Sistemas de medición integrados en máquina para procesos de rectificado
Estas señales se utilizan para cambiar los avances del proceso de rectificado y determinar cuando la pieza a alcanzado la dimensión programada interrumpiendo el avance de la muela y finalizando el proceso de rectificado. A este tipo de medición la denominaremos en-proceso.
Una vez finalizado el proceso de producción, en función de los procedimientos de calidad existentes, las piezas producidas se miden en equipos de medición externos para verificar que estas cumplen los requerimientos de precisión exigidos. Los parámetros que se suelen verificar son la redondez, cilindricidad, cono, rugosidad, etc. Estos equipos de medición emiten determinados informes de las mediciones realizadas. A este tipo de medición la denominaremos post-proceso.
Los fabricantes de CNC's actuales están apostando cada vez más por los denominados controles abiertos, los cuales básicamente aprovechan la arquitectura PC para permitir al usuario implementar funciones propias, poniendo a su alcance muchos recursos internos del control. Este tipo de arquitectura de CNC's posibilita el desarrollo de sistemas de medición integrados con el propio CNC que permiten incluir en la maquina la funcionalidad de medición en-proceso y post-proceso sin tener que recurrir a equipos externos.
Además existen ciertos procesos de rectificado cuya medición no puede ser satisfecha con la utilización de equipos comerciales y por lo tanto requieren del desarrollo de soluciones especificas a la medición. En este articulo se presentarán 2 desarrollos de medidores para procesos de rectificado que utilizarán la arquitectura de los controles abiertos para su implementación, concretamente un medidor multidiámetros y un medidor de puntas de álabe para proceso de rectificado de alta velocidad. Inicialmente se presentan las bases para la integración de sistemas de medición en las máquinas.
La integración de funciones para medición post-proces en la máquina hace que ésta también se convierta en una máquina de medición y, por lo tanto, además de las funciones de mecanizado propiamente dichas, tiene que soportar las funciones de medición tales como almacenamiento de resultados, generación de informes e impresiones, etc. Es fundamental dotar a estos sistemas de los sistemas de calibración que permitan una trazabilidad de las mediciones de acuerdo a los estándares nacionales e internacionales.
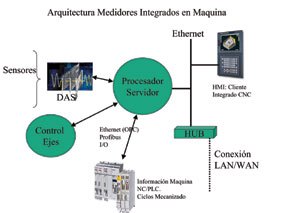
Arquitectura de un sistema de medición integrado
- Sensores: Son los encargados de convertir la magnitud física, en nuestro caso una dimensión, una magnitud eléctrica. En el caso del rectificado la técnica más utilizada es la de la medición dimensional por contacto (LVDT, encoder lineal), principalmente por su inmunidad en el operación con refrigerante. La medición por contacto presenta limitaciones para la operación a alta velocidad, por lo que se suelen utilizan sensores sin contacto (fibra óptica, triangulación láser, corrientes inducidas, capacitivos, etc.).
El interface más habitual de los sensores es la disposición de una señal analógica proporcional a la magnitud a medir. En algunos casos también se disponen de señales compatibles con encoders (TTL, 1VPP, etc.).
- DAS: (Data Acquisition System). Es un sistema que permite adquirir (digitalizar) la información proveniente de uno o más sensores. Los requerimientos del sistema de adquisición de datos varían en función del tipo de sensor utilizado y la respuesta en frecuencia necesaria.
- Control Ejes Posicionamiento: Los sensores tienen que ser posicionados en los puntos apropiados que les permitan capturar la información requerida. El medidor tiene que ser capaz de comandar los ejes de posicionamiento de los sensores. Los requerimientos de precisión de estos ejes son altos y se suelen utilizar sistemas de medición de mucha precisión ( <0,1 µm). El control de posicionamiento de estos ejes se puede integrar en el procesador del medidor o bien se puede comandar desde el CNC de la máquina.
- Procesador: es la unidad encargada de recoger y analizar la información de los diferentes sensores y de su procesamiento. Así mismo tiene que ser capaz de actuar sobre los procesos mecanizado. Para ello es necesario que este procesador disponga de canales de comunicación con el contralor de la máquina. Estos canales también son necesarios como canales de entrada de información, ya que el procesador no solo tiene que evaluar la información proveniente de los sensores, sino que necesita información del proceso de mecanizado que esta contenida en el CNC/PLC, como por ejemplo parámetros del proceso (rpm, avances, posiciones de los ejes, etc.), solicitudes de operaciones de medida, etc.
En función del grado de procesamiento requerido se puede optar por integrar el procesamiento en el procesador de la máquina (CNC abierto) o bien optar por un procesador independiente con comunicación con el CNC/PLC si se requiere mucha capacidad de cálculo y procesamiento.
Canales de Comunicación (interface) con la máquina (CNC/PLC).
Los interfaces de comunicación más utilizados con la máquina son los siguientes:
- Entradas/Salidas digitales: Son los más sencillos. Un conjunto de señales digitales permiten intercambiar información con otros dispositivos. Son los más utilizados en los medidores comerciales, pero limitan enormemente la cantidad de información a intercambiar.
- Buses de campo. La conexión del medidor al bus de campo del CNC/PLC es una posibilidad de intercambiar información entre el medidor y el controlador de la máquina. PROFIBUS es la más opción más aconsejable en este tipo de comunicación ya que esta soportada por 2 grandes fabricantes de CNC´S Siemens y Fanuc. Mediante este tipo de bus se accede a la información del PLC por lo que en caso de requerir información contenida en le CNC es necesario pasar dicha información al arrea del PLC.
- Ethernet. Cada vez es más habitual que los CNC disponga de este tipo de interfaces para intercambio de información con el CNC/PLC. Tanto Sienes como Fanuc disponen de esta posibilidad, y el desarrollo de librerías de comunicación permite el intercambio de información con la máquina. Utilizando este tipo de comunicación es posible acceder a prácticamente toda la información contenida en le controlador de la máquina (CNC/PLC). OPC (Ole Process Control) es una técnica de programación que se está imponiendo como intercambio de información con el CNC/PLC.
- En el caso de los medidores experimentados se ha optado por una combinación de Ethernet y I/O cableados. Las I/O cableadas se utilizan debido a requerimiento de rapidez de comunicación y seguridad cableada.
- HMI (Human Machine Interface): El entorno de manejo y programación tiene que estar integrado en el CNC. Para ello la solución adoptada ha sido la de software distribuido. Una arquitectura Servidor-Cliente posibilita que el cliente (HMI) solicite cualquier tipo de información y comandos al servidor (Procesador). Estas aplicaciones Servidor-Cliente pueden funcionar en un único procesador (PC) o en procesadores independiente. Una conexión en red local entre servidor y cliente facilita el intercambio de información. Este tipo de arquitectura facilita que los clientes se puedan ejecutar en cualquier PC conectado en red al servidor.
- Integración Redes del cliente: Mediante una conexión Ethernet se permite integrar el medidor en una red local (Lan Area Network) o red de área extensa (Word Area Network).Este tipo de conexión facilita que los resultados de las mediciones puedan ser almacenados y evaluadas en dispositivos (PCs) conectados a la red. La integración en una red de área extensa (WAN) es importante de cara al mantenimiento remoto facilitando el teleservicio.
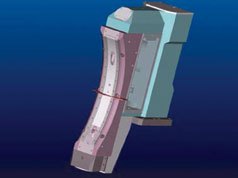
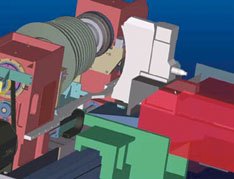
Medidor de puntas de álabes
Las rectificadoras de alta velocidad son el método utilizado actualmente y realizan este proceso a velocidades cercanas a la de operación del motor, realizándose la medición de los álabes en unas condiciones similares a las de vuelo (hasta 6000 RPM). Este es un factor muy importante, ya que los álabes no están fijos y por lo tanto la fuerza centrípeta originada durante la rotación del compresor a alta velocidad origina que estos están en condiciones similares a las de operación.
Es obvio que los medidores comerciales que utilizan la técnicas de medición por contacto no son apropiados para el trabajo con piezas discontinuas a alta velocidad. Por eso se ha desarrollado un sensor al cual denominaremos TOD (Transductor Optico Desplazamiento) para este tipo de medición y se ha desarrollado un medidor integrado en la rectificadora siguiendo la arquitectura descrita anteriormente.
El sistema diseñado dispone de la arquitectura que se muestra en la figura 3.2.
- Una cabeza de medición o sensor que contiene un TOD (transductor óptico de desplazamiento) de fabricación propia.
- Un/dos ejes que posicionan la cabeza de medición en el punto de medición.
- Un encoder incremental para leer la posición angular del rotor durante el rectificado y de esta forma sincronizar la medición de cada álabe.
- Un procesador para la adquisición y tratamientos de las señales generadas por la cabeza de medición. Este sistema proporciona todo el interface necesario con los controladores del proceso de rectificado.
Como se muestra en la figura el DAN-BTM se monta en la rectificadora, en oposición a la muela. A medida que el proceso de rectificado genera una variación en la dimensión de los álabes, el sistema de medición proporciona en tiempo real la medida de los álabes e interactúa con el controlador de la rectificadora.
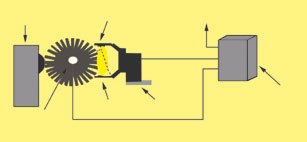
Usando este transductor óptico de desplazamiento, el modelo DAN-BTM determina el radio del álabe del compresor midiendo el arco del álabe mientras gira. Como se muestra en la figura 3.3, se coloca una fuente de luz colimada (diodo infrarrojos) en un lado, colocando un transductor óptico (cámara) en el lado opuesto. Una lente y un sistema de espejos captan la imagen de la punta del álabe y la proyectan sobre el fotocátodo del convertidor de imagen o tubo fotomultiplicador que es un transductor muy rápido con anchos de banda de 1MHZ. Mientras el álabe rota a través de la fuente de luz, se generara un flanco negro/blanco (o sombra) en el transductor. Midiendo la máxima longitud del flanco, representada por el pico del arco del álabe, se determina el radio. El TOD mide el radio de cada uno de los álabes, generando una señal analógica proporcional al desplazamiento del borde o radio del álabe (ver figura 3.4).
La señal analógica es analizada por un sistema de adquisición de datos, y mediante un procesamiento de dicha señal en combinación con la posición angular del rotor determinada con un encoder se calcula el radio de cada álabe.
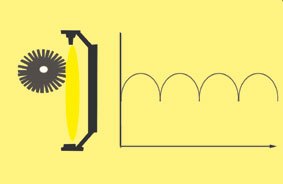
Sistema medición. Software adquisición y análisis
El medidor dispone de tratamiento de señal optimizado, con implementación de filtros para eliminación de ruidos eléctricos, análisis de 1 o varias vueltas con cálculos de la media o mediana de cada álabe y curvas de linealización de las señales. Los sistemas comerciales precedentes únicamente procesan la señal de una vuelta. La gran capacidad de calculo que dispone con un PC dedicado a la medición permite procesar información de varias vueltas, promediando resultados de cada uno de los álabes y eliminando las medidas erróneas. Las pruebas realizadas utilizando este algoritmo producidos mejores resultados de repetibilidad siendo más inmune a interferencias eléctricas en la señal a medir. Se han conseguido repetibilidades de < 0,003 mm frente a las 0,016 mm obtenidas sin la aplicación de los algoritmos optimizados.
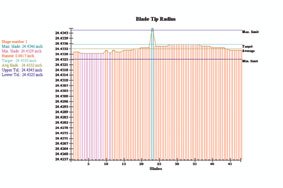
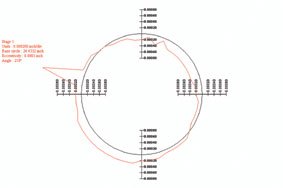
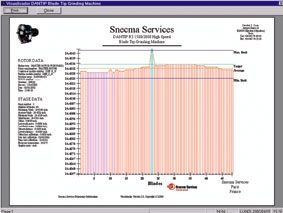
Medidor multidiámetros
Se trata de un Medidor Absoluto que permita la medición en proceso integrado con el CNC de la máquina. También se dispone de la posibilidad de realizar mediciones Post-Proceso de redondez, cilindricidad, cono y perfil, así como disponer de software de análisis de las mediciones realizadas.
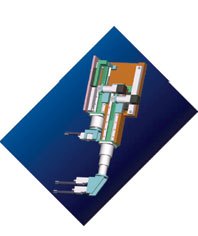
Los medidores comerciales disponen de rangos de medida limitados y no permiten medidor diámetros grandes. Con este tipo de medidor se puede medir cualquier diámetro entre 50-300 mm, y se pueden programar la medición de múltiples diámetros en la misma pieza.
La figura muestra el tipo de medidor. Dos brazos motorizados y controlados numéricamente por el medidor, posicionan unos palpadores de contacto en la zona de medición. Dependiendo del diámetro a medir el sistema de medida calcula la posición de los brazos, y procesa la información de los palpadores para obtener las dimensiones de la pieza.
La integración con el CNC permite al sistema de medida conocer en todo momento la posición de giro de la pieza y la posición de la mesa, obteniendo las formas y perfiles de las piezas.
La resolución del sistema es < 0,1 µm y la precisión de ±2µm en todo el rango de medida.
El manejo de medidor, la programación de los ciclos de medición, presentación de informes de medición esta totalmente integrada con el CNC de la máquina.
También se facilitan la impresión de informes, así cono la conexión en redes LAN, WAN para el almacenamiento de medidas o análisis de las mediciones en otros PCs conectados con el CNC.
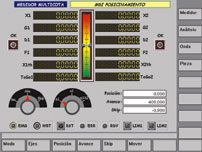
Conclusiones
El desarrollo de sistemas de medición integrados en las máquinas conlleva el dominio de ciertas tecnologías como son :
- Conocimiento de la máquina y los procesos de mecanizado.
- El conocimiento de los sensores y su aplicación. En la mayoría de los casos se podrán aplicar sensores comerciales, realizando la labor de la ingeniería de medición o procesamiento de las señales suministradas por los sensores y otros casos más complejos se requerirá el diseño del propio sensor.
- Conocimiento de procesamiento de señal.
- En conocimiento de la arquitectura de los CNC abiertos y las técnicas de programación.
- Comunicaciones industriales.
Los fabricantes de las máquinas además del dominio técnico en estas áreas, deberán evaluar el coste del desarrollo de sistemas de medición propietarios integrados en el CNC, frente a la utilización de sistemas comerciales. Una vez realizado el proyecto el coste unitario se reduce con lo que existen más posibilidades de incorporar nuevas prestaciones en las máquinas con un menor incremento de costes. El número de unidades a producir para amortizar el desarrollo del producto es fundamental a la hora de tomar decisiones de implementación.

Por otra parte la arquitectura servidor/clientes y los interfaces de comunicación de alta velocidad desarrollados permiten la total integración con el controlador del proceso de rectificado, incluso con la posibilidad de que ambos sistemas funcionen en el mismo procesador. Esto permite un intercambio de información en tiempo real entre proceso de mecanizado y medidor, pudiéndose adaptarse el proceso en función de la información suministrada por el medidor. Todo esto unido al desarrollo de interfaces de operador amigables y representaciones gráficas en un entorno Windows permiten disponer de un software actual y fácil de manejar, frente a los sistemas propietarios comerciales que cada cual utiliza interfaces diferentes.
Además de la verificación dimensional de las piezas producidas, se pueden integrar otro tipo de mediciones mediante la inclusión de nuevos sensores, como pueden ser:
- Calidad superficial de la pieza.
- Dureza del material.
- Detección de fisura y grietas.
- Caracterización de herramientas (muelas).
- Desequilibrio de muela, corte de aire (GAP).
Todos estas mediciones se integran en un mismo equipo sin necesidad de incorporar instrumentación y paneles de operador de diferentes fabricantes de equipos de medición. Todo ello facilita la labor del operario de la maquina disponiendo de un único entorno de manejo en un lenguaje amigable.
La aplicación de nuevas tecnologías en la miniaturización de sensores y la utilización de sensores sin hilos (wireless) con autogeneración de energía (self energised) acrecentará la posibilidades de la integración de medición en la máquina. n