferentes características de las máquinas de alta velocidad. El ensayo propuesto para la medición de la capacidad de procesamiento de bloques del CNC fue utilizado por los autores de este artículo, produciendo resultados significativos.
Los parámetros medidos habitualmente en máquinas-herramienta son entre muchos otros, la precisión geométrica, deformaciones térmicas, rigidez estática, comportamiento dinámico y velocidad de desplazamiento. Algunos ensayos de precisión de corte están estandarizados en ISO 10791 y NAS 913. La norma ISO 230-4 también especifica ensayos para la verificación de la precisión en trayectorias circulares, pero desafortunadamente, no hay ensayos estandarizados en la actualidad para la medición de la precisión de trayectoria de una máquina.
La norma Americana ANSI/ASME B5.54 [4] considera muchos aspectos de los centros de mecanizado CNC. Se incluyen factores ambientales como el comportamiento térmico del recinto y las vibraciones del suelo, así como ensayos de máquina. Entre los ensayos de máquina se consideran las medidas de histéresis, flexibilidad estática, repetibilidad, precisión geométrica y de posicionamiento, repetibilidad de los subconjuntos y la capacidad de corte.
Muchos fabricantes de máquina-herramienta han definido sus propios ensayos para la caracterización del comportamiento de sus máquinas. Por supuesto, es difícil obtener información de ellos. Por otra parte, en muchos casos, no es fácil adivinar qué parámetro particular se caracteriza mediante el ensayo. Por ejemplo, los autores tienen constancia de un ensayo consistente en mecanizar una trayectoria recta de ángulo muy pequeño en un eje. Se supone que lo que se caracteriza mediante el ensayo es la suavidad de desplazamiento del eje que realiza el recorrido corto, o en otras palabras, la rigidez del accionamiento ante la fuerza de rozamiento.
La rigidez estática de una máquina es un parámetro que es medido por muchos fabricantes. Probablemente el método más usual para medirla consiste en aplicar una fuerza controlada entre la herramienta o el cabezal y la pieza, y medir el desplazamiento relativo. Este procedimiento de ensayo no es muy complicado y no requiere equipamiento muy caro, pero aún y todo se requieren algunas horas para realizarlo. La medición mediante un ensayo de corte podría ser más interesante para eliminar la influencia de no linealidades y para incluir mejor el comportamiento de los accionamientos.
Un ensayo interesante utilizado por algunos fabricantes y usuarios de máquina-herramienta para caracterizar la rigidez estática consiste en realizar un fresado tangencial de una pieza a velocidad constante hasta un punto, parar durante unos segundos, y continuar el fresado. La herramienta dejara una marca en la zona de parada, cuya profundidad depende de la rigidez estática de la máquina. El ensayo es de alguna manera similar al propuesto en la norma ANSI/ASME B5.54, y tiene el mismo problema: no hay manera de trasladar el resultado medido en micras a un valor de rigidez.
La precisión de contorneado se está convirtiendo en un parámetro muy importante, especialmente en máquinas de alta velocidad. La manera habitual de caracterizarla es mediante el mecanizado de piezas patrón como Mercedes, Cachan o NCG. La mayoría de las veces, los resultados son evaluados de manera subjetiva aunque es posible medir las piezas obtenidas en una máquina de medida de coordenadas. En la práctica, no se realiza esta medición debido al largo tiempo requerido. Por otra parte no existe una guía clara que determine exactamente qué medir y como obtener conclusiones sobre la calidad de la máquina.
Varios ensayos han sido propuestos [3] para el análisis del comportamiento de los ejes de avance en tornos, pero también requieren la verificación de la pieza mecanizada fuera de la máquina.
Otra propuesta interesante para la verificación de máquinas mediante el mecanizado de piezas patrón, que incluye la justificación del interés de las diferentes formas de la pieza, fue ofrecida por E. Duc [5]. Se puede argumentar que el artículo propone la evaluación de la mayoría de los resultados por análisis visual, mientras que los resultados restantes son medidos o calculados fuera de la máquina-herramienta. Ninguno de los métodos propuestos puede ser considerado objetivo y simple al mismo tiempo.
El presente artículo propone ensayos, simples comparables y rápidos para la caracterización de la capacidad de aceleración y de jerk, la rigidez estática y la precisión de interpolación. Estos ensayos son realizados sin instrumentación específica y cubren algunos de los aspectos que no son correctamente caracterizados mediante los ensayos estándar.
Capacidad de aceleración y de Jerk
Las máquinas de alta velocidad utilizan CNCs de altas prestaciones, los cuales incluyen la función de control previo (Feed Forward) así como la de Look Ahead. El control previo da lugar a cambios de aceleración repentinos, lo cual produce fuertes vibraciones en el accionamiento y en la estructura de la máquina. Para evitar eso, se utiliza la función de Look Ahead para limitar el jerk (o rampa de aceleración) a un nivel que la máquina pueda soportar.
Se puede argumentar que la aceleración y el jerk son parámetros programados en el CNC y que por tanto no hay necesidad de que sean medidos. Sin embargo, en ocasiones, puede suceder que la máquina sea incapaz de alcanzar la aceleración programada bien por limitaciones mecatrónicas o bien por un valor programado de jerk excesivamente bajo. Otras veces, las unidades en las que se programan estas magnitudes pueden dar lugar a confusiones. La experiencia demuestra que es muy interesante medir estas magnitudes.
Para la medición de la aceleración suelen utilizarse osciloscopios, o la propia función de osciloscopio del CNC, y representar la evolución de la velocidad haciendo que cada eje vaya desde parado a un valor alto de velocidad. Dividiendo el incremento de velocidad entre el tiempo transcurrido en obtener el incremento, se calcula la aceleración del eje. Los problemas de este procedimiento son que debe ser ejecutado por una persona experimentada y que no permite hacer una buena estimación de la capacidad de jerk de la máquina.
Medir el jerk real es más complicado que medir la aceleración y, en la práctica, no se mide.
El ensayo propuesto para medir la capacidad de aceleración y de jerk real de cada eje de la máquina, consiste en medir el tiempo requerido para realizar dos recorridos de diferente longitud y puede ser realizado con la ayuda de un simple cronómetro. La longitud de los recorridos debe ser seleccionada de tal manera que en ambas se alcance la aceleración máxima pero no la velocidad programada (que es la velocidad máxima programable). De esta manera, los perfiles de aceleración y velocidad en función del tiempo tienen la forma mostrada en la Figura 1.

Sea S1 la longitud del recorrido corto y S2 la del largo. Similarmente, si t1 es el tiempo empleado en realizar el recorrido corto yt2 el empleado en realizar el largo, se calcula el tiempo de jerk (tiempo requerido para obtener la aceleración máxima) mediante la siguiente expresión:
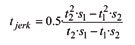

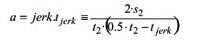
Una segunda verificación debe ser realizada para asegurarse de que no se ha alcanzado la velocidad programada en el recorrido largo. Para eso, la velocidad máxima alcanzada en este recorrido es calculada mediante

Como valores iniciales de los recorridos pueden ser seleccionados 15 y 30 mm. Si fuera necesario cambiar estos recorridos es aconsejable mantenerlos tan separados como sea posible, siendo un límite práctico s2>1.25s1.
Si no fuera posible obtener recorridos que cumplan la condición s2>1.25s1, indicaría que la máquina no está bien balanceada, es decir, que el valor de jerk es demasiado bajo para la máxima velocidad y aceleración de la máquina.
Es interesante reseñar que ejecutando estos ensayos, se ha descubierto que muchas máquinas tienen motores dimensionados para obtener elevadas aceleraciones que en la práctica nunca se obtienen, porque se alcanza la velocidad máxima antes de alcanzar la aceleración máxima. Una solución evidente es aumentar el valor de jerk, pero entonces, surgen las limitaciones estructurales de la máquina.
La aceleración es uno de los parámetros de las máquinas herramienta que no puede ser medidos con facilidad. Este hecho ha dado lugar históricamente a que los fabricantes hayan comunicado valores muy exagerados de este parámetro
Concluyendo, hay que tener un cuidado especial cuando se diseñan máquinas grandes de alta velocidad. Por ejemplo, una velocidad de trabajo de 0.4 m/s y aceleración de 8 m/s2 requieren un valor mínimo de jerk de 160 m/s3. Para que una máquina sea capaz de soportar este valor de jerk con un buen comportamiento dinámico, sus frecuencias naturales deberían estar por encima de los 90Hz, lo cual está lejos del estado del arte en máquinas grandes. Valores más bajos de jerk producen que la máquina nunca alcance esa aceleración.
Siguiendo con el ejemplo propuesto, si el jerk máximo esperado es de 40 m/s3 , la máxima aceleración que podrá ser obtenida es 4 m/s2. Dimensionar los motores para una aceleración más grande sería derrochar dinero, a no ser que los desplazamientos rápidos (en vacío) sean una parte importante del tiempo de mecanizado.
Precisión de interpolación
Actualmente muchos controles numéricos son capaces de efectuar ensayos de trayectoria circular y comparar la trayectoria programada con la trayectoria medida por las reglas, es decir, sin necesidad de mecanizado de piezas. Estos ensayos dan una buena información, pero sin olvidar que en trayectorias con aceleraciones elevadas, puede haber diferencias notables entre la medida de las reglas y la posición de la herramienta, debido a las deformaciones inerciales de la máquina. Como referencia, una máquina de grandes dimensiones, con una frecuencia natural de flexión del carnero de unos 37 Hz, dará lugar a deformaciones inerciales del orden de 0.280 mm para una aceleración de 10 m/s2. Una máquina más pequeña, con una frecuencia natural de 60 Hz dará lugar a una deformación inercial de unas 100 um para la misma aceleración. Se comprende que estas grandes deformaciones darán lugar a que la trayectoria de la herramienta sea muy diferente a la trayectoria detectada por el sistema de medida.
Por ello, para la caracterización de la máquina en estos casos, es más adecuada la utilización, cada vez más extendida, del ball-bar, o la realización de ensayos de fresado (las ya mencionadas pieza NAS 913 o ISO 10791 por ejemplo).
La información proporcionada por las trayectorias circulares está lejos de ser completa. Estas trayectorias tienen cambios de aceleración muy suaves, y con la función de control previo, la posición medida por las reglas puede ser muy similar a la posición comandada. Trayectorias más complicadas con repentinos cambios de velocidad y de aceleración, producen errores más grandes, los cuales tienen que ser reducidos por la limitación de jerk de la función de Look Ahead.
Hay varias piezas patrón que han sido prácticamente estandarizadas para la caracterización del comportamiento de fresadoras de alta velocidad: Mercedes, Cachan, NCG, etc. El valor de estas piezas está probado por su amplia aceptación. Su mayor deficiencia es la dificultad de obtener comparaciones objetivas. La medición de las piezas debe realizarse en máquinas de medición de coordenadas, lo cual es un proceso largo, y por otra parte, no está definido qué medir exactamente y como procesar las medidas. En la práctica estas piezas son comparadas por inspección visual, lo cual es propenso a errores e imposible de realizar si todas las piezas no están disponibles al mismo tiempo.
Para obtener resultados objetivos y rápidos, se ha desarrollado una nueva pieza patrón, mostrada en la Figura 2. La pieza puede ser verificada en la misma máquina y los resultados son representados en gráficas que pueden ser comparadas de máquina a máquina.

Los primeros tramos (arcos de círculo) producen escalones de aceleración, es decir, impulsos de jerk. La forma triangular produce escalones de velocidad, suavizados por el radio de las esquinas y de forma similar, el escalón produce un escalón de posición suavizado.
La pieza debe ser pre-mecanizada y posteriormente el ensayo de mecanizado debe ser realizado con una penetración radial muy baja: 0.4 mm son suficientes. El material de la pieza es un aluminio fácil de mecanizar. Las condiciones de corte son seleccionadas de tal manera que las fuerzas de corte sean mínimas y los errores de forma se deban solamente a fuerzas inerciales y al error de seguimiento en los lazos de control. El diámetro de la herramienta debe ser menor que 20 mm, siendo 12 mm un tamaño razonable. La Figura 3 muestra la máquina, la herramienta y la pieza mecanizada.
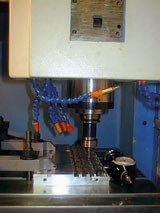
La fricción entre la bola y la superficie mecanizada es una fuente de error porque produce una desviación tangencial del palpador. Por esta razón la penetración de la bola debe ser programada al valor mínimo que evite la separación de la misma durante la medida.
El programa de medida debe parar antes de cualquier discontinuidad en la trayectoria. Así, los valores máximo y mínimo del palpador en el tramo anterior son grabados.
Es también necesario medir el tiempo requerido en mecanizar la pieza. Para ello, lo mejor es repetir el recorrido en vacío adelante y atrás varias veces sin parada, medir el tiempo total, y dividirlo por el número de repeticiones.
El ensayo debe ser repetido para diferentes velocidades de avance. La velocidad real será menor que la programada la mayor parte del tiempo, debido a la limitación producida por la función de Look Ahead y por esta razón se propone representar gráficamente los valores de los errores máximos registrados en cada uno de los tramos contra el tiempo requerido en completar la trayectoria.
La experiencia ha demostrado que en una máquina de altas prestaciones, bien ajustada, capaz de obtener excelentes piezas “Mercedes”, los errores obtenidos en el ensayo son del orden de 0,02 a 0,04 mm para tiempos de mecanizado del orden de 2,2 s. Máquinas de peores prestaciones, incapaces de obtener buenas piezas “Mercedes” tienen errores 10 veces más grandes, 0,2 a 0,4 mm para el mismo tiempo de mecanizado.
Rigidez estática
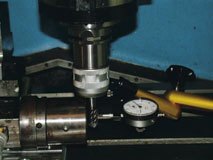
Con el objetivo de obtener un ensayo de corte simple y rápido para determinar la rigidez estática, fue considerado necesario que el corte fuera realizado en una trayectoria continua de manera que pudiera ser medido usando un comparador en el cabezal. Para ello el procedimiento mostrado en la Figura 5 fue definido.
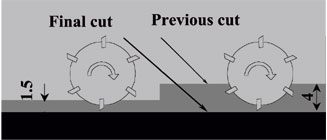
En estas condiciones la fuerza en la dirección de avance es prácticamente inexistente, la fuerza axial tiene un valor medio de 25N y la fuerza perpendicular a la superficie tiene un valor medio de 135 N. Se asume que la influencia de la fuerza axial en la deformación radial es despreciable.
El ensayo puede ser realizado con el avance en las direcciones X e Y, para medir la rigidez estática en las direcciones Y y X respectivamente. Aún no se ha definido ningún ensayo para la dirección axial.
La deformación medida incluye la deformación de la máquina y de la herramienta. Si una pieza razonablemente rígida es usada, su deformación debería ser despreciable. La deformación de la herramienta puede ser estimada mediante

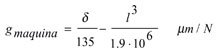
En los ensayos realizados, los valores de rigidez estática obtenidos siguiendo esta propuesta tienen una tendencia a ser sobre un 10 por ciento más bajos que por medidas tradicionales.
Referencias
[2] Weck, M., 1991, Werkzeugmaschinen Fertigungssysteme Band 4, Messtechnische Untersuchun und Beurteilung, VDI Verlag.
[6] M. Arnone, 1998, High Performance Machining, Hanser Gardner Publications, Cincinnati.
[4] ANSI/ASME B5.54, 1993, Method for Performance Evaluation of Computer Numerically Controlled Machining Centers, ASME, NY
[3] T. Bispink, 1992, Performance Analysis of Feed Drive system in diamond turning by machining specified test samples, Annals of the CIRP 41/1:601-604
[5] E. Duc, C. Lartigue, F. Thiebaut, 1998, A test part for the machining of free-form surfaces, International Seminar on Improving Machine Tool Performance, CIRP, San Sebastián.