La velocidad es el factor determinante en la logística
18 de marzo de 2010
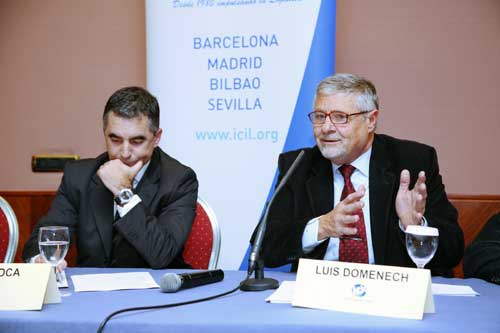
Este cambio no obedece a una maduración del concepto, ni a una tendencia de mercado, sino a una modificación tanto de las necesidades empresariales como del entorno de soluciones posibles, cada una de las cuales precisa apoyarse en una consolidación de las aplicadas en una situación anterior, lo que impide eliminar etapas e ir directamente a la solución correspondiente a las necesidades actuales. Además, la rapidez de la evolución experimentada ha provocado que el desfase entre las empresas líderes y las restantes se haya ampliado. Las compañías que deseen permanecer en el mercado tienen la necesidad urgente de realizar los cambios competitivos que las líderes han implantado.
Como consecuencia el primer reto logístico que tiene una empresa hoy consiste en aplicar la ‘velocidad’ a ‘actualizarse’. Es decir, situarse en la etapa en que la estructura de una logística integral responsable global del suministro y los stocks, con jerarquía sobre distribución física, planificación, producción y aprovisionamiento esté implantada, donde se valore el coste logístico y el stock global y no los costes y los stocks parciales. Esta actualización inicial supone también la aplicación de las reingenierías de Distribución Física y Producción:
- La Reingeniería de Distribución Física es el diseño de la misma adaptado para la atomización de pedidos, lo más centralizada posible, con stocks virtuales o de choque donde el tiempo de servicio lo requiera, con suministros directos desde origen, aplicando cross-dockings cuando exista más de un origen, eliminando la figura del almacén regulador y externalizando la ejecución hacia operadores logísticos.
- La Reingeniería de Producción es la externalización de todas las actividades que no constituyan el ‘Core Business’ de la empresa hacia proveedores con los que se establecido una relación de colaboración-integración, y el establecimiento de un criterio idóneo de flexibilidad que balancee correctamente los costes de producción con los stocks.
Estas condiciones, que podemos considerar como punto de partida, sitúan a una empresa orientada al cliente con muy poco o nulo capital invertido y por tanto con una elevadísima rentabilidad, lo que hace absolutamente desaconsejable la inversión en cualquier actividad no absolutamente necesaria, estimula las estrategias de renting y favorece todas las soluciones encaminadas a reducir o eliminar los stocks, con lo que el suministro y la producción JIT adquieren una importancia crucial y la filosofía de calidad total está fuertemente implementada. Una empresa que alcance estas características está al día y su logística ha alcanzado un alto nivel de consolidación pero frente a ella se abren hoy nuevos retos provocados por las nuevas circunstancias que concurren actualmente y que definiremos a continuación.
Cuando una empresa intenta por si sola afrontar estas circunstancias sus modelos de solución suelen ser los siguientes, todos ellos basados el la clave de ‘velocidad’:
- Aplicar el concepto de ‘agilidad’, es decir, intentar producir y suministrar contra pedido la demanda imprevista, pese al incremento de coste que ello suponga, forzando a sus proveedores a realizar entregas JIT con plazo de suministro inmediato.
- Si su estructura de producto lo permite, diseñar los modelos de forma que pueda fabricar contra stocks y previsiones las partes comunes a un gran número de modelos, con una producción eficaz en costes (Lean), y realizar el acabado contrapedido (Agile). La ventaja que presenta este método es que la previsión de venta agregada de las partes comunes tiene mucho menos error que el de la previsión de venta por tipo. Así para cubrir la demanda necesitamos mucho menos stock. Electrodomésticos, automóviles, ordenadores, etc. son ejemplos claros de esta nueva filosofía denominada ‘postponement’. Sin embargo, su aplicación se ha extendido a sectores donde hace poco se consideraba imposible. Así, en el mundo textil Benetton empezó tiñendo las prendas de punto después de confeccionadas, contrapedido, y en el mundo de la moda hoy Inditex repone a sus tiendas en 3 días los modelos y tallas realmente vendidos con una adaptación continua a las nuevas tendencias detectadas en base a acabar las prendas sobre la necesidad real en cada momento.
- Si el tiempo de respuesta ágil para fabricar o acabar contrapedido es excesivo para satisfacer en el plazo requerido la demanda, se emplaza un stock de choque en origen que cubra el desfase existente. Esto aparentemente permite adaptarse competitiva y satisfactoriamente a las circunstancias citadas anteriormente, pero cuando analizamos con una mayor profundidad el modelo descubrimos que no es así. En efecto, en una situación en que cada empresa actúa por separado todos los eslabones de la cadena de suministro tienden a cubrirse de las variaciones de demanda con stocks para poder suministrar JIT y desde los últimos distribuidores comerciales a los proveedores más primarios la cadena de suministro se llena de stocks, tanto mayores en cada eslabón cuanto menor es su agilidad, y esto tiene dos consecuencias fatales.
La primera se denomina ‘Efecto Forrester’, aunque recientemente los estadounidenses lo denominan ‘Bullwhip’, y consiste en que una pequeña variación de la demanda o inclusive la suposición de un posible incremento provocan impactos que se amplifican a lo largo de la cadena, provocando en sus orígenes grandes oscilaciones.
Las necesidades del cliente permanecen constantes, pero por cualquier razón su suministrador (A) prevé un incremento con lo que incrementa su producción ligeramente. En consecuencia, su stock de componentes suministrado por (B) disminuye y por tanto precisa reponerlo por lo que solicita a B no solo la reposición del stock consumido sino también y simultáneamente el incremento hasta el stock normativo correspondiente al nuevo nivel de producción, lo que provoca un incremento de impacto. Si el fenómeno lo repite cada eslabón las consecuencias son un incremento continuo. Obviamente al detectar que la demanda permanece constante A reducirá su producción a un nivel más bajo de la demanda para compensar el sobrante fabricado, detectará que el stock de suministro de B se incrementa, ya que B suministra a un nivel superior y ajustará su demanda no solo al nuevo nivel productivo sino a un nivel que absorba el exceso de stock con lo que el impacto generado será ahora en sentido contrario. En consecuencia, nos encontramos con grandes vaivenes en los eslabones medios y finales de la cadena que obligan a establecer stocks que actúen de amortiguadores del fenómeno.
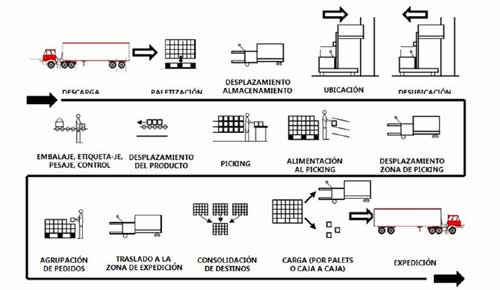
La segunda consecuencia consiste en que al estar la cadena llena de stock el tiempo necesario para lanzar un nuevo producto o modelo se alarga hasta que el stock existente se ha consumido a efectos de no asumir un enorme coste de obsolescencia. Esto es aunque técnicamente seamos capaces de realizar una introducción rápida no podremos efectuar la misma, hasta que nuestros proveedores y también nuestros clientes hayan ‘vaciado’ sus stocks. Una experiencia ejemplar la constituye Dell Computer que consiguió liderar el mercado de Estados Unidos al poder ofrecer 6 semanas antes que su competencia las novedades técnicas aparecidas, debido fundamentalmente a que las cadenas de suministro de IBM y Compaq precisaban este periodo para vaciar las existencias que estaban en poder de sus distribuidores y detallistas.
Como conclusión, el mayor reto logístico actual para las empresas consiste en aceptar que en solitario no podemos seguir progresando y que de una forma u otra debemos integrarnos con nuestros proveedores y con nuestros clientes para crear una cadena de valor que nos permita reaccionar con velocidad a la demanda de modelos y cantidades del mercado. Para llevar a la práctica esta política las empresas han adoptado lo que se ha denominado Collaboration Planning for Forecasting and Replenishment (CPFR).
Los grandes ‘gurús’ actuales pronostican que las empresas individuales ya no pueden competir y que para alcanzar el éxito es necesario generar una cadena que aporte la agilidad global necesaria, lo que constituye una cadena de valor. Esto provoca en la práctica que las relaciones comerciales de suministro dejen absolutamente de ser de oposición para superar la colaboración y alcanzar una integración donde proveedor y cliente están juntos en la misma cadena y por tanto comparten los éxitos y los fracasos de la misma. De esta forma, la selección de un proveedor se transforma en la selección de la mejor alianza para optimizar la cadena de valor. La logística empresarial obviamente experimenta de nuevo un gran cambio y los nuevos modelos se basan en conseguir la velocidad necesaria según los siguientes puntos:
- Eliminación del tiempo inútil, sin añadir valor de la cadena, lo que equivale a mejorar el tiempo de suministro, buscando nuevas formas de trabajar a lo largo de la misma que, en la mayoría de los casos responden a un ‘split’ ente el sistema ‘agile’ y el ‘lean’.
- Análisis de la previsión de la demanda y su transmisión a lo largo de la Cadena para evaluar las capacidades necesarias así como la determinación del error que contiene en los diversos niveles de agregación para poder determinar los stocks.
- Establecimiento y control de los canales de conectividad y transmisión real de información entre proveedores y clientes.
- Aplicación de CPFR.
En los casos más avanzados se ha evidenciado que la implantación efectiva de una cadena de valor precisa de un coordinador o máster que se responsabilice de su optimización y que actúe como el coordinador de los responsables logísticos de las empresas que la integran. Prepararse para poder desarrollar esta nueva función es sin duda un nuevo reto, en este caso no para las empresas, pero si para los profesionales que nos dedicamos a la logística.