Sistema automático de almacenamiento y preparación de pedidos
“La automatización nos permite llegar a los puntos de destino en 24 horas”
Cuando Walter Martínez concibió la idea de dotarse de un nuevo almacén, ya pensó que la automatización sería un requisito necesario. Con este propósito confió a Ulma Handling Systems el diseño y la ejecución del proyecto, que finalmente se ha concretado en la instalación de un completo sistema de almacenamiento automático con capacidad para 8.840 paletas -el triple de la capacidad de almacenamiento que tenía la compañía-, constituido por cuatro transelevadores capaces de elevar un peso máximo de 1 tonelada, con una altura de 16,5 metros.
El nuevo sistema ha cambiado muchas cosas en el seno de la compañía, como asegura Walter Martínez: en primer lugar, ha reducido, hasta niveles inapreciables, los errores en las expediciones y se ha visto aumentada de manera extraordinaria la calidad del trabajo, pero, sobre todo, se ha conseguido llegar a los puntos de destino en tan sólo 24 horas desde la formalización del pedido.
“Antes jugábamos con la urgencia que tuviese cada cliente para organizar la logística, de tal manera que, en determinados casos, podíamos tardar de 3 a 10 días en realizar la entrega en cualquier punto de España. Hoy este proceso se ha reducido a unas pocas horas”, asegura.
Los responsables de la compañía, a la hora de tomar la decisión de dotarse de un sistema automático de almacenamiento, se inspiraron en las prácticas que observaron en otros clientes homólogos europeos. “Desde hace años tenemos contactos con grandes almacenistas europeos, y habíamos visto que contaban con este tipo de instalaciones. Así que pensamos que nuestro futuro tenía que pasar obligatoriamente por la automatización”, explica Walter Martínez.
El presidente de la compañía se siente orgulloso de que, en este caso, automatización no ha sido sinónimo de reducción de recursos. “Todo lo contrario, la automatización nos permite hacer más con los mismos medios, y nos va a facilitar abordar nuevos mercados y seguir creciendo”, asegura.
La implantación del sistema, incluidas las fases de consultoría, diseño, instalación y formación, no ha llevado más de un año, sin que se hayan detectado problemas de asimilación relacionados con la introducción de una nueva manera de hacer las cosas. “No hemos tenido ningún problema, en buena medida, creo, porque un número muy elevado de los empleados es gente joven que se desenvuelve sin dificultades en el entorno de las nuevas tecnologías. Por esta razón no han tenido problemas de adaptación; al contrario, han podido comprobar que ha aumentado la calidad de su trabajo”, explica Walter Martínez.
El proceso de selección del proveedor tecnológico llevó algún tiempo a la compañía. “Manejamos tres ofertas, pero al final nos quedamos con Ulma porque pensamos que estaba más cerca de nuestra cultura empresarial, de nuestro espíritu metálico. Nosotros optamos por Ulma y estamos muy contentos”, afirma Walter Martínez.
El directivo no descarta ampliar el sistema a las otra instalaciones del Grupo, aunque el proceso de incorporación de esta tecnología se dilatará algo más en el tiempo. “Hoy por hoy, no todos nuestros centros disponen de las características necesarias para albergar un sistema de este tipo. Por tanto, en algunos casos, deberemos pensar en dotarnos de nuevos espacios”, concluye.
Entre los próximos retos de la compañía figura el de alcanzar la “calidad total”, lo que supondrá involucrar a todos sus departamentos en el logro de la excelencia. Merece la pena señalar a este respecto que la compañía dispone en sus instalaciones de un laboratorio de calidad, dotado de varios sistemas de medición de dureza, elasticidad, resistencia y espesores de las piezas, con el fin de garantizar el nivel de calidad necesario. Su actividad, además, está certificada por las normas BVQI (Bureau Veritas Quality International): BVQI-ENAC, BVQI-UKAS e ITA.
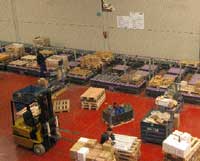