Prototipo de control inteligente para un FMS basado en bloques funcionales, STEP-NC y controladores CNC abiertos
En este trabajo se exponen los elementos clave de un sistema de control prototipo, desarrollado para un sistema de fabricación flexible, que soluciona alguna de las deficiencias que presentan este tipo de sistemas como la necesidad de desarrollos a medida, la falta de reconfigurabilidad o su bajo rendimiento. El desarrollo se apoya sobre dos pilares centrales: la descentralización del control de fabricación, mediante el uso de bloques funcionales y una arquitectura holónica; y la integración de la información resultante de planificación de procesos en el control, explotando la orientación a objetos del estándar STEP-NC y la posibilidad para representar planes de procesos con alternativas.
1. Introducción
La globalización de los mercados ha hecho que la demanda de los productos sea muy volátil y variante, tanto en el tipo de productos demandados como en su cantidad. Una exigencia que ha forzado a adaptar y modernizar los actuales sistemas de fabricación, para mejorar su respuesta dinámica. Una de las posibles soluciones para mejorar su agilidad consiste en la utilización de sistemas de fabricación flexibles (FMS) con nuevas y mejores capacidades que salven las limitaciones de los FMS tradicionales, con arquitecturas centralizadas con adaptabilidad reducida frente a cambios en el entorno de producción (disponibilidad, cambios de capacidad, etc.)
Los FMS son sistemas altamente automatizados que se componen de un conjunto de máquinas de propósito general, un sistema automatizado de transporte y un sistema de control del conjunto. Las máquinas, CNCs normalmente, y el sistema de transporte aportan gran parte de la flexibilidad al sistema, mientras que el control actúa de director de orquesta, coordinando el uso de los diferentes recursos para lograr producir los productos demandados de la forma más eficiente posible. Para que la implementación de los FMS sea exitosa, es clave que se integre a los CNCs con el control del sistema, mejorando así la capacidad adaptativa del conjunto, necesaria para adecuarse a los cambios y fundamental para optimizar el uso de los recursos y mejorar la calidad de los productos fabricados.
Esta falta de integración ha sido en el pasado uno de los factores limitantes en la adopción de los FMS, debido especialmente al carácter cerrado de los controladores CNC (interfaces de comunicación y lenguajes propietarios), que llevaba, en ocasiones, a tener que desarrollar soluciones a medida, incrementando enormemente los costes. De ahí que desde hace algunos años ya se venga apuntando [1] la necesidad de desarrollar controladores más abiertos, basados en interfaces y lenguajes estandarizados, que posibiliten el desarrollo de FMS con mayor agilidad y flexibilidad. Un paso importante en esta dirección son los controladores basados en PC, que han empezado a abrirse paso en el mercado en los últimos años. Éstos, en esencia, se aprovechan del abaratamiento y de las mejoras de rendimiento computacional de equipos cada vez más estandarizados, de forma que parte de las funcionalidades del controlador, que se ejecutaban sobre hardware dedicado, pasan a realizarse por componentes software ejecutados en PCs industriales, lo que permite reducir los costes de desarrollo. A su vez, estos controladores pueden calificarse como abiertos cuando aprovechando el uso de interfaces de comunicación estándar permiten el intercambio de información con el exterior utilizando protocolos conocidos.
Esto abre un nuevo abanico de posibilidades en el desarrollo de FMS, posibilitando la aparición de sistemas más integrados y más inteligentes haciendo uso de sistemas de control basados en arquitecturas descentralizadas. En la consecución de este objetivo, cobra especial interés el estándar IEC 61499, una arquitectura de referencia que permite crear sistemas de control distribuidos (DCS) de forma sencilla mediante la utilización de bloques funcionales (FB). Los FBs son unidades computaciones independientes que se encargan de realizar tareas muy elementales, cálculos simples, y que se conecta entre sí mediante un flujo de señales y datos creándose redes de bloques que en su conjunto conforman sistemas de control complejos. La principal ventaja de utilizar FBs es que las distintas partes de la red pueden distribuirse entre los recursos que componen el sistema siempre que existan redes de comunicación que posibiliten su interconexión.
En base a estas consideraciones, en las siguientes secciones detallaremos algunos de los desarrollos realizados en este proyecto de investigación, para mostrar como la adopción de nuevos principios de control pueden mejorar sustancialmente las prestaciones de los FMS y, por lo tanto, su viabilidad. Para ello, primero se discute la problemática de la integración semántica entre los CNC y el sistema de control, y expondremos las ventajas de la utilización de STEP-NC. Después, presentaremos brevemente el prototipo de control desarrollado y detallaremos como se integra el controlador FAGOR 8070OL. Por último discutiremos las ventajas, presentes y futuras, que ofrece el prototipo desarrollado y las orientaciones que guiarán los futuros trabajos.
2. La integración semántica al sistema de control/CNC
La mayor limitación en la integración de los controladores CNC con el control del FMS es el lenguaje máquina utilizado para comunicarse. En la mayoría de casos los controladores utilizan lenguajes propietarios basados en el conocido código G-M (ISO 6983) o pseudo-lenguajes propietarios de mayor nivel, ambos caracterizados por su falta de estandarización y por limitar la retroalimentación [2]. Los programas creados con estos lenguajes se limitan a una secuencia lineal de instrucciones, que hay que adaptar para cada CNC en particular y que éste debe ejecutar. La consecuencia, a nivel de control, es la imposibilidad de integrar todo el conocimiento elaborado en la planificación de procesos (operaciones y condiciones de trabajo alternativas, etc.) con el de ejecución, limitando así la aparición de sistemas de control más inteligentes, que puedan explotar toda la información generada durante la planificación [3].
Para poder explotar la información del proceso de planificación en el nivel productivo, a principios de los años 2000 aparece la iniciativa STEP-NC (ISO14649), cuyo objetivo es proporcionar un nuevo modelo de transferencia de datos, orientado objeto y que se basa en los modelos del estándar STEP (ISO10303). Una iniciativa que se estableció para favorecer la interoperabilidad semántica la cadena CAD/CAPP/CAM/CNC y remplazar al código-G. En lugar de programas de mecanizado en código-G, compuestos por acciones elementales, STEP-NC propone la transferencia de información relativa a planes de procesos basados en ‘features’ estandarizados (ST EP AP224), donde esté contenida tanto las características geométricas, qué se debe fabricar, como tecnológicas, cómo se debe fabricar, de forma que los controladores de los CNC tengan un mayor poder de decisión y adaptación, dando lugar a sistemas más inteligentes. Además, STEP-NC también posibilita la transferencia de planes de proceso no lineales, uno de los principales campos de investigación en la fabricación en las últimas décadas, de forma que se pueda incluir alternativas en cuanto a los pasos que hay que realizar para fabricar un producto, tanto a nivel de macro como de micro-planificación. Estas alternativas pueden mejorar mucho la agilidad de un sistema de fabricación ya que, por ejemplo, se puede adaptar la secuencia de subfases u operaciones a ejecutar al estado de cada sistema en particular, sin tener que rehacer la planificación, o seleccionar las herramientas más adecuadas para cada operación en función del estado de las mismas. Finalmente, STEP-NC también permite agilizar la integración directa de la planificación con las tareas de control de mayor nivel como el despacho de órdenes, gracias a que sus modelos son orientados al objeto y, por tanto, directamente comprensibles por los dispositivos de control actuales.
En resumen, la utilización de STEP-NC en lugar de lenguajes máquina como el -M, potencia las posibilidades de crear sistemas de fabricación más inteligentes, que pueden rentabilizar el uso de los recursos, adaptando las variables del proceso de fabricación, de forma dinámica y en función de una información que muchas ocasiones es generada durante la planificación de procesos pero que se pierde.
3. Prototipo de control desarrollado
Para mostrar las ventajas de la utilización de un control de FMS más inteligente se ha desarrollado un prototipo de control distribuido, basado en una arquitectura genérica estructurada según una holarquía de bloques funcionales de 4 niveles. Dicho sistema se encarga de realizar todas las tareas del llamado control de fabricación (niveles 2 -3 del ISA) que en esencia son: programación del trabajo, despacho de las unidades, monitorización de los recursos y recuperación de los errores. Estas tareas se han programado íntegramente mediante FBs agrupados en redes, de forma que la lógica de control esté distribuida entre agentes autónomos, que colaborarán entre ellos para obtener una solución para cada problema de forma rápida y teniendo en cuenta el estado real del sistema en cada momento, en lugar de hacerlo aplicando pesados algoritmos de optimización que requieran mayores recursos y tengan una menor tolerancia a las perturbaciones.
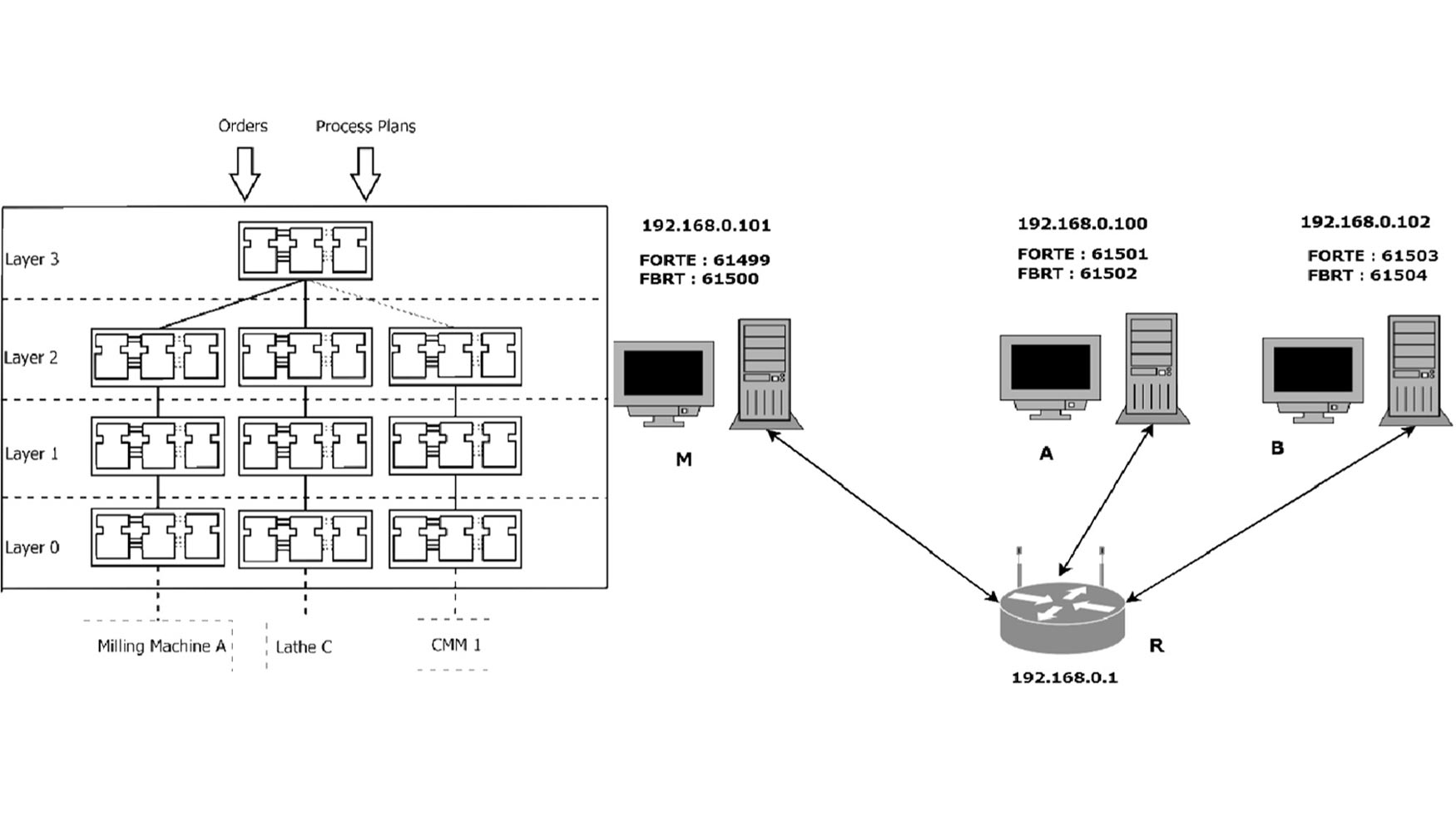
A nivel físico el prototipo está compuesto por 3 equipos y una red de comunicaciones inalámbrica (Figura 1). El control se distribuye entre los tres equipos de forma que el equipo ‘M’ se encarga de ejecutar los FB encargados de las tareas de mayor nivel, programación y despacho, y los equipos ‘A’ y ‘B’ se encargan de ejecutar los FB de gestión de las máquinas, que en este caso son dos fresadoras controladas mediante sendos Fagor 8070OL basados en PC y que, por el momento, se simulan usando el Simulador de CNCs de Fagor (figura 2).
De los cuatro niveles de la arquitectura de control, por motivos de brevedad, en este documento sólo mostraremos información del de menor nivel (Layer 0), que es el encargado de comunicar directamente con los controladores CNC, actuando de interfaz con los mismos. Para más información sobre el resto del prototipo, remitimos al lector a [4] donde se detallan los cuatro niveles y sus funcionalidades.
4. Comunicación con el Fagor 8070 OL
Uno de los aspectos más interesantes del desarrollo realizado, desde la perspectiva de los controladores CNC, reside en cómo se ha establecido la comunicación entre el control, modelado e implementado según el IEC61499, y las máquinas, y en concreto con los controladores Fagor 8070 OL. A nivel software el controlador simulado, al igual que lo haría el real, se ejecuta sobre un PC, que a su vez corre un SO Windows. En este mismo equipo también se ejecuta un runtime (4DIAC-FORTE) sobre el que se ejecutan los bloques funcionales de nuestro control, de forma que sobre un mismo equipo tenemos dos programas que se ejecutan en paralelo: el 8070 y un runtime de FB. Estos dos programas se comunican a través de objetos compartido, usando la tecnología COM de Microsoft (ComponentObjectModel), gracias a los 22 servidores que ofrece el 8070OL y un API (ApplicationProgramming Interface) que permite utilizarlos. De este modo, desde el control del sistema podemos acceder fácilmente a todo tipo de datos del controlador, como su estado, las herramientas disponibles o los tiempos de ejecución, y remontarlos a los niveles superiores, utilizando las señales y datos del IEC61499, pudiendo así utilizar los datos reales y actuales de las máquinas para la toma de decisiones de mayor nivel, como la programación o el despacho. Más aún, a través de estos servidores también podemos enviar directamente comandos de ejecución, lo que permite realizar una atomización de los programas de mecanizado, es decir, en lugar de transmitir programas enteros, podemos enviar al controlador instrucciones individuales o bloques reducidos. Esta atomización cobra especial relevancia porque la planificación se realiza en STEP-NC y este estándar no se puede usar para comunicar directamente con las máquinas debido a la falta de compatibilidad de los controladores con el mismo, necesitándose de una traducción atómica de STEP-NC a código -G (nivel 1 de la arquitectura). De esta forma podemos aprovechar mucha de la información de la planificación y condicionar el avance de la fabricación en función de los resultados de la ejecución, a través de una fragmentación adecuada que permita, por ejemplo, correcciones de las trayectorias para compensar determinados defectos geométricos. En conjunto, esto permite ampliar enormemente las posibilidades de integración entre el controlador, el control de fabricación y la planificación de procesos, dando lugar a sistema s más inteligentes y adaptativos.
5. Conclusiones
En este breve documento se han mostrado algunas de las ventajas que supone la adopción de nuevos estándares y estrategias de control, especialmente las referentes a la integración tanto de la planificación de procesos, a través de STEP-NC, como de los CNC, a través de controladores basados en PC y abiertos, en el sistema de control de un sistema de fabricación flexible. A través del prototipo de control desarrollado se evidencia como las capacidades de los FMS pueden mejorarse, en términos coste, reconfigurabilidad o rendimiento, mediante la utilización de un control más inteligente y adaptado a las tecnologías de control distribuido actuales.
Como nota final y avance de los trabajos futuros, hay que resaltar que los desarrollos realizados hasta el momento sólo representan una primera fase, que pretende fijar las bases para crear FMS inteligentes según el paradigma de la fabricación distribuida y holónica. A través de la integración se pueden lograr numerosas mejoras en el proceso de fabricación, especialmente en lo referente a la calidad de las piezas obtenidas. Por ejemplo, gracias la integración de los datos geométricos en los planes de proceso de STEP-NC, y la comunicación bidireccional con los controladores, se pueden recalcular las trayectorias de las herramientas en función del posicionamiento real de las piezas sobre las máquinas, o se puede extender el uso de planes de proceso no lineales que capaciten a cada sistema de fabricación, partiendo de una base común, a adaptarse en el nivel temporal que se establezca para la macro-planificación (cambio de secuencias de subfases y operaciones) y en un nivel temporal menor para la micro-planificación, llegando en su caso, bajando en la escala de tiempos de reacción, a sistemas adaptativos en tiempo real.
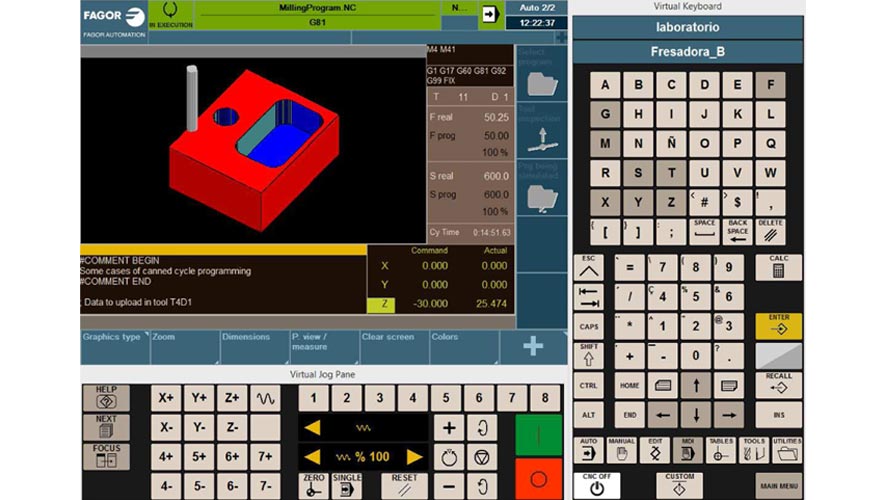
Agradecimientos
Este trabajo ha sido financiado por el proyecto P1.1B2012-60 de la Universitat Jaume I.
Bibliografía
[1] M. Minhat, V. Vyatkin, X. Xua, S. Wong, Z. Al-Bayaa. A novel open CNC architecture based on STEP-NC data model and IEC61499 function blocks. Robotics and Computer-Integrated Manufacturing, 2009, p.560–569. (DOI: 10.1016/j.rcim.2008.03.021)
[2] D.M. Elias, Y. Yusof, M. Minhat. A review of intelligent CNC controller development based on STEP-NC. 2nd International Conference on Mechanical and Manufacturing Engineering (ICME 2011), 2011.
[3] L. Wang, M. Holm, G. Adamson.Embedding a process plan in function blocks for adaptive machining. CIRP Annals - Manufacturing Technology, 2010, Vol. 59, p. 433-436
[4] E. Querol, F. Romero, A.M. Estruch, J. Serrano. Design of the Architecture of a Flexible Machining System using IEC61499 Function Blocks. Proceedings of the 6th Manufacturing Engineering Society International Conference, 2015.