Inspeccionar piezas en sus máquinas-herramienta
Este artículo explica cómo algunas de las empresas más competitivas utilizan técnicas complementarias para mejorar el funcionamiento de las máquinas y realizar una inspección final de las piezas mientras las mismas todavía se encuentran en la máquina. Reducir los ciclos de fabricación y verificación mientas se incrementa el rendimiento de la máquina-herramienta supone el siguiente reto:
• Fabricación de piezas “buenas” mediante la seguridad de que sus máquinas son capaces de fabricar las piezas según las especificaciones requeridas antes de empezar a fabricarlas.
• Demostrar que las piezas están según las especificaciones requeridas mediante la introducción de procesos de control y métodos de verificación de la máquina.
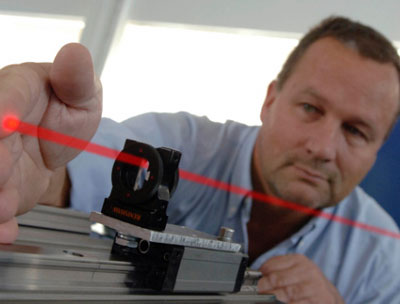
¿Cómo puede hacer que sus piezas sean correctas desde un principio?
Para asegurarse de que sus máquinas siempre están a pleno rendimiento, sólo tiene que seguir los pasos especificados a continuación. Las herramientas que necesitará son las siguientes:
• Un interferómetro láser - puede utilizar el suyo propio o bien solicitar un servicio de calibración.
• Un Sistema Ballbar - que le permitirá conseguir las normas requeridas en ASME B5.54 e ISO 230-4.
• Un juego de galgas para ayudar al diagnóstico y, en algunos casos, rectificar los problemas identificados.
• Errores de calibración. Use sistema de calibración láser para eliminar errores de posicionamiento. Por ejemplo, si el ballbar identifica errores de escala calibre con láser el eje que necesita ser corregido su error lineal. Empleando un sistema láser en sus máquinas las fabricará con características de repetibilidad y precisión.
• Establezca un nuevo punto de inicio de control. Una vez la causa del error geométrico ha sido eliminada o minimizada, vuelva a testear el ballbar para establecer el nuevo punto de inicio de control para su máquina.
• Ensayos de diagnóstico regulares. Realice diagnósticos regularmente (al menos una vez al mes) para detectar alguna desviación desde el punto de inicio de control. Para trazar los parámetros de calidad de la máquina crítica en un gráfico de control (vea el ejemplo a la derecha), usted tiene un gráfico con histórico de los ensayos de su máquina, y usted puede programar el mantenimiento antes de que los resultados de la calidad de los resultados de la máquina se deterioren. Si ocurriese una colisión, emplee el ballbar para ver si su máquina está todavía en buen estado para continuar la producción.
Seis pasos para mejorar la capacidad de su máquina
- Determinación de la precisión requerida - la tolerancia del plano determinará la precisión que se requiere de la máquina.
- Establecimiento de líneas básicas: rendimiento actual - hacer una inspección con el ballbar. En esta simple acción que dura 10 minutos, su máquina se moverá en un plano circular programado. El ballbar detectará las desviaciones de la máquina comparándolas con el plano circular, que representarán los errores sobre una interpolación de dos ejes.
- Identificar y categorizar las fuentes del error - el software del ballbar está preparado para aislar 18 parámetros de la máquina y para analizar la precisión del posicionamiento (los campos de error incluyen errores cíclicos, de cuadratura, vibración de la máquina, picos de inversión, descompensación de contaje entre ejes, “stick-slip”, juego de los ejes, desregulación de servos).
- También ofrece una indicación de la precisión del posicionamiento dinámico desde los valores de “circularidad” y “error de circularidad” en concordancia con las normas internacionales. Utilice esta información para priorizar el mantenimiento y determinar la mejor acción correctiva, compensación o reparación.
- Elimine o calibre los errores - use sistema de calibración láser para eliminar errores de posicionamiento. Por ejemplo, si el ballbar identifica errores de escala calibre con láser el eje en el que necesita ser corregido su error lineal. Empleando un sistema láser en sus máquinas las hará repetibles y precisas.
- Establezca un nuevo punto de partida - una vez la causa del error geométrico ha sido eliminada o minimizada, vuelva a pasar el ballbar para establecer el nuevo punto de partida de su máquina.
- Ensayos de salud regulares - realice diagnósticos regularmente (al menos una vez al mes) para detectar alguna desviación desde el punto de partida. Para trazar los parámetros de calidad de la máquina crítica en un gráfico de control (vea el ejemplo a la derecha), usted tiene un gráfico con histórico de los ensayos de su máquina, y puede programar el mantenimiento antes de empezar a generan piezas malas. Si ocurriese una colisión, emplee el ballbar para ver si su máquina está todavía en buen estado para continuar la producción.
Otras formas de mejorar el rendimiento de la máquina
El rendimiento de los encóderes láser puede mejorarse a través de la compensación a tiempo real de la dilatación térmica de otras partes de la máquina, como la mesa o el mandrino u otros componentes. Un sistema de compensación de un eje simple, como es el sistema RCU10 de Renishaw mejora la precisión de posicionamiento de la máquina al ajustar el número de pulsos desde el encóder en concordancia con múltiples lecturas de la temperatura tomadas en distintas partes de la máquina. También le proporciona una compensación del índice de refracción en tiempo real para los encóderes láser, resultando la precisión del sistema en posicionamiento por debajo de una parte por millón (PPM) a través de una amplia gama de temperatura (0-40 °C), presión (750-1150 mbar) y humedad (0-95% sin condensación).
Hay tres técnicas que han evolucionado para permitir la inspección de piezas en máquina con carga y con incertidumbre conocidas
¿Cómo puede verificar que sus piezas son correctas?
Mito 1 - la utilización de sonda aumenta los ciclos de tiempo.
Usted debería solamente utilizar una sonda en su máquina para reducir los ciclos de tiempo. Esto puede sonar un poco contradictorio, pero no lo es cuando se define “ciclos de tiempo” de una forma correcta. Los ciclos de tiempo no se refieren simplemente al tiempo que usted utiliza mecanizando.
La utilización de sondas le hará acortar los ciclos de tiempo al reducir:
• Tiempo de Ajuste - la utilización de sondas automatiza el ajuste de pieza y herramienta, reduciendo tiempos muertos.
• Tiempo de certificación - la verificación post-proceso y fuera de la línea de producción a veces, además de necesitar tiempo extra, en algunos casos es imposible de realizar ya que puede acumular el trabajo y los costes hasta puntos inimaginables. Los métodos manuales necesitan evaluaciones extras y además están expuestos al error humano. En cambio, las sondas para máquina-herramienta le permitirán verificar la pieza sin demora y sin ningún equipo adicional.
• Piezas rechazadas - los pasos de centrado e inspección de pieza con retroalimentación de la información automatizada pueden eliminar errores del operario y compensar el tiempo utilizado en el proceso.
Mito 2 - no se puede fiar de la máquina que mecaniza las piezas para medirlas.
Así pues, sus máquinas están rindiendo al máximo de sus posibilidades, pero usted todavía se enfrenta al reto diario de obtener piezas buenas a pesar de posibles variaciones en el utillaje, los materiales, los cambios ambientales del taller y del error del operario. El reto es: probar que sus piezas están dentro o fuera de especificación mientras están todavía en la máquina, pero ¿puede confiar en la máquina en la que mecanizó sus piezas para que ésta las mida?
La respuesta es sí -usted puede utilizar cualquiera de sus máquinas como un dispositivo de inspección, asumiendo que usted conoce la incertidumbre de las mediciones que ellas realizan y que las mediciones son trazables. Si esta incertidumbre es suficientemente baja en relación a sus tolerancias, entonces usted puede inspeccionar piezas con una sonda y “pasarlas” en sus máquinas-herramienta. Recuerde que la inspección con sonda es un proceso libre de carga y en consecuencia puede detectar errores que hayan ocurrido durante el mecanizado y que no estarán presentes al medir- por ejemplo, rotura de herramienta, desgate y deflexión, excentricidad del mandrino y conformidad de máquina.
El problema de la incertidumbre
• Las máquinas-herramienta no suelen estar en entornos con temperatura controlada -la temperatura ambiente afecta a las piezas y a las máquinas y los gradientes de temperatura pueden causar distorsión en las piezas y en las máquinas.
• Las máquinas-herramienta generan calor -calor del motor del cabezal que puede afectar al eje Z, mientras que los motores de accionamiento de los ejes y la fricción en los cojinetes puede afectar a la longitud de los husillos a bolas.
Más aún, los errores geométricos subyacentes en las máquinas-herramienta tienden a ser mayores que en las MMC dado que para muchas máquinas, sólo algunos errores pueden ser compensados en el CNC- fuentes de error como la cuadratura, rectilinealidad o ladeo y cabeceo angular con frecuencia permanecen sin ser corregidas. Estos errores sistemáticos además de errores térmicos, si no se remedian, degradarán las prestaciones de su máquina como herramienta de corte y como dispositivo de medición. Si usted debe inspeccionar piezas en su máquina-herramienta con confianza, necesita eliminar algunos de estos errores y cuantificar aquéllos que no sean eliminados.
Introducción de una medición precisa y trazable en sus máquinas
Hay tres técnicas que han evolucionado para permitir la inspección de piezas en máquina con carga y con incertidumbre conocidas. Cuál debería escoger usted, depende de su proceso de mecanizado:
La trazabilidad puede ser introducida en la inspección en su máquina-herramienta en forma de un artefacto (una pieza genérica o bien una réplica) de las que hemos obtenido sus dimensiones en una MMC a 20°C. El artefacto puede “vivir” en su máquina-herramienta debe ser del mismo material que los componentes mecanizados, asegurándose así que sufre las mismas distorsiones térmicas que los componentes mecanizados. Antes de medir su componente, debe inspeccionar el artefacto con la sonda y utilizar las diferencias entre las dimensiones reales y las teóricas para derivar las correspondientes compensaciones, que tienen en cuenta las condiciones actuales de la máquina. Utilice estas compensaciones para ajustar las mediciones de los componentes también llevadas a cabo en su máquina. Esta técnica es muy adecuada para la fabricación de componentes pequeños, en la que el artefacto puede estar permanentemente acomodado en la máquina o introducido en ella con facilidad, de manera que el proceso puede ser completamente automatizado. Sin embargo, puede también aplicar esta técnica en máquinas más grandes con intervención adicional del operario.
Midiendo con una precisión trazable de ±6 µm.
En una línea de muchas máquinas-herramienta CNC en sus instalaciones en Inglaterra, los ingenieros de Renishaw utilizan artefactos para certificar piezas en la máquina según una norma trazable.
Tras mecanizar, las piezas y el artefacto son limpiados con refrigerante para limpiarlos e igualar la temperatura. El artefacto y los útiles de fijación se montan en un eje indexado de manera que pueden ser posicionados bajo el cabezal e inspeccionados durante el giro.
En el caso de un artefacto genérico, se derivan factores de escala de las diferencias entre las dimensiones teóricas y las medidas y entonces son aplicadas a las mediciones de tamaño tomadas en el componente. Cuando se utilizan réplicas, se pueden hacer correcciones directas de posición y de distancia entre características.
Al utilizar la máquina como un comparador se pueden conseguir incertidumbres de medición trazables próximas a la repetibilidad local de la máquina en un plazo corto de tiempo. Se consiguen incertidumbres tan buenas como ±6 µm.
Para Renishaw, el beneficio de medir piezas en las máquinas-herramientas incluye la no intervención manual, operación a 3 turnos y un muy bajo porcentaje de piezas desechadas.
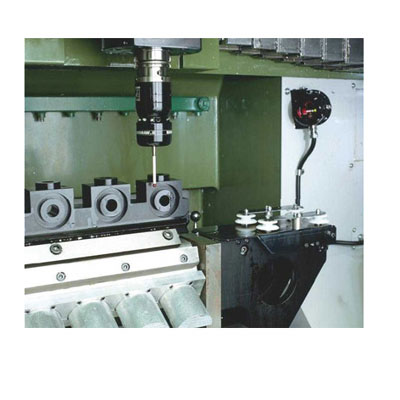
Una MP700 midiendo características en un artefacto genérico calibrado en una MMC.
Las compensaciones derivadas de esos errores en esas medidas son usadas para corregir las dilataciones térmicas y errores geométricos que afectarían a la precisión de la medición.
Huella
Mida todas las demás piezas en su máquina-herramienta ajustando cada medición (en bruto) con las correcciones determinadas a través del proceso descrito anteriormente. Este proceso genera un mapa de error que está contenido en la piel de cada pieza que va a ser medida y es relevante sólo para las características medidas en ese tipo de pieza. La técnica de la huella es adecuada para producción de series en condiciones de temperatura y entorno consistentes - si la temperatura cambia de modo significante, entonces se requerirá una corrección térmica sistemática o bien una re-certificación periódica.
Incertidumbre de la medición derivada
• Midiendo las cuatro diagonales del cuerpo con un interferómetro láser para establecer Ed - la desviación sistemática bi-direccional mayor en posicionado. Como ya se ha discutido, usted puede reducir este error montando reglas láser y compensación de temperatura en tiempo real.
• Midiendo una característica pequeña (un anillo patrón o una esfera calibrada) diez veces y entonces calculando el error de repetibilidad del vector (ERV) y la precisión de medición de la pieza (PMP).
• RMV = Ed + ERV + PMP
El RMV identifica el límite de la capacidad de su máquina-herramienta para medir - si sus tolerancias de fabricación demandan que usted mida con mayor precisión que ésta, entonces tendrá que buscar otros métodos. Por supuesto, usted también tendrá que tener en cuenta los efectos de la temperatura si éstos son significantes. Tenga en cuenta que la norma B5.54 también recomienda utilizar un “ballbar” para obtener mejor conocimiento de los factores que contribuyen al rendimiento volumétrico.
Incertidumbre de la medición derivada:
Allá donde no resulta práctico mover sus piezas para ser medidas, y donde los artefactos no pueden ser acomodados o introducidos en su máquina, entonces necesita otra alternativa
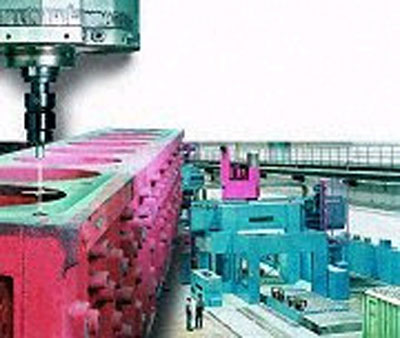
Medición en ciclo para control trazable de proceso
• Establecer la capacidad de proceso de mecanizado - entender la variación inherente y subrayar el ratio de desviación en sus procesos de mecanización midiendo piezas en la máquina, utilizando una de las técnicas trazables explicadas previamente, o en su MMC trazable. Compare esta capacidad con las tolerancias de su pieza para determinar cuán a menudo usted necesitará inspeccionar las piezas para mantener el proceso bajo control.
• Dé cuentas de la capacidad del proceso de inspección - conozca la precisión trazable de las mediciones en su máquina, incluyendo la repetibilidad de las mediciones. Téngala en cuenta al definir el umbral de su proceso de control.
• Establezca un régimen de retroalimentación del proceso - usted no quiere medir más características de las que sean necesarias, así que identifique aquéllas que son críticas para el comportamiento del producto fabricado. De forma ideal, mida una característica de control por cada herramienta de acabado, y utilice la error de la medición para compensar el “offset” de la longitud o tamaño de esa herramienta.
El software de centrado e inspección de pieza, como el “Inspection Plus” de Renishaw, simplifica el control de proceso estableciendo límites de control y aplicando un cierto factor a las correcciones de los “offsets”. Usted puede, por supuesto, utilizar reglaje de herramientas para producir piezas buenas desde la primera asegurándose de que los “offsets” de las herramientas están correctamente entrados en las tablas de correctores al iniciar un ciclo productivo, e incluir detección de rotura de herramientas para aumentar su confianza en un mecanizado desatendido.
El software de centrado e inspección de pieza, como el “Inspection Plus” de Renishaw, simplifica el control de proceso estableciendo límites de control y aplicando un cierto factor a las correcciones de los “offsets”