Escáner láser 3D para ingeniería inversa, pruebas y control dimensional
Tras realizar un análisis minucioso del mercado, Spring srl decidió adquirir un brazo de medición articulado CNC de 7 ejes y un escáner láser digital de Nikon Metrology. El equipo no solamente permite que las piezas de los clientes de Spring se digitalicen rápidamente y con precisión para la ingeniería inversa y la impresión en 3D sino que además incrementa enormemente las capacidades del departamento de control de calidad de la división. Con él se pueden medir piezas grandes además de pequeñas con el brazo portátil MCAx, el cual lleva un escáner láser 3D ModelMaker. La adquisición de ambos elementos de Nikon Metrology asegura una compatibilidad perfecta y significa que Spring puede confiar en un proveedor individual para asistencia y servicio. La opinión del proveedor fue inestimable en los primeros días para proporcionar experiencia en las aplicaciones, ya que la tecnología era nueva para Spring. Roberto Toniello, cofundador de la empresa y jefe del Departamento de Ingeniería explica: “El equipo de Nikon nos permite cumplir de manera más eficiente con las necesidades y demandas de nuestros clientes, de tal forma que podemos ofrecer un servicio más integrado, global y preciso en plazos más cortos y asegurar una fiabilidad máxima de los resultados”.
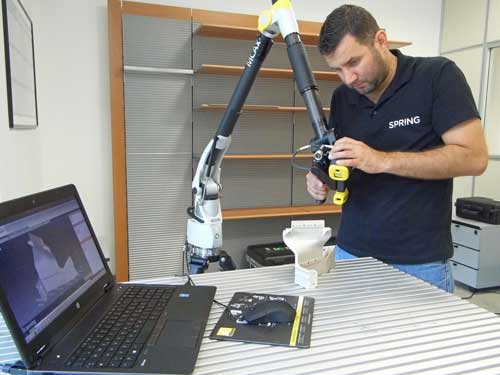
Aplicación de la ingeniería inversa como la introducción para la fabricación aditiva
Si un producto necesita ser reproducido pero el modelo de CAD no existe o la pieza original se ha modificado, es necesario aplicar la ingeniería inversa a un componente real. El procesado de los datos de digitalización se lleva a cabo por parte de la oficina técnica de Spring que utiliza Geomagic Studio, el cual importa la nube de puntos original adquirida al utilizar el software Focus Handheld de Nikon Metrology. A los datos de la nube de puntos se les aplica la ingeniería inversa dentro de una superficie precisa, polígono y modelos de CAD nativos. Estos se exportan a uno de los 10 asientos CAD de Spring de Pro Engineer y Unigraphics NX, donde los archivos STL se generan para accionar seis máquinas de fabricación aditiva Stratasys Fortus FDM (modelado por deposición fundida) en el lugar. Dos son impresoras grandes en 3D con volúmenes de producción de 900 x 600 x 900 mm, convirtiendo a Spring en una de las pocas empresas italianas que pueden producir objetos de ese tamaño por medio de FDM (modelado por deposición fundida). Las máquinas producen componentes partiendo de materiales termoplásticos, capa por capa. Estos van desde ABS estándar a través de ASA resistente a la intemperie hasta Ultem 9085, un material ignífugo con una relación alta de resistencia-peso certificado para el uso aeroespacial. También es ideal para el sector naval, Fórmula Uno y otras aplicaciones del deporte del motor.

Spring srl utiliza la tecnología de impresión 3D FDM para producir apoyabrazos de uso final en un número de aeronaves. Permite a la empresa reducir su tiempo de servicio en un 66% y los costes en un 50% en comparación con los métodos tradicionales tales como el mecanizado con CNC.
Control de calidad incrementado de las piezas impresas
Una vez que las piezas se han construido, se inspeccionan utilizando el equipo de digitalización con objeto de determinar su precisión, utilizando tanto el escáner láser como un palpador de contacto intercambiable, o ambos en una rutina de medición combinada. El software de Nikon Metrology proporciona el entorno de medición y análisis, con herramientas intuitivas tanto para las aplicaciones de láser como las de digitalización por contacto. El escáner se utiliza, de hecho, para dos tercios del tiempo como herramienta de metrología. Los datos del control de calidad recogidos se comparan analíticamente en la pantalla con el archivo de CAD original, tanto si es suministrado por el cliente como si se deriva de la ingeniería inversa. Cualquier característica que esté fuera de tolerancia se puede observar y medir. Las comparaciones pieza a pieza se pueden realizar similarmente para determinar la reproducibilidad de un proceso de producción. El software Focus de Nikon Metrology soporta estas actividades, gestionando las nubes de puntos adquiridas, realizando las comparaciones, llevando a cabo la inspección avanzada de los elementos y produciendo informes. Es fundamental para Spring controlar con precisión la calidad de los componentes de esta manera para verificar la precisión de las piezas y para generar los informes corroborativos para sus clientes exigentes.
El sector aeroespacial y la F1 en particular requieren un completo seguimiento de la producción desde la materia prima pero fue difícil para Spring proporcionar ese nivel de servicio antes de que su metrología propia se hubiera incrementado. Un área particular de crecimiento es la provisión de los núcleos termoplásticos impresos en 3D solubles, los cuales se utilizan por parte de sus clientes del sector aeroespacial y del deporte del motor para producir estructuras compuestas laminadas.
Apreciación de la importancia de la fabricación aditiva
Spring se estableció en 1998 por Fabio Gualdo y Roberto Toniello con objeto de combinar su experiencia en el diseño de componentes y moldes con la tecnología de fabricación aditiva emergente. Fueron de los primeros en reconocer que les permitiría la personalización a gran escala de los productos hechos a medida de acuerdo con los deseos de los clientes, como una alternativa a la producción en serie. Hoy en día, la división de investigación, diseño y desarrollo sirve a ambos extremos del mercado, fabricando prototipos y lotes de componentes por medio de la impresión en 3D, mientras que además diseña y suministra moldes para la inyección de plástico y la fundición a presión para ciclos de producción más largos.
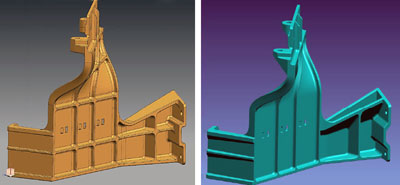
Una guía de cable para una aeronave modificada e impresa en Ultem 9085 por Spring srl utilizando la tecnología FDM (derecha) y la versión en aluminio original (izquierda). El peso se redujo en un 60%, mientras que se ahorraron tanto costo como tiempo. El escáner de Nikon Metrology se utilizó para ayudar en el rediseño y para controlar la fabricación de la pieza.
Los clientes italianos suponen el 80% del negocio de la empresa mientras que el resto se extiende a través de otros países europeos. Fabio Gualdo, cofundador de Spring comenta: “En la fabricación aditiva en serie a menudo es necesario optimizar el diseño de un componente. Una pieza prevista originalmente a realizar por medio de procesos de eliminación de viruta tiene que ser, frecuentemente, completamente remodelada, especialmente si es un material nuevo, para proporcionarle las características mecánicas requeridas o para reducir el peso”. “Un buen ejemplo es nuestra fabricación reciente de una pieza de helicóptero en termoplástico Ultem 9085, en lugar del aluminio de calidad aeroespacial utilizado anteriormente. La fabricación tradicional requería un tiempo de servicio de cuatro a seis semanas y un coste de alrededor de 500 euros por pieza. Esto se ha reducido a la mitad por medio de la impresión en 3D y la escala de tiempo también se ha reducido en una tercera parte”.
La necesidad de la actualización de la metrología
En cuanto a la necesidad de la actualización de la metrología, Gualdo explica que durante los últimos años él y sus colegas habían sentido la necesidad de ofrecer a los clientes la capacidad de producir piezas de forma más compleja. Sin embargo, los métodos manuales de medición de la empresa utilizaban los equipos de metrología tradicionales y las limitaciones significativas, de aquí el despliegue o la implementación del brazo de medición digital de Nikon Metrology. Y añade: “De todos los proveedores que examinamos, Nikon Metrology ofreció el mejor producto en términos de especificaciones y servicio técnico. El brazo MCAx, a diferencia de una máquina de medición de coordenadas, es conveniente para transportar y nos permite examinar todos los tamaños de componentes que producimos, hasta los más grandes”. “El escáner láser ModelMaker dispone de la versatilidad para inspeccionar todas las piezas termoplásticas que imprimimos en nuestras instalaciones, además de los componentes que compramos hechos de materiales diferentes. Otros sistemas de digitalizado que investigamos no eran capaces de procesar todos estos materiales, lo cual es el motivo por el que nos decidimos a favor de Nikon Metrology como proveedor”.
Datos de gran calidad a partir de todas las superficies
El rentable y potente escáner láser ModelMaker MMCx, como sucede con los cabezales de nivel más alto de Nikon Metrology, se caracteriza por la adaptación de la intensidad de la fuente del láser, permitiendo que se pueda digitalizar cualquier superficie sin la necesidad de pulverización ni ningún otro pretratamiento. El equipo se caracteriza por una mejora del rendimiento del sensor (ESP3) que evita que el operario tenga que ajustar manualmente los parámetros cuando digitaliza superficies diferentes, incluso aquellas con variación del color, alta reflectividad y transiciones. La cámara digital dispone de una cadencia rápida de digitalizado y ofrece una precisión de medición hasta 24 micras, más que suficiente para inspeccionar las piezas en las instalaciones de Monteviale, las cuales tienen tolerancias de dibujo normalmente hasta 0,2 mm. Además, el escáner tiene una resolución no interpolada verdadera, lo que permite que se puedan digitalizar elementos y superficies de forma libre de manera precisa y eficaz. La anchura de las líneas del láser es de 160 mm y la densidad es de 800 puntos sobre la anchura de la línea. El diseño ligero pero robusto de ModelMaker permite su utilización sin problemas en los entornos de producción y la conexión Ethernet del escáner permite una conexión fácil a un ordenador portátil. El brazo MCAx en el que se monta el cabezal es también ligero, ya que es de una construcción tubular de fibra de carbono que está también equilibrada y estable térmicamente. La rotación infinita de todos los ejes principales contribuye a un funcionamiento sin esfuerzo y los encóderes absolutos eliminan el tiempo de referenciación y calentamiento.
Proceso más rápido para los pedidos de los clientes
Roberto Toniello concluye: “El brazo de digitalización por láser ha hecho una gran diferencia para nuestro negocio. Anteriormente, imprimiríamos en 3D las piezas de un cliente y las subcontrataríamos para la inspección dimensional. Ello llevaba de dos a tres días para que los componentes e informes estuvieran de vuelta”. “Ahora, podemos utilizar fácilmente el brazo de digitalización de Nikon Metrology para comprobar las piezas el mismo día que salen de la máquina de FDM (modelado por deposición fundida), lo que supone un ahorro de mucho tiempo y, obviamente, también un ahorro de mucho dinero”. “Nos permite presupuestar precios más competitivos y además entregar los pedidos de forma más rápida, así que nuestros clientes se benefician por partida doble”. “De forma similar, ahorramos tiempo y dinero en otras áreas, herramientas de inspección, plantillas y dispositivos de sujeción, por ejemplo, además de los moldes de inyección de plástico y fundición a presión”.