Descripción de los procesos de tratamiento de superficies
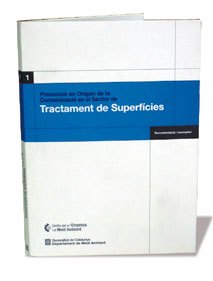
Además, la recionalización del consumo del agua, por ejemplo, y mejorar las operaciones internas, contribuyen a hacer una empresa más competitiva y reducir la generación de corrientes residuales.
Cualquier ciclo de preparamiento en el cual las piezas a tratar presentan restos de aceite como óxido, se debe eliminar mecánicamente estos contaminantes, antes de introducir las piezas directamente en la línea de proceso, ya que facilitará la eliminación más uniforme de los aceite y óxidos, posteriormente.
Decapado mecánico
Desengrase químico
En el desengrasado con disolventes, éstos son utilizados tanto en fase vapor como en frío. Eliminan las grasas, las pinturas y los barnices.
En fase vapor, se utilizan normalmente disolventes cloratos, los cuáles se evaporan en el baño para producir los vapores disolventes.
A continuación, se citarán los disolventes más utilizados actualmente para el desengrase:
- tricloroetano, tricloroetileno i percloroetileno,
- cloruro de metileno,
- triclorofluoretano,
- cloroformo, como en básicos.
En el caso de la utilización del desengrase con disolventes en frío, se utilizan los mismo compuestos, pero se aplican por inmersión.
En el desengrase químico con detergentes (comerciales), se consigue eliminar cualquier tipo de grasa gracias a la presencia de elementos tensoactivos que disminuyen la tensión superficial del baño y que se añaden a una solución alcalina. Se trata de un sistema muy empleado en Cataluña, por ejemplo.
En los medios alcalinos utilizados para desengrasar las piezas se pueden encontrar la siguiente formulación:
- sosa cáustica 40 g/l
- carbonato sódico 25 g/l
- fosfato trisódico 12·H2O 10 g/l
- metasilicato sódico 5·H2O 10 g/l
- humectantes 2-5 g/l
- complejantes metálicos variable
En este medio, las condiciones óptimas de trabajo son las siguientes:
- pH 12-14
- temperatura 60-90 ºC
Por otro lado, para favorecer el efecto mecánico de la limpieza, normalmente se utiliza algún mecanismo de agitación del medio, como el aire, por ejemplo.
2.1.4 Desengrase por ultrasonidos
2.1.5 Desengrase electrolítico
La formulación básica del medio es la siguiente:
- sosa cáustica 50-60 g/l
- fosfato trisódico 12·H2O 10-20 g/l
- gluconato sódico 10-30 g/l
En este casi, las condiciones de trabajo más frecuentes son los siguientes:
- pH 12-14
- temperatura 80 ºC
- densidad de corriente 5-10 A/dm2
2.1.6 Activado ácido/decapado
Entre los principales compuestos que se utilizan se pueden destacar:
- ácido clorhídrico,
- ácido sulfúrico,
- agentes inhibidores.
También se ha observado la utilización de dos ácidos mezclados, aunque algunos activadores especiales de metales utilizan el biofloruro amónico (F2HNH4) como una sustancia de activación. Después del decapeado, la superficie contiene productos químicos que se generen por la acción de los ácidos sobre los óxidos. A continuación, por tanto, se eliminan estos productos mediante su neutralización y posterior, limpieza con agua corriente.
2.2 Los principales procesos galvánicos
Según el material a recubrir y las características dinales que se pretenden del recubrimiento, se utilizan diferentes técnicas y materiales. A continuación se ven los principales procesos de tratamiento que se llevan a cabo en Cataluña.
En el caso de los recubrimiento electrolíticos, el mecanismo de recubrimiento consiste en sumergir la superficie a recubrir, limpiada previamente por alguno de los procedimientos citados anteriormente, en un electrolito adecuado, que posee los iones del metal a deposita; la pieza a recubrir constituye el cátodo de la cubeta electrolítica.
Por otro lado, el ánodo está formado por barras de gran pureza del metal de deposición, la misión del cual es mantener constante la concentración de los iones metálicos en el electrolito.
El grueso del recubrimiento se regula por variación de la intensidad de la corriente empleada y de los tiempos que dura el proceso. Hay que resaltar, también, la presencia de agentes diversos –humectantes, abrillantadores, complexants, etc…- que, en diversas funciones, forman también parte del baño.
Dentro del sector de la industria del acabado se superficies en Cataluña se pueden encontrar, principalmente, los procesos industriales que se describen a continuación, que, con diversas funciones, forman también parte del baño.
Zincado electrolítico y pasivación
Existen en la actualidad tres formas básicas de depositar el zenc por vía electrolítica:
- zinc ácido,
- zinc alcalino,
- zinc cianurado
- cloruro de zinc 62-85 g/l
- cloruro potasio 186-255 g/l
- ácido bórico 30-38 g/l
- humectantes 60-90 g/l
- abrillantadores 0,5-1 g/l
Las condiciones de trabajo en esta formulación son las siguientes:
- temperatura 21-35 ºC
- densidad de corriente 1-4 A/dm2
- tensión 1-18 V
- pH 4,8-5,4
Más utilizada que la anterior es la solución de zinc alcalina. En este caso, el zinc reacciona con los alcalinos dando zincados solubles, según la reacción siguiente, en la que también se libera hidrógeno:
Zn + 2(OH)– --> (ZnO2)2– + H2
En este caso, la formulación básica más común es la siguiente:
- óxido de zinc 9,5 g/l
- hidróxido sódico 90-120 g/l
- abrillantadores 10-50 ml/l
- temperatura 20-30 ºC
- densidad de corriente catódica 2-4 A/dm2
- voltaje 2-15 V
El ultimo tipo de zincado, cada vez menos utilizados que el zincado ácido y alcalino, es el de zincado cianurado, en forma alcalina, que se basa en la reacción siguiente:
Zn(CN)2 + 2 NaCN --> Na2Zn(CN)4
Las formulaciones básicas dependen fundamentalmente de la concentración de cianuro sódico variando de la siguiente manera:
En cuanto a las condiciones de trabajo, las más utilizadas son las siguientes:
- temperatura 20-30 ºC
- densidad de corriente catódica 2-6 A/dm2
- voltaje 2-15 V
Una vez se ha realizado el proceso de zincado de las piezas, para incrementar su resistencia a la corrosión, se les somete a un proceso de pasivación crómica o cromatizado. Esta pasivación puede ser de cuatro tipos:
- pasivación azul (resistencia a la corrosión baja),
- pasivación verde (alta resistencia a la corrosión),
- pasivación amarillo (resistencia a la corrosión similar a la anterior),
- pasivación negra (resistencia de tipo medio).
Hasta ahora se continua utilizando el cromo hexavalente en las formulaciones para la pasivación.
Subcapas y acabados
Este tipo de proceso es el que se denomina general.
El proceso de niquelaje se utiliza normalmente como una subcapa para tratar hierro, aluminio, latón, cobre, zinc y sus aleaciones.
En algunos casos particulares, las piezas son acabadas con un recubrimiento de níquel químico de características específicas (dureza, lubricación, etc…).
Dado que las reacciones que se producen en el niquelaje químico son catalíticas, es decir, las inicia el mismo material a recubrir, es muy importante en este tipo de recubrimiento conseguir una buena adherencia y por tanto, limpiar a fondo las piezas a tratar.
La formulación básica común es:
- sulfato de níquel 7·H2O 250-350 g/l
- cloruro de níquel 6·H2O 60-90 g/l
- ácido bórico 30-60 g/l
- abrillantadores 20-30 g/l
- humectantes 2-5 g/l
Con estas materias primas, las condiciones de trabajo requeridas son las siguientes:
- temperatura 50-65 ºC
- densidad de corriente 1-10 A/dm2
- pH 4-5
- tensión 1-16 V
La reacción general que tiene lugar para la deposición del níquel es la siguiente:
2 Ni2+ + (BH4)– + 4 OH– 2 Ni + (BO2)– + 2 H2O + 2 H2
Como ya se ha comentado, el niquelaje electrolítico se emplea en muchos casos como una base para favorecer la deposición de otro metal (cromo, principalmente).
Los baños de cromo estudiados, como las materias primas de uso más generalizado se pueden destacar:
- trióxido de cromo 150-400 g/l
- ácido sulfúrico 2,5-4 g/l
- catalizadores 0,5-1 g/l
Las condiciones de trabajo seguidas son:
- temperatura 40-50 ºC
- densidad de corriente 5-55 A/dm2
- ánodos insolubles 93% Pb, 7% Sn
El baño de cobre también es bastante utilizado dentro del sector. La formulación del baño es variada y se puede clasificar según:
- cobre alcalino cianurado,
- cobre alcalino sin cianuros,
- cobre ácido con ácidos sulfúricos,
- cobre ácido con ácido bórico.
Para el cobre alcalino cianurado, la composición es:
- cianuro de cobre 22,5 g/l
- cianuro sódico 34,0 g/l
- carbonato sódico 15,0 g/l
- hidróxido sódico control de pH
Respecto a las condiciones de trabajo, son estas a las condiciones de trabajo, son éstas:
- temperatura 32-43 ºC
- densidad de corriente. 10-15 A/dm2
- pH 12-12,6
- ánodos cobre y acero
Se utiliza para los grosores finos sobre todo tipo de metales de base y actúa como una capa de bases para nuevas capas de otros tipos de baño de cobre. Por este motivo, su aplicación está muy extendida.
Existe también una versión de alta concentración, que llega hasta los 120 g/l de cianuro de cobre y 135 g/l de cianuro sódico.
El baño de cobre alcalino sin cianuros tiene la composición siguiente:
- pirofosfato de cobre 345,0 g/l
- hidróxido potasio 18,0 g/l
- amonio (29%) 1 ml/l
Respecto a las condiciones de trabajo del baño, son éstas:
- temperatura 43-60 ºC
- pH 8,2-9,2
- densidad de corriente 1-7,5 A/dm2
- ánodos cobre
Es una subcapa para baños de níquel brillante y cromo. Se aplica sobre cualquier metal que presente una capa de cobre. También se utiliza en circuitos impresos.
Para el caso del cobre ácido como ácido sulfúrico, la composición del baño está formado por:
- sulfato de cobre 195-248 g/l
- ácido sulfúrico .................................................. 30-75 g/l
Respecto a las condiciones de trabajo son :
- temperatura 21-49 ºC
- densidad de corriente 2-10 A/dm2
- ánodos cobre
Es un baño aplicable sobre cualquier metal ferroso con base previa de cobre; también se puede utilizar como un recubrimiento bajo baños de níquel- cromo, para ofrecer más resistencia a la corrosión. Se utiliza mucho en la fabricación de circuitos impresos, ya que se consiguen capas muy final de recubrimiento, aunque también permite recubrimientos gruesos.
Respecto al baño de cobre ácido con ácido bórico, la composición es la siguiente:
- fluoborate de cobre 225,0 g/l
- ácido fluobórico control de pH
Condiciones de trabajo:
- pH 0,8-1,7
- temperatura 27-77 ºC
- densidad de corriente 7,5-12,5 A/dm2
- ánodos cobre
Se trata de un proceso que puede ofrecer cualquier tipo de grosor a las piezas de cualquier metal base que tenga una base de cobre. Utilizado también en la confección de circuitos impresos.
Otro tipo de recubrimiento que utiliza el níquel como base es el baño de latón. En este caso, la formulación más empleada es la siguiente:
- cianuro de cobre 60-75 g/l
- cianuro de zinc 8-30 g/l
- cianuro sódico 130-150 g/l
- sosa cáustica 3-4 g/l
- amoníaco 1-5 g/l
- abrillantadores 1-10 g/l
En este proceso, las condiciones de trabajo son :
- temperatura 40-60 ºC
- pH 9,5-11,5
- densidad de corriente 0,5-2 A/dm2
- ánodos Cu-Zn 80% Cu, 20% Zn
Otro baño que necesita un primer tratamiento con níquel es el de argent. La formulación en este proceso es:
- cianuro de plata 30-40 g/l
- cianuro potásico 160-200 g/l
- abrillantadores 0,1-10 g/l
y las condiciones de trabajo son:
- temperatura 22-30 ºC
- densidad de corriente 0,5-2 A/dm2
- ánodos plata(99,99%)
Finalmente, un último proceso muy común, que también necesita una primera capa de níquel es el baño de oro. En esta caso, la formulación empleada es la siguiente:
- cianuro doble de oro y potasio: 0,5-2 g/l
- fosfato disocio:10-20 g/l
- abrillantadores:1-5 g/l
Las condiciones de trabajo más utilizadas son:
- temperatura 50-70 ºC
- pH 11-12
- densidad de corriente 0,2-0,6 A/dm2
- ánodos titanio platinizado (inertes)
Dentro de este tipo de tratamientos generales, se debe mencionar el proceso de recubrimiento con estaño por baño electrolítico en el cual intervienen el estaño sódico, acetato sódico, sosa cáustica,
Perorado sódico y agua. La temperatura de trabajo es de 70 ºC.
Básicamente, se da el proceso porque el perborato sódico oxida el ión estanado a estánico.
Procesos de conversión de superficie
- fosfatación i pavonaje, en el caso del hierro y del acero,
- anodización del aluminio y sus aleaciones.
La fosfatación consiste en la formación de capas de fosfatos sobre la superficie del metal a tratar. Además de proteger contra la corrosión, este proceso facilita el trabajo mecánico de los metales tratados.
El proceso de fosfatación se consigue introduciendo la pieza a recubrir en una solución diluida de ácidos fosfórico, el cual reacciona con el hierro según la reacción:
Fe + 2 H3PO4 --> Fe(H2PO4)2 + H2
Por su parte, el pavonaje consiste, en esencia, en la oxidación de la superficie controlando el proceso de manera que se forme óxido férrico que, dada su compacidad, protege el hierro.
Esta oxidación se consigue de diversas maneras:
- electrolíticamente (oxidación anódica), con una solución de agua con hiposulfito;
- químicamente (oxidación alcalina), con hidróxido de sodio i nitrato sódico o potasio;
- químicamente también (baño de sales), con un baño formado por una mezcla de nitratos de sodio y potasio, a los cuáles se añade dióxido de manganeso.
Por otro lado, también existe el proceso de anodización del aluminio. La oxidación anódica del aluminio puede considerarse un proceso de pasivación acelerada mediante el paso de la corriente continua. En realidad, se trata de su oxidación por electrólisis haciendo actuar como un ánodo la pieza a tratar. Es una aplicación muy importante que, en la mayoría de los casos, sirve para la protección de piezas de aluminio destinadas a la construcción.
El mecanismo que tiene lugar es el siguiente: cuando la corriente eléeléctrica pasa a través del electrolito, donde las piezas del aluminio a oxidar hacen de ánodo, se forma una capa de óxido de aluminio (alúmina) que va creciendo poco a poco, hasta llegar a gruesos del orden de 25-60 micras.
En este caso, a diferencia de otros procesos, el tratamiento que se debe dar al aluminio es el siguiente:
- desengrasado químico,
- lavado,
- satinaje de aluminio (alcalino),
- lavado,
- decapaje ácido nítrico,
- lavado,
- anodizaje de ácido sulfúrico,
- lavado,
- coloración,
- lavado,
- sellado con agua caliente.
Para hacer el desengrasado químico, la formulación más empleada es la siguiente:
- carbonato sódico 40 g/l
- metasilicato sódico 20 g/l
- gluconato sódico 10 g/l
- fosfato disocio 20 g/l
- humectantes 1-5 g/l
Por otro lado, para hacer el proceso de satinaje del aluminio, la formulación básica es:
- sosa cáustica 50-60 g/l
- gluconato sódico 20-30 g/l
- humectantes 1-5 g/l
En el decapaje con ácido nítrico, la formulación es:
- ácido nítrico 500 ml
- agua 500 ml
La temperatura de trabajo en este caso es el ambiente.
En cuanto al proceso de anodización propiamente dicho, existen diferentes tipos de electrolitos que son utilizados en la oxidación anódica, aunque el más importante es el ácido sulfúrico a un 20% en peso.
- temperatura 21-23 ºC
- densidad de corriente anódica 0,5-1,5 A/dm2
Como el tratamiento anódico del aluminio, el ácido sulfúrico ataca la superficie disolviéndola parcialmente, cuando la concentración de aluminio en el medio llega a un valor concreto, se debe proceder a la dilución de electrolito.
En algún caso se debe proceder a la coloración del aluminio mediante la utilización de colorantes adecuados, tanto orgánicos como inorgánicos. La concentración de cada colorante depende de cada caso. También las condiciones de trabajo dependen de cada colorante en concreto, así como del grado de intensidad de absorción demandada.
Finalmente, en el proceso de sellado se utiliza agua destilada a 98ºC, para hidratar la capa de alúmina.
Parta acabar con el estudio de los procesos galvánicos realizados, se describe, a continuación, el proceso de electropulido.
Electropulido
La pieza actúa como un ánodo, en una cubeta que contiene ácidos concentrados calientes.
En este acaso, la composición del electrólito es la siguiente:
La pieza actúa como a ánode, en una cubeta que conté ácidos concentrados calientes.
- ácido fosfórico 90% (peso)
- ácido sulfúrico 10% (peso)
- glicerina 1% (peso)
Así, las condiciones de trabajo son éstas:
- temperatura 80-90 ºC
- tiempo 2-3 minutos
- densidad de la corriente anódica 10-50 A/dm2