Ultrasonidos por láser para la inspección de componentes aeronáuticos en fase de producción
Entre las principales ventajas del composite en el sector aeronáutico está su menor peso en relación a sus propiedades mecánicas, o lo que es igual, cuenta con propiedades especificas superiores gracias a su baja densidad. Naturalmente, esto implica menor consumo de combustible. El CFRP no se oxida, es resistente a la corrosión y, todo ello, unido a su comportamiento a la fatiga, permite disminuir las tareas de mantenimiento. Ambos aspectos, además de reducir el coste a las compañías aéreas, contribuyen a contener el impacto ambiental del transporte aéreo. Pero este material resulta también ventajoso para el confort de los pasajeros. Si se utiliza aluminio como material estructural principal, la humedad dentro del avión debe mantenerse a un 10% como máximo. Gracias al nuevo material, la humedad en cabina en el Boeing 787 puede aumentarse hasta casi un 50%. Esto crea un ambiente mucho más agradable para los pasajeros.
Considerar estas ventajas ha llevado a que, en la actualidad, más del 50% del peso estructural del A350 y del B787, y entre el 30-37% de los nuevos modelos de Embraer y Bombardier, sean de material compuesto.
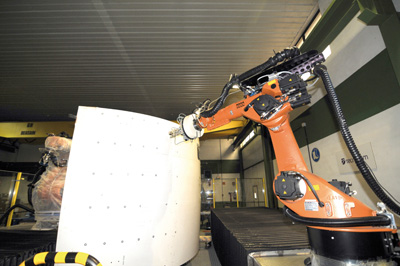
El crecimiento del consumo de composite, en la industria aeroespacial, se ha concretado en que las 1.000 toneladas del año 1984, en la que se inició su aplicación para estructuras primarias en aviones comerciales, subieran a 7.250 toneladas en el año 2010. Las previsiones actuales con la fabricación del A350, B787 y los nuevos modelos de otros fabricantes estiman una demanda de 18.100 toneladas para el año 2019. Naturalmente, hay que considerar que, unido a la tendencia a incrementar el volumen de composite en las diferentes aeronaves, se prevé un crecimiento de su volumen de fabricación anual. Ante este panorama de uso creciente del composite, considerando que todos los componentes estructurales fabricados en este material deben ser examinados mediante ultrasonidos, y que el coste de esta operación supone, en algunos casos, hasta el 30% del total de su fabricación, comprenderemos la importancia y el significado de la evolución tecnológica que este proceso de inspección está experimentando.
La inspección mediante Ensayos No Destructivos (END), y especialmente con ultrasonidos (UT) es una necesidad ineludible en dos situaciones de la vida del componente estructural: al finalizar su fabricación, para garantizar su integridad y calidad, y durante su vida en servicio, para detectar daños incipientes derivados del uso de la estructura.
La inspección inicial debe garantizar la integridad estructural del componente, o lo que es lo mismo, la ausencia de defectos originados durante el proceso de fabricación. Verificar el correcto encolado entre partes, la ausencia de porosidades y de despegamiento entre telas o del revestimiento respecto al núcleo en el caso de estructuras sándwich, es el objetivo principal de la inspección. Cubrir el 100% del volumen del componente con la necesaria sensibilidad, garantizando la detección, caracterización, dimensionamiento y localización de los posibles defectos, es el desafío a cubrir en esta actividad. Más tarde, durante la vida en servicio del componente, será preciso aplicar técnicas de inspección capaces de detectar nuevos defectos surgidos por el uso y las solicitaciones mecánicas a que se somete la estructura, tales como impactos y grietas o el crecimiento de defectos pre-existentes, aceptados dentro de los límites permisibles de diseño. Si nos centramos en el proceso de fabricación, tenemos que hablar del método de ultrasonidos. Esta inspección se aplicaba, inicialmente, de forma manual, de manera que la calidad y fiabilidad de la inspección descansaba únicamente en la pericia y experiencia del operador. Aún, en ocasiones, por el tamaño y complejidad geométrica de algunos componentes se sigue haciendo de esta forma.
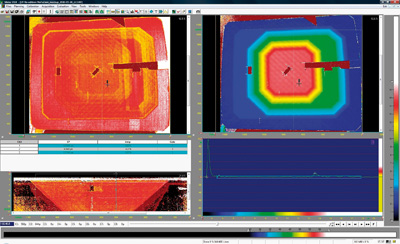
Todos los fabricantes, ante la demanda creciente de aviones, se encuentran inmersos en proyectos de integración de la cadena de suministro y de industrialización de los procesos de fabricación. Lógicamente, se requiere de la inspección mayor automatización, ejecución en línea e integración con otros procesos. Un primer paso muy importante en la automatización de la inspección fue, hace ya algunos años, la aplicación de técnicas de transmisión (en general mediante chorros de agua que facilitan el paso de los ultrasonidos a través de la pieza). Estos sistemas utilizados intensamente en la fabricación del A320, aunque ya más sofisticados que los inicialmente diseñados, han quedado en los nuevos programas limitados a su uso para estructuras sándwich, puesto que el avance importante más reciente consiste en la aplicación masiva de la técnica de pulso-eco.
Si el programa A380 fue el que incorporó el pulso-eco, la incorporación del Phased Array en el A350, como base para la aplicación de esta técnica, ha supuesto un gran avance en el proceso de automatización, que puede ahora realizarse a mayor velocidad, reduciendo tiempos y costes. Simultáneamente, se han sustituido los viejos sistemas cartesianos, como los del tipo gantry, por los que incorporan robots industriales que cuentan con una mayor flexibilidad.
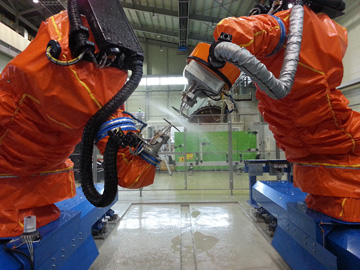
La automatización necesaria está llegando a todas las fases del proceso de inspección, desde el reconocimiento de la pieza y su posición, definición del plan y recorrido de la exploración hasta la evaluación automática de los resultados, pasando por la calibración ultrasónica y el almacenamiento de datos.
Finalmente hay que señalar lo que aparece como el futuro de la aplicación de la inspección por ultrasonidos para composite: los ultrasonidos generados por láser. Si bien esta tecnología viene aplicándose en EE.UU. (Lockheed Martin) desde hace ya algunos años, lleva poco tiempo, disponible para otros fabricantes. Los ultrasonidos por láser (LUS) incorporan ventajas muy significativas especialmente al considerar componentes de pequeño tamaño y geometría compleja, que, todavía en muchos casos, sólo pueden inspeccionarse manualmente. Los sistemas LUS, además de automatizar la inspección y garantizar la disponibilidad de un registro de los datos obtenidos, elimina el agua requerido en técnicas convencionales como acoplante acústico y la necesidad de un contacto físico del elemento auscultador con la superficie de la pieza a inspeccionar. En los sistemas tradicionales, ya fueran para la aplicación de técnicas de transmisión o de pulso eco, los ultrasonidos deben introducirse en la pieza a inspeccionar una vez generados en un elemento piezoeléctrico exterior. Para ello, hay que asegurar el acoplamiento mediante el chorro de agua o el contacto húmedo, mientras que en los sistemas basados en LUS los ultrasonidos se generan en la pieza que es excitada con un rayo láser. Si consideramos que el ángulo de incidencia del láser admite un gran margen de variación, puede entenderse las posibilidades que esta tecnología abre para el futuro de la inspección en los procesos de fabricación en material compuesto.