El grupo Interbon presenta su nueva fábrica Unopan, con una producción de 350 m3 de tablero al día
2 de febrero de 2009
Unopan irrumpe en el mercado con notables ventajas competitivas: materia prima próxima, abundante y de alta calidad, un alto grado de automatización en planta (generará 200.000 metros cúbicos de tablero de fibra con 75 personas en plantilla) y la limpieza en seco de la astilla (gracias a la extraordinaria calidad de la madera).
Sobre una superficie de 20 hectáreas en el municipio burgalés de Salas de los Infantes (Burgos) se encuentra Unopan. El proyecto se inició hace tres años, con una inversión directa de 78 millones de euros, subvencionada en un 30 por ciento por la Junta de Castilla y León.
En julio de 2006 comenzaron las obras de explanación (hubo que mover medio millón de metros cúbicos de tierra), y en enero de 2007 la cimentación de los 24.000 metros cuadrados de naves cubiertas. El día 5 de junio de 2008, Día Internacional del Medioambiente, Unopan fabricaba su primer tablero.
La instalación ha sido concebida y diseñada para ser duplicada. Planta de energía, desfibrador, secadero, línea de producción, almacén… todas las áreas de la fábrica tienen anexo un espacio para multiplicar su capacidad por dos en el futuro.
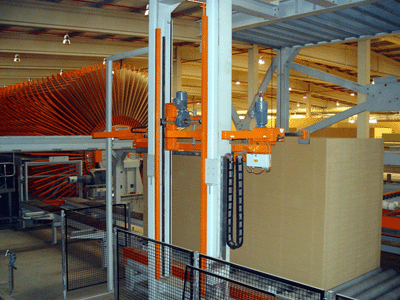
Automatización extrema
Una de las grandes ventajas competitivas de Unopan es su altísimo grado de automatización, logrado sobre la base de la experiencia de ingenieros propios de la compañía burgalesa: Andrés Medrano (director general) y cuatro técnicos de la casa, coordinados por el actual director de la planta, Carlos Navarro.
Línea de fabricación de tablero, línea de acabado y secadero son tecnología de Dieffenbacher. La planta de energía de Unopan, de la firma Intec, es la más grande de Castilla y León y genera 50 Megavatios térmicos sólo con biomasa. Y el corazón de Unopan, su desfibrador, es de la marca Andritz, responsable también de la maquinaria del parque de madera.
El desfibrador trabaja con un motor Siemens de 8.160 CV de potencia, equivalentes a 6 megavatios eléctricos. Aquí, una muela gira a 1.500 revoluciones por minuto contra la otra, que está fija, a sólo décimas de milímetro de distancia, generando 30 toneladas por hora de fibra en continuo a la cual se le va inyectando cola, parafina, endurecedor, urea y, en cada caso, colorante verde para el tablero hidrófugo o rojo para el ignífugo.
Hecha y tratada la fibra, es secada al 10 por ciento de humedad y limpiada en seco por densidad. Una vez acondicionada, el material básico del tablero de Unopan forma una ‘manta’ continua que será preprensada y prensada antes de adquirir el aspecto de un tablero. La prensa, que determina la capacidad de producción de la fábrica, mide 34 metros (ampliable hasta 42). Es la trayectoria necesaria para lograr que calor y presión hagan polimerizar la cola y obtener tablero en continuo.
Los tableros reposan en volteadores para enfriarse y curarse antes de ser apilados. A continuación, quedan entre uno o dos días en un almacén intermedio para estabilizarse. Allí aún podrían sufrir alguna retracción, con lo cual su escuadrado y calibrado final lo obtendrán en una línea de acabado que representa el final del proceso de fabricación del tablero.
Absolutamente todo el proceso se gobierna desde una oficina de control, desde los silos, la planta de energía, el desfibrador, la línea de producción, hasta los sistemas de detección de incendios. En ningún momento mano alguna ha tocado o manipulado el producto o sus materiales.
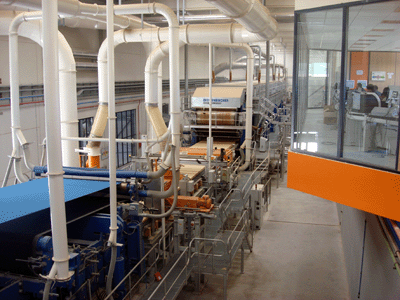
Unopan es capaz de producir 200.000 metros cúbicos de tablero de fibra MDF al año, de 3 a 40 milímetros de espesor, para lo cual necesita 400.000 metros cúbicos de madera. La planta funciona con madera de pino 100 por cien, “esto explica la decisión estratégica de ubicar aquí Unopan –explica su director, Carlos Navarro-, nuestro criterio es hacer un producto de la máxima calidad, y aquí tenemos la mejor materia prima, y muy cerca, lo cual es una ventaja competitiva”. En la Sierra de la Demanda existen más de 60 serrerías, su astilla y la madera delgada de pino procedente de primeras claras son los recursos básicos de Unopan (actualmente la planta consume un 70 por ciento de rollo y un 30 por ciento de astilla, aproximadamente).
La limpieza en seco de la astilla (gracias a la alta calidad de la materia prima), evita a Unopan tener que realizar el costoso proceso de depuración de aguas residuales, que podría suponer en torno a 600.000 euros anuales.
El Grupo Interbon es actualmente la compañía de aprovechamiento forestal más potente de la Región, cuenta con siete equipos mecanizados compuestos por procesadora y autocargador y dos manuales cortando madera para las 2 fábricas de tablero, en un radio de abastecimiento de 150 kilómetros.
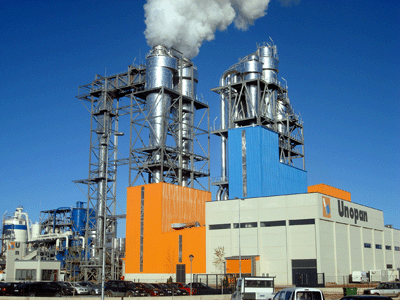
Una industria limpia
El único residuo de Unopan es la ceniza de la caldera, que incluso se reutiliza para generar tierras y compostaje para sellado de vertederos; un fertilizante pobre e inerte que resulta inofensivo para el medio ambiente.
La planta de energía de la fábrica no produce emisiones. Los gases que genera la caldera a 700º sirven para calentar más de 100.000 litros de aceite térmico por radiación y convección, tras ello son depurados en 12 multiciclones y mezclados con aire del exterior hasta bajar su temperatura a 200º, temperatura apta para secar la fibra en secadero.
Un ventilador de 1,6 MW impulsa más de 450.000 metros cúbicos de aire caliente junto con la fibra que sale del desfibrador. La fibra entra en el secadero y en 5 segundos se eleva por un tubo de 130 metros donde caerá por su propio peso, mientras que el agua de constitución de la fibra más la que se le ha inyectado en el proceso de desfibrado sale en forma de vapor por las chimeneas, a 55 metros de altura.
Unopan no amenaza la masa forestal de su entorno. Según el Tercer Inventario realizado en Castilla y León, la masa forestal crece 7,3 millones de metros cúbicos todos los años, y sólo se está cortando 1,5 cada año (el 20 por ciento de lo que ofrece el monte). La industria pide a la Administración (y ésta ha puesto en marcha una movilización de recursos) que saque más madera del monte, porque hay una capacidad de consumo para ello, y así no será preciso importarla de otras comunidades.
Interbon fue la primera fábrica de tablero de la Península Ibérica y la tercera empresa de la madera en certificar con el sello PEFC su cadena de custodia.
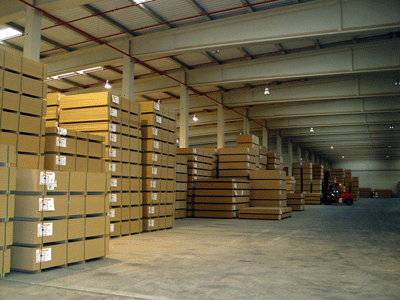
Interbon es un grupo industrial configurado por:
una fábrica de tablero aglomerado y revestimientos melamínicos (Burgos) y una fábrica de tableros de fibras (Salas de los Infantes, Burgos).
En el año 1965 comienza su producción como fabricante de tablero aglomerado. Desde sus comienzos ha centrado sus inversiones en innovación tecnológica para el desarrollo permanente de sus procesos productivos asegurando así, la incorporación de productos de valor añadido.