Tomografía computarizada como método de ingeniería inversa
A. Pascual e I. Holgado, del Centro de Fabricación Avanzada en Aeronáutica, CFAA (UPV/EHU); N. Ortega y S. Plaza, del Departamento de Ingeniería Mecánica. Escuela de Ingeniería de Bilbao (UPV/EHU)
18/02/2020Con el propósito de demostrar la capacidad de aplicación de la tomografía computarizada por rayos X como método de ingeniería inversa, se ha procedido inicialmente a contextualizar cada técnica por separado, siempre desde la perspectiva a estudio, para posteriormente realizar una pequeña revisión bibliográfica poniendo de manifiesto el potencial de esta tecnología en distintas aplicaciones de ingeniería inversa, en este caso centradas en el ámbito clínico e industrial.
Finalmente, se presentan algunos de los proyectos de investigación que se han llevado a cabo en el CFAA, alineados con esta temática.
1. Ingeniería inversa
1.1. Introducción
El concepto de ingeniería inversa hace referencia a la regresión de un proceso habitual de ingeniería, como se puede apreciar en la figura 1. De este modo, en lugar de partir de la información pertinente para la generación de un producto o sistema, se obtiene la información a partir del propio producto o sistema. Por tanto, la aplicación de dicha estrategia permite discernir los principios tecnológicos que rigen el funcionamiento del conjunto y de cada subconjunto por separado, con el objetivo de proporcionar la mayor cantidad de información técnica posible. Dicha información puede ser referente a los principios físicos y de funcionamiento, a los tipos de materiales y a las estrategias de diseño y ensamblado, cuando se trata de productos o sistemas físicos tales como máquinas, dispositivos o componentes (lo que se denomina como ingeniería inversa de hardware), mientras que, en caso de tratarse de códigos de programación o de aplicaciones digitales, hace referencia a soluciones de software (que se conoce como ingeniería inversa de software) [1].
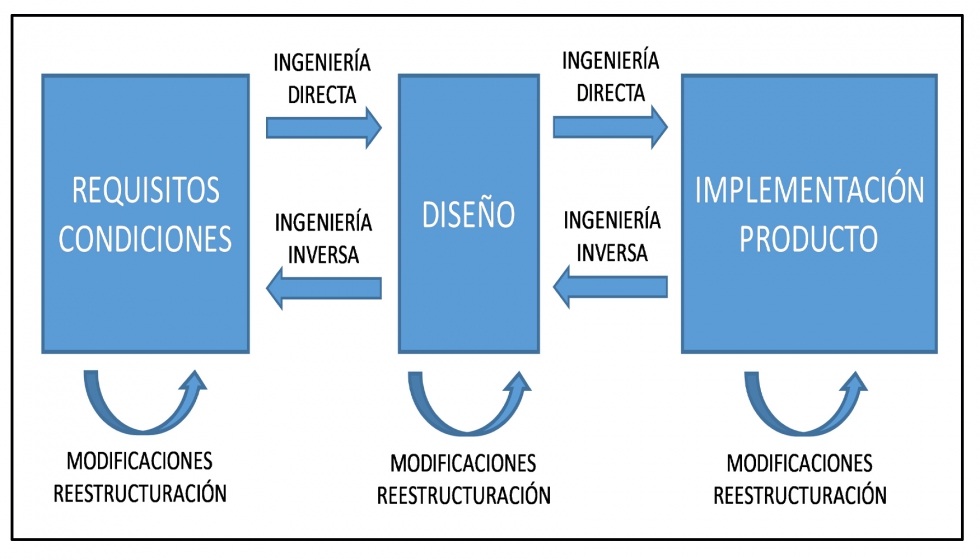
Por tanto, la implementación de este procedimiento adquiere mayor importancia cuando se carece de dicha información para la ejecución de un proceso y únicamente se dispone del producto o sistema final.
En resumen, la ingeniería inversa consiste en desensamblar un sistema producto o dispositivo con el propósito de entender su funcionamiento y composición para generar una copia del mismo, un diseño alternativo (pero manteniendo la funcionalidad) o una versión mejorada del mismo.
1.2. Antecedentes
El origen de la ingeniería inversa se remonta a la Segunda Guerra mundial, donde los avances tecnológicos de ambos bandos determinaban la diferencia. En este contexto, el conocimiento de los productos y avances del enemigo se retornaba vital. De modo que, la implementación de esta técnica fue esencial para la resolución del conflicto.
Un caso de éxito y digno de mención en la aplicación de este procedimiento es el referente a los sistemas informáticos. A principios de los 80, IBM dominaba el sector de la informática empresarial gracias a una BIOS legalmente irreproducible, cuyo código ocupaba apenas 8 kB. Sin embargo, la irrupción de Phoenix Technologies a mediados de la década, aplicando el concepto de ‘clean room’ (también conocido como ‘Chinese wall’) de ingeniería inversa, fue capaz de replicar la funcionalidad de dicho subsistema sin copiarlo, permitiendo la aparición de los PCs clónicos y propiciando la pérdida de control hegemónico que IBM patentaba sobre el hardware hasta entonces.
1.3. Campos de aplicación
En vista de la manifiesta versatilidad del empleo de esta técnica, su aplicación presenta innumerables posibilidades con un amplio rango de campos de aplicación, desde los relacionados con productos industriales a los involucrados en el ámbito de las aplicaciones informáticas o de software, pasando por soluciones del dominio de la medicina y la biología.
A modo de ejemplo, se muestran algunas de las aplicaciones habituales de esta técnica en la tabla 1.
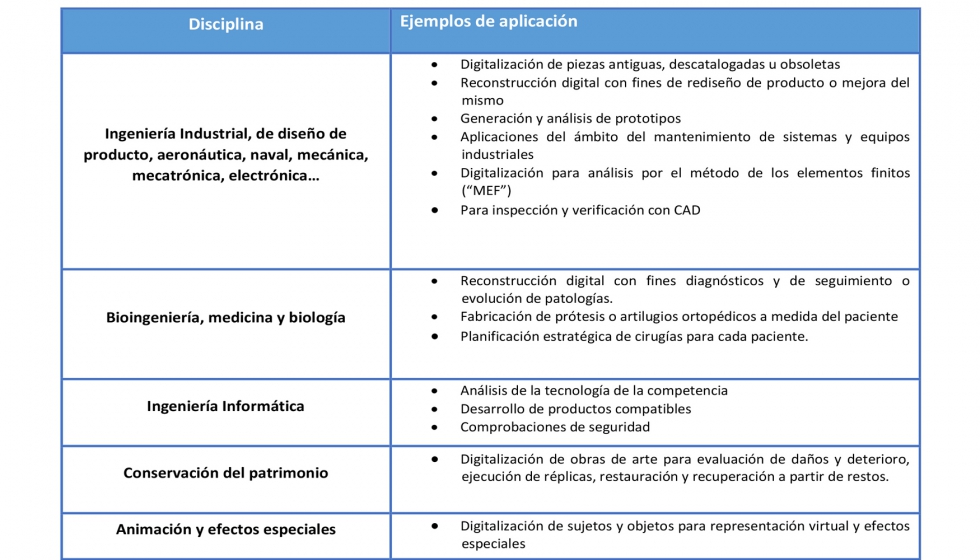
Este artículo se contextualiza principalmente en el ámbito industrial, aunque se realizan ciertas alusiones al ámbito sanitario. A pesar de ello, su metodología es extrapolable prácticamente a cualquiera de los ámbitos y aplicaciones descritas previamente.
1.4. Generalidades
Dado que el ámbito de la ingeniería inversa de hardware hace referencia a sistemas, dispositivos, conjuntos u objetos físicos, su principal competencia consiste en la adquisición de información a partir de un producto real en 3D. Posteriormente, la denominada ingeniería inversa de software es la encargada del procesamiento de dicha información con el propósito de alcanzar la versión CAD del mismo (modelo geométrico en 3D).
A) Adquisición de información (Ingeniería inversa de hardware)
Esencialmente, existen tres tipos de tecnologías principales para la adquisición de información: por contacto, sin contacto y destructivas. Por tanto, las variables de salida de este tipo de procesos de adquisición de información serán principalmente imágenes 2D en secciones transversales y nubes de puntos capaces de definir la geometría del producto analizado.
En la figura 2 se muestra un esquema de clasificación de cada tecnología y en la tabla 2 se describen brevemente cada uno de los métodos mencionados de forma genérica, según lo expuesto en [1], [2] y [3].
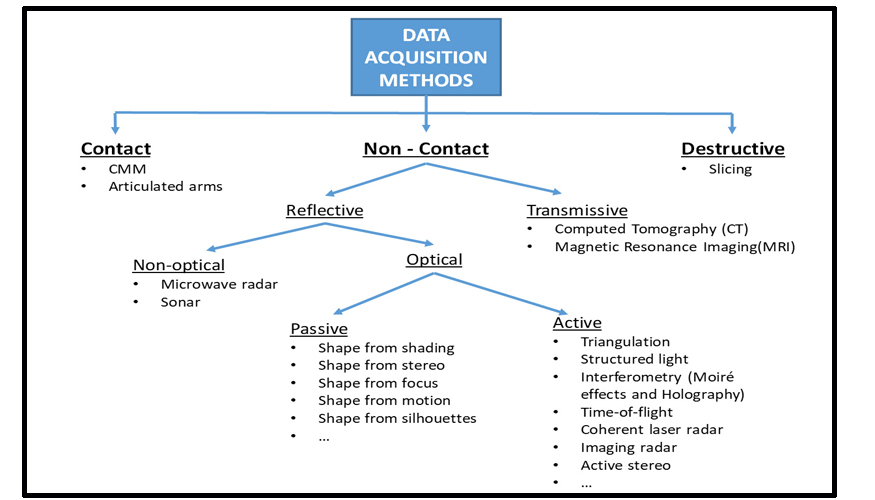
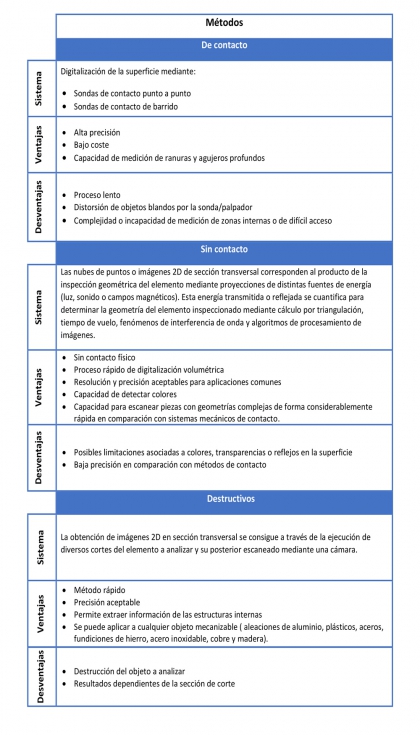
Una de las técnicas expuestas que se presenta como una alternativa muy prometedora a los sistemas convencionales, es la referente a la XRCT. La principal virtud del empleo de esta técnica frente a sistemas de medición táctiles y ópticos, es la capacidad de facilitar información de las estructuras internas del elemento a inspeccionar, mientras que los sistemas descritos requieren de geometrías y superficies accesibles y visibles para su correcta interpretación [4]. Por consiguiente, el empleo de esta tecnología permite una reducción considerable del tiempo de escaneo necesario, especialmente cuando se trata de piezas con formas complejas u ocultas, además de generar un mayor conocimiento del funcionamiento del sistema, dada su idoneidad para la ejecución de un análisis más exhaustivo que el permitido mediante la utilización de las tecnologías competentes mencionadas.
Por otro lado, resulta imprescindible mencionar su capacidad de inspección de las estructuras internas sin necesidad de destruir el objeto a estudio. De ahí su empleo tanto a nivel industrial como técnica para ensayos no destructivos, como en el ámbito médico-biológico al tratarse de una técnica no invasiva. En este último campo, también resulta frecuente el empleo de la adquisición de Imágenes por Resonancia Magnética (MRI), cuyo interés radica en la ausencia de radiación durante el proceso de adquisición de la información, además de ofrecer una calidad superior en las imágenes de tejidos blandos como órganos, músculos, cartílagos, ligamentos y tendones de distintas partes del cuerpo humano. Sin embargo, dada la capacidad de la XRCT para inspeccionar materiales de densidades diversas, al igual que tejidos blandos, sus competencias abarcan desde huesos y tejidos, correspondientes al sector biosanitario, hasta cerámicas, plásticos y metales, en el ámbito industrial.
Según lo dispuesto anteriormente, es evidente que esta técnica de XRCT se postula como una de las opciones más alentadoras a tener en cuenta en la aplicación de un proceso de ingeniería inversa, jugando un papel imprescindible para ciertas aplicaciones sanitarias, sin desestimar su creciente repercusión en el ámbito industrial, entre otros. Por este motivo, esta técnica y su aplicación como método de ingeniería inversa se analiza con mayor profundidad en los apartados siguientes.
B) Procesado de la información (Ingeniería inversa de software)
El procesamiento de la información proporcionada por la etapa anterior tiene como resultado la obtención de un modelo geométrico en 3D. Este modelo final puede ser de dos tipos: mallas poligonales (normalmente en formato STL) o NURBS. Los modelos constituidos por polígonos se emplean principalmente en aplicaciones de prototipado rápido, mecanizado por láser, simulación, animación y gráficas 3D, mientras que las superficies o sólidos definidos con formato NURBS se utilizan de forma frecuente en aplicaciones relacionadas con diseño asistido por ordenador, fabricación y aplicaciones de ingeniería (CAD-CAM-CAE).
La calidad del modelo geométrico obtenido en esta etapa vendrá definida por la cantidad de puntos extraídos del objeto inspeccionado, el formato de extracción de dicha información y el método de reconstrucción geométrico en base a los puntos obtenidos, además del software empleado para la ejecución de esta tarea.
2. Tomografía computerizada por Rayos X
2.1. Introducción
Conceptualmente, se puede definir que la XRCT consiste en un método de tratamiento de imágenes generadas por la irradiación de rayos X o gamma sobre un objeto. Estas imágenes son procesadas mediante un algoritmo matemático para generar un volumen en 3D del objeto, otorgando la capacidad de realizar un minucioso estudio tanto de la geometría interna como de la externa del mismo, mediante la creación de secciones transversales virtuales sobre el objeto a estudio [5].
Por lo tanto, los principios que rigen esta tecnología pertenecen tanto al ámbito físico como al matemático. En primer lugar, los fundamentos físicos corresponden a los fenómenos de generación, propagación y atenuación de los rayos X. Por otro lado, los principios matemáticos hacen referencia al proceso de detección, digitalización y procesamiento de imágenes de rayos X, además de ser la base fundamental de los algoritmos de reconstrucción tomográfica. En la figura 3, se representa de forma esquemática el proceso de tomografía computarizada por rayos X según los principios que rigen cada operación.
![Figura 3. Representación esquemática del proceso de tomografía computarizada por rayos X [5] Figura 3. Representación esquemática del proceso de tomografía computarizada por rayos X [5]](https://img.interempresas.net/fotos/2154701.jpeg)
2.2. Antecedentes
Los inicios de esta técnica datan de 1895, cuando el físico alemán Wilhelm Conrad Rötgen descubrió los rayos X y realizó la primera radiografía humana (de la mano de su esposa). Posteriormente, en 1901 fue galardonado con el premio Nobel de Física por sus descubrimientos. En base a estos hallazgos, André Bocage patentó el primer método de tomografía convencional dos décadas más tarde [5].
La repercusión de esta tecnología en el ámbito sanitario ha sido indiscutible desde el principio, marcándose un punto de inflexión en 1969, con la construcción del primer escáner de tomografía computarizada para fines médicos. Sin embargo, su relevancia en el entorno industrial se ha percibido de forma exponencial, alcanzando su máxima trascendencia actualmente. A pesar de ello, cabe mencionar algunos hitos importantes, como pueden ser la primera aplicación industrial en la década de los 80 como método de ensayos no destructivos o el primer análisis cuantitativo en 3D con medición de volumen y distancias en 1990 (con precisiones menores de 0,1 mm) [6].
2.3. Campos de aplicación
La capacidad de inspección tanto de estructuras internas como externas que permite esta tecnología, prácticamente para cualquier material y geometría, le confiere un carácter diferenciador frente a otras técnicas. Este aporte de valor distintivo le postula como una de las opciones más prometedoras en una gran variedad de campos de aplicación.
Su utilización en campos como la medicina o biología es evidente dado su carácter no invasivo. Sin embargo, a nivel industrial también está presente en otro tipo de aplicaciones, como pueden ser:
- Caracterización de materiales
- Ensayos No Destructivos (END)
- Aplicaciones en metrología (centradas en alcanzar la máxima resolución y precisión posible)
- Inspección de composites
- Análisis multimodal
Por ende, su auge en multitud de aplicaciones de ingeniería inversa en detrimento de otras tecnologías se torna cada vez más palpable y consolidado.
2.4. Generalidades
Inicialmente, se considera conveniente discernir entre tomografía computarizada clínica e industrial. En primer lugar, la tomografía clínica presenta ciertas limitaciones ineludibles debido principalmente a las dosis y tiempos de exposición a los que se somete al paciente. Naturalmente, se deben procurar valores lo más bajos posibles, justificando la ventaja de su aplicación para fines de diagnóstico o planificación quirúrgica frente a los posibles perjuicios provenientes del mismo.
Asimismo, cabe destacar que, de forma generalizada, la configuración más habitual de este tipo de dispositivos es manteniendo fijo al paciente mientras el aparato rota a su alrededor a gran velocidad.
Estas circunstancias plantean un escenario en el que la precisión y la estabilidad se ven comprometidas, especialmente, en comparación con los equipos industriales, donde la intensidad de la fuente de rayos X y el tiempo de exposición se pueden incrementar considerablemente en busca de mejorar estas propiedades. Otro aspecto con influencia en estas características es la permanencia inmóvil de una pieza industrial durante su inspección, frente al movimiento del ser humano (respiración, pulso…).
Por tanto, en segunda instancia, en lo referente a los equipos del ámbito industrial, cabe destacar que su configuración de forma genérica es exactamente la opuesta a los sistemas clínicos. En esta ocasión será el objeto a inspeccionar el que realiza la rotación durante la inspección, mientras el conjunto del dispositivo permanece inmóvil, cumpliendo así las especificaciones de la industria de una forma más eficiente.
A continuación, en la figura 4 se muestra de forma visual el flujo de trabajo de un proceso de tomografía computarizada habitual, en este caso particular para una aplicación metrológica. Este diagrama está en concordancia con lo dispuesto en la guía alemana VDI/VDE 2630 parte 1.2 [7].
![Figura 4. Diagrama del proceso de aplicación de Tomografía Computarizada por rayos X en el ámbito industrial [8] Figura 4. Diagrama del proceso de aplicación de Tomografía Computarizada por rayos X en el ámbito industrial [8]](https://img.interempresas.net/fotos/2154703.jpeg)
Sin embargo, a pesar de la gran capacidad y prestaciones que ofrece esta tecnología, la componente tanto física como matemática inherente al proceso, en ciertas ocasiones, limita su trazabilidad. Algunos de los factores de mayor influencia son los expuestos en la figura 5.
![Figura 5. Esquema de los factores que influyen directamente en la incertidumbre de medida mediante CT [6] Figura 5. Esquema de los factores que influyen directamente en la incertidumbre de medida mediante CT [6]](https://img.interempresas.net/fotos/2154705.jpeg)
En vista del potencial expuesto de la tecnología y de sus inconvenientes, la comunidad científica está centrando sus esfuerzos en dar soluciones a estas cuestiones con el objetivo de aprovechar al máximo sus virtudes. Por consiguiente, el conocimiento generado de estas labores de investigación tiene una repercusión evidente en cualquier aplicación de ingeniería inversa en la cual este sistema sea considerado el más apropiado.
3. Revisión bibliográfica
Según lo dispuesto en los apartados anteriores, donde se manifiestan de forma evidente las posibilidades que plantea la tomografía computarizada como método de ingeniería inversa, se considera oportuno realizar una breve revisión bibliográfica de algunas de las labores de investigación realizadas hasta el momento en esta temática. Para esta revisión se han adoptado dos enfoques: sanitario e industrial (los dos sectores más predominantes en el empleo de esta tecnología).
3.1. Ámbito sanitario (biología y medicina)
En este ámbito, la aplicación de la tomografía computarizada como método de ingeniería inversa es incuestionable. A modo de resumen, se exponen algunos casos de investigación aplicando esta técnica:
- En [9] se presenta la primera aplicación de prototipado rápido en medicina forense empleando la técnica de tomografía computarizada como método de ingeniería inversa para la fabricación de un modelo de cráneo por el proceso de SLS (‘Selective Laser Sintering’).
- [10] desarrolla un nuevo método basado en tomografía computarizada en 3D para la evaluación postoperatoria de la artroplastia invertida de hombro, analizando el posicionamiento del implante y el volumen del tornillo en el hueso. Este nuevo método arroja resultados muy prometedores y ventajosos frente a los métodos 2D convencionales.
- Mediante tomografía computarizada se realiza un análisis de la articulación de la rodilla a medida del paciente, generando un modelo 3D para su estudio por elementos finitos en [11]. Además, se realiza una comparativa de la viabilidad del empleo de distintos materiales como prótesis de esta articulación, en función de sus propiedades mecánicas (con FEM) y de biocompatibilidad.
- En [12] se presenta una revisión bibliográfica muy interesante sobre la micro-tomografía computarizada por rayos X (microCT) en el campo del biomimetismo. Este tecnicismo se define como la imitación de los diseños y procesos de la naturaleza en la resolución de problemas técnicos. En el estudio se relaciona el potencial de esta tecnología en combinación con la fabricación aditiva tanto para soluciones de ingeniería inversa del ámbito sanitario como en aplicaciones industriales.
- Las posibilidades que brinda la combinación de la micro-tomografía computarizada (microCT) con la impresión 3D para la exploración y el estudio del proceso de desarrollo craneofacial, quedan expuestas en [13]. El desarrollo de este estudio de ingeniería inversa sobre la capsula nasal de un embrión de ratón ofrece una visión prometedora para la implementación de esta técnica en futuros estudios e investigaciones biológicas.
- [14] desarrolla un estudio sobre la influencia de los parámetros de tomografía computarizada (CT) en la calidad y precisión alcanzadas para la obtención de modelos de superficies complejas en 3D. Este método de ingeniería inversa, aplicado en este caso al peroné humano, confiere aptitudes suficientes para su consideración en otras aplicaciones como planificaciones quirúrgicas o análisis por elementos finitos (FEM).
- En [15] se muestra un estudio de modelización por elementos finitos de huesos de grandes dimensiones en base a la tomografía computarizada de estos. Para este caso específico, se han empleado huesos del tercer metacarpiano equino (MC3).
- Finalmente, [16] expone un estudio aplicando la técnica de tomografía computarizada como método de ingeniería inversa para analizar la fijación del tornillo pedicular en la columna cervical de la forma menos invasiva.
3.2. Ámbito industrial
El empleo de la tomografía computarizada a nivel industrial ha experimentado un crecimiento exponencial. A día de hoy, se postula como clara alternativa al empleo de sistemas convencionales, dadas sus capacidades. Sin embargo, los problemas inherentes a los principios que rigen esta tecnología relevan su candidatura para ciertas aplicaciones. Por esta razón, se puede apreciar una tendencia al alza en investigaciones en esta temática. De forma breve, se describen algunas labores de investigación realizadas en este ámbito de aplicación de la tomografía computarizada como método para ingeniería inversa:
- En primer lugar, cabe destacar la estrecha relación entre la tecnología de fabricación aditiva y la tomografía computarizada. La combinación de ambas tecnologías es frecuente y de gran utilidad, especialmente, para aplicaciones de ingeniería inversa tanto de ámbito sanitario como industrial. Dada su relevancia, en [17] se expone una revisión bibliográfica genérica sobre la combinación de ambas tecnologías.
- En [18] se resume de forma genérica un proceso de ingeniería inversa para el ámbito industrial, exponiendo las alternativas y metodologías que existen actualmente para cada etapa del proceso. Se insta, además, a realizar la selección más adecuada en función del propósito. También, cabe destacar el enfoque sugerido sobre el empleo de la tomografía computarizada para este fin.
- Un punto de partida interesante es el expuesto en [4], que a pesar de tratarse de un artículo de hace 20 años, expone los retos y el potencial que presentaba esta tecnología por aquel entonces. De esta manera, se sientan las bases de algunos de los avances desarrollados hasta el día de hoy y facilita el entendimiento de esta técnica.
- [19] presenta una metodología para replicar piezas a través de procesos de mecanizado basados en la información obtenida mediante tomografía computarizada. Este análisis de ingeniería inversa se completa realizando una comparación entre la pieza de partida y la duplicada con este sistema, identificando virtudes y defectos, así como factores potenciales de mejora.
- En [20] se plantea un estudio de ingeniería inversa para elementos con superficies de forma libre, como son los álabes de turbina de Inconel 718. En esta ocasión se combinan tanto técnicas de escaneado óptico como tomografía computarizada para comparar los resultados con máquinas de medición por coordenadas (CMM). Además, se realiza una estimación de la incertidumbre de cada técnica para analizar la trazabilidad de las mismas.
- Un caso similar es el expuesto en [21], donde se realiza un análisis de la precisión de un proceso de ingeniería inversa para álabes de turbina. En este estudio también se combinan ambas técnicas, tanto escaneado óptico como tomografía computarizada, para la generación de un modelo de réplica. Finalmente, se evalúa la precisión de dicho modelo generado por el proceso de SLM (‘Selective Laser Melting’), analizando el origen de las desviaciones, ya sean por el proceso de adquisición de datos o por el proceso de fabricación empleado.
- En [8] se presenta la capacidad cuantitativa de esta técnica en aplicaciones metrológicas, como puede ser una comparativa de la pieza fabricada con el CAD de referencia, para un análisis de desviaciones por ingeniería inversa. De esta manera, se pone de manifiesto la capacidad de la misma frente a los sistemas convencionales.
- Finalmente, con el propósito de visibilizar el amplio campo de aplicación de esta técnica, resulta interesante mencionar la idoneidad de la misma en labores de recuperación de piezas históricas. Un claro ejemplo es el expuesto en [22] y [23], donde la combinación de la tomografía computarizada, técnicas de diseño asistido por ordenador (CAD) y fabricación aditiva permiten recuperar estas piezas de las que se carece de información o se encuentran defectuosas.
4. Proyectos de investigación en el CFAA
El Centro de Fabricación Avanzada Aeronáutica (CFAA), dispone de una instalación de radiografía digital de GE modelo X-CUBE compact 225. Las especificaciones del equipo son las correspondientes a la Tabla 3, que se muestra a continuación:
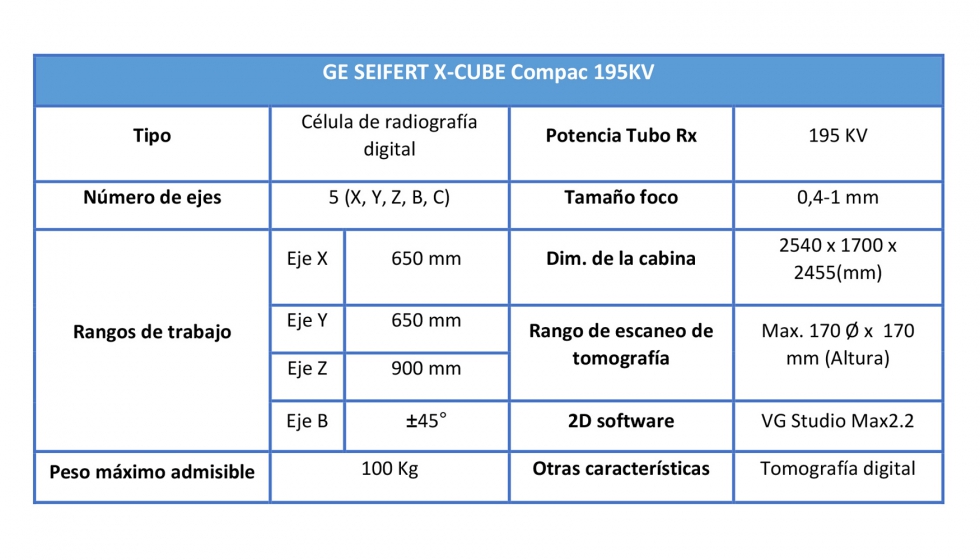
Los proyectos de I+D desarrollados en el CFAA se llevan a cabo en colaboración con los socios del centro que realizan actividades avanzadas de metrología dimensional e, incluso, que dan servicios en este ámbito. En el caso de uno de los ejemplos aquí mostrados, se ha establecido una colaboración con la empresa Trimek Metrology Engineering. Esta empresa es experta en el desarrollo de aplicaciones para la generación de ‘digital twins’ y ha llevado a cabo la digitalización por escaneado láser del componente fabricado por SLM y diseñado por Renishaw (también socio del CFAA) que aparece en las figuras 11 y 12. La generación de la superficie en STL se ha llevado a cabo empleando el software M3.
Para concluir, se realiza una breve exposición de los proyectos de investigación abiertos en el CFAA alineados con esta temática. El objetivo principal de estos estudios consiste en realizar un análisis de las mallas poligonizadas (STL) generadas por dos software distintos a partir de la inspección CT, además de un estudio adicional comparando ambas mallas con la generada por el proceso de escaneado láser mencionado para uno de los casos. Previsiblemente, la obtención de una malla poligonizada del objeto a estudio mediante técnicas de tomografía computarizada, permite la generación de un CAD a partir de la misma para su posterior fabricación por métodos convencionales o incluso su fabricación directa mediante técnicas de fabricación aditiva, concluyendo así un proceso de ingeniería inversa. Además, en caso de tratarse de análisis de procesos de fabricación, permite un estudio diligente del mismo para la implementación de acciones de corrección y mejora con gran precisión y agilidad.
De manera que, aplicando la técnica de ingeniería inversa mediante tomografía computarizada por rayos X, se presentan 3 análisis realizados a piezas de distintos sectores industriales.
4.1. Caso nº1
En este caso se analiza el proceso de ingeniería inversa aplicado a una pala de aspiradora, comparando las mallas poligonizadas (STL) obtenidas mediante distintos software (VGStudio Max2.2 y GOM Inspect 2019) a partir de la inspección CT. En la tabla 4 se exponen las especificaciones del material de la pieza a analizar y sus condiciones de inspección.
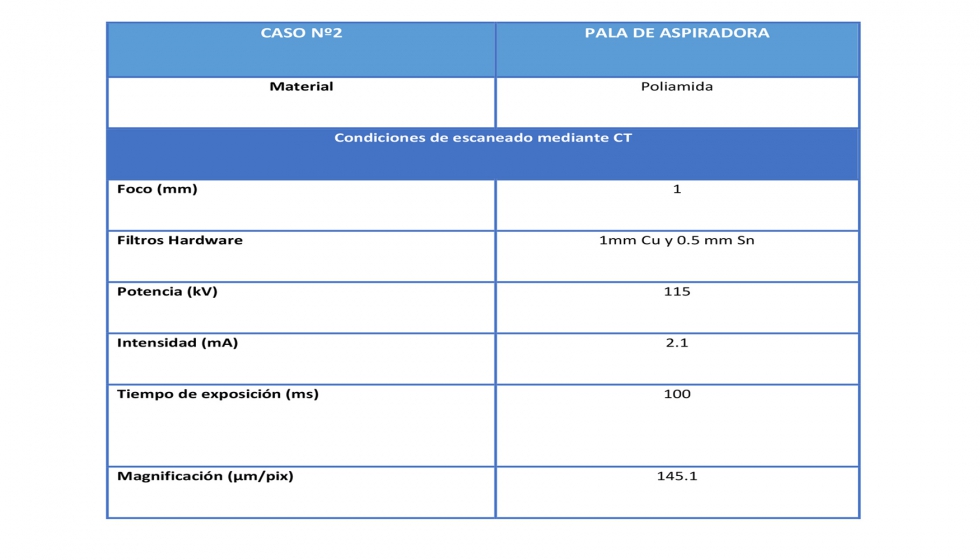
En el proceso de post-procesado de la información obtenida por CT para la creación de mallas poligonizadas (STL) se ha procurado, en ambos software, la generación de mallas de alta calidad y lo más precisas posible, obteniendo el mayor número de puntos admitido en cada una de ellas. En la figura 6 se muestra una comparativa de las mallas generadas automáticamente por cada software empleado.
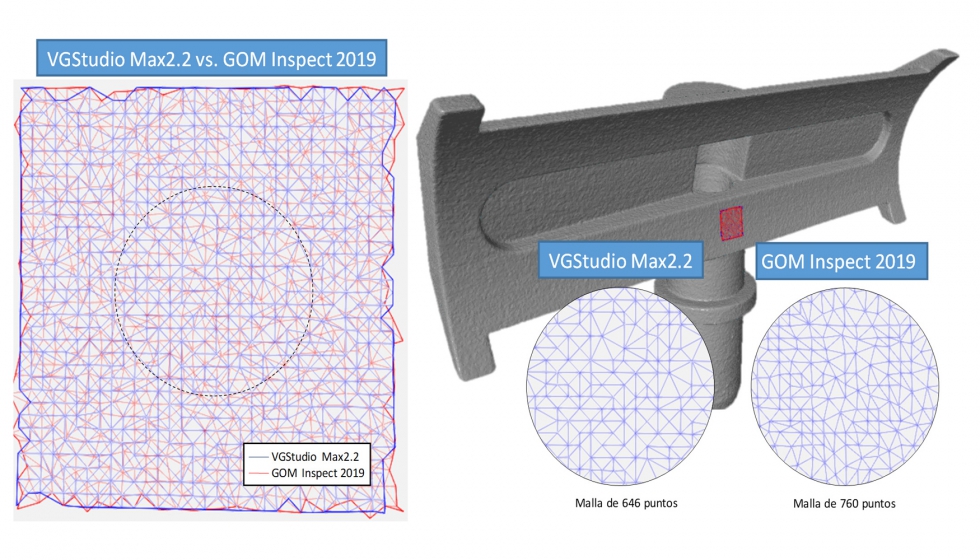
A priori, se puede apreciar que, en la región estudiada, el software GOM Inspect 2019 genera un mayor número de puntos para la construcción de la malla. Además, tanto los puntos como los elementos triángulos generados parecen seguir una disposición más aleatoria que en el software VGStudio Max2.2. Por tanto, la construcción de la malla mediante el software GOM Inspect 2019, procurará una malla de mayor precisión que la generada por el software VGStudio Max2.2. pero padecerá de un mayor coste computacional para su creación, además de presentar una mayor sensibilidad al ruido procedente de la inspección CT.
Esta mejora de la precisión directamente relacionada con el número de puntos empleado y los elementos de construcción de la malla, se define visualmente en la figura 7, donde se demuestra que, a mayor número de puntos, mayor capacidad de la malla para definir una geometría, especialmente, formas curvas.
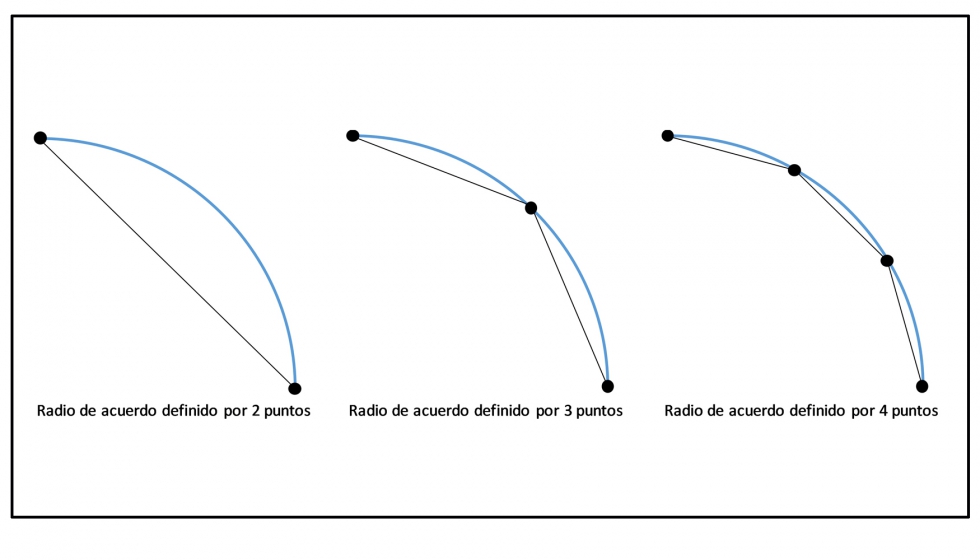
Sin embargo, en la definición de caras planas o formas rectas, el empleo de un mayor número de puntos puede resultar contraproducente, por la posible aparición de distorsiones y ruido en dichas geometrías. Por tanto, los métodos de construcción de dichas mallas representan un campo a estudio, dada la influencia de estos en la aplicación de un proceso de ingeniería inversa.
Con este propósito, se realiza un análisis comparativo de desviaciones entre las mallas poligonizadas (STL) generadas por cada software (VGStudio Max2.2 y GOM Inspect 2019) bajo las mismas condiciones de inspección CT, como se muestra en la figura 8.
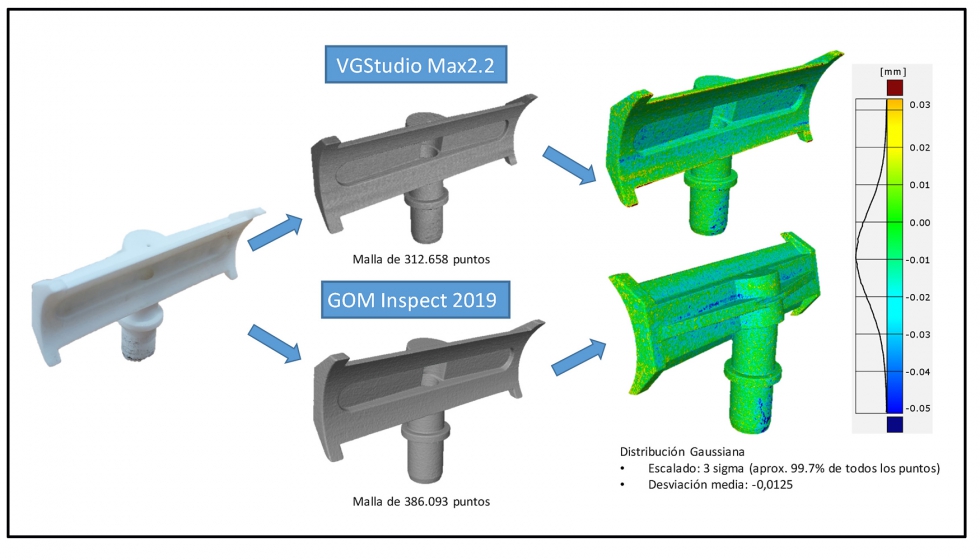
Al igual que en la región estudiada previamente, el conjunto de la malla generada por el software GOM Inspect 2019, presenta un aumento considerable en el número de puntos empleados para la construcción de la misma, en comparación con el software VGStudio Max2.2. Por otro lado, resulta interesante destacar que aproximadamente el 99,7% de todos los puntos se encuentran dentro de la escala 3 sigma expuesta gráficamente, es decir, en un intervalo de desviación entre los puntos de ambas mallas de -0,05 a 0,03 mm, con una mayor concentración en torno a la media. De este modo, se puede concluir que ambas mallas presentan resultados similares con desviaciones inferiores a las 50 micras prácticamente en la totalidad del conjunto.
4.2. Caso nº2
En este segundo caso, se lleva a cabo el mismo estudio que en el ejemplo anterior, pero para una pieza de mayor complejidad. Las condiciones de inspección y las especificaciones del material de la pieza a estudio quedan expuestas en la tabla 5.
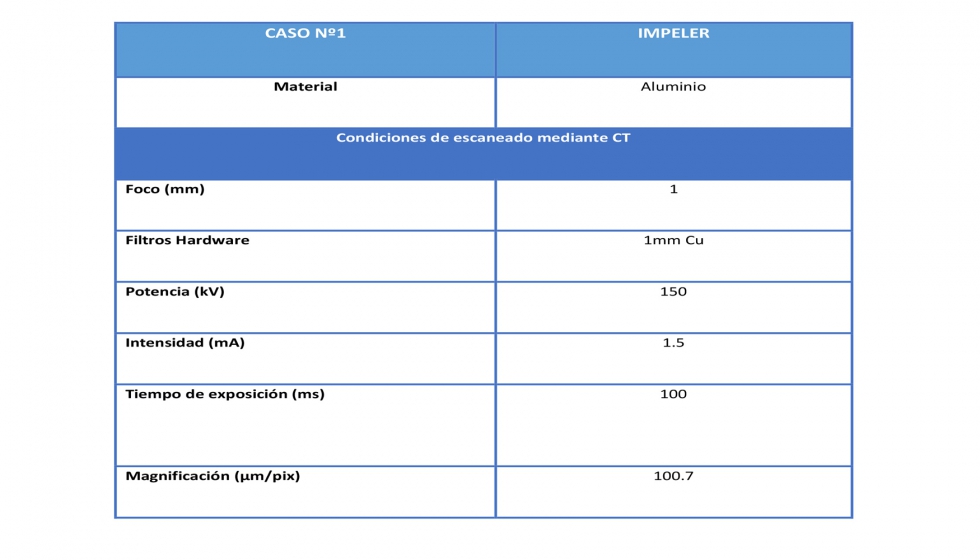
Para este caso también se ha procurado la generación de las mallas de la mayor calidad y precisión posible con cada software. Al igual que en el caso previo, el mallado con el software GOM Inspect 2019 emplea un número de puntos considerablemente superior al software competente estudiado, como se demuestra en la figura 9.
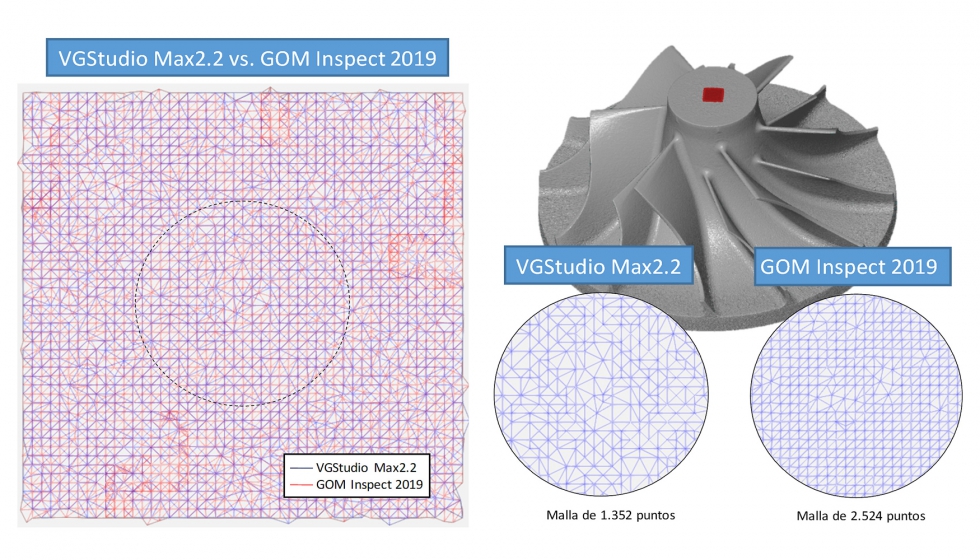
Finalmente, en la figura 10 se exponen los resultados de las desviaciones entre las mallas poligonizadas generadas con cada software. Resulta interesante destacar que una de las zonas donde se aprecian mayores desviaciones es la cara superior plana de la pieza, analizada en la figura anterior, donde el número de puntos de una de las mallas prácticamente doblaba el de la otra. Por tanto, esta desviación podría deberse a la mayor sensibilidad al ruido que presentan las mallas de mayor densidad. Sin embargo, el resto del conjunto de la pieza, a pesar de la complejidad de su geometría, presenta desviaciones concentradas en torno a la media y próximas al 0, aunque el intervalo, evidentemente, es superior a la pieza del caso anterior.
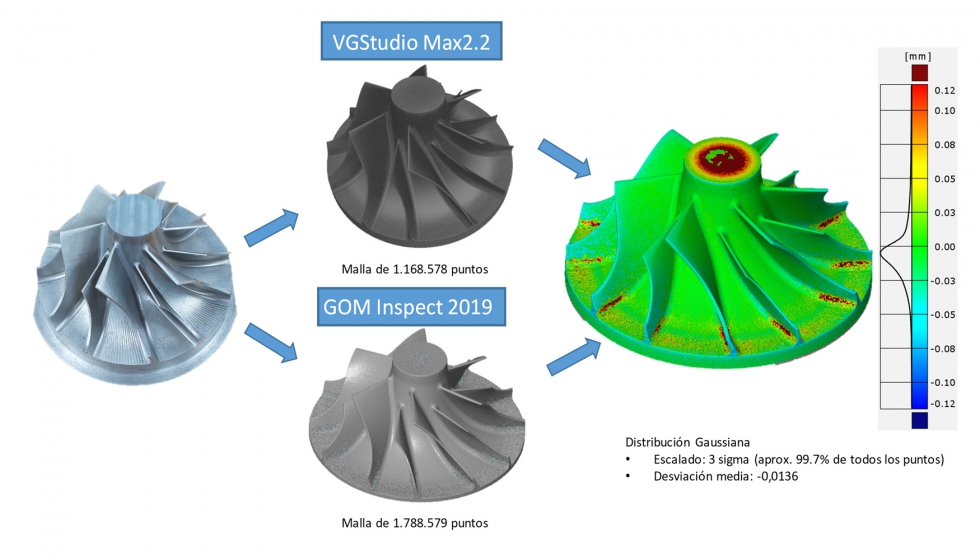
4.3. Caso nº3
En este último caso, además de realizar el mismo análisis que en los casos anteriores, se lleva a cabo un estudio adicional, comparando ambas mallas generadas por cada software a partir de la inspección CT, con la generada mediante escaneado láser por Trimek Metrology Engineering. En esta ocasión, tanto la geometría de la pieza como el material suponen un reto adicional, de ahí el interés por su análisis más exhaustivo. En la tabla 6 se exponen las especificaciones del material de la pieza de SLM y sus condiciones de inspección.
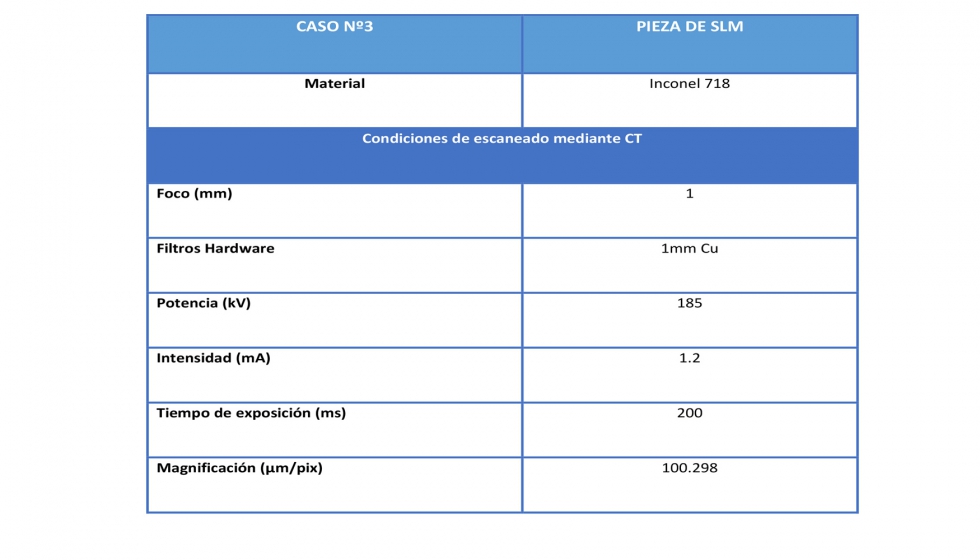
En la figura 11, se muestra la diferencia entre las mallas generadas con cada software a partir de la inspección CT, tanto la generada con VGStudio Max2.2 como la obtenida con GOM Inspect 2019. Como se puede apreciar, la diferencia entre el número de puntos y elementos empleado para la construcción de las mallas sigue la misma tendencia que en los casos anteriores.
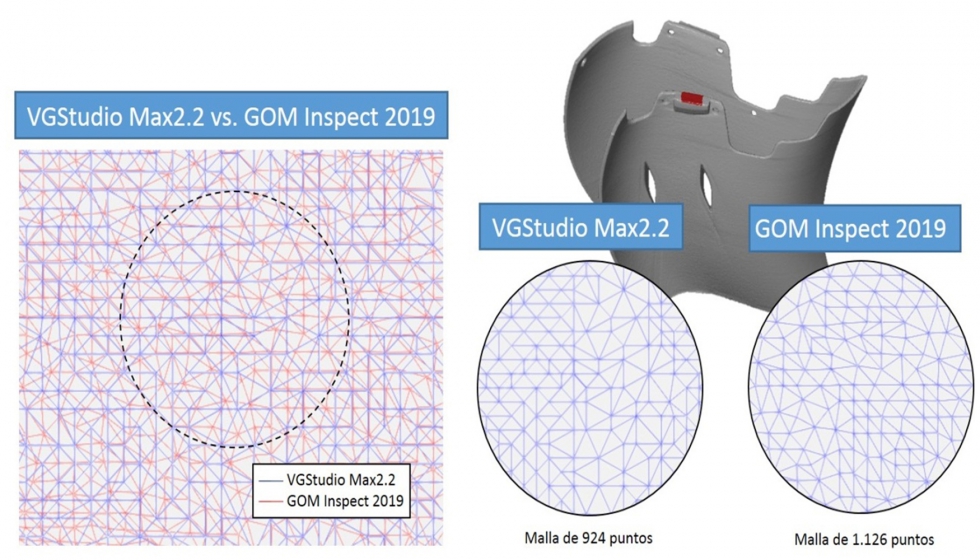
Para concluir, en la figura 12 se exponen las desviaciones obtenidas tanto entre las mallas generadas a partir de CT con los software estudiados, como las aparentes del estudio comparativo entre estas mismas y la obtenida mediante el escaneado láser.
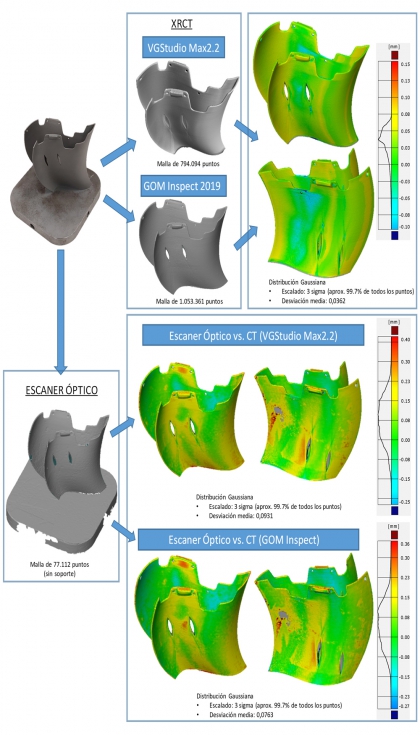
Como se puede apreciar, las desviaciones obtenidas entre ambos software para la inspección CT se encuentran dentro de un rango similar al del caso anterior, sin embargo, la concentración de desviaciones y la media se encuentran algo más alejadas del 0. Por otro lado, del estudio comparativo con la malla del escaneado láser, se advierten desviaciones mayores y con menores concentraciones, probablemente debidas a la menor calidad y precisión obtenidas con este último procedimiento.
De este modo, se puede concluir que la inspección por CT arroja resultados alentadores para su implantación en soluciones de ingeniería inversa, con capacidad para la obtención de mallas poligonizadas precisas y de calidad en función de los requerimientos de dicho componente.
5. Conclusiones
Bibliografía
[1] D.T. Pham and L.C. Hieu, ‘Reverse Engineering – Hardware and Software’, 2008.
[2] C. Rocchini, P. Cignoni, C. Montani, P. Pingi, and R. Scopigno, ‘A low cost 3D scanner based on structured light’, Comput. Graph. Forum, vol. 20, no. 3, pp. 299–308, 2001.
[3] A. Moreno and J. Campos, ‘Revisión de diferentes técnicas de metrología óptica’, Opt. Pura y Apl., vol. 40, no. 3, pp. 267–280, 2007.
[4] A. Flisch et al., ‘Industrial computed tomography in reverse engineering applications’, Comput. Tomogr. Image Process., pp. 45–53, 1999.
[5] W. D. (ed.. y R. L. (ed.. S. Carmignato (ed.), Industrial X-Ray Computed Tomography. 2018.
[6] N. Ortega, I. Cerrillo, and A. Fernández, ‘De la precisión, la repetibilidad y la realidad de la tomografía computarizada’, Interempresas - Automoción, pp. 1–21, 2017.
[7] VDI/VDE 2630 parte 1.2. 2018.
[8] H. Villarraga-Gómez, ‘Seeing is believing: X-ray Computed Tomography for Quality Control’, pp. 20–23, 2016.
[9] M. Kettner, P. Schmidt, S. Potente, F. Ramsthaler, and M. Schrodt, ‘Reverse engineering-rapid prototyping of the skull in forensic trauma analysis’, J. Forensic Sci., vol. 56, no. 4, pp. 1015–1017, 2011.
[10] G. Venne, M. Pickell, R. E. Ellis, and R. T. Bicknell, ‘Reliability of a novel 3-dimensional computed tomography method for reverse shoulder arthroplasty postoperative evaluation’, JSES Open Access, vol. 3, no. 3, pp. 168–173, 2019.
[11] A. Soni, Y. Kumar Modi, and S. Agrawal, ‘Computed tomography based 3D modeling and analysis of human knee joint’, Mater. Today Proc., vol. 5, no. 11, pp. 24194–24201, 2018.
[12] A. du Plessis and C. Broeckhoven, ‘Looking deep into nature: A review of micro-computed tomography in biomimicry’, Acta Biomater., vol. 85, pp. 27–40, 2019.
[13] M. Tesarová et al., ‘Use of micro computed-tomography and 3D printing for reverse engineering of mouse embryo nasal capsule’, J. Instrum., vol. 11, no. 3, 2016.
[14] N. Hayat and M. Ahmad, ‘The effects of computed tomography scanner parameters on the quality of the reverse triangular surface model of the fibula’, J. Brazilian Soc. Mech. Sci. Eng., vol. 38, no. 1, pp. 21–31, 2016.
[15] S. Mouloodi, H. Rahmanpanah, C. Burvill, and H. M. S. Davies, ‘Accuracy Quantification of the Reverse Engineering and High-Order Finite Element Analysis of Equine MC3 Forelimb’, J. Equine Vet. Sci., vol. 78, pp. 94–106, 2019.
[16] Z.-J. Zhou et al., ‘Morphometric measurement of the cervical spine for minimally invasive pedicle screw fixation using reverse engineering and three-dimensional reconstruction’, Int. J., no. April, pp. 211–215, 2006.
[17] A. Thompson, I. Maskery, and R. K. Leach, ‘X-ray computed tomography for additive manufacturing: A review’, Meas. Sci. Technol., vol. 27, no. 7, 2016.
[18] Greg Growth, ‘A How-To Guide to Reverse Engineering’, FOUNDRY Manag. Technol., pp. 17–19, 2019.
[19] J. Yu, R. Lynn, T. Tucker, C. Saldana, and T. Kurfess, ‘Model-free subtractive manufacturing from computed tomography data’, Manuf. Lett., vol. 13, pp. 44–47, 2017.
[20] A. Gameros, L. De Chiffre, H. R. Siller, J. Hiller, and G. Genta, ‘A reverse engineering methodology for nickel alloy turbine blades with internal features’, CIRP J. Manuf. Sci. Technol., vol. 9, pp. 116–124, 2015.
[21] F. Bauer, M. Schrapp, and J. Szijarto, ‘Accuracy analysis of a piece-to-piece reverse engineering workflow for a turbine foil based on multi-modal computed tomography and additive manufacturing’, Precis. Eng., vol. 60, no. June, pp. 63–75, 2019.
[22] S. D. Laycock et al., ‘Using a combination of micro-computed tomography, CAD and 3D printing techniques to reconstruct incomplete 19th-century cantonese chess pieces’, J. Comput. Cult. Herit., vol. 7, no. 4, pp. 2–7, 2015.
[23] F. Celentano, R. Dipasquale, E. Simoneau, N. May, Z. Shahbazi, and S. Shahbazmohamadi, ‘Reverse Engineering and Geometric Optimization for Resurrecting Antique Saxophone Sound Using Micro-Computed Tomography and Additive Manufacturing’, J. Comput. Inf. Sci. Eng., vol. 17, no. 3, pp. 1–6, 2017.