Fabricación eficiente de automóviles con tecnología RFID
Desde que se construye la carrocería hasta que se realiza el primer viaje en el vehículo nuevo, hay, ciertamente, un largo camino por recorrer. En muchas estaciones es necesario asegurarse de que el vehículo se esté fabricando exactamente como el cliente lo había pedido. En la ciudad alemana de Neckarsulm, Audi resuelve esta tarea con una solución de identificación basada en RFID que cubre todas las tareas de su planta. En la línea de producción del modelo sucesor del Audi A8, presentado en 2017, se usan dispositivos de lectura y escritura RFID (UHF) que identifican con fiabilidad etiquetas pasivas RFID en los vehículos en cada paso del proceso de producción.
Identificación con la máxima disponibilidad…
“Cuando planificamos una nueva línea de producción, naturalmente también tenemos en cuenta la cuestión de cómo se pueden identificar las piezas de trabajo en las distintas estaciones”, afirma Jan-Erik Butt, responsable de tecnología RFID de Audi en Neckarsulm. “Lo que realmente deseábamos era encontrar una solución de identificación que cubriera todas las tareas de la planta, desde las del taller de carrocerías hasta las del taller de pintura y las del área de montaje final. La resistente tecnología RFID resulta particularmente idónea para esta tarea, ya que ofrece múltiples posibilidades de conexión y una gran flexibilidad a la hora de integrarse en el sistema de producción”.
Finalmente, para comparar el rendimiento de los diferentes proveedores, Audi realizó pruebas durante toda una semana en el taller de pintura, lugar en el que la etiqueta RFID del vehículo se somete a la máxima solicitación. “En estas pruebas, Sick nos ha convencido por su fiabilidad. Requerimos una disponibilidad del 100%. En la industria del automóvil no nos conformamos con el 90%”, destaca Thomas Vogel, director técnico de proyectos para la Fabricación Digital de la Serie A8.
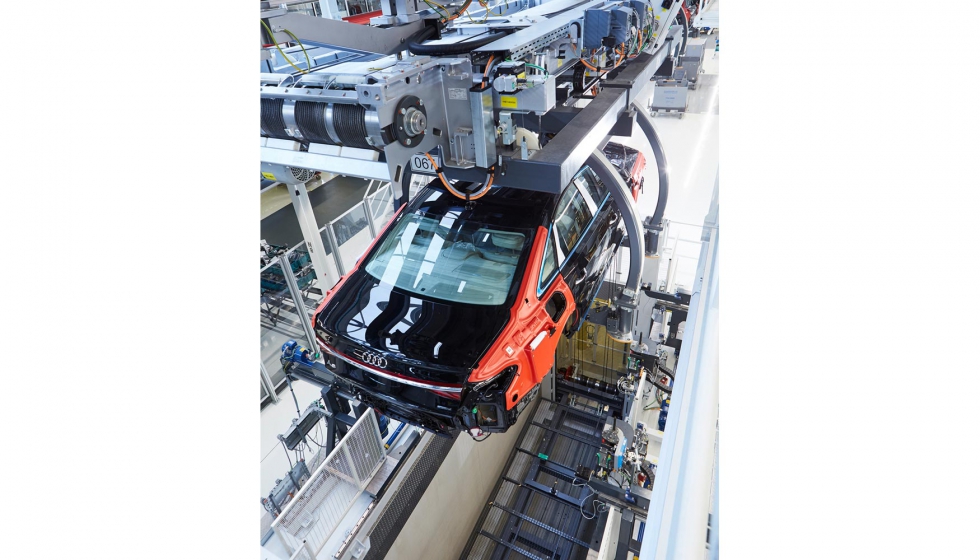
…y en entornos exigentes
Durante el proceso de fabricación, los vehículos están expuestos a fuertes influencias externas, tales como las altas temperaturas y los productos químicos. El aire circulante en el taller de pintura alcanza temperaturas de hasta 230 ºC y, en el proceso pintura catódica por inmersión, el vehículo se sumerge completamente en un tanque que contiene una mezcla de ácido/base. Allí se aplica una corriente eléctrica y el metal se recubre con un tratamiento anticorrosivo, explica Jan-Erik Butt.
La solución que buscábamos tenía que soportar estas duras condiciones, por lo que el equipo del proyecto decidió utilizar etiquetas RFID pasivas de un solo uso. Estas etiquetas pueden soportar grandes cargas, y son fáciles de fijar en la carrocería y de quitar durante el montaje final. “La fabricación de la carrocería comienza en el momento en el que se etiqueta o individualiza un larguero. Es entonces cuando se asigna el número de pedido y también se incorpora la etiqueta RFID. Se trata del primer momento en el que se produce una variación que utilizamos con fines de identificación. A partir de entonces, la tecnología RFID ya no se separará del vehículo”. La etiqueta RFID tiene aproximadamente el tamaño de una tarjeta de visita y está fabricada con material Nomex, que protege la antena integrada y el chip del calor y otras influencias.
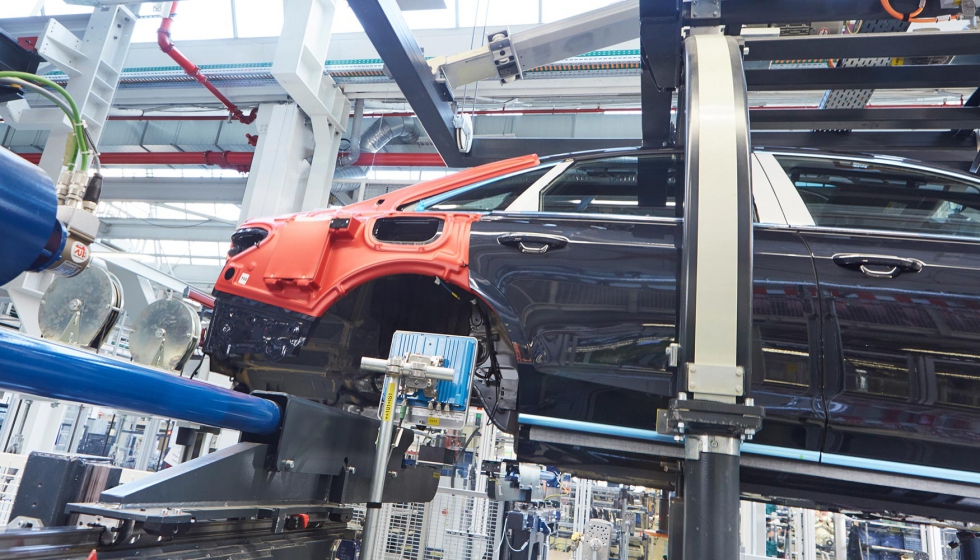
La solución que buscaba Audi debía soportar condiciones duras en, por ejemplo, el taller de pintura. Por ello el equipo del proyecto decidió utilizar etiquetas RFID pasivas de un solo uso.
La mayor parte las características de individualización entre los vehículos se introducen durante el montaje, en función del diseño solicitado por el cliente. En esta fase, se da un nivel muy elevado de variaciones, por lo que es decisivo identificar correctamente los vehículos. En definitiva, cada empleado debe saber qué vehículo tiene delante para poder procesarlo como corresponda. Además, Audi ha optado por un concepto específico que confiere mayor importancia a la fiabilidad de la solución RFID. En este concepto, la lectura RFID está vinculada a una parada de la cinta, lo que significa que la línea de producción se paralizará si la identificación RFID de un vehículo falla en un punto concreto. De este modo, Audi se asegura de que ningún vehículo salga de una estación sin haberse identificado. Finalmente, la etiqueta RFID se elimina durante el montaje final, algunas veces a causa de los datos de producción sensibles.
Compendio de datos homogéneo durante todo el proceso
Para Jan-Erik Butt, otra razón para confiar en la tecnología RFID es la calidad uniforme de los datos en las lecturas de todas las estaciones. “Si obtenemos el mismo tipo de datos de todas las áreas, podemos generar, por ejemplo, análisis de tendencias significativos, ya que las situaciones de lectura son comparables. Esto nos proporciona mucha información sobre todo el proceso de producción, lo que no sería posible si usáramos una mezcla de tecnologías. Obviamente, esto nos permite actuar de una manera completamente diferente, es decir, adoptar medidas preventivas en lugar de simplemente reaccionar siempre a las situaciones. Por ejemplo, estamos trabajando en métodos para observar cómo la calidad de la lectura se deteriora gradualmente y cómo intervenir antes de que ocurran los fallos”.
La función apropiada para aplicaciones específicas
La planta de Audi de Neckarsulm utiliza como solución RFID el ecosistema Sick AppSpace, con el que puede programar aplicaciones de sensores personalizadas con facilidad. “Deseamos crear nuevas alternativas de procesamiento de datos que se adapten exactamente a nuestras necesidades. Por ejemplo, utilizamos Sick AppSpace en un punto de lectura para permitir que la antena se comunique directamente con el sistema MES, a través del cual controlamos la producción, y hacerlo de forma apropiada para el receptor. Sin necesidad de middleware adicional, somos capaces de implementar un marco arquitectónico orientado al servicio como OPCUA, que no depende de ninguna plataforma ni de ningún fabricante. Esto significa que no necesitamos cambiar todos los ajustes del sistema con cada nueva programación. En lugar de eso, podemos utilizar una aplicación para indicar a la antena de forma descentralizada cómo tiene que procesar y transmitir los datos. Queremos ser capaces de controlar de forma flexible una amplia gama de funciones dentro de un único dispositivo de lectura, por lo que tiene sentido que la propia antena sea más inteligente”.
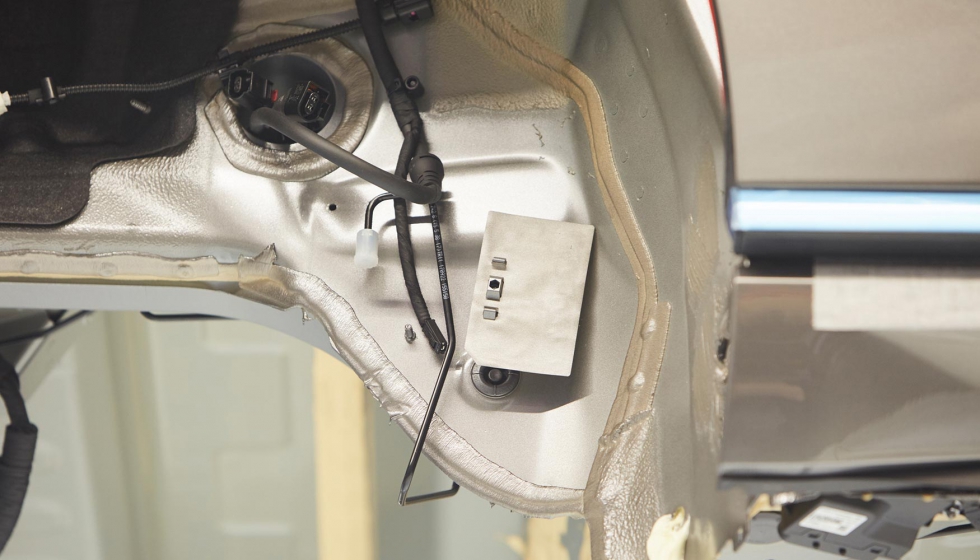
RFID como estrategia de identificación integral
La conclusión de Jan-Erik Butt es positiva: “Si comparamos la situación anterior con la actual, podemos ver que, tras implementar las modificaciones correctamente, hemos logrado una mayor disponibilidad e incluso un ahorro de tiempo significativo en muchos casos. A diferencia de los sistemas propietarios originales, la puesta en servicio de las antenas RFID requiere menos tiempo”.
Lo que comenzó como parte de un proyecto de vehículo y se diseñó para un producto derivado de otro se usa desde hace tiempo de forma generalizada. “Los resultados obtenidos de la identificación RFID nos han convencido. En lugar de usar la tecnología RFID como solución de identificación solo en una nave o como parte de un proyecto de vehículo individual, la planta de Neckarsulm la utiliza para fines de identificación en todas las fases de la producción”.