El mundo de la logística interna está en evolución continua al son que marca la evolución de la tecnología
2 de agosto de 2011
Esto, en esencia, no ha variado, aunque ahora para llevar a cabo sus proyectos cuentan con múltiples avances, desde programas de diseño que permiten concebir la instalación en tres dimensiones, pasando por materiales mejorados, mecanismos más sofisticados, nuevas tecnologías...
Pero indudablemente lo que sí ha variado es la importancia que se le otorga a la automatización en la logística. Durante años todos los esfuerzos se han centrado en mejorar los procesos productivos. Sólo recientemente se le ha empezado a prestar a la logística la atención que merece como fuente de importantes costes, y en muchas ocasiones innecesarios, que se pueden reducir significativamente gracias al uso de las nuevas tecnologías.
Fruto de la coyuntura económica y de la evolución del mercado europeo se observa un gran desarrollo del sector logístico, para dar respuesta a las necesidades de un mercado que se enfrenta a un aumento de las importaciones y que necesita aumentar su nivel de competitividad para hacer más atractivos sus productos. Por tanto el mercado está analizando sus procesos, identificando aquellos que aportan valor para sistematizarlos al máximo posible y aquellos que no lo aportan (coste) para minimizarlos y los que queden automatizarlos.
Así se vio la imperiosa necesidad de buscar una solución a tareas como el transporte entre estaciones de trabajo o procesos de ensamblaje, que no aporta un valor añadido al producto pero que por el contrario supone una importante carga de costes.
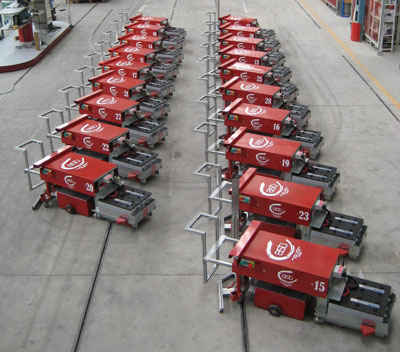
ASTI, como especialista en la producción de AGV (Vehículos de Guiado Automático), detectó el potencial que está tecnología tiene en el mundo industrial.
Hasta el desarrollo de los Easybots, los AGV de ASTI se concebían exclusivamente en base a una maquinaria convencional, dedicándose al trasporte puntual de cargas paletizadas.
La especialización en este tipo de soluciones hizo surgir la pregunta: por qué no utilizarlos para el transporte de otro tipo de cargas diseñando un chasis a medida. ¿Y si se utilizasen en tareas de ensamblaje, como medio para unir distintos procesos productivos?
Fue entonces cuando la materia gris de ASTI se puso en funcionamiento.
Uno de los objetivo que se marcó, fue intentar fabricarlos reduciendo los costes de producción al máximo, ya que las tareas para las que estaban concebidos no requerían de una gran sofisticación y no era necesaria la utilización de tecnologías de alto coste que garantizasen una precisión extrema.
El primer paso a realizar fue identificar los elementos que forman un AGV. Se identificaron cinco módulos base:
● Modulo mecánico: este módulo es el que determina la apariencia del vehículo y sus propiedades mecánicas, tales como capacidad de carga o velocidad a desarrollar. Así en función del modo en cómo se transporta la carga, diferenciamos a su vez tres tipos: tractores, tractores integrados y portadores.
Los tractores son aquellos vehículos que por medio de carros, transportan la carga a través del arrastre, por otro lado los tractores integrados son aquellos vehículos que adaptan su chasis para poder transportar un útil concreto que acaba formando parte del vehículo final.
Los portadores se caracterizan por realizar el transporte de la carga sobre el propio vehículo.
● Módulo de guiado: este módulo es el que determina el modo en el que el AGV va a seguir la ruta premarcada. Aquí se encuentran varios métodos de guiado aunque todos ellos caracterizados por la simplicidad de la que hablábamos al principio:
- Banda óptica: este sistema conlleva la instalación de una banda en el suelo para marcar la ruta a seguir y un identificador de la misma instalado en el vehículo y que sirve para que el vehículo se mueva a lo largo de dicha ruta.
- Banda magnética: este sistema consiste en la instalación de una banda magnética en el suelo para marcar el recorrido del AGV, y un lector en el vehículo. De esta forma, el lector detecta la banda y la sigue de manera automática.
- Banda pintada: al igual que en los otros dos métodos, se marca la ruta en el suelo, esta vez simplemente pintándola. El AGV lleva una cámara instalada, para la identificación de la banda, lo que le permite seguirla a lo largo del trayecto.
Dentro de este módulo, también se puede hablar de otro tipo de tecnologías que permiten marcar los puntos clave dentro de una ruta, tales como paradas o puntos de inflexión en el comportamiento del vehículo. Se trata de tags y spots magnéticos que, enterrados en puntos concretos del recorrido, hacen que el vehículo se detenga, varíe de velocidad o eleve la carga como ejemplo.
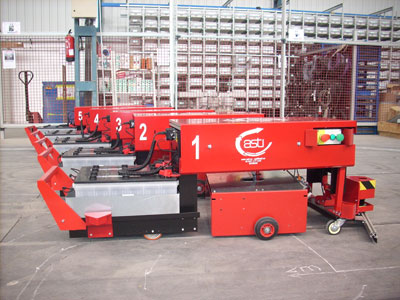
● Módulo de seguridad: como todo AGV, una parte fundamental del vehículo es poder garantizar la convivencia segura con personas, otros vehículos y en general el entorno que le rodea. Al AGV además de contar con botones de parada de emergencia, se le puede dotar de medidas como bumpers de detección y escáneres láser. Mientras los primeros son medidas mecánicas de detección e implican el contacto con los obstáculos para activar la parada, los segundos detectan el obstáculo haciendo que el vehículo reduzca su velocidad hasta parar totalmente al alcanzar una determinada distancia totalmente configurable, sin llegar en ningún momento a entrar en contacto con el obstáculo. La velocidad que desarrolla el vehículo será uno de los condicionantes principales para la elección o exclusión de estos sistemas, ya que si las velocidades son altas, el bumper no será suficiente para garantizar la seguridad.
● Módulo de alimentación: los AGV obtienen la energía necesaria para moverse a través de un sistema de baterías. Estas pueden ser de varios tipos: baterías de gel o baterías de ácido plomo. La decisión para instalar un tipo u otro dependerá de variables como el mantenimiento o las características de las instalaciones. Nuevamente nos encontramos con un aspecto importante como es la recarga de baterías, la cual se puede llevar a cabo de dos formas distintas, por medio de la sustitución manual de baterías o a través de un sistema de carga en caliente. En el primero de los casos las baterías agotadas han de intercambiarse por baterías completas y depositarlas en un cargador para proceder a su recarga. En el caso de la recarga en caliente, el AGV aprovecha los periodos de inactividad para aproximarse a los puntos habilitados para la recarga de baterías sin que el vehículo llegue a dejar de funcionar en ningún momento.
● Módulo de sistemas auxiliares: este módulo engloba varios sistemas que dotan de mayores funcionalidades a los vehículos.
Dentro de este módulo se incluye la posibilidad de definir rutas, que es de gran utilidad en plantas donde convergen más de una ruta, para diferenciar el camino correcto que cada AGV ha de seguir. Otra funcionalidad que incluye es la de la sincronización con las líneas de producción para acompasar los movimientos de los vehículos con las líneas y evitar tiempos muertos de espera.
Adicionalmente, a los AGV se les puede dotar de la capacidad de comunicación con los elementos en planta. De esta manera además de capturar datos del funcionamiento del centro productivo, son capaces de automatizar en mayor medida las operaciones, ya que una señal recibida de una máquina, será suficiente para que el vehículo inicie una operación programada.
Otro de los complementos que pueden incluir tiene que ver con el mantenimiento. El servicio de aviso vía SMS hace que en caso de avería el equipo de mantenimiento de la empresa reciba un SMS informándole de la parada del AGV. Relacionado con esto, destacar la capacidad con la que se les dota, para poder diagnosticar en remoto la causa de la parada y dar así respuesta inmediata para la resolución del problema.
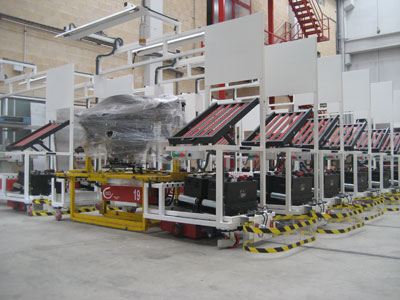
Prueba piloto
La oferta y posterior venta de un sistema basado en Easybots a una empresa del sector de la automoción sirvió a ASTI como experiencia piloto de desarrollo y funcionamiento. El proyecto comprendía hasta un total de 37 vehículos para la automatización de las líneas de ensamblaje de paragolpes, calderines y salpicaderos.
Se estudiaron las necesidades concretas de la compañía para diseñar el sistema que mejor se adaptase a estas y que mayores beneficios pudiese proporcionar. Desde el área de sistemas de transporte y manutención se diseñó un chasis que fuese lo suficientemente pequeño para moverse libremente por la fábrica, pero lo suficientemente grande como para albergar todos los componentes electrónicos y mecánicos imprescindibles para llevar a cabo su tarea y teniendo en cuenta que tenía que estar adaptado al útil usado en la empresa en el proceso de ensamblaje.
El área de AGVs, a su vez, se encargó de dotarles en general de la capacidad de funcionamiento automático. El resultado fueron 37 vehículos tractores integrados con el útil de transporte de la carga, que guiaban de manera óptica y que se movían entre los distintos puestos de ensamblaje de elementos para la fabricación de salpicaderos, paragolpes y calderines. Estas tres líneas a su vez se comunicaban con una línea de ensamblaje principal de camiones, sincronizando los ritmos de producción de los componentes con el producto final.
El funcionamiento es muy simple, un easybot transporta la pieza base a la que en los distintos puestos de trabajo se le van incorporando el resto de componentes, fomentando de esta forma la división del trabajo y la especialización en tareas sencillas y concretas. De esta manera el producto a ensamblar es el que va al encuentro del operario en lugar de hacer al operario ir en busca del producto, mejorando significativamente la ergonomía de su puesto de trabajo.