Control del 100% de la producción de piezas en el sector eólico con sistema de escaneo
1. Objetivo del estudio
El objetivo del proyecto es generar un demostrador que cumpla la necesidad de la medición del 100% de las cotas en el total de la producción con la suficiente fiabilidad para el control total de la producción.
2. Ensayos
Las pruebas realizadas han sido las siguientes. Primero se hizo un estudio previo de la mejor tecnología a usar, para lo cual se desplazó una pieza tipo a las instalaciones de Trimek, y ahí se hizo el estudio previo. A continuación, decidida cual era la tecnología más adecuada a este caso, se pasó a la instalación de la misma en la zona de fabricación de la pieza para realizar el análisis de la mejor solución para este desarrollo.
2.1. Análisis de pieza en instalaciones de Trimek
La pieza tipo sería un portasatélites [1]. Se trata de una pieza que forma parte de los molinos de viento, la cual hace girar las palas.
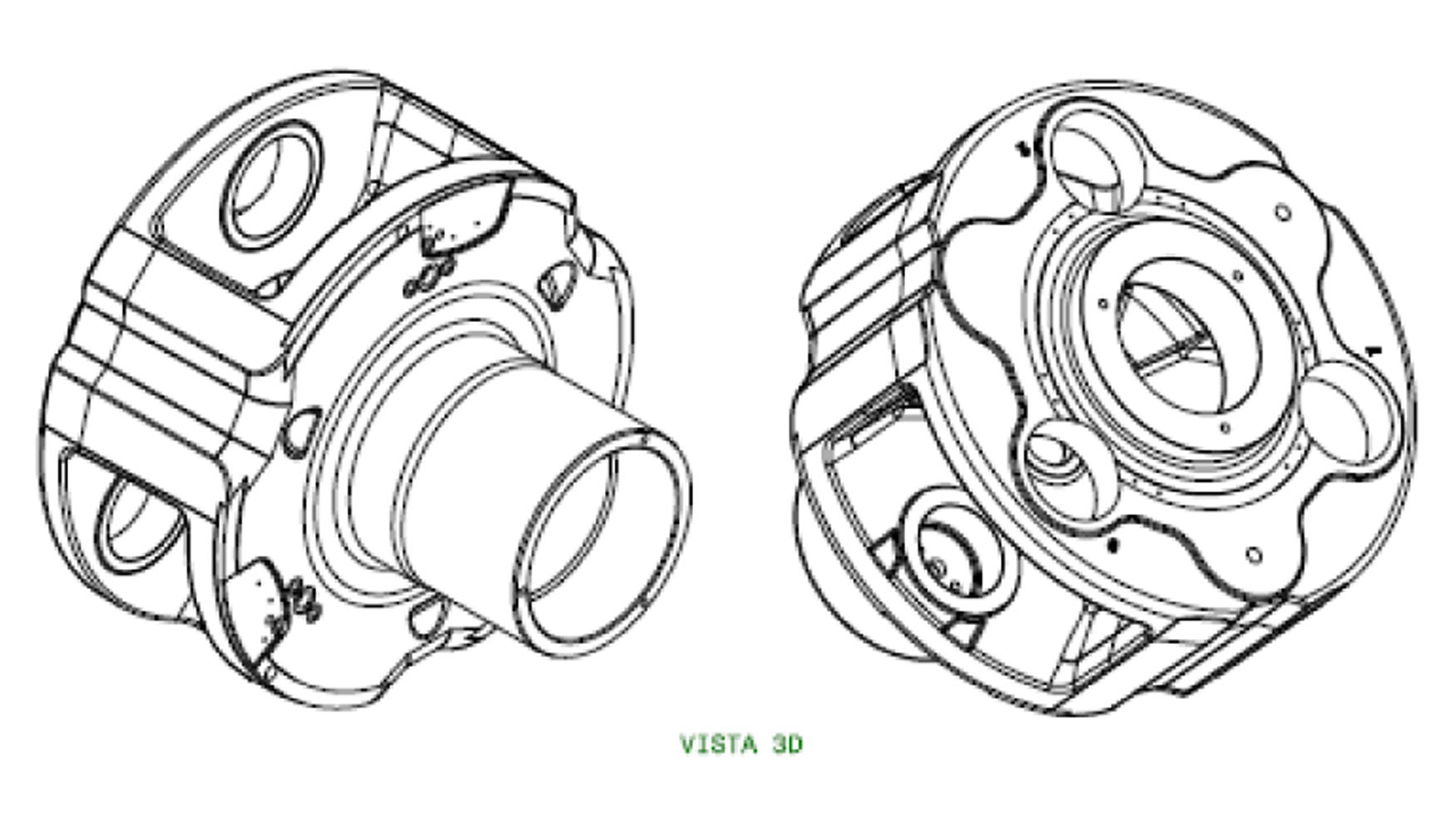
Debido a la necesidad de una reducción de tiempos en la obtención de la medición, se optó por un sistema óptico en detrimento de un sistema por contacto; que es lo utilizado hasta el momento. Dentro de la sensórica, se usó uno de triangulación activa de línea, el cuál agrupaba los dos requerimientos: precisión y velocidad. Este tipo de sensores están formados por un láser de luz estructurada, el cual generará un haz de luz. Esta luz es reflejada por el objeto de la superficie captándose en la cámara. [2]
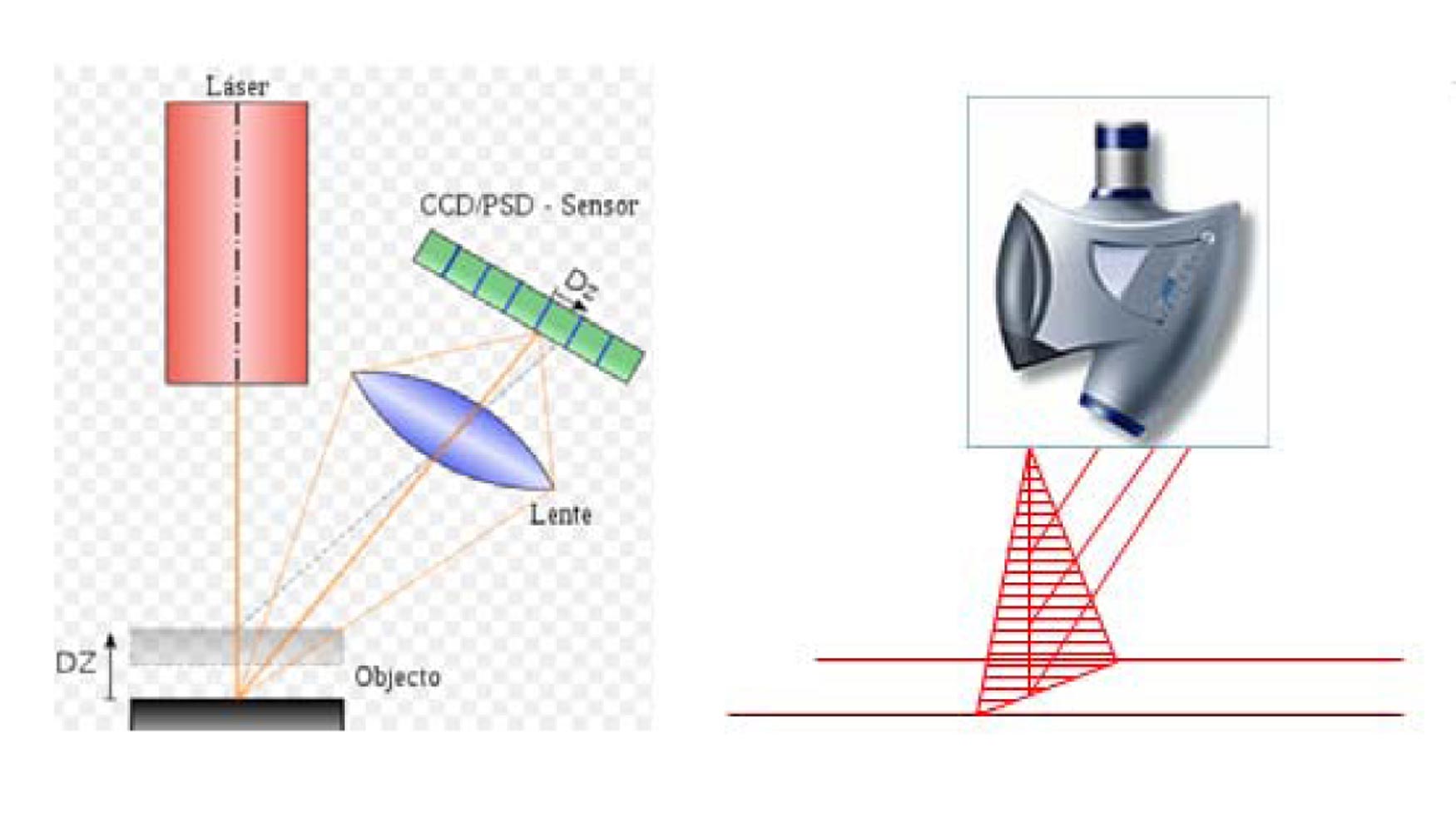
Las características técnicas del sensor elegido, el Optiscan 1040 L Standard, son: peso de 400 g, campo de visión máximo de 42 mm, distancia de trabajo de 93 mm, resolución mínima lateral de 30 micras, seguridad del láser ClassII, error de escaneo 4 micras y adquisición de puntos 60.000 puntos/s. Una vez seleccionado el láser con el que se va a trabajar, es necesario seleccionar el sistema óptico, es decir, que tipo de máquina va a usar este laser. En este caso se seleccionó una máquina de medir por coordenadas de tipo puente, más concretamente una Gantry [3], debido a la alta precisión de este tipo de máquinas cuando se van a medir piezas de medio tamaño. Estas máquinas tienen unas precisiones entre 1 y 10 micras.
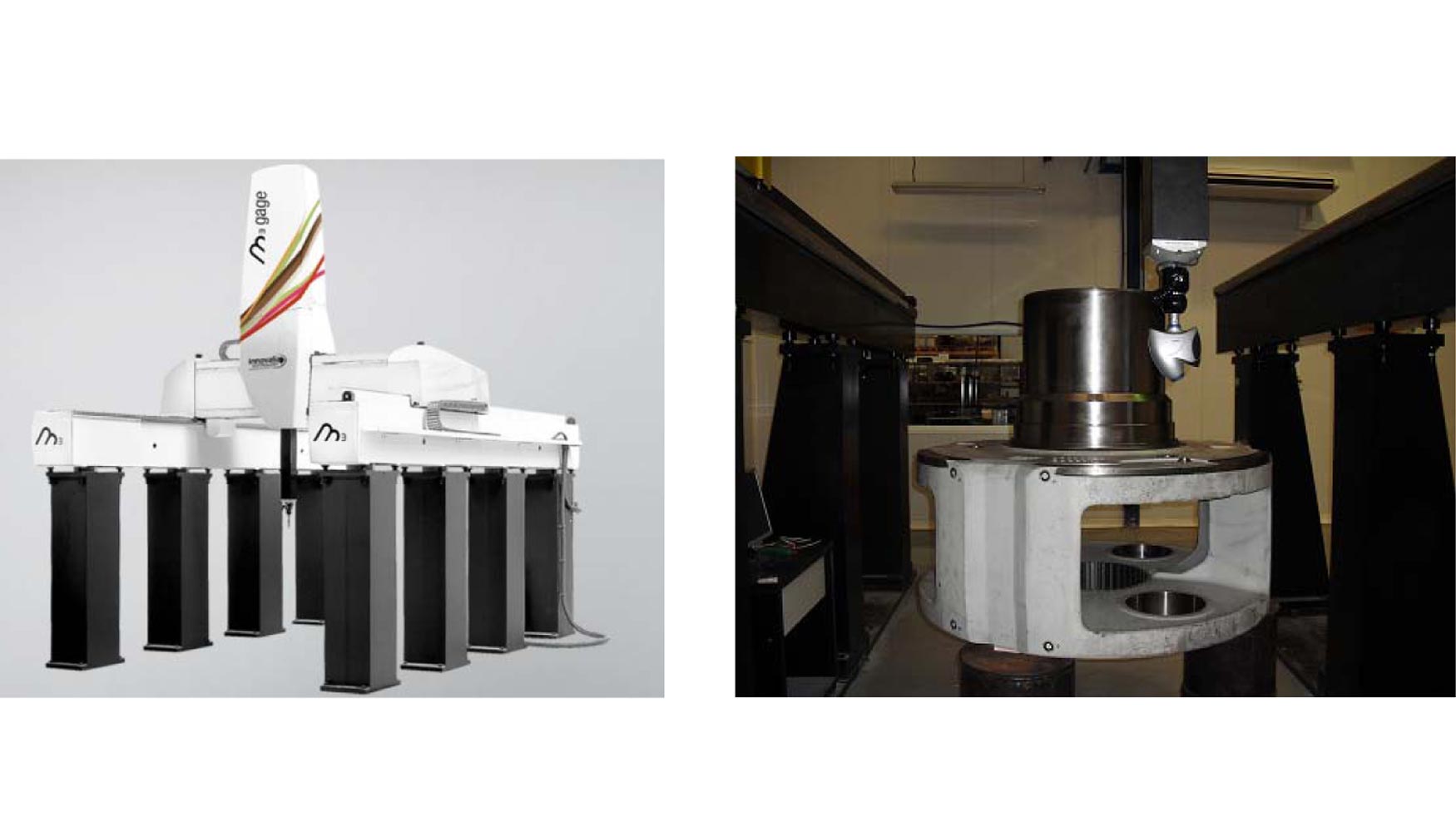
Eligiendo este sistema óptico lo que se pretendía era averiguar si este laser era capaz de recoger toda la información de la pieza y con la calidad suficiente. En esta pieza surgieron dos problemáticas cuando se escaneaba; por un lado la accesibilidad a la pieza y por otro la precisión de la pieza escaneada debido al tipo de superficie (mecanizada). Para tener acceso a toda la pieza se tuvo que escanear la pieza en dos partes. Es decir, una según la imagen [3] y otra girada 180 grados. Para enlazar las dos digitalizaciones se usaron unas referencias en común. Para la digitalización correcta de la superficie, se tuvo que ir programando la pieza, modificando los parámetros de captura del sensor óptico. En concreto existe un parámetro, que es el tiempo de exposición, que consiste en ajustarse dependiendo de cuanta luz refleja la superficie. De esta forma, se consiguió de una forma automática que la nube de puntos [4] extraída sería de una calidad adecuada para la medición.
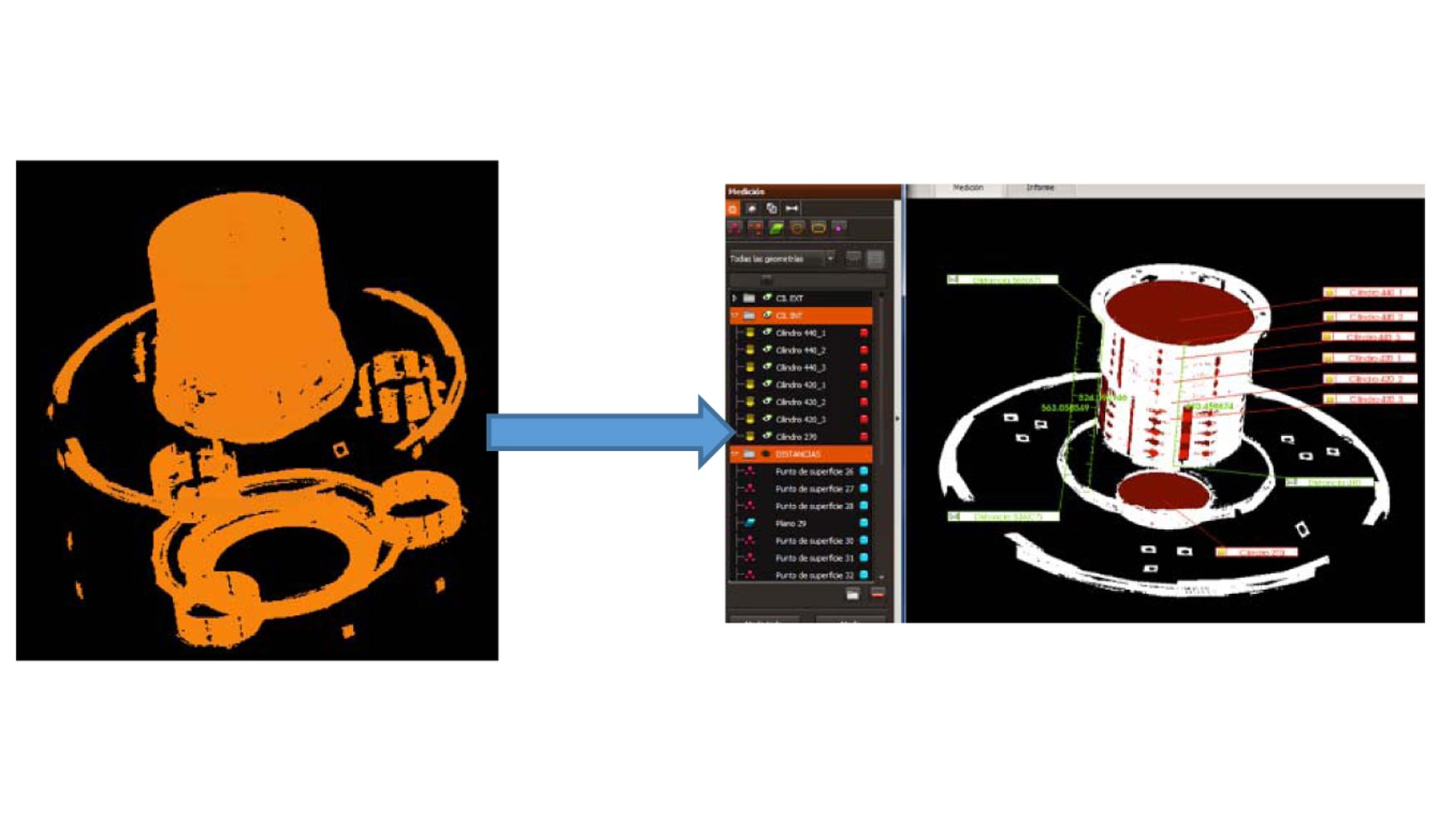
2.2. Análisis de pieza en instalaciones del fabricante de pieza
Para conseguir la medición del 100% de la producción, se debía realizar una instalación lo más cerca de la línea de producción. De forma que fuera el propio usuario del torno quien realizase el proceso de medición de la pieza.
Debido a esto, se descartó la máquina puente; la cual está diseñada para trabajar en laboratorio, y se optó por una máquina tipo brazo [5] diseñada para trabajar a altas velocidades y en entornos de producción. Su principal característica es que trabaja con husillos, por lo que le da una mayor velocidad y además le afectará en menor medida la suciedad del ambiente que en el caso de las máquinas que se desplazan a través de colchones de aire. Estas máquinas tienen unas precisiones entre 10 y 100 micras, dependerá del volumen de trabajo. Si se compara con las precisiones que nos da una máquina de puente, son peores. Pero, en conjunto lo que se va a estudiar es si este tipo de máquinas nos van a dar unas mayores prestaciones para la búsqueda de la solución más adecuada en este caso.
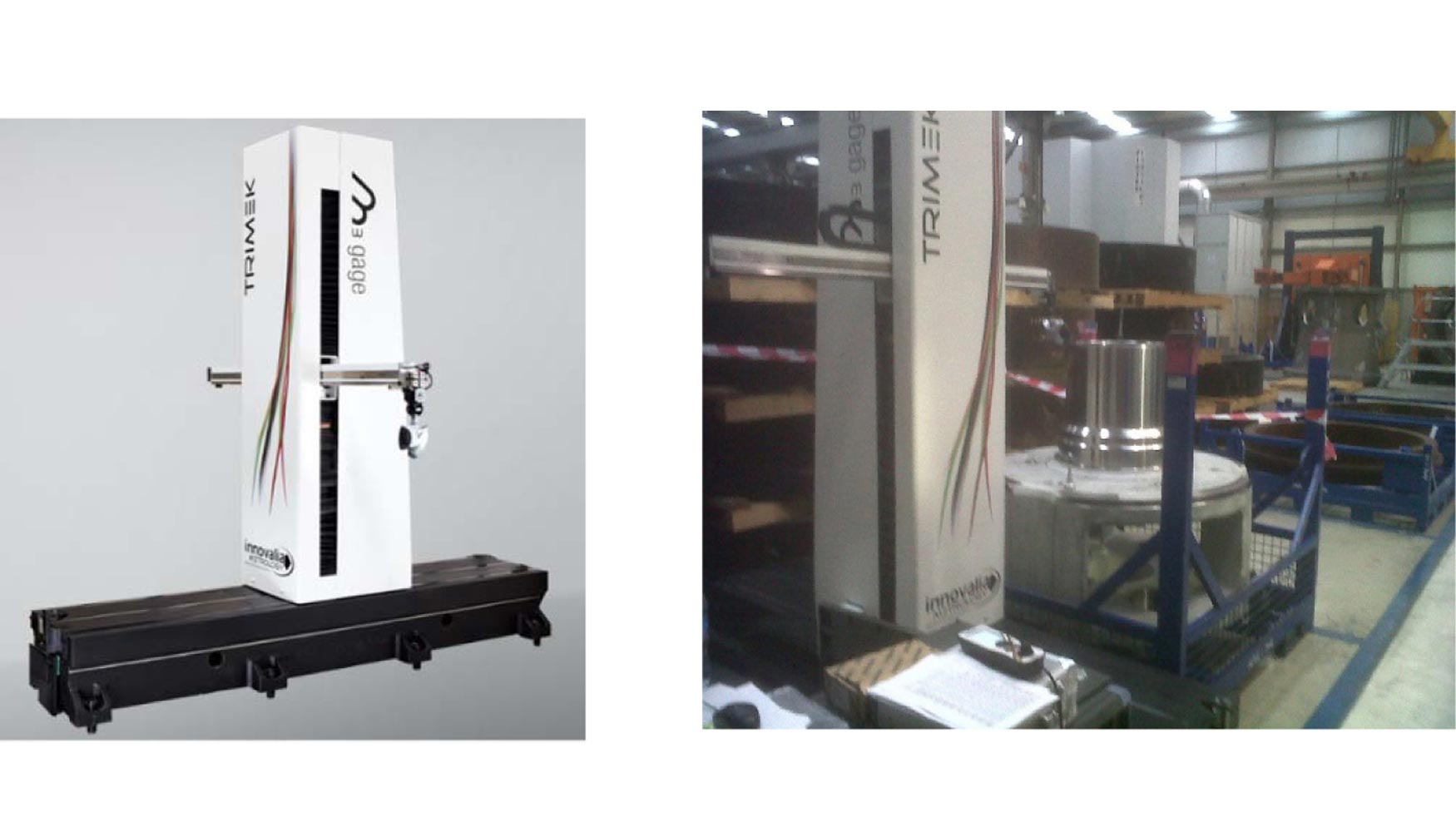
Las geometrías que se iban a medir eran: diámetros, paralelismos, tolerancias de posición, concentricidades y distancias. Las tolerancias de algunas de estas geometrías eran las indicadas en la siguiente tabla [6].

Como se indica en la tabla, estas tolerancias son bastantes restrictivas; por lo que el primer punto a tratar era en cuanto repetían estas mediciones en las condiciones del proceso. En un laboratorio el control de los diferentes factores son más fáciles de controlar. Pero la realidad es que cada vez se tiende más a realizar el control de la producción in-situ. Existen diferentes efectos ambientales que hay que tenerlos en cuenta a la hora de un escaneo, algunos podremos disminuir su efecto y otros habrá que asumirlos. Los factores ambientales más importantes a tener en cuenta son: la temperatura, la suciedad, las vibraciones del suelo y las vibraciones debido al ruido. Los primeros ensayos que se realizaron fueron los de la repetibilidad del sistema óptico con la pieza a testear, es decir, un ciclo normal de medición. Digitalizado por un lado de la pieza, giro de la pieza y digitalizado por el otro lado de la pieza.
Se obtuvieron resultados por debajo de las 17 micras, lo cual no era suficiente, ya que se buscaban unas repetibilidades por debajo de las 10 micras. Aunque para las tolerancias vistas con anterioridad no sería suficiente, si se puede conseguir un control más óptimo del proceso si se cumple esta condición.
Como mejoras al proceso de medición se propuso fijar el útil de fijación de la pieza al suelo [7] y la automatización del tiempo de exposición, ya que se detectó que existían una serie de focos en el entorno que hacían que las condiciones externas variaran a lo largo del proceso.
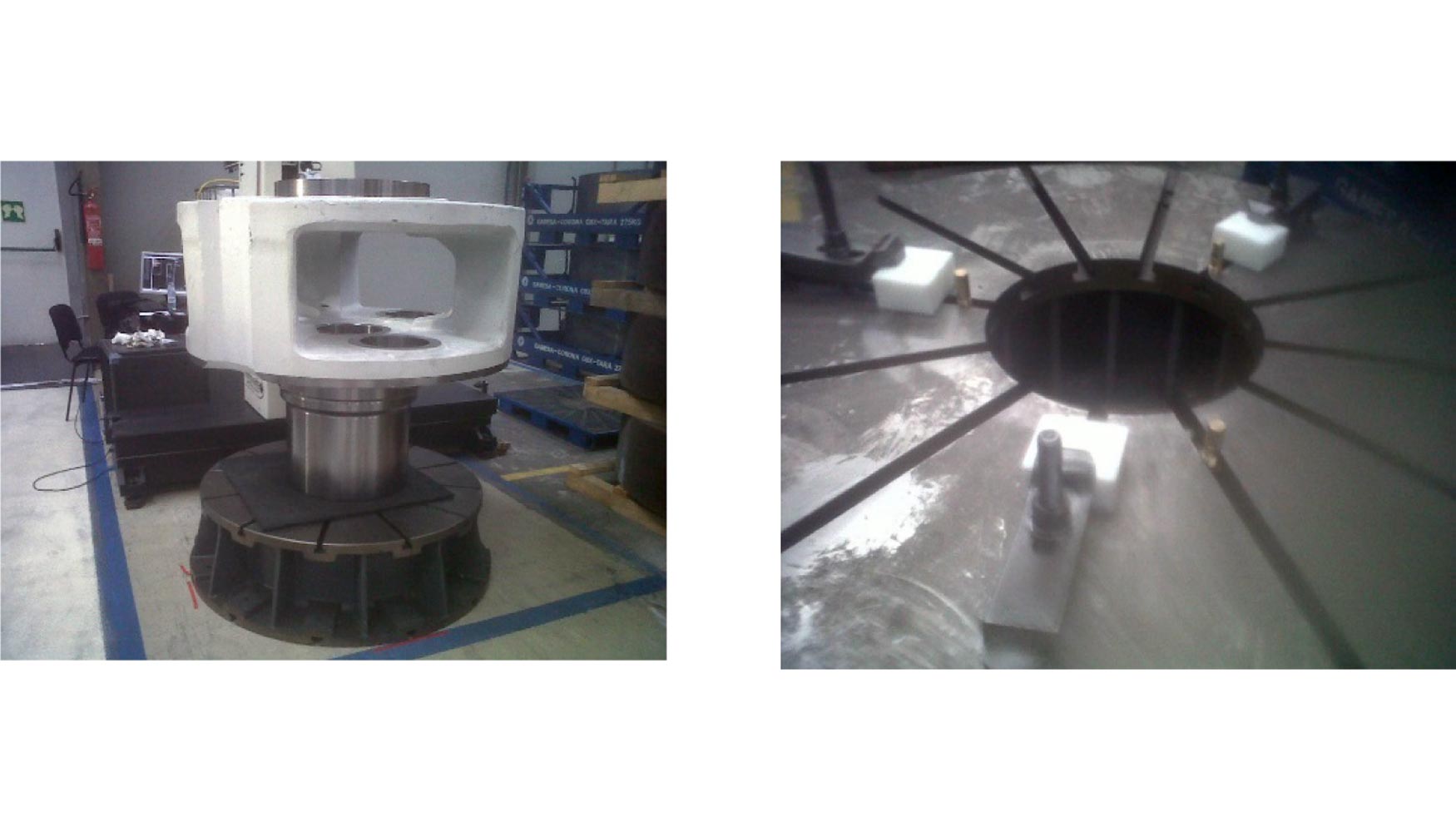
Una vez realizadas estas modificaciones en el proceso, se volvió a realizar los ensayos, cumpliendo esta vez sí, las mediciones una repetibilidad por debajo de las 10 micras.
2.3 Asistente en el proceso de medición
Una vez definido el proceso de medición se necesitaba una asistencia para el usuario de este sistema. El operario que estaba a pie de máquina es el que iba a realizar el control de calidad, es decir, no era una persona con conocimientos previos de este tipo de sistemas de metrología. Para esto se desarrolló una asistente [8] que iba indicando de una manera sencilla lo que se tenía que hacer para la medición: qué pieza se iban a controlar y la colocación de las mismas.
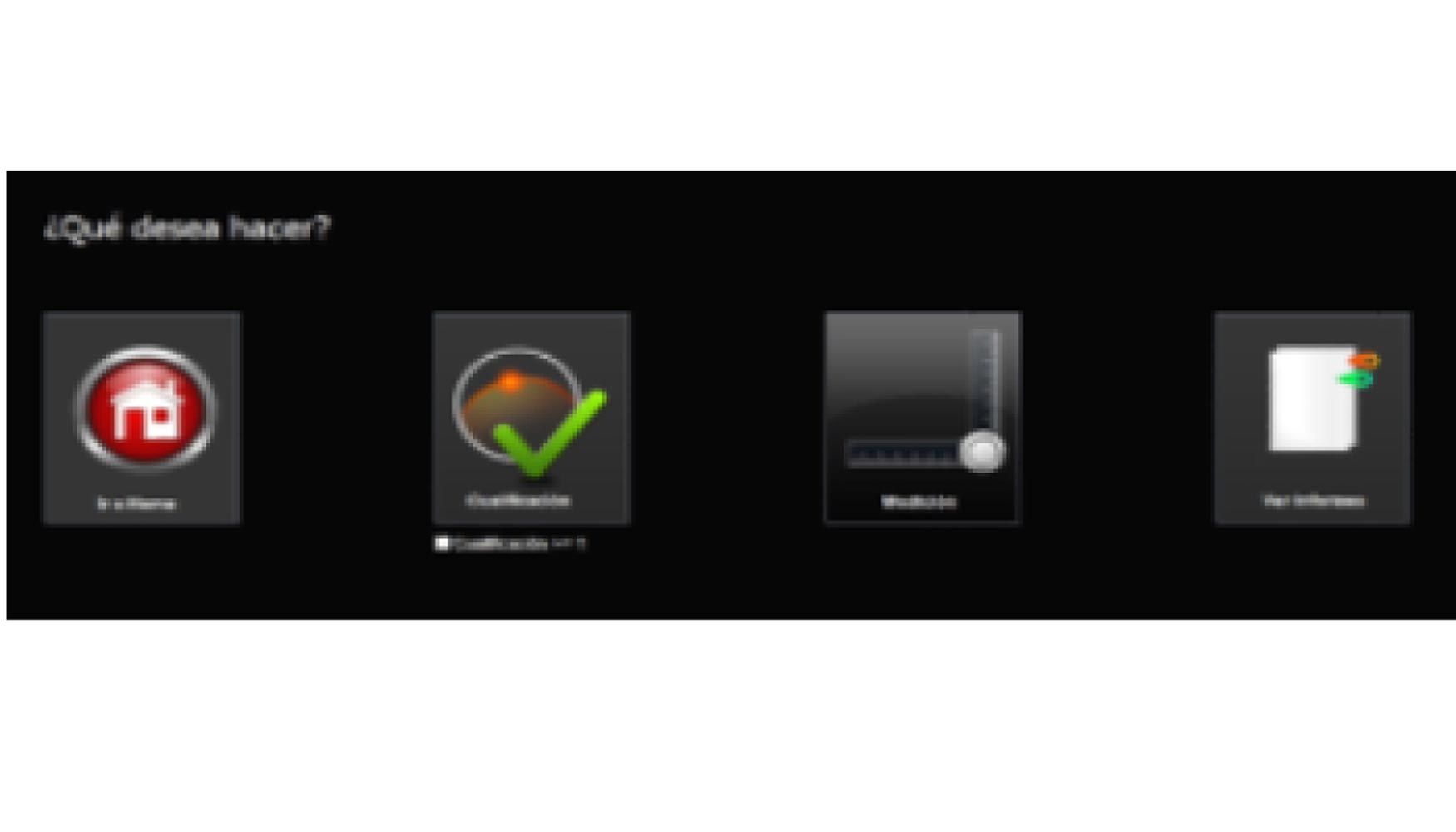
Conclusiones
Con este demostrador se ha conseguido la instalación de un sistema que es capaz de controlar un 100% de la producción con la precisión suficiente como para tener una idea clara de calidad de todo el proceso.
Para llegar a este punto, las claves han sido la utilización de un sistema óptico y la utilización de un asistente. Ambas mejoras nos van aportar una velocidad del análisis de la calidad.
Analizando el punto al que se ha llegado, se está estudiando posibles mejoras del proceso para optimizar aún más en tiempos y en precisiones. De esta forma se podrían chequear piezas de otras máquinas. Algunas de estas mejoras sería: la manipulación automática de la pieza, colocación de antivibratorios de más alta calidad, etc.