La integración de equipos, básica en el empaquetado y en la línea de producción
1 de diciembre de 2011
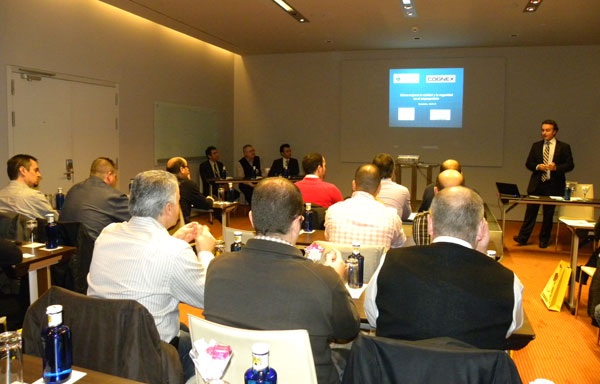
Bajo el título ‘Cómo mejorar la calidad y la seguridad en el empaquetado’, se celebró una jornada, el pasado día 30 de noviembre en el hotel W Barcelona, donde se dieron a conocer las últimas innovaciones técnicas en inspección, marcaje y pesaje de productos empaquetados. Cerca de 40 profesionales asistieron a la sesión que contó con demostraciones en directo de equipos pensados para optimizar la calidad y la seguridad del empaquetado farmacéutico, cosmético y alimentario.
¿Es posible inspeccionar, marcar y pesar productos empaquetados a gran velocidad y con las máximas garantías en cuanto a seguridad y trazabilidad? ¿Cómo se incrementa la eficiencia en la línea de producción reduciendo el porcentaje de paradas para cambiar un consumible determinado? Estas son algunas de las cuestiones que se abordaron durante la sesión, y a las que se trató de dar respuesta desde las empresas Domino, Gognex, InvesControl y OCS Checkweighers, organizadoras de estos encuentros técnicos.
Evitar el mayor número posible de paradas en la línea de producción
Manuel Hernández, jefe de productos y proyectos de la empresa Domino Amjet Ibérica, especializada en tecnología de marcaje y subsidiaria perteneciente a la multinacional inglesa del mismo nombre, dio el pistoletazo de salida a este seminario en el que la compañía dio a conocer los equipos de codificación diseñados para garantizar la trazabilidad en líneas de producción. En este sentido, la compañía ofrece codificadores primarios, secundarios (destinados a grupos de productos, presentados en packs o cajas) y terciarios o final de línea, por ejemplo para productos ya dispuestos en palés.
De entre las novedades de este año, Hernández destacó la impresora inkjet A320i, para codificación primaria, a la que calificó de “revolucionaria” en cuanto a su sistema de tintas. “Es un equipo ‘premium’ que incorpora tecnología inteligente como el sistema de tintas i-Tech y el Qube, un depósito que alberga las tintas y los filtros. ¿Qué tiene de revolucionario? Mediante esa inteligencia integrada, este equipo puede llegar a saber la fecha de caducidad de las tintas. Se trata pues, de una impresora pensada para producciones muy rápidas y constantes, de hasta dos y tres turnos de trabajo, 24 horas al día”. Esto es así porque según el jefe de producción de Domino, “cuanto más recircula la tinta, menos impurezas se producen con lo cual la expiración de la tinta es mayor”. En este caso, el cambio de consumibles es mínimo, no necesita servicio técnico para ello, ni para tareas de limpieza, filtros, etcétera. “No se requiere –continúa– parar la máquina durante dos o tres horas, tan solo se efectúa una parada ocasional, cuando se aproxima la fecha de caducidad, se extrae el Qube y se sustituye por uno nuevo. En ello, se emplean 10 minutos de reloj, con lo que se gana mucha eficiencia en la línea”.
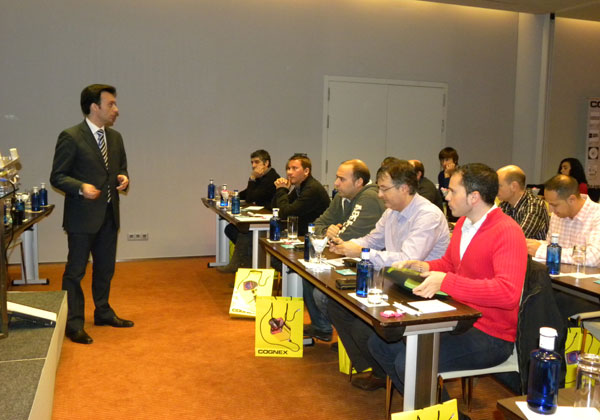
Por su parte, Toni Garcia, district sales manager de Cognex, aseguró que, en la actualidad, los 6.000 equipos de visión artificial instalados, inspeccionan cerca de dos millones de productos por segundo en todo el mundo. La visión artificial se utiliza, sobre todo, en inspecciones de producto, ya sea para comprobar que todas las piezas están bien orientadas dentro de la línea de producción, que reúnen las medidas y el tamaño correctos, en control de calidad… pero también en tareas de identificación, ya sea lectura de código de barras, OCR o Datamatrix. “En packaging, los equipos de visión se emplean para dos aplicaciones: trazabilidad de productos y procesos de control. En el primer caso, se trata de hacer un seguimiento del producto desde la unidad hasta el palé; en el segundo, que la conformidad del producto sea la correcta. Es decir, que se haya incluido el prospecto y lleve la etiqueta correcta, por ejemplo. Así se reducen los costes de mala fabricación y se protege la imagen del producto… estos serían algunos de los beneficios que se pueden obtener”, explicó.
Posteriormente, el representante de Cognex especificó 10 razones de porqué elegir un equipo de visión artificial en lugar de un lector de láser convencional. “El ratio de lectura es superior. Si se produce un fallo en la impresión, un sistema de visión sí puede reconstruir un código de barras, algo que el lector de láser no hace. Si tienes un código de barras con perspectiva, estos equipos pueden leer inclinaciones de hasta 90º. Además, pueden leer en packs o cajas donde no hay mucho contraste los equipos funcionan en cajas donde no hay mucho contraste”. Otra ventaja, según Toni Garcia de Cognex, es que los equipos de visión no tienen partes móviles, por lo que no se han de reparar, únicamente se reemplazan en un periodo no superior a las 48 horas. Asimismo, se puede visualizar en línea qué está pasando, ya que el sistema se conecta vía Ethernet al servidor de la planta, lo que permite establecer un ‘feed-back’ de cómo se imprime. Finalmente, y por si estos motivos no fueran suficientes, el ponente recordó que con estos equipos se pueden hacer lecturas Datamatrix, menor coste de impresión y mayor información, y que desbancará al código de barras actual, en su opinión.
“¿Para qué necesito una controladora de peso?”
A continuación, David Alujas, director comercial de OCS Checkweighers Ibérica, en nuestro país desde hace tres años y medio, centró su intervención en sistemas de pesaje, básicamente controladoras de peso en dinámico a las que definió como “la policía de la línea de producción”. “En cuanto al desarrollo de nuestros equipos, os puedo decir que cada mes producimos más o menos 110 controladoras y ninguna se parece a la otra, ya que hay diferentes requisitos de instalación. En este aspecto, somos una compañía muy flexible”, puntualizó. Durante su intervención, Alujas explicó qué aporta una controladora de peso en la línea de producción, a pesar que en teoría “no produce nada”. “Básicamente, por dos motivos. El primero, hacer números para saber cuánto me ahorro por paquete, minuto, y turno de trabajo, al año. Es decir, cuánto vale un gramo de mi producción; el segundo, garantizar mi imagen de marca. Se trata de ofrecer un producto estable, que siempre pese lo mismo”.
Además, el portavoz de OCS resaltó uno de los aspectos más importantes de estas pesadoras: su capacidad de integración en el resto de la línea de producción. Asegura pues, que estos equipos pueden interactuar con dosificadoras o transmitir datos a un software, en tiempo real, a fin de hacer cambios si se añade producto de más o se quita, durante su empaquetado. “La controladora de peso contribuye a la mejora del OEE (Overall Equipment Effectiveness o Eficiencia General de los Equipos). Éste es uno de los últimos elementos donde el paquete circula de forma individual. A partir de ahí, se hacen las agrupaciones. Es decir, los productos se colocan en fardos, cajas y palés”.
En este sentido, se pudo observar y comprobar in situ cómo trabaja la controladora de peso HC-A, desarrollada por OCS. Se trata de un equipo que trabaja, básicamente a velocidad alta, por lo que llega a pesar hasta 600 productos por minuto. Una aplicación que reúne, en un mismo módulo, lector de código de barras, cámara de visión y software de control. “Estos módulos suponen varias ventajas para los clientes. Por un lado, ocupan menos espacio, y por el otro, se compran los tres sistemas de una sola vez, en lugar de por separado. Asimismo, se controlan los tres sistemas a la vez, desde un mismo panel”. Entre sus principales características técnicas destaca la célula de pesaje con tecnología EMFR (principio electromagnético de compensación de fuerzas) que hace posible la determinación automática del tiempo de medición y el bastidor macizo de acero inoxidable que aporta una gran estabilidad y garantiza resultados de pesaje extremadamente precisos a altas velocidades de banda, eliminando por completo las vibraciones.
En alimentación, OCS Checkweighers Ibérica trabaja para empresas de congelados, loncheados, lácteos, fabricación de jamones, empanadillas y platos preparados.
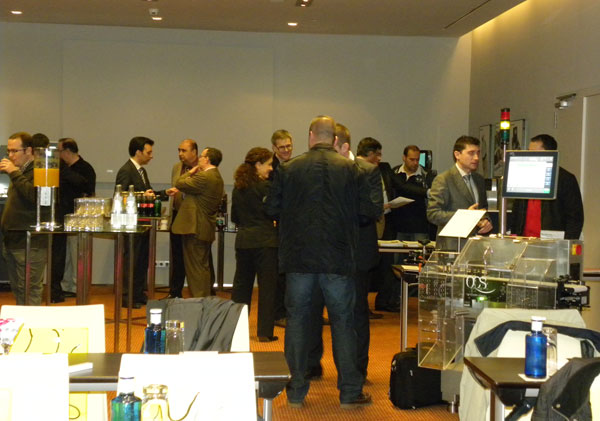
El broche final a la sesión lo puso Eduardo Ruiz, director de Invescontrol, empresa que proyecta, fabrica y comercializa sistemas de control para la industria del packaging, especialmente para los sectores farmacéutico, cosmético y alimentario. “Básicamente, nosotros aprovechamos las tecnologías que se han presentado en esta sesión y las unificamos”, resumió. En concreto, desde Invescontrol han diseñado un gestor de dispositivos, al que han bautizado como Invesnet, que se conecta a los mismos a través de unos drivers. Dispositivos que varían desde los sistemas de impresión a las cámaras de control y también las controladoras de peso. Un software flexible que, en su opinión, pretende unificar toda la información que se pueda obtener y también introducir datos desde un solo punto, lo que facilita el proceso. “Disponemos de productos específicos para las aplicaciones más usuales, desde el control de código de barras, control de códigos de impresión, sistemas de impresión, trazabilidad, control de blister y del etiquetado, por citar algunos”.
En concreto, y durante su exposición, recordó algunos de los equipos ‘estrella’ de la firma, como el CLB o Control de llenado en blíster, para así evitar roturas, efectuar controles de conformidad (color, dimensiones, integridad, forma, producto vagante, etc.) del producto, ya se presente en comprimido, cápsula o gelatina. O el CTE o Control total del etiquetado, que analiza la presencia, identificación, alineación y estética de la etiqueta, clave en productos “donde la estética es muy importante”. “Nuestra especialidad es conocer las tecnologías que nos proporciona el mercado, tanto en visión, impresión, peso y transporte así como los protocolos de comunicación que les permitan interactuar entre ellas. Así, podemos ofrecer una solución fácil de utilizar y, sobre todo, un servicio que las mantenga en funcionamiento el mayor tiempo posible”.
Básicamente, ¿cómo surgió la idea de organizar esta jornada conjunta sobre calidad y seguridad en empaquetado? ¿Fue difícil concretar y poner en marcha una sesión de este tipo?
Ya desde el principio, nos propusimos unificar varios conceptos en uno solo. Tratamos de reunir, en un solo evento, equipos de visión artificial, marcaje, inspección y ofrecer a los asistentes, además, soluciones de integración como nuestro módulo de transporte, donde se acopla la maquinaria que he mencionado antes. Con el sistema que presentamos aquí, que permite trabajar a velocidades de 400 o 500 productos por minuto, a la inspección de productos le añadimos el valor añadido del pesaje. Otra consideración a tener en cuenta es que, normalmente, se precisa mucho espacio para ubicar estos equipos, por lo que el hecho de adquirir un módulo donde se integran todos, permite reducir espacio y coste.
Precisamente, durante la jornada, se ha hecho hincapié en las prestaciones que aporta la integración de equipos de inspección, marcaje y pesaje en una misma línea de producción…
Sí, y quizás la ventaja principal sea el hecho de obtener datos de la producción desde un solo punto, lo que agiliza el proceso burocrático y facilita el manejo del sistema, que se efectúa desde un solo panel. Eso es lo que nos hemos propuesto transmitir, a lo largo del día de hoy, resaltando además el menor coste económico, clave en el contexto de crisis que atravesamos.
Además, durante las ponencias se ha insistido en la eficacia en áreas como control de calidad, seguridad y trazabilidad, pero eso sí, a través de equipos que ofrezcan una alta velocidad de trabajo. ¿Cómo casa una cosa con la otra?
Exactamente. Al final, lo que queremos es que la eficiencia en la línea y el OEE (Overall Equipment Effectiveness o Eficiencia General de los Equipos) sean lo más altos posible. Es decir, que la disponibilidad y el rendimiento en la línea no se conceptualicen como algo unitario, sino como conceptos que interactúen con los equipos de fabricación. Para que te hagas una idea, la gracia es disponer de sistemas de control que en sí mismos no producen –como sí lo hacen las máquinas de llenado, empaquetado, por citar algunas– pero que los primeros ejerzan una función de retroalimentación, que se comuniquen con estos equipos. Ello permitiría, por ejemplo, ajustar un cabezal de dosificación si la máquina llena de más o de menos los envases. No se trata únicamente de controlar, sino de interactuar con otras máquinas para, de manera automática, obtener la producción deseada. También se intenta, con estas soluciones integradas, reducir al mínimo e incluso eliminar los posibles fallos humanos que pudieran surgir.
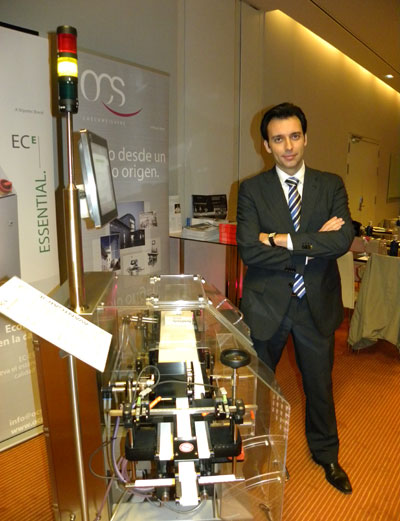