Los menos convencionales
Este proceso de corte por hilo está basado en la utilización de un electrodo en forma de hilo o alambre que atraviesa la pieza y cuyo movimiento puede controlase de una forma muy precisa mediante un sistema de Control Numérico (ver figura 1).
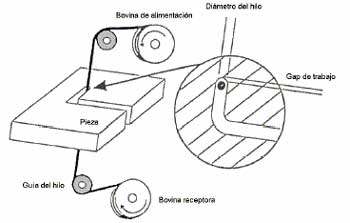
Según se recoge en Sommer [1], algunas de las ventajas de este proceso son que:
- Se puede mecanizar de forma muy precisa prácticamente cualquier tipo de contorno ya que, como no existe contacto entre el electrodo y la pieza, se elimina la posible distorsión mecánica.
- Se pueden mecanizar un elevado número de piezas a un coste menor con respecto a los procesos de mecanizado convencional, pudiéndose obtener precisiones dimensionales de hasta 0,0025 mm y rugosidades superficiales inferiores a una rugosidad media aritmética Ra = 0,037 mm.
- A menudo, se evita la posibilidad de procesos de mecanizado posteriores tales como el rectificado u otro tipo de procesos de acabado.
- Los materiales mecanizados mediante este proceso se encuentran libres de cualquier tipo de rebaba, siendo los bordes obtenidos en el proceso de corte perfectamente rectos.
- La dureza del material de la pieza no afecta a la capacidad de corte del proceso.
- No se necesitan introducir los valores exactos de la trayectoria del electrodo ya que ésta puede digitalizarse, sin existir la necesidad de programarla de forma manual.
- Las piezas se pueden mecanizar incluso al aire, aunque las velocidades de trabajo que se obtienen son, por supuesto, menores.
- El proceso de corte por hilo tiene un valor elevado de su repetibilidad. Esto es debido principalmente a que el electrodo de hilo se alimenta de manera constante durante el proceso a partir de un carrete. Además, debido a lo anterior, el desgaste del electrodo deja de ser un problema en comparación con el proceso de la electroerosión por penetración.
Otros tipos de procesos basados en la electroerosión que también son importantes, son el taladrado rápido de agujeros por electroerosión y el proceso de micromecanizado por electroerosión.
En el caso del taladrado rápido de agujeros por electroerosión se utiliza dicho término porque, aunque el proceso de electroerosión por penetración se puede usar también para el mecanizado de taladros, éste es mucho más lento que los equipos que son diseñados de forma específica para el taladrado por electroerosión. El taladrado por electroerosión usa los mismos principios que la electroerosión por penetración, ya que en este proceso se generan también una serie de chispas en el gap que se establece entre el electrodo y la pieza Kurafuji [2], Jeswani [3], Masuzawa [4] y Thompson [5].
El fluido dieléctrico realiza la función de evacuar de la zona del gap las diminutas y esféricas virutas erosionadas, además de proporcionar un medio aislante entre el electrodo y la pieza. Como fluido dieléctrico, se suele usar, generalmente, agua desionizada aunque también se recomienda la utilización de determinados aditivos. Para llevar a cabo el proceso, se usa una presión de limpieza en el dieléctrico que puede ser de hasta diez veces la que se utiliza para el caso de la electroerosión por penetración; además, en este proceso de taladrado dicho factor de la presión de limpieza es fundamental Durgan [6].
Los electrodos empleados son cilíndricos y huecos, y se encuentran en constante rotación durante el proceso de taladrado, mientras que el dieléctrico es succionado a través del interior del electrodo: Durgan [7].
Entre las desventajas del proceso de taladrado rápido por electroerosión se encuentra el gran desgaste que sufre el electrodo, la incapacidad de taladrar agujeros con diámetros menores de 3 mm, la pequeña velocidad del proceso para el caso de agujeros de gran tamaño y las dificultades de control del mismo en el caso de agujeros ciegos. Por otro lado, entre las ventajas se pueden citar la facilidad de taladrado para el caso de superficies curvadas o en ángulo, así como de agujeros profundos, la no formación de rebabas de mecanizado y el taladrado de agujeros perfectamente rectos, es decir, con pequeñas tolerancias de rectitud: Durgan [6] y Durgan [7].
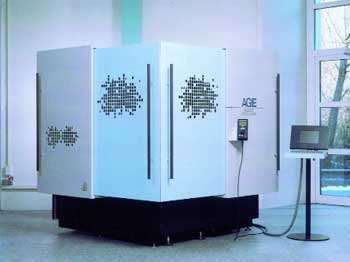
En el proceso de la microelectroerosión se suelen emplear generadores de intensidad de tipo relajación, ya que presenta diversas ventajas tales como que dichos generadores son de fabricación sencilla y duraderos, son precisos y adecuados para la utilización de frecuencias elevadas, poseen un bajo coste y un buen control de la cantidad de energía que se suele utilizar en este tipo de procesos.
Actualmente, algunas de las aplicaciones más interesantes del proceso de micromecanizado por electroerosión son el mecanizado de microcavidades con formas y geometrías complejas así como la fabricación de los microelectrodos para llevar a cabo el proceso: Uhlmann [12], Yu [13] y Allen [14]
Referencias bibliográficas
- Sommer, C., Non-Traditional Machining Handbook, Advance Publishing, Inc., 2000
- Kurafuji, H.; Suda K., Electrical Discharge Drilling of Glass–I, Annals of the CIRP, 1968.
- Jeswani, M.L., Small hole drilling in EDM, Machine Tools, Design & Research, 1979.
- Masuzawa, T.; Tsukamoto, J.; Fujino, M., Drilling of Deep Microholes by EDM, Annals of the CIRP, 1989.
- Thompson, R. B., EDM High-Speed Hole Drilling CNC and Special Applications, Electrical Discharge Machining Conference (Michigan), Septiembre 1991.
- Durgan, P. R., Fast EDM Drilling, Non-traditional Machining Conference (Florida), Octubre-Noviembre 1989.
- Durgan, P. R., High-Speed EDM Drilling, Electrical Discharge Machining Conference (Michigan), Septiembre 1991.
- Langen, H. H.; Masuzawa, T.; Fujino, M., Modular Method for Microparts Machining and Assembly with Self-Alignment, Annals of the CIRP, 1995.
- Yu, Z. Y.; Masuzawa, T.; Fujino, M., Micro-EDM for Three Dimensional Cavities - Development of Uniform Wear Method -, Annals of the CIRP, 1998.
- Rajurkar, K. P.; Yu, Z. Y., 3D Micro-EDM Using CAD/CAM, Annals of the CIRP, 2000.
- Li, H.; Masaki, T., Micro-Edm, Electrical Discharge Machining Conference (Michigan), Septiembre 1991.
- Uhlmann, E.; Spur, G.; Daus, N. A.; Doll, U., Application of m-Edm in the Machining of Micro Structured Forming Tools, International Machining and Grinding Conference (Ohio), Octubre 1999.
- Yu, Z.; Rajurkar, K. P., Generation of Complex Micro Cavities by Micro-EDM, NAMRC XXVIII Conference (Kentucky), Mayo 2000.
- Allen, D. M.; Almond, H. J. A.; Bhogal, J. S.; Green, A. E.; Logan, P. M.; Huang, X. X., Typical Metrology of Micro-Hole Arrays Made in Stainless Steel Foils by Two-Stage Micro-EDM, Annals of the CIRP, 1999.