Láser “cladding”: novedosa técnica de aporte de material
I. Fundación Tekniker - CIC Margune01/06/2006
El láser “cladding” permite dar solución a los problemas de porosidad, distorsión térmica de la pieza tratada o dificultades en el procesado de zonas muy localizadas que suelen aparecen con otras técnicas de tratamiento superficial con aporte de material.
Es una tecnología con la que se empieza a trabajar en la década de los 70, surgiendo la primera aplicación industrial en 1981, por parte de la empresa Rolls-Royce, que utiliza este proceso para el endurecimiento de superficies de álabes de turbina. Desde entonces se ha seguido investigando en el desarrollo del proceso, apreciándose un claro aumento de publicaciones científicas desde el año 2000. En la actualidad, el láser “cladding” se puede utilizar como técnica de “rapid manufacturing” o fabricación por capas, proporcionando la capacidad de fabricar componentes complejos funcionales sin pasos intermedios o postratamientos.
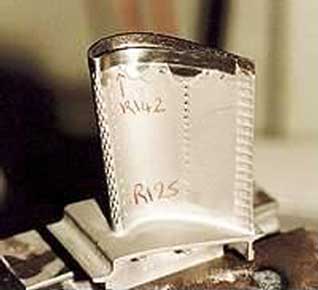
Figura 1: Álabe de turbina reparado mediante láser “cladding”
El láser “cladding” es un tratamiento superficial, que se engloba dentro del grupo de procesos termoquímicos donde se produce un aporte de material al material substrato. La aleación de la base y el material de aporte se produce en la zona central, de manera que cuanto más pequeña sea la zona, menor dilución existe. Con el proceso de láser cladding se consigue que el material aportado forme el recubrimiento, es decir, que la capa que se forma apenas contenga elementos del sustrato, con lo que mantiene las propiedades originales del material de aporte.
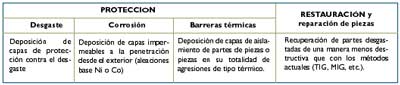
Aplicaciones
Los sectores aeronáuticos, de automoción y el del molde y matriz presentan muchas aplicaciones, como:
• Protección al desgaste o a la corrosión: válvulas de motor, álabes de turbina, ejes, etc.
• Reparación y restauración: moldes y matrices, engranajes, cuchillas de corte, cigüeñales, etc.
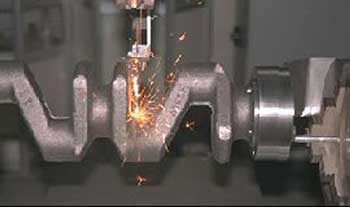
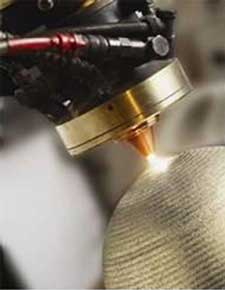
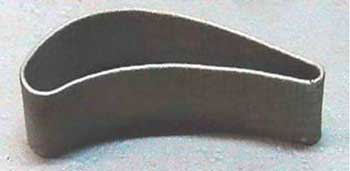
Equipamiento
El equipamiento completo, que se muestra en la figura 6, consta de:
• Un generador láser de estado sólido de Nd:YAG continuo bombeado por diodos de 2.200W de potencia de la empresa Rofin.
• Cabezal de aporte comercial YC50 de Precitec. Es un cabezal compacto y modular que se puede utilizar para llevar a cabo el proceso de “cladding”, y el de soldadura.
• Una fibra óptica de 600 ºm de diámetro para transporte del haz láser hasta el cabezal de Precitec.
• Robot de la empresa ABB con una capacidad de carga en pinza de 45 kg.
• Alimentador Twin 10C de la casa Sulzer Metco para la inyección, de manera precisa, de las partículas de polvo en el baño fundido.
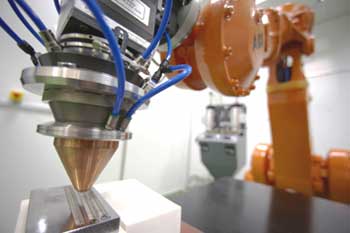
Estudio del proceso
El estudio científico del proceso que se está llevando a cabo pretende determinar los parámetros de proceso adecuados para la obtención de unos requisitos de salida concretos.
En la calidad del recubrimiento obtenido interviene el elevado número de parámetros de operación y muchos fenómenos físicos. La cantidad de parámetros de proceso a tener en cuenta es considerable, tal y como se muestra en la figura 4.
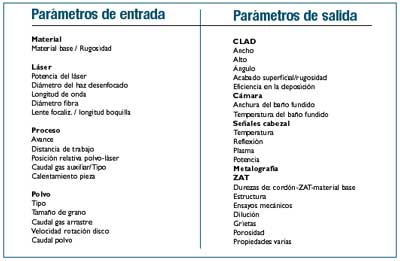
• Realizar un examen microscópico según las normas PE-1016-MT y PE-1005-MT, obteniendo una imagen que refleja el cordón obtenido.
- Comprobación de existencia de grietas y/o porosidades.
• Medir durezas según la norma UNE-EN ISO 6507-1:1998. Estas durezas HV 1 se miden en el cordón, en la zona afectada térmicamente (ZAT) y en el metal base sobre las probetas preparadas metalográficamente.
• Realizar la medición dimensional del cordón o clad (anchura, sobreespesor y penetración).
En la figura 9 se muestra una de las probetas tipo utilizadas para la experimentación, en las figuras 10 y 11 se pueden apreciar la sección de un clad unitario y de clads solapados.
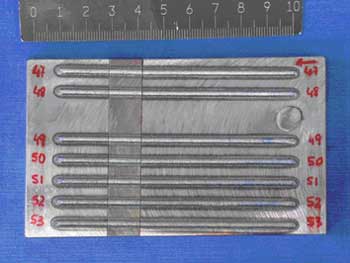
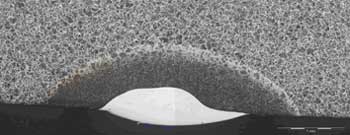
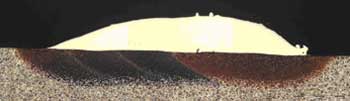
• Una buena unión del recubrimiento sobre el sustrato.
• Una baja dilución, es decir, que apenas se produzca una aleación entre el material base y el material de recubrimiento, preservando de esta manera las buenas pro• Pequeña ZAT (Zona Afectada Térmicamente). Una de las características del láser es que no produce grandes zonas que estén afectadas térmicamente, lo cual se traduce en una pequeña distorsión térmica.
• Que no se produzca formación de grietas en el material.
• Que no haya porosidad.
Con el objeto de controlar el proceso de una manera más precisa, se lleva a cabo su monitorización.
Por una parte, el uso de sensores específicos permite obtener señales de temperatura, potencia, plasma y reflexión del sistema. En la figura 11 se muestra la representación gráfica de dichas señales.
Por otra parte, se utiliza una cámara de visión externa, tal y como se muestra en la figura 12, como sensor de visión digital que sirve para analizar la imagen proveniente del proceso. La imagen capturada, que se genera dentro del espectro visible y está directamente relacionada con la temperatura a la que se está realizando el proceso, permite obtener de su posterior análisis el gradiente de temperaturas en la zona de fusión, y la temperatura del baño fundido en el centro y en sus alrededores.
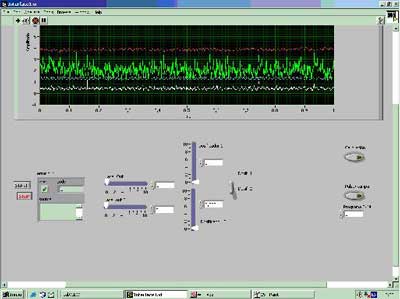
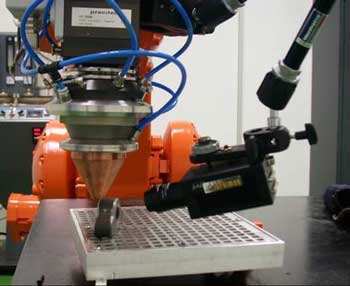
Ventajas
• Es un tratamiento localizado, es decir, se produce un bajo aporte de calor, con lo que el área afectada térmicamente es mínima.
• Se obtienen solidificaciones rápidas, es decir, se dan calentamientos y enfriamientos rápidos, formándose microestructuras finas y o fases meta estables.
• La energía total que da el láser no es muy grande reproduciendo una distorsión térmica mínima del substrato y mejorando con ello su calidad.
• La dilución en el material base es mínima, es decir, el porcentaje del sustrato que se encuentra en el recubrimiento obtenido es mínimo, por lo que no se alteran en absoluto las características del material aportado.
• Introduce una baja porosidad, es decir, se produce un relleno óptimo de material de aporte a nivel superficial.
• Conforma un amarre de tipo metalúrgico de gran calidad entre el material de aporte y el sustrato.
• Proporciona un buen acabado superficial, homogéneo y sin defectos.
• Se puede afirmar que es un proceso de alta precisión en las capas de material depositadas, tanto a nivel dimensional como a nivel metalúrgico y de precisión, que, por otra parte, son inherentes a las características del propio haz láser.
• Permite la fabricación “on-line” de diferentes composiciones.
La fuente de energía, se puede controlar de manera fácil y precisa.