Fabricación y reparación de turbinas mediante aporte láser en 5 ejes
El trabajo que se presenta desarrolla una metodología para la obtención sistemática de los parámetros y estrategias óptimas para piezas que requieran la utilización de procesos de aporte en 5 ejes continuos. En primer lugar se diseña una geometría que tiene en cuenta los movimientos de máquinas multi-axiales. Posteriormente, se realiza una serie de ensayos para establecer los parámetros y estrategias óptimas. Para ello, se plantea un criterio de selección basado en la ponderación de las diferentes características medidas tras los ensayos. Además se aplica un algoritmo para proporcionar una velocidad de avance constante del cabezal de aporte, Por último, utilizando los parámetros y estrategias aplicadas, se procede a la aplicación de la metodología con un caso real del sector aeronáutico.
1. Introducción
El aporte de material mediante láser es un proceso que utiliza un haz láser para generar un baño fundido muy localizado en un substrato o material base. Dentro de este baño fundido se inyecta un material de aporte que puede encontrarse en forma de hilo o de polvo, generándose así una capa de material. Destacan como aplicaciones principales de este proceso el recubrimiento superficial de piezas, la reparación de zonas dañadas y la fabricación directa de piezas de alto valor añadido pertenecientes a diferentes sectores como pueden ser el sector aeronáutico [1] y el sector moldista [2].
El estudio del proceso de aporte láser puede realizarse bien a partir de la modelización de los fenómenos que definen el proceso o bien a partir de métodos experimentales. Por un lado, gracias a las técnicas de modelización del proceso de aporte láser, es posible predecir con anterioridad cual va a ser el resultado final del proceso y reducir el coste del estudio una vez que se prescinde de los ensayos experimentales. Sin embargo, el número de trabajos que se decantan por este tipo de enfoque [3], [4] es mucho más reducido que en el caso experimental. Por otro lado, la aproximación más frecuente en lo que se refiere al proceso de aporte láser es recurrir a técnicas experimentales. Este tipo de estudios se basan en la variación de una serie de parámetros como pueden ser la potencia del láser, el tamaño y tipo de flujo de polvo, la velocidad de avance, etc. para una pieza de un material y material de aporte concretos. Así, la metodología se basa en realizar una serie de aportes en línea con diferentes parámetros y obtener una ventana de parámetros de proceso adecuada. Para obtener esta ventana de parámetros se estudia la calidad de los cordones en función de su geometría o de la productividad del proceso. Este tipo de metodología es más empleada en trabajos científicos e industriales por ahora, por lo que las referencias con este enfoque son más abundantes [5], [6], [7], [8], [9].
Dentro de los estudios publicados hasta el momento, la gran mayoría se centran en la optimización del proceso en función de los parámetros o estrategias de aporte para técnicas de aporte en 3 ejes o, en algún caso, 3+2 ejes [10], [11], [12]. No obstante, en términos generales, se puede decir que la estrategia óptima de aplicación del aporte por láser se consigue aplicando el láser perpendicularmente a la superficie que se desea reparar, por lo que la aplicación de este proceso sobre geometrías complejas pasa por el empleo de una estrategia de aporte en 5 ejes continuos. Dado que cada día el número de piezas a las que se aplica este proceso aumenta conforme lo hace también la complejidad de las mismas, la demanda del proceso de aporte en 5 ejes continuos es creciente.
Se ha planteado por tanto, el desarrollo de una metodología específica para la optimización del proceso de aporte láser en 5 ejes continuos. Para comenzar el estudio experimental del aporte láser es necesario estudiar tanto las estrategias de aporte óptimas como los parámetros de aporte óptimos.
Así, en primer lugar es necesario determinar los equipos y materiales a utilizar en la fase experimental, dado que el comportamiento de cada material puede variar ante equipos diferentes. En cualquier caso, la metodología planteada podría adaptarse a otras configuraciones y sistemas láser diferentes.
Posteriormente, es necesario identificar cuáles son los parámetros principales del proceso que influyen en el estado final del cordón generado para definir la ventana de los parámetros que van a ir variando a lo largo de la serie de ensayos. Uno de estos parámetros es la potencia del láser cuya influencia es directa sobre la anchura del cordón aportado. También se definen otros parámetros como el flujo de polvo aportado que se relaciona con la altura que alcanza el cordón o la velocidad de avance del cabezal. De esta forma, y con la intención de facilitar la selección de los parámetros de aporte óptimos, se ha desarrollado un factor de optimización gracias al cual es posible conocer cuáles de los parámetros propuestos son los más apropiados para el aporte del material estudiado en cada momento aplicando un criterio cuantitativo. En este factor de optimización se ponderan una serie de parámetros dándoles mayor o menor peso dependiendo de su influencia positiva o negativa en la calidad del cordón aportado.
Por otro lado, una de las condiciones que el sistema de aporte de material debe cumplir consiste en poder mantener una velocidad de avance del cabezal constante. Esta condición que se cumple sin problemas en los aporte de material en 3 ejes, puede representar uno de los principales problemas en los sistemas de aporte en 5 ejes continuos ya que la interpolación de más ejes puede provocar cambios repentinos en la velocidad de avance del cabezal viéndose reducida en algunas situaciones extremas a valores muy por debajo de la velocidad de avance programada. Así, este fenómeno afecta negativamente a la calidad del cordón aportado ya que en esos instantes de disminución de la velocidad del cabezal de aporte se deposita más material del deseado. Por esta razón, se ha desarrollado un algoritmo para mantener la velocidad de avance constante en cada momento.
De la misma forma que las estrategias de aporte de material son determinantes en los aportes de material en 3 ejes, en 5 ejes también es necesario estudiar las mismas para determinar cuáles son las más apropiadas para cada caso, ya se trate de recubrimientos de piezas, reparaciones o fabricación directa de las mismas. Además, no hay que olvidar que en la actualidad no existe un software específico para el diseño de estrategias de aporte de material, motivo por el cual es necesario recurrir a un software general de CAM y posteriormente adaptar las trayectorias generadas (generalmente válidas para procesos de mecanizado) a procesos de fabricación aditiva como es el aporte por láser. Es decir, en vez de restar material, se invierte el sentido de las de las trayectorias para ir añadiendo material.
Dado que el proceso de aporte de material mediante láser es un proceso térmico, los gradientes de calentamiento y enfriamiento influyen en la microestructura final del material y en las tensiones residuales generadas. De esta forma, el riesgo de aparición de grietas y su influencia en las propiedades mecánicas de las piezas dependen directamente de la elección de parámetros y estrategias de aporte del proceso. Es por ello, por lo que dentro de la fase experimental de la metodología planteada se procede también al análisis de la integridad del cordón una vez que se ha realizado el aporte de material.
De esta forma, se ha realizado un estudio experimental profundo con el objetivo de disponer de datos propios del proceso y contrastarlos con trabajos de otros autores, con lo que se dispone de una base de conocimiento sólida para posteriormente abordar de forma razonada la ejecución del proceso.
Este trabajo plantea una metodología de obtención de parámetros para el proceso de aporte de material en polvo en 5 ejes. En primer lugar, se establece la geometría de la pieza test donde se van a realizar los ensayos y la naturaleza de los mismos. Los ensayos realizados son de dos tipos, por un lado, se realiza una serie de ensayos para obtener los parámetros óptimos del proceso, y por otro, se completan los ensayos con el objetivo de estudiar cual es la distancia óptima que se tiene que mover el cabezal entre capas para que la desviación con respecto a lo que crece el cordón sea mínima. Se desarrolla un criterio que pondera los aspectos más importantes de los cordones con el objetivo de poder comparar las características de éstos y elegir así los parámetros óptimos. Por último, se utilizan estos parámetros para la realización de los diferentes aportes presentados.
Finalmente, una vez que se da por finalizado la fase de aporte de material se remecanizan las piezas para darles el acabado final. El valor añadido de la pieza en esta etapa final es muy elevado y la utilización de todas las herramientas disponibles para garantizar la correcta ejecución del mecanizado está justificada. La verificación virtual del proceso de aporte también se ha llevado a cabo, lo que permite verificar la ausencia de colisiones entre los diferentes elementos del sistema, que podría acarrear potenciales daños en la pieza o en el sistema de aporte por láser.
2. Descripción de los equipos y materiales empleados
2.1. Equipos empleados
Los equipos utilizados para el desarrollo de los ensayos experimentales se describen en este apartado. En resumen, los equipos empleados son una cinemática de 5 ejes, sobre la que se ha instalado un láser de alta potencia y un cabezal de aporte de polvo. Finalmente, ha sido necesaria la instalación de un sistema de aporte de polvo para alimentar el cabezal.
Los ensayos se han realizado en una máquina de procesado láser de 3+2 ejes continuos Kondia Aktinos-500 (Figura 1a). Se trata de un desarrollo propio realizado sobre un centro de mecanizado, por lo que se trata de una célula única con esta configuración. Para la realización de los ensayos se ha empleado un láser de fibra ROFIN FL010 de última generación con una potencia de 1 kW. El equipo utilizado para el aporte de material en forma de polvo ha sido un alimentador SULZER Twin-10C. Este alimentador permite regular el flujo másico de material a través del giro de un disco que distribuye el polvo hacia la boquilla de aporte.
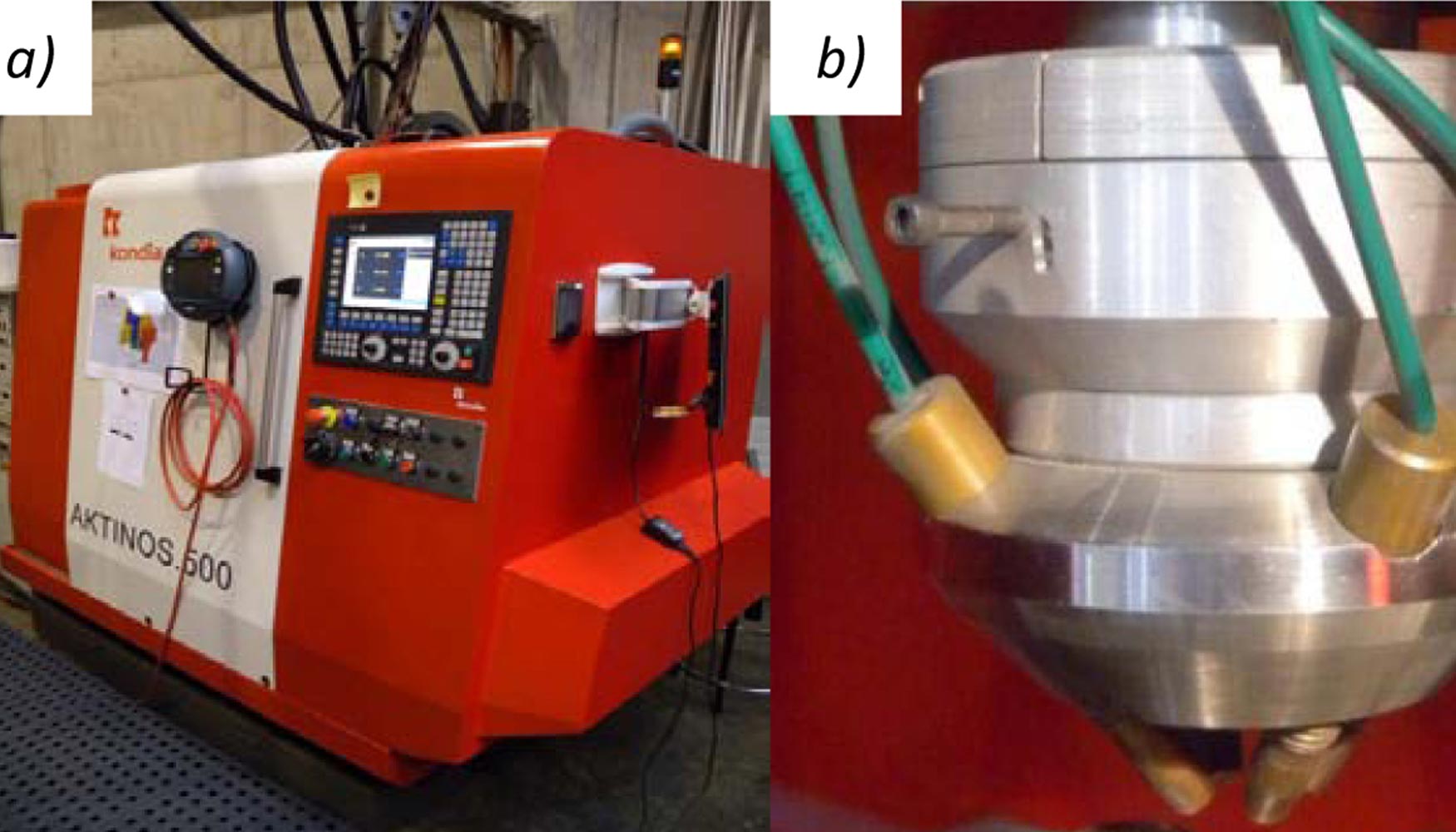
La boquilla utilizada para la inyección de polvo es una boquilla coaxial discreta (Figura 1b) diseñada y fabricada dentro del Dpto. de Ingeniería Mecánica de la Universidad del País Vasco, UPV/EHU [4].
2.2. Selección de materiales sometidos a estudio
En este trabajo se realiza el estudio experimental de la técnica de aporte láser en 5 ejes para las aplicaciones de recubrimiento, reparación y fabricación directa de piezas metálicas principalmente del sector aeronáutico. Por este motivo, uno de los materiales seleccionados ha sido el Inconel 718, dado que es uno de los más frecuentes en este sector. También se han utilizado materiales de bajo coste para la realización de pruebas de validación inicial de la metodología.
La técnica de aporte de material mediante láser permite tanto la combinación de materiales diferentes para el substrato y el recubrimiento como la utilización del mismo material de aporte y substrato para la reparación de componentes. Los materiales utilizados como substrato son el acero estructural AISI 1045, el acero inoxidable AISI 304 y la aleación base Níquel comercial Inconel 718. Por otro lado, además de los materiales ya mencionados, se utiliza como material de aporte el acero inoxidable AISI 316L.
3. Evaluación del proceso de aporte láser mediante la fabricación de piezas tipo
3.1. Cordones para reparación sobre superficie ondulada
La primera aproximación a aporte láser en 5 ejes continuos se lleva a cabo a través de la deposición de una serie de cordones que delimitan un contorno cerrado con forma de ‘D’. La superficie sobre la que se aporta el material ha sido previamente mecanizada con una doble ondulación de forma que el láser se ve obligado a avanzar de mayor a menor curvatura y viceversa, de menor a mayor curvatura. Asimismo, se varía también la geometría de los cordones para ver la influencia de la curvatura en los mismos. Se programan las trayectorias de aporte (Figura 2a y 2b) y condiciones que se muestran en la tabla 1. Como puede observarse, se programan los mismos valores de potencia, velocidad de avance del cabezal de aporte y el mismo valor del flujo de polvo para realizar una comparación entre las mismas con el objetivo de ver cómo influye la variación de la curvatura en la calidad de los cordones.
Material base |
Material aporte |
Potencia (W) |
Avance (mm/min) |
Flujo polvo (g/min) |
Nº pasadas |
Δz (mm) |
Altura teórica (mm) |
AISI 304 |
AISI 316L |
350 |
200 |
3,3 |
13 |
0,15 |
2 |
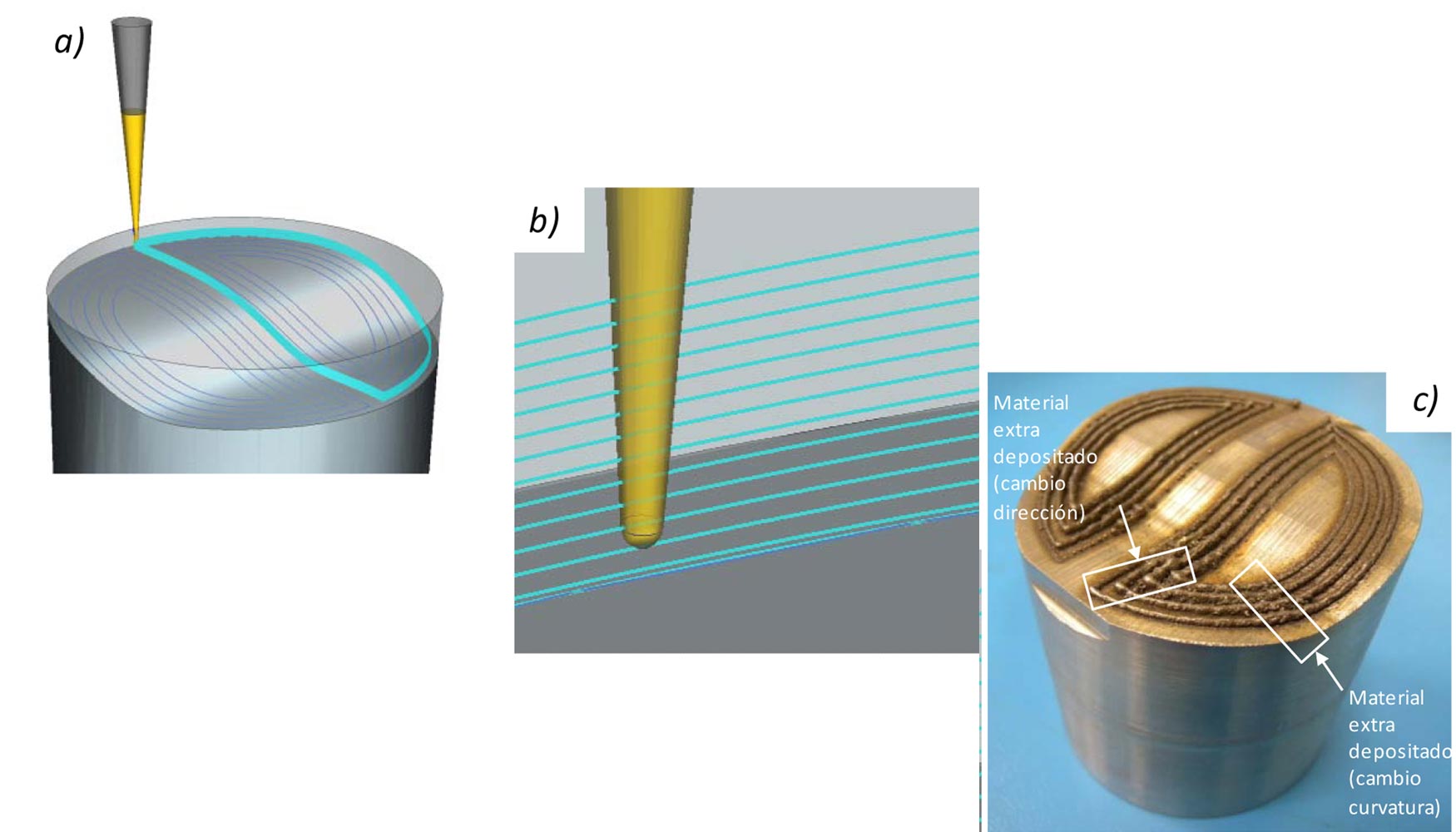
En esta primera aproximación al aporte en 5 ejes continuos, se hacen patentes las dificultades del proceso. Como puede observarse en la figura 2c, aparecen zonas de material depositado en exceso, tanto en las esquinas (cambios de dirección de trayectoria) como en los cambios de curvatura de la superficie. Esto es debido a que en esos puntos la velocidad de avance del cabezal disminuye y por ese motivo se aporta una cantidad de material mayor. Tras la medición de la altura de los cordones se encuentran zonas que cumplen con la altura prevista (2 mm) y zonas que superan con creces esta altura debido a las disminuciones de velocidad de avance.
3.2. Recubrimiento de una zona esférica
Tras una primera aproximación al proceso de aporte de material en 5 ejes continuos en la que se observa la influencia de la curvatura de la superficie y de las estrategias de aporte, se lleva a cabo el aporte sobre una segunda pieza en la que se aporta material sobre un casquete esférico. El material de aporte AISI 316L y el material base AISI 1045. En este caso se llevan a cabo cuatro tipos de aportes (Tabla 2) diferentes. En un primer lugar se programan una serie de cordones que parten desde la zona superior de la esfera hasta recorrer media esfera. Se diseñan una serie de ensayos variando potencia, velocidad de avance y flujo de polvo con el objetivo de determinar cuáles son los parámetros de aporte óptimos.
Además de la programación de los parámetros de aporte mencionados, es necesario controlar el incremento de altura del cabezal. El proceso de aporte láser tiene una zona óptima de distancia entre el cabezal y el substrato en la cual se debe realizarse el aporte, ya que una distancia muy lejana o muy cercana del cabezal da lugar a cordones de menor calidad. Una vez que se conocen los valores más apropiados para el aporte de material (potencia, velocidad de avance, flujo de polvo, Δz) se realiza un tercera serie de ensayos con diferentes estrategias de aporte para el recubrimiento de la esfera y se determina cuáles son las estrategias óptimas de aporte. Finalmente, con los parámetros y estrategias de aporte óptimas se recubre por completo el casquete esférico.
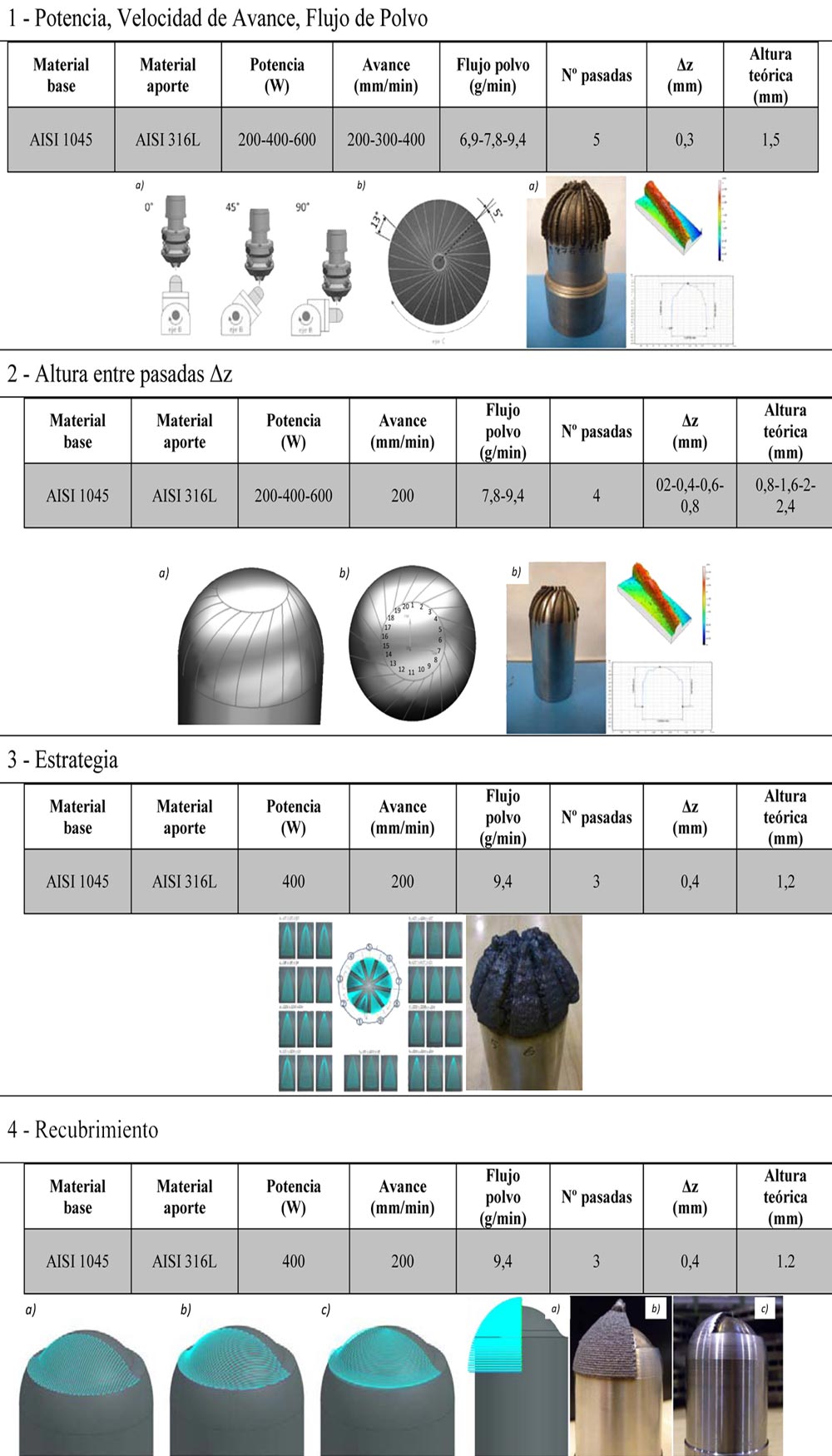
3.3. Fabricación directa álabes en un impeller
Se diseñan las estrategias para la fabricación directa de los álabes de un impeller (Figura 3). Al tratarse de una pieza rotativa únicamente es necesario programar dos tipos de aportes, el referente al álabe de mayor tamaño (blade) y las estrategias de aporte para los álabes de menor tamaño (splitter). De este modo se crean tantas capas de material como sean necesarias para alcanzar la geometría completa del álabe. En el caso del álabe pequeño (splitter), son necesarias 75 capas con una diferencia entre pasadas de 0,2 mm hasta completar los 15 mm de altura. La programación de todas las capas de aporte de material cumplen con la condición de perpendicularidad entre el haz láser y la superficie de aporte del material. Los parámetros de aporte se muestran en la tabla 3.
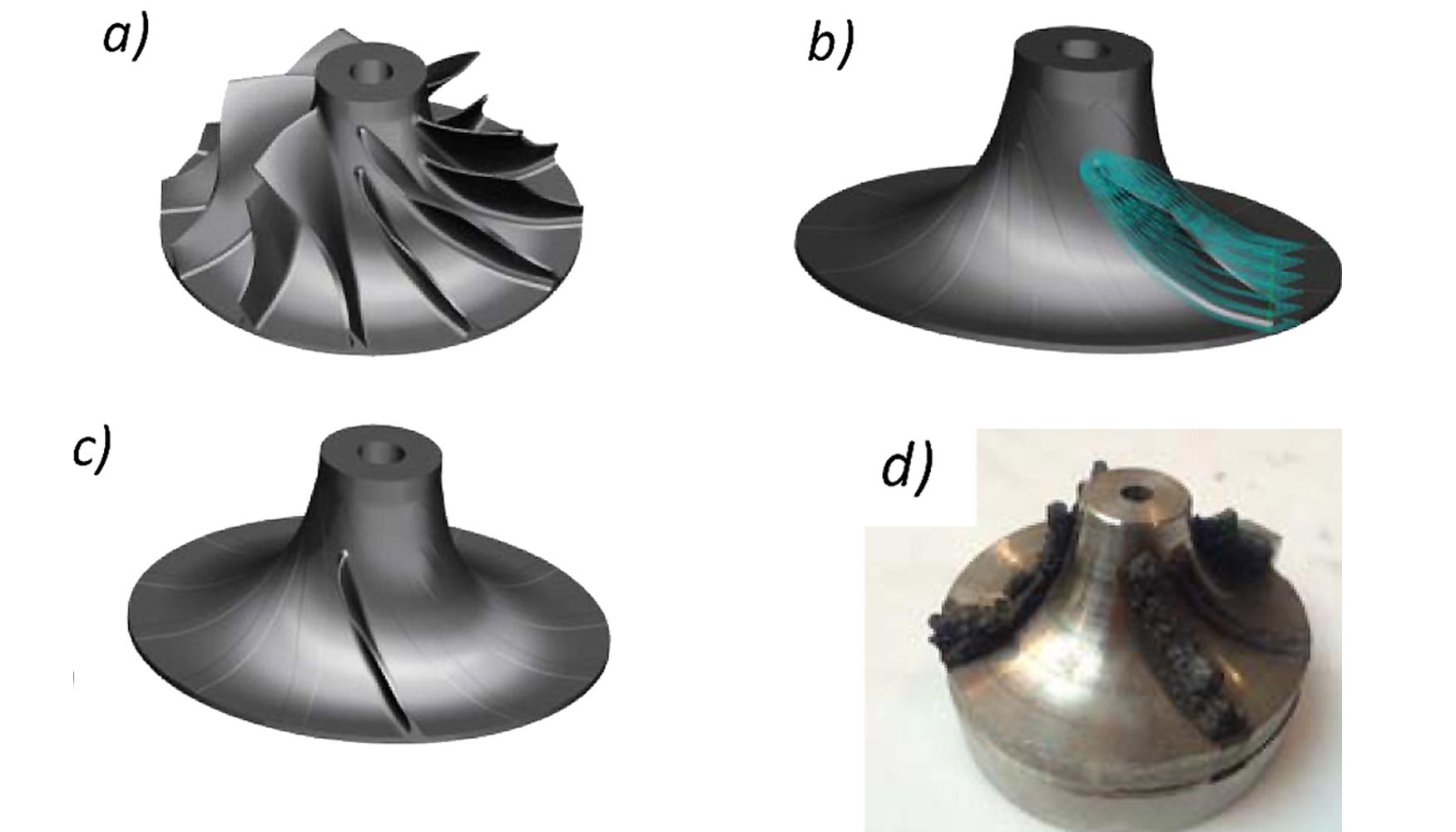
Material base |
Material aporte |
Potencia (W) |
Avance (mm/min) |
Flujo polvo (g/min) |
Nº pasadas |
Δz (mm) |
Altura teórica (mm) |
AISI 304 |
AISI 316L |
400 |
200 |
9,4 |
75 |
0,2 |
15 |
El proceso de aporte de los álabes pone de manifiesto nuevamente las dificultades del sistema para mantener constante la velocidad de avance de la boquilla de aporte respecto de la pieza. Este efecto se hace más patente en las zonas de cambio de sentido de la trayectoria, en las esquinas o en zonas donde se ha programado la trayectoria con una tolerancia muy fina y que por lo tanto hay muchos puntos en poco espacio. Todos estos fenómenos provocan una disminución de la velocidad de avance del cabezal con lo que se aporta mayor cantidad de polvo en esas zonas lo que se traduce en material extra depositado. Por este motivo, se observa la necesidad de dirigir los esfuerzos de programación hacia trayectorias que permitan mantener la velocidad de avance contante.
3.4 Fabricación directa álabe blisk
Se estudia por otro lado el proceso de aporte de material mediante aporte por láser para la fabricación directa de álabes en un blisk. Se diseñan una serie de cordones sobre una superficie de un blisk (Figura 4b) con el objetivo de determinar los parámetros óptimos de aporte para posteriormente poder aportar la geometría completa de sus álabes. Se programan una serie de cordones que corresponden con la base de cada uno de los álabes.
La estrategia de aporte (Figura 4b) diseñada para el proceso de aporte de los álabes es de tipo espiral siendo el paso de la espiral de 0.15mm. La continuidad de una estrategia espiral permite la realización del aporte de forma continua no siendo necesario el apagado y posterior encendido del láser entre trayectorias de transferencia entre las diferentes capas. Este fenómeno mejora la calidad del aporte y la productividad del proceso. En relación con la programación de las trayectorias de aporte de los álabes hay que destacar que se mantiene la perpendicularidad entre el haz láser y el material base o substrato con el objetivo de evitar reflexiones y obtener el máximo nivel de absorción de energía.
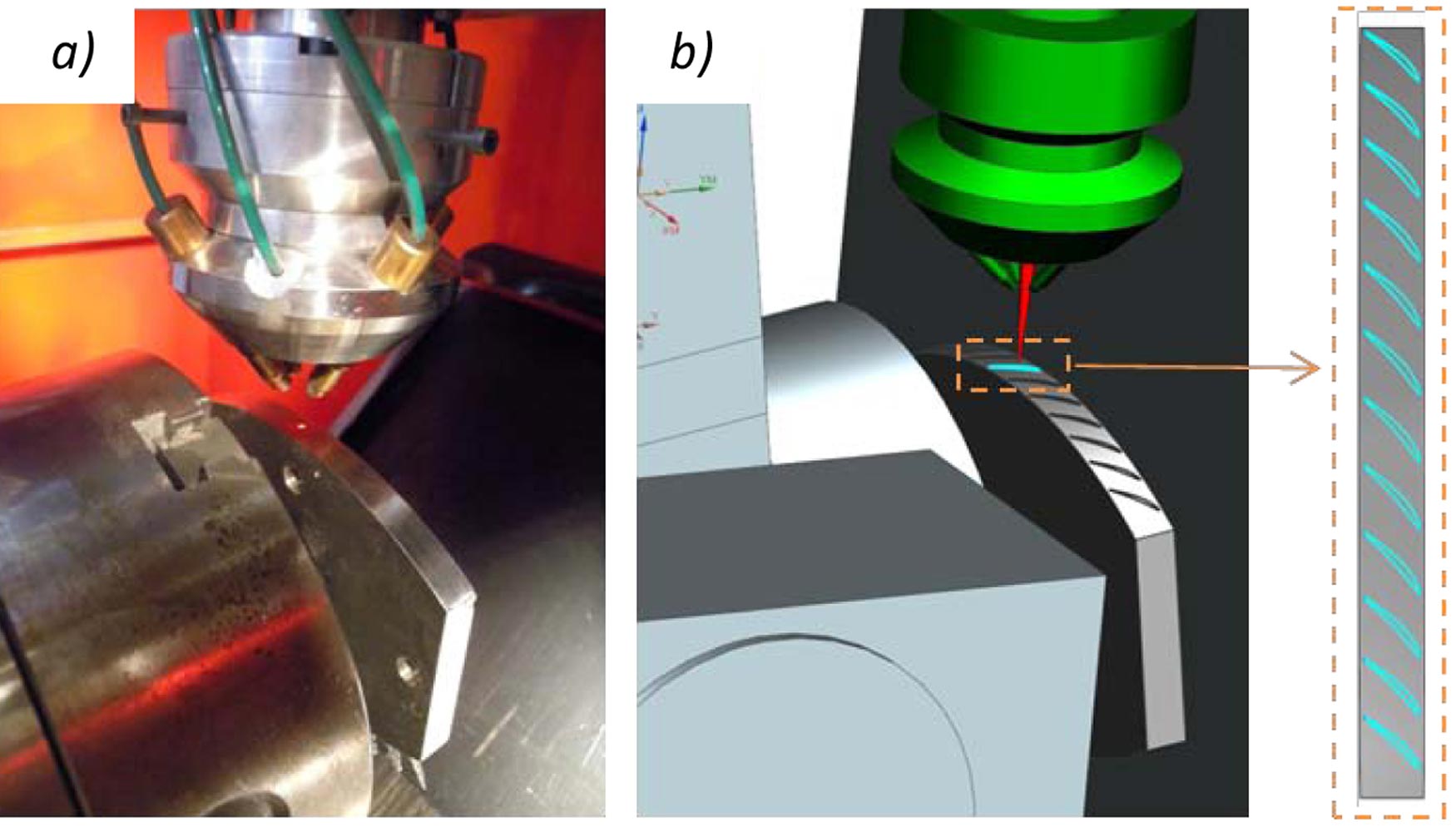
Se establecen una serie de condiciones de aporte (Tabla 4) entre las que se determinara cual es la más apropiada y que por lo tanto proporciona el cordón de mayor calidad. En el proceso de aporte de material mediante láser se utiliza el gas Argón como gas protector y de arrastre siendo el flujo de 13 y 5,5 l/min respectivamente. Tanto el material de aporte como el material base corresponde a la aleación base niquela Inconel 718.
Material base |
Material aporte |
Potencia (W) |
Avance (mm/min) |
Flujo polvo (g/min) |
Nº pasadas |
Δz (mm) |
Altura teórica (mm) |
Inconel 718 |
Inconel 718 |
200-400-600 |
100-200-300 |
6,3-7,4 |
3 |
0,2 |
0,6 |
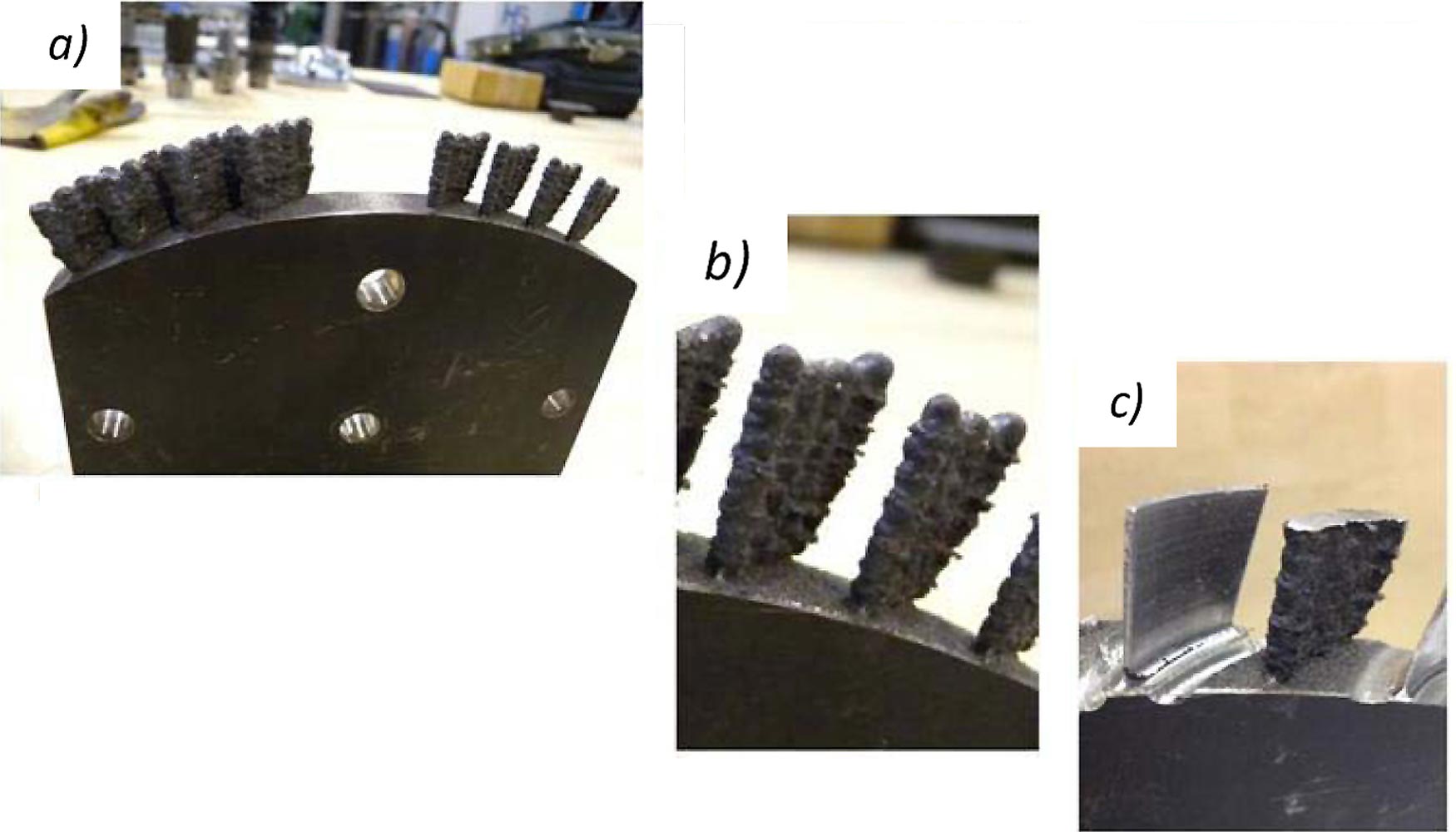
4. Evaluación de la estructura metalúrgica de las piezas fabricadas por aporte
Una vez realizadas las pruebas para la base de los álabes, se han diseñado las estrategias de aporte para la fabricación directa de los álabes completos del blisk. Se diseñan unas trayectorias en espiral cada 0,2 mm hasta completar los 18mm de altura del álabe.
Para la fabricación directa de álabes blisk (figura 5) es necesario aportar capa a capa cada uno de los álabes. Así, es necesario que todos los álabes vayan creciendo al mismo nivel ya que de otra forma el hecho de que se fabrique un álabe, generaría un obstáculo para fabricar el siguiente y podría provocar una colisión entre el álabe recién fabricado y la boquilla de aporte. Se programan las estrategias con una velocidad de avance de 200 mm/min, una potencia del cabezal de 400 W y un flujo de polvo de 9,4 g/min. En este caso, el material base es Inconel 718 que ha sido fresado para conseguir la curvatura del blisk y el material de los álabes es Inconel 718 polvo.
4.1. Análisis macroestructural
Es necesaria la realización de un análisis macroestructural de la zona aportada. En la Figura 5 se pueden observar superficies aportadas homogéneas (figura 5a y 5b). En la figura 5c se puede observar como algunos aportes presentan grietas debidas a la falta de unión entre las diferentes capas depositadas en forma de V.
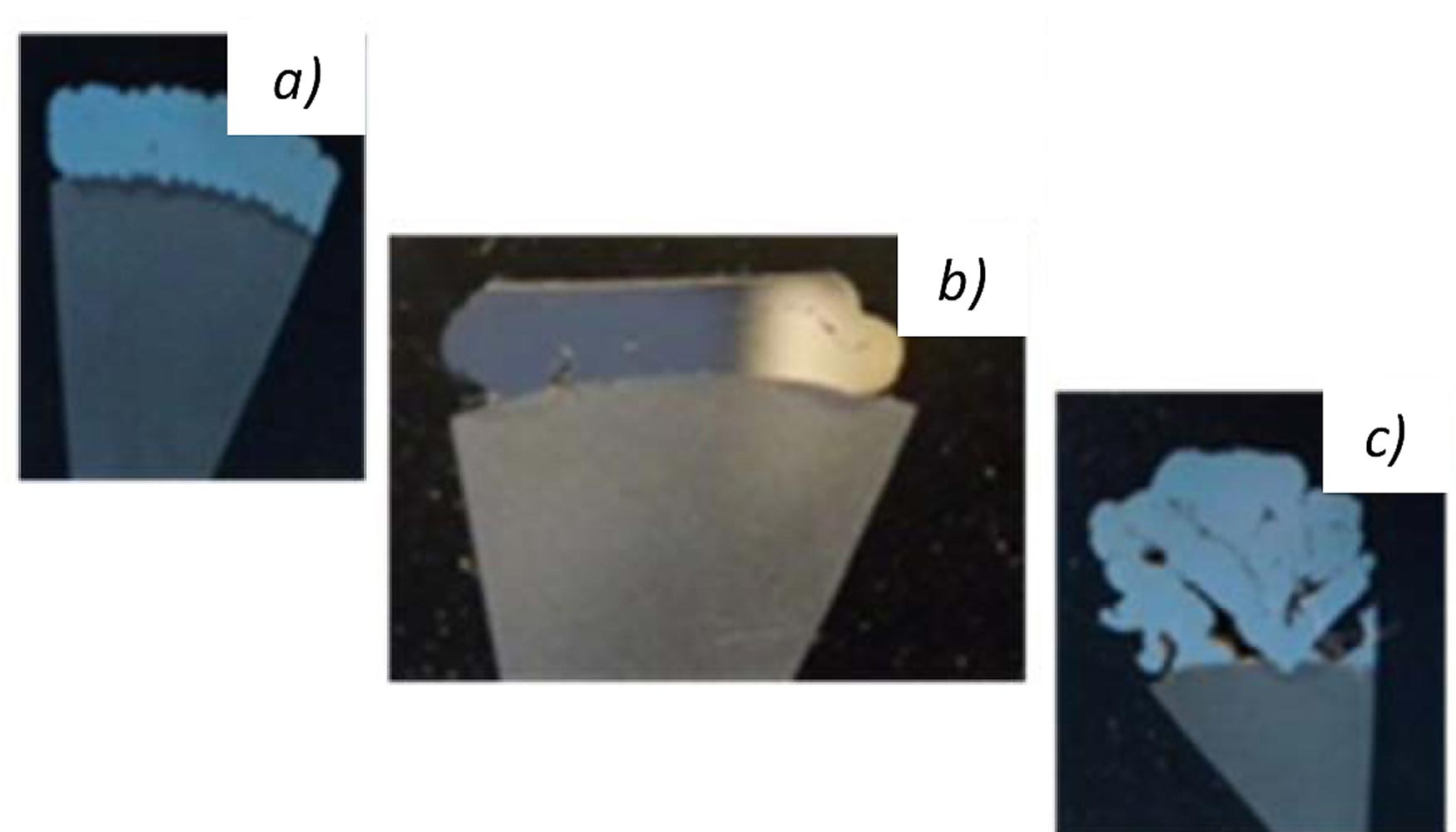
5. Criterio ponderado
5.1. Análisis microestructural
Tras observaciones macroscópicas preliminares se realiza un estudio microscópico de las superficies para la identificación de grietas (Figura 6a), zonas sin aportar o defectos generados en el sustrato (Figura 6b) o poros (Figura 6c). El estudio microscópico es una herramienta útil para la determinación de cuál es la estrategia de aporte óptima basándose en la ausencia de defecto (Figura 6d) o la mínima cantidad de defectos encontrados en la pieza aportada.
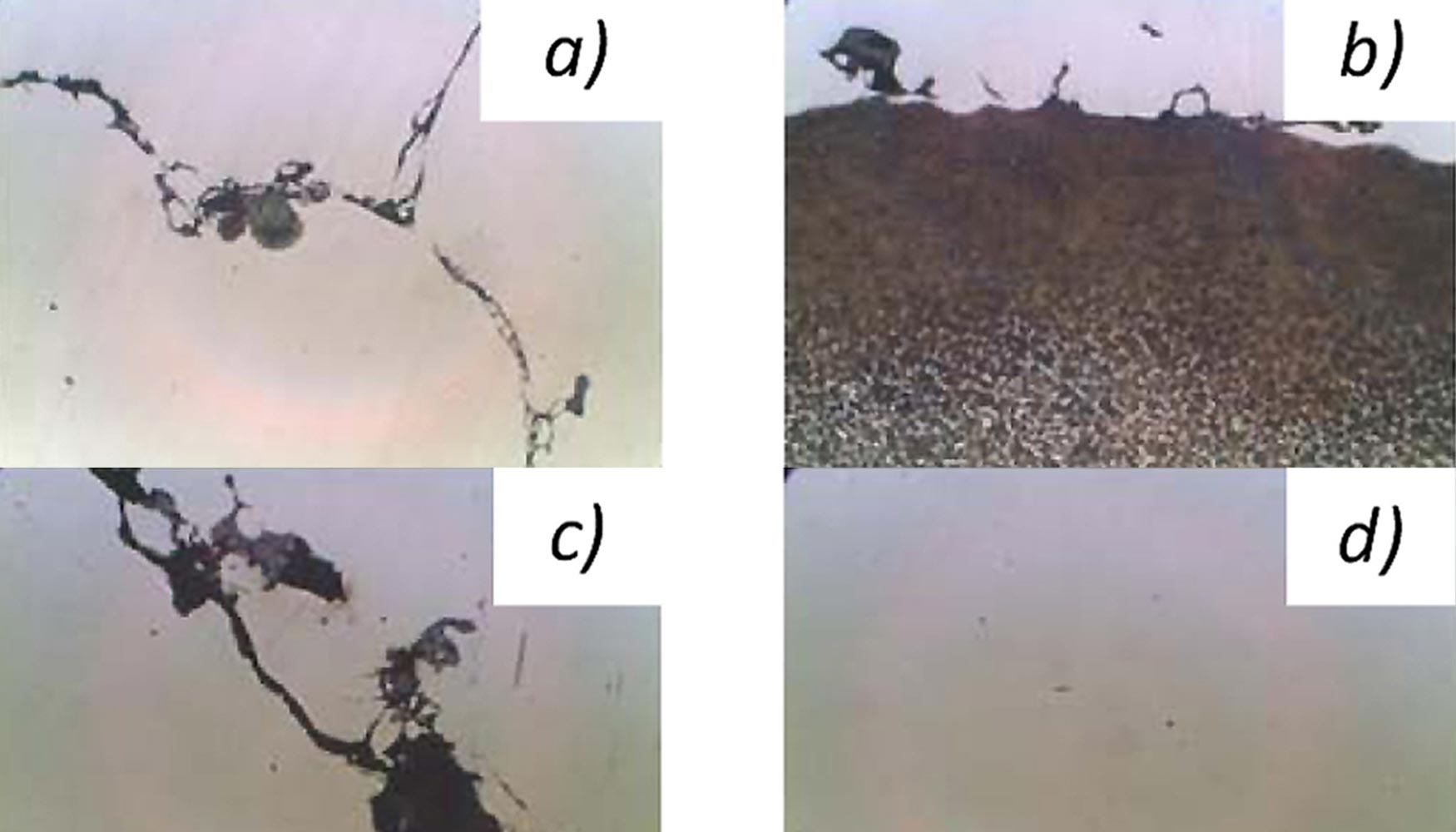
Para la elección de los parámetros óptimos se ha utilizado un criterio ponderado a partir de los resultados obtenidos tras la medición de los cordones aportados. Se han tenido en cuenta cuatro valores-factores para el cálculo del valor ponderado de optimización (δop). En primer lugar se utiliza la tasa de aporte (TA) que es un indicativo de la productividad del proceso y se calcula como la sección media del cordón multiplicada por la velocidad de avance del proceso. En segundo lugar, se tiene en cuenta la variación de la altura (Δh) y anchura (Δa) del cordón respecto a la media medida. Por último, el criterio de optimización utiliza el ángulo de mojado (θ), que es el ángulo que forma la base del cordón con el sustrato y muestra la capacidad de llevar a cabo un solapamiento entre cordones de calidad. Para poder introducir los valores en el criterio de evaluación todos estos valores se escalan a la unidad según la ecuación 1.
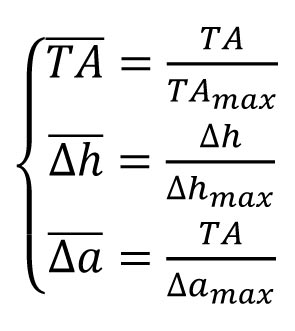
En cuanto al ángulo de mojado, éste se calcula a través de la ecuación 2 utilizando los valores de altura (h) y anchura (a) medios medidos. Para su ponderación, sólo se tienen en cuenta los valores comprendidos en el rango de 0°-80°, ya que fuera de este rango el solapamiento es defectuoso. Posteriormente, se establece 40° como valor óptimo del ángulo de mojado y se le asigna un valor escalado de 1. Los demás ángulos de mojado van tomando valores linealmente hasta los límites donde el valor escalado es de 0.
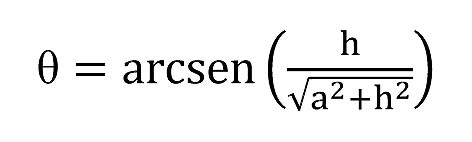
Una vez obtenidos los valores escalados, se obtiene el valor ponderado de optimización a través de la ecuación 3. En esta ecuación se le da mayor importancia a la tasa de aporte por lo que se asigna un peso de 0,7. Otro aspecto a tener en cuenta es el ángulo de mojado al que se le da un peso de 0,3. Por último, la variación en altura y anchura tiene un efecto negativo en el proceso por lo que aparecen minorando el criterio de optimización con unos pesos de 0,2 y 0,1, respectivamente. La razón por la que a la variación de anchura se le otorga un efecto menor es que ésta puede ser subsanada en gran medida mediante el solapamiento de cordones, mientras que la variación en altura puede provocar más fácilmente aportes defectuosos.. Es importante recalcar que los valores de ponderación pueden adaptarse a diferentes criterios (maximización de altura, maximización de la uniformidad de los cordones, …).

6. Algoritmo velocidad de aporte constante
Como se ha visto a lo largo de este trabajo, un problema relativamente frecuente en los aportes de material láser en 5 ejes está relacionado con la dificultad de mantener una velocidad de avance constante en el cabezal de aporte. Con el objetivo de dar solución a este problema mecatrónico se propone un algoritmo para lograr mantener la velocidad de aporte constante.
6.1. Descripción del algoritmo
El objetivo del algoritmo es mantener constante a lo largo de la trayectoria de deposición de material la velocidad de avance. En la práctica, el algoritmo modifica una nueva velocidad de avance en cada bloque del programa para finalmente obtener una velocidad resultante constante a lo largo del programa a pesar de las limitaciones de los ejes presentes en el proceso.
En primer lugar el algoritmo toma dos bloques consecutivos de programa y calcula la distancia Δr que tienen que recorrer tanto los ejes lineales (Δx, Δy, Δz) como rotativos (ΔB and ΔC) entre las coordenadas de un bloque y del siguiente. De esta forma la distancia entre dos bloques consecutivos cumple la ecuación (Ecuación 4).
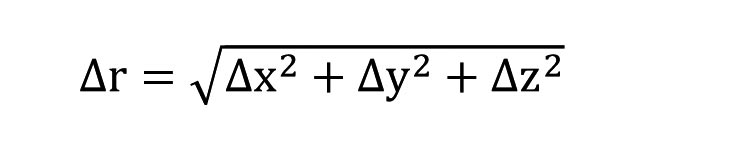
En segundo lugar, se calcula la velocidad de los ejes X, Y, y Z como la proyección de la velocidad de avance en cada eje a través de los cosenos directivos que se calculan a su vez teniendo en cuenta la distancia Δr y los incrementos en los ejes X, Y y Z (Ecuación 5).
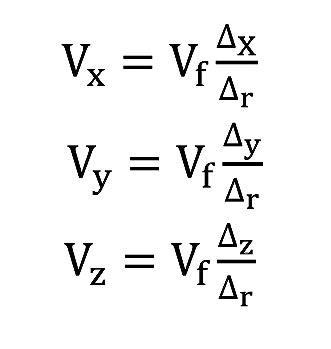
En tercer lugar, se calcula el tiempo que necesita cada eje de la máquina para alcanzar la posición deseada considerándose de igual valor para los tres ejes lineales por un tema de simplicidad (Ecuación 6).
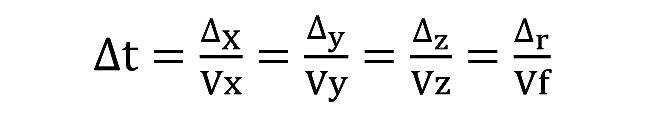
A continuación, se calcula la velocidad de rotación de los ejes B y C como función de Δt e indirectamente como función de la velocidad de avance programada en la punta del cabezal de aporte de material (Ecuación 7).
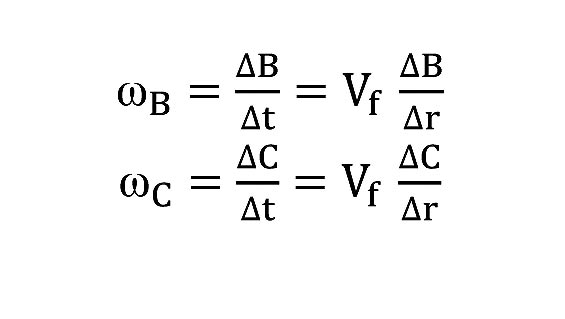
En caso de que se produzca una limitación en uno de los ejes rotativos y no sea posible alcanzar la velocidad ω necesaria para mantener la velocidad de avance programada constante en el intervalo de tiempo Δt, el control de la máquina reduce la velocidad de avance. En el caso del ejemplo mostrado en la Figura V. 23, la limitación del eje rotativo C provoca que se le asigne a ese eje un valor de la velocidad igual al módulo de la velocidad de avance, esto es, si ωC>Vf, entonces se reescribe la velocidad del eje rotativo C como ωC’ =Vf. Cuando se produce este cambio, para poder mantener la sincronización en el movimiento de los 5 ejes, se reduce la velocidad de avance siendo la nueva velocidad Vf’ (Ecuación 8).

A fin de poder dar solución a este problema, el algoritmo planteado detecta si el módulo de la velocidad de los ejes rotativos es mayor que la velocidad de avance programada para el movimiento entre dos puntos consecutivos. En los bloques de programa en los que ωC>Vf, se programa una velocidad mayor Vf’’ igual al módulo de la velocidad ωC, siendo Vf’’=ωC.
Finalmente, cuando el control de la máquina lee alguno de los bloques en los que se han realizado cambios y detecta que la nueva velocidad rotativa programa ωC’’ es mayor que el módulo de la velocidad de avance programada, Vf’’, realiza el siguiente ajuste: ωC’’=Vf’’=ωC. Como consecuencia del ajuste, la velocidad decrece proporcionalmente hasta el valor de Vf’’’, de acuerdo con la ecuación (Ecuación 9). Como resultado, la velocidad de avance mantiene el valor de la velocidad de avance programada Vf, y los correspondientes valores para Vx, Vy, Vz, ωB y ωC.
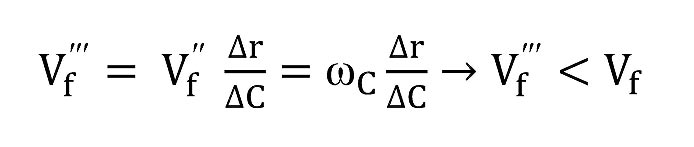
7. Remecanizado
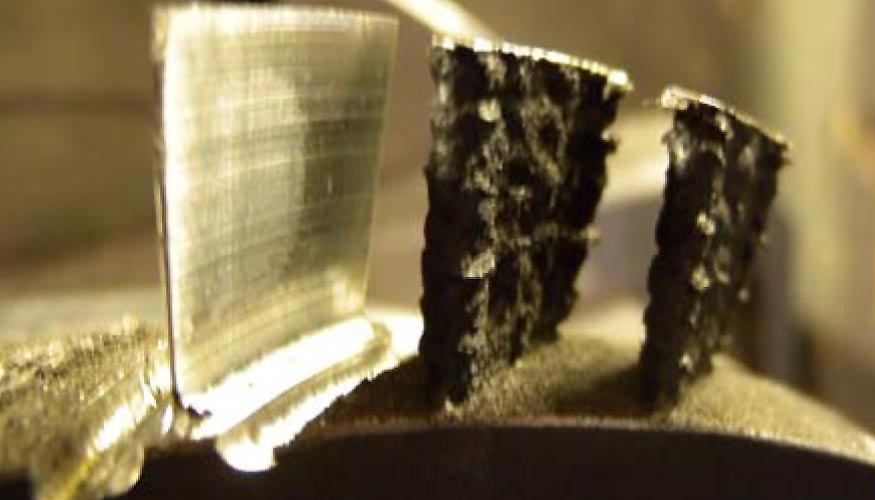
El proceso de aporte de material llevado a cabo para cualquiera de sus aplicaciones, bien sea reparación de una zona de la pieza, recubrimiento o fabricación directa, es un proceso de tipo ‘near to net shape’. Es decir, sea cual sea la aplicación del proceso de aporte láser se logra una geometría aproximada a la forma final siendo necesario remecanizar la superficie tratada para lograr las dimensiones y la calidad de la superficie requerida por la pieza final (Figura 7). En términos cuantitativos, las tolerancias del proceso de aporte láser oscilan entre 0,2 mm hasta varios milímetros en función del tipo de láser, sistema de aporte y condiciones empleadas. En cualquier caso, son tolerancias muy lejanas a las que se pueden obtener en procesos de mecanizado y que normalmente no cumplen los requisitos demandados en las piezas sometidas a estudio. La solución industrial a este problema se basa en aportar un volumen mayor de material sobre la geometría que se desea construir y, posteriormente, aplicar un proceso de mecanizado para obtener la precisión y acabado superficial demandado. En cualquier caso, la capa de material mecanizado suele ser inferior a un milímetro, siendo lo habitual mecanizar espesores de 0,2-0,3 milímetros.
8. Verificación virtual del proceso de aporte
Una etapa ya integrada en la actualidad dentro del proceso de mecanizado es la etapa de verificación virtual. En esta etapa se verifica el proceso de mecanizado a nivel de posibles colisiones, altas tasas de arranque de material, acabado superficial de la pieza, optimización de velocidades y movimientos en vacío. En este campo son varios los softwares comerciales disponibles. Algunos ejemplos son Vericut o el propio NX que en las últimas versiones incorpora un módulo de verificación virtual del proceso de mecanizado. De esta forma, es posible trabajar con el mismo software en todas las etapas de fabricación de una pieza: Diseño, mecanizado, verificación virtual del proceso de mecanizado, postprocesado, etc.
En el caso concreto del proceso del aporte láser no existe actualmente un software capaz de simular el propio proceso de aporte. Por este motivo, en este trabajo se ha integrado el centro de aporte láser en un software de verificación virtual de aplicación de procesos de mecanizado para realizar la verificación virtual del proceso de aporte. Si bien es cierto que, en este caso, el objetivo principal de la integración del centro de aporte en este software es la comprobación de posibles colisiones. La verificación virtual del proceso de aporte (Figura 8) es necesaria dada la cantidad de elementos que intervienen en el propio proceso (cabezales de aporte, utillajes, escáner…) y las posibilidades de colisión existente entre ellas mismas. Además, para garantizar la perpendicularidad del haz láser, es necesario realizar la operación de aporte en 5 ejes. La complejidad de la trayectoria implica que las posibilidades de colisión entre los diferentes elementos sea muy alta y es por ello por lo que la simulación virtual permite una previsualización rápida de los movimientos de la máquina y observar la ausencia de colisiones.
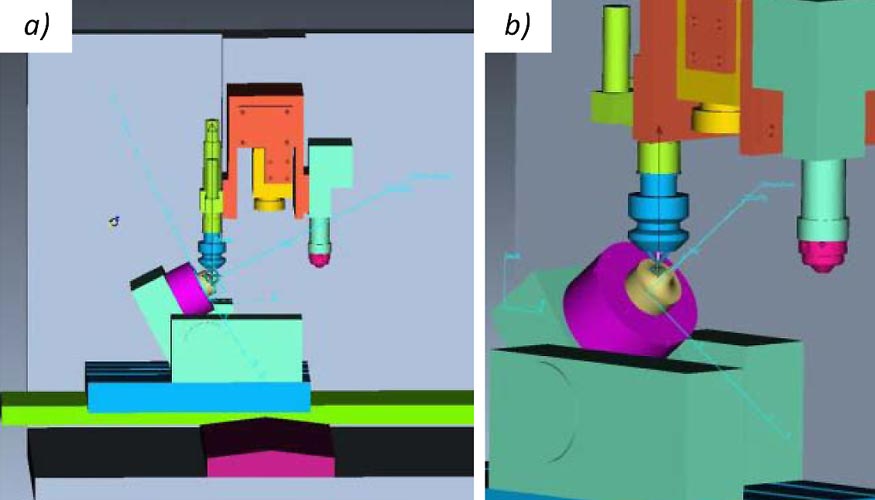
En este trabajo se ha integrado el centro de procesado láser Aktinos 500 tanto en el software de simulación virtual Vericut (Figura 8) como en Siemens NX 8.5 (Figura 9a). La información obtenida es similar en ambos softwares, sin embargo NX permite realizar la verificación virtual del proceso de mecanizado en el propio software de CAD/CAM mientras que la utilización de Vericut obliga a un cambio de software para la esta comprobación final del proceso de mecanizado.
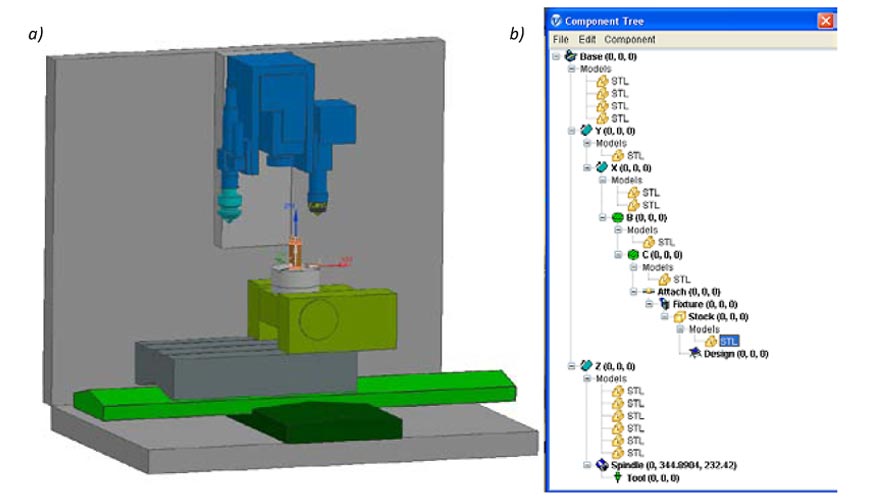
9. Conclusiones
El estudio experimental realizado determina los parámetros y estrategias más influyentes en la calidad del aporte realizado. El estudio se ha llevado a cabo para diferentes materiales, geometrías y aplicaciones (reparación, recubrimiento, fabricación directa) utilizados en los sectores objetivos a los cuales está enfocado el proceso. Para la búsqueda de dichos parámetros óptimos se ha utilizado un criterio ponderado a partir de los resultados obtenidos experimentalmente.
Por otro lado, dadas las limitaciones de la mecatrónica de los sistemas utilizados para el aporte por láser dan lugar a variaciones de la velocidad de avance del cabezal programada, se aplica un algoritmo con el objetivo de mantener la misma constante.
Además, se ha evaluado la idoneidad del proceso de aporte láser en aplicaciones industriales a través de la fabricación de una serie de piezas tipo para demostrar la validez del proceso en aplicaciones industriales reales.
Finalmente se realiza una verificación virtual del proceso de aporte mediante láser: Se ha realizado tanto la programación de las estrategias de aporte en 5 ejes como la verificación virtual del proceso de aporte a partir de un software comercial inicialmente diseñado para procesos de mecanizado.
Agradecimientos
Este trabajo se ha realizado gracias a la financiación de la Universidad del País Vasco UPV/EHU mediante la UFI 11/29 y por el Ministerio de Industria y Competitividad en el proyecto DPI2013-46164-C2-1-R titulado “Implantacion de una solucion integral para la fabricacion y reparacion de componentes de turbo maquinaria para propulsion aerea y produccion de energia (Turbo)”.
Referencias
[1] Sexton L., Lavin S., Byrne G., Kennedy A. (2002) Laser cladding of aerospace materials, Journal of Materials Processing Technology.
[2] Jeng J-Y., Lin M-Ch. (2001) Mold fabrication and modification using hybrid processes of selective laser cladding and milling, Journal of Materials Processing Technology, 110, 98-103.
[3] Pinkerton A.J. (2007) An analytical model of beam attenuation and powder heating during coaxial laser direct metal deposition, Journal of Physics D: Applied Physics, 40, 7323-7334.
[4] Tabernero I. (2013) Optimización del proceso de aporte por láser mediante la predicción de la geometría del recubrimiento generado, Tesis Doctoral, Dpto. de Ingeniería Mecánica, Escuela Superior de Ingeniería de Bilbao, UPV/EHU.
[5] Lin J. (1999) Concentration mode of the powder stream in coaxial laser cladding, Optics & Laser Technology, 31, 251-257.
[6] G. Chryssolouris, S. Zannis, K. Tsirbas, C. Lalas (2002) An experimental investigation of laser cladding, CIRP Annals-Manufacturing Technology, 51-1, 145-148.
[7] de Oliveira U., Ocelík V., De Hossom J.Th.M. (2005) Analysis of coaxial laser cladding processing conditions, Surface & Coatings Technology, 197, 127-136.
[8] Cao X., Jahazi M., Fournier J., Alain M. (2008) Optimization of bead spacing during laser cladding of ZE41A-T5 magnesium alloy castings, Journal of Materials Processing Technology, 205, 322-331.
9] Emamian A., Corbin S.F., Khajepour A. (2010) Effect of laser cladding process on clad quality and in-situ formed microstructure of Fe-TiC composite coatings, Surface and Coatings Technology, 205, 2007-2015.
[10] Ren L., Sparks T., Ruan J., Liou F. W. (2008) Process planning strategies for solid freeform fabrication of metal parts, Journal of Manufacturing Systems, 27-4, 158-165.
[10] Eiamsa-ard K., Nair H. J., Ren L., Ruan J., Sparks T., Liou F. W. (2005) Part Repair using a Hybrid Manufacturing System, SFF Symposium, 425-433.
[11] Ruan J., Eiamsa-ard K., Liou F. W., Engineering A. (2005) Automatic Process Planning and Toolpath Generation of a Multiaxis Hybrid, Journal of Manufacturing Processes.