Guzmán Polímeros, en Plast 2009
26 de febrero de 2009
Dentro del campo de las instalaciones centralizadas del sector de la extrusión, MainTech ha desarrollado una instalación especial para el estocaje, alimentación, dosificación, reciclaje y filtrado de poliestireno triturado, que puede crear grandes problemas de procesado.
La utilización optimizada de los descartes de producción para su reutilización, es hoy en día de una importancia estratégica dado el elevado coste de la materia prima virgen.
Por esta razón, el fabricante de sistemas auxiliares MainTech, proyecta especialmente silos con sistemas de extracción patentados, transporte neumático con densidad controlada, sistemas de control de vacío y con regulación automática del flujo de aire, silos de pequeñas dimensiones para gránulos ligeros, sistemas de carga del termoconformado con extracción mecánica, dosificadores colocados sobre la extrusora para mantener la producción requerida, etc. Con respecto a los materiales en lámina o ligeros se presenta la necesidad de desarrollos específicos como los descritos en este artículo.
“Algunas de las nuevas máquinas de MainTech fueron expuestas durante la última K, Fakuma y Equiplast, pero durante la próxima feria Plast de Milán se presentará la gama completa de transporte, dosificación y estocaje”, así lo indicó Renato Pegoraro, administrador de MainTech.
“Se trata de equipos sencillos, de bajo costo que exigen una tecnología particular para el procesamiento de los materiales. Además, es muy útil optimizar la recuperación de materiales para obtener un producto competitivo ya que los márgenes de venta son muy bajos y se necesita la máxima recuperación posible del material para mantener bajos los costes de producción”.
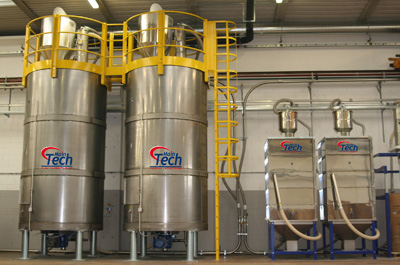
Estas líneas no trabajan sólo con materiales reciclados, y constituyen el 60% del total del material utilizado, constituido por: recortes de planchas procedentes del proceso de termoconformado físicamente situado más abajo y material triturado que el transformador adquiere a bajo precio. Todos los recortes son extremadamente ligeros y tienden a apelmazarse bloqueando el sistema de transporte y dosificación. Por ello ha sido necesario estudiar sistemas eficaces de extracción en correspondencia con los silos de almacenaje, los contenedores de recogida y con toda la instalación de transporte.
Todo ello teniendo en cuenta que la línea de extrusión alcanza un flujo igual a 1.500 kg/h y que, por consiguiente, es necesario almacenar, transportar y dosificar cerca de 750 kg de material a la hora.
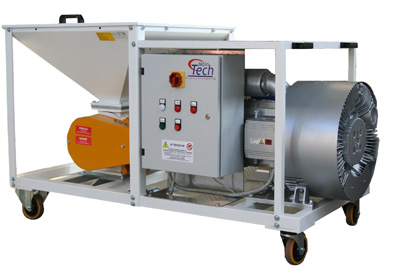
Almacenamiento y carga de los materiales
Dos silos externos para el almacenamiento de poliestireno virgen (de 55 metros cúbicos) para la línea de producción y dos silos internos (de 3.400 dm3) que contienen el poliestireno alto impacto. Un sistema de carga de los silos que permite hacerlo desde big bag o del clásico saco de granza o de cisterna.
Para el material recuperado difícil de tratar procedente de los restos del termoconformado, se almacena en dos silos grandes de 24 metros cúbicos. Éstos últimos están basados en una unidad definida como ‘sistema rotativo de extracción de recuperado’. En la práctica, en el interior del silo se ha instalado un sistema rotativo de gran dimensión que, en función de la llamada del sistema de aspiración (procedente de la línea del vacío), se acciona de acuerdo con un husillo, el cual dosifica el material en base a la propia densidad. Este sistema está constituido por un árbol central rodeado de dos hélices y de un cono central que dirige el material a la boca de extracción, donde está situado el husillo. Toda la instalación está gestionada por un PLC.
Los silos para el triturado se alimentan desde una estación especial para la descarga de este tipo de materiales; la estación está constituida por un sistema de extracción con husillo y un sistema de vibración que permite el transporte y dosificación del material.
Otro tipo de material procede de la línea de termoconformado, se recoge en big bags y, en primer lugar, atraviesa un gran triturador fabricado por MainTech. Está situado en una zona de la fábrica donde se ha centralizado toda la recogida de restos del proceso y descartes internos particularmente voluminosos. El molino se alimenta de forma automática y dos silos recogen el material triturado transportado por línea de vacío.
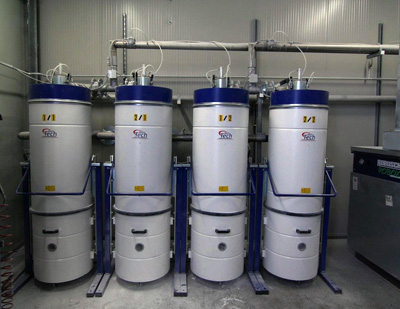
Alimentación y dosificación
Todos los materiales que salen de los distintos silos descritos anteriormente son transportados mediante un sistema de tuberías rígidas a la central de control manual donde se seleccionan los distintos materiales que van a ser incorporados a la unidad de dosificación gravimétrica colocada sobre la extrusora.
El dosificador gravimétrico es una unidad para cinco componentes que permite una capacidad de 1.500 kg/h y está programada para dosificar dos materiales recuperados (PS cristal y alto impacto), dos poliestirenos vírgenes y un colorante. Está colocada sobre una estructura correctamente dimensionada situada sobre la extrusora.
De la unidad de dosificación se pasa directamente a la tolva de alimentación forzada, necesaria debido a la ligereza del material en forma de escamas para mantener una alimentación correcta y continua de la extrusora.
Al final de la línea hay un molino pequeño que tritura los restos de la línea y se envían a un contenedor que mediante un husillo flexible alimenta directamente la extrusora.
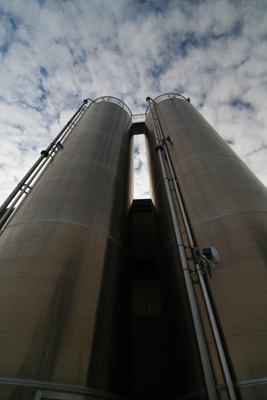
Sistema de carga mediante vacío
La carga de los materiales se realiza mediante una gran unidad de vacío. Una zona está dedicada a la bomba para la carga de los silos de almacenamiento de gránulos y de recuperado, con aspiraciones en varios puntos, y otra para la carga de la unidad de dosificación, contando con una tercera de reserva para sustituir de forma inmediata en caso de alguna anomalía.
Control de los sistemas auxiliares
Toda la instalación está gestionado con un control central con PLC ‘maestro’, dotada de una pantalla táctil a color donde se representan gráficamente todos los elementos de la instalación.
El PLC comunica con cada máquina a través de la línea serial de control denominada Touch Sys, desarrollada por Main Tech. Este sistema permite conocer todos los históricos de alarmas de la instalación y ver la intervención de los operarios. Control sobre el dosificador gravimétrico, el generador de vacío y el consumo de materiales, registrando el volumen presente en ese momento en los silos.
El sistema de control informático está utilizado por MainTech en todos y cada uno de las instalaciones que realiza y se ajusta en función de las exigencias de los clientes. Puede ser controlado por un PLC o por un ordenador en un punto o en varios puntos de la empresa conectado mediante un módulo telefónico.
Rapid presenta la gama completa de la serie 600
Rapid Granulator AB presenta la gama completa de la serie 600 con la incorporación de la máquina más grande con diseño ‘corazón abierto’, el modelo 600-150. Estas innovaciones de ahorro de tiempo y costes para inyectadores y procesadores tendrán un papel destacado en la presentación de la compañía.
También se muestran los equipos de la Serie 100 de Rapid, una línea completamente nueva de baja velocidad, molinos sin rejilla con detección de metales integrado, para aplicaciones a pie de máquina, diseñados específicamente para triturar materiales duros y quebradizos. El catálogo de estos equipos comprenden ocho modelos base; el más pequeño para manejar rechazos como coladas y restos de la producción de rodamientos y el de mayor tamaño capaz de triturar componentes muy grandes como parachoques y salpicaderos, por ejemplo. Todos los modelos están equipados con ‘acoplamiento suave’ para asegurar la absorción de la tensión operacional y prevenir daños en el motor y engranajes.
La serie 100 también se suministra con un sistema anti bloqueo, el cual no solo previene el bloqueo en la cámara de corte sino que permite que productos más gruesos puedan ser triturados.
Continuando el éxito de las series ‘corazón abierto’ 300, 400 y 500, se ha completado la gama de la serie 600 corazón abierto con diámetros de rotor de 600 mm y está disponible en 3 anchuras; 900, 1200 y 1500 mm, pudiendo alcanzar capacidades de hasta 2500 Kg/h. Además, la serie 600 puede equiparse con la cámara de corte súper tangencial de Rapid, que permite que la máquina pueda trabajar con piezas más grandes que indicadas para el diámetro de rotor actual.
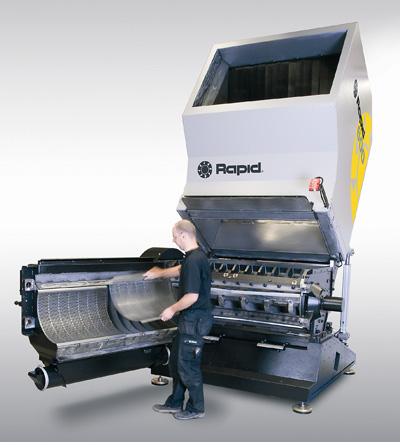
Los molinos ‘corazón abierto’ de Rapid están indicados para centrales de gran volumen o trituración a pie de máquina de piezas inyectadas, restos de soplado o extrusión, o rechazos para reciclado directo. Todos ellos utilizan la técnica de corte de Rapid, que comprende la acción de corte de doble tijera y el círculo constante de corte, para producir gránulos de tamaño uniforme con un mínimo contendido de polvo, incluso con los materiales más duros.
También se presenta el sistema Modular Silencing System (MSS) de Rapid. Debido a las cada vez mayores restricciones al ruido aplicadas al entorno de trabajo por las autoridades de regulación nacionales y europeas, el MSS ofrece a los transformadores y OEMs una innovadora solución para la reducción de ruido.
El MSS puede adaptarse virtualmente a cualquier configuración de máquina y reducir las emisiones de ruido entre 10 – 20 dB(A). Aunque concebido para su uso con molinos para plástico y sus sistemas de transporte, el MSS se puede aplicar en casi todo tipo de maquinaria que emita ruido reduciendo los niveles de ruido durante el funcionamiento y mejorando los regímenes de salud y seguridad en el trabajo.
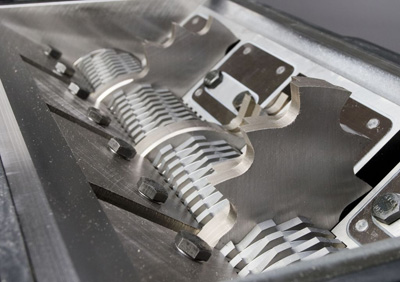