Técnicas metalográficas para la caracterización morfológica de la viruta en el mecanizado de aleaciones ligeras de uso aeronáutico
La industria aeronáutica ha experimentado en las últimas décadas un desarrollo exponencial a nivel nacional, situándose España entre los principales países europeos tanto en nivel de producción como de generación de empleo. A pesar de esta buena situación, los continuos retos tecnológicos a los que se enfrenta esta industria, unidos a la fuerte competencia a nivel internacional, obligan al desarrollo de nuevas estrategias que refuercen la competitividad de este sector. De este modo, uno de los factores claves radica en la mejora del rendimiento de los procesos de fabricación utilizados en esta industria, desde un punto de vista funcional, económico, energético y medioambiental.
Otro factor importante que se enfrenta el sector aeronáutico es la innovación en la fabricación de aeronaves más eficientes, precisándose el desarrollo de nuevos materiales alternativos en los que destacan las aleaciones ligeras (de aluminio y titanio principalmente), debido a sus cualidades de baja densidad y excelentes propiedades mecánicas. Estas propiedades hacen que sean muy utilizadas en la fabricación de componentes estructurales para aeronaves. En su fabricación se suelen utilizar distintos procesos de conformado, siendo el mecanizado uno de los más empleados. El estudio y optimización de estos procesos suele ser complejo, dado el gran número de variables que intervienen. En este sentido, el análisis de la morfología de la viruta obtenida durante el mecanizado suele ser un factor de especial relevancia, dada su relación con otros factores que afectan de forma notable al rendimiento del proceso, como el desgaste de la herramienta de corte o la integridad superficial de la pieza mecanizada. Este análisis adquiere una mayor relevancia en procesos de mecanizado que utilizan técnicas con bajo impacto medioambiental, como es el caso del mecanizado en seco. Bajo estas condiciones, las temperaturas alcanzadas en la zona de corte son muy elevadas, dando lugar a fenómenos de incorporación de material mecanizado a la herramienta que alteran la morfología de la viruta y que a veces dificultan su evacuación. Por ello, la monitorización y control de la viruta es un aspecto a tener en cuenta en la mejora del rendimiento de los procesos de mecanizado.
De este modo, se va a exponer una metodología para el análisis y la caracterización de la viruta en procesos de mecanizado en seco de aleaciones ligeras. La metodología diseñada se ha basado en el estudio de la viruta, y su relación con parámetros y variables de entrada y/o salida asociados a la misma y al proceso. Se ha tenido en cuenta tanto la monitorización ON-LINE del proceso de formación de la viruta como la monitorización OFF-LINE de distintos parámetros geométricos característicos (longitud, anchura, espesor, factor de recalcado, entre otros). Dada la dificultad que representa el estudio a simple vista de los parámetros geométricos que caracterizan a la viruta, ha sido necesario recurrir al uso de técnicas de microscopia óptica combinadas con técnicas metalográficas.
Finalmente, a partir de los resultados experimentales se han obtenido una serie de modelos paramétricos que permiten predecir el comportamiento de alguno de los parámetros geométricos de la viruta en función de las variables de entrada consideradas (velocidad de corte y avance). Estos modelos facilitan la selección de los valores de los parámetros de corte a aplicar, de forma que se consiga una mejora en el rendimiento del proceso.
Metodología experimental
La metodología experimental fue diseñada de forma genérica con el propósito de ser utilizada como un modelo que permita conocer el comportamiento de distintas aleaciones ligeras durante el proceso de mecanizado a través del análisis de la viruta. Se pueden considerar las siguientes fases que la conforman (Figura 1), así como los recursos materiales e instrumentales empleados.
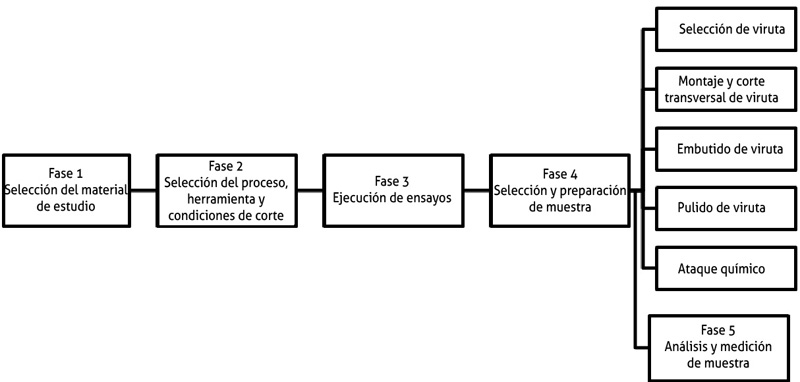
- Fase 1. Selección del material de estudio
La primera fase ha consistido en seleccionar una de las variables de entrada al proceso, la aleación objeto de estudio, así como la forma y dimensiones de las probetas a utilizar en los ensayos de mecanizado. Aunque esta metodología se ha diseñado para aplicarse a cualquier aleación ligera, se particulariza el estudio para la aleación de Titanio UNS R56400 (Ti6Al4V). Esta aleación se utiliza en la fabricación de componentes estructurales para aeronaves, frecuentemente de forma hibridada con materiales compuestos reforzados con fibra de carbono (CFRP, Carbon Fiber Reinforced Polymer), para formar estructuras laminadas metalo-compuestas (FML, Fiber Metal Laminates). Para este estudio se han utilizado probetas con forma cilíndricas, cuyas dimensiones y composición se muestran en la Tabla 1.

- Fase 3. Selección del proceso, herramienta y condiciones de corte
El proceso de mecanizado seleccionado ha sido el cilindrado horizontal, por su sencillez de ejecución y baja complejidad geométrica. Con objeto de utilizar técnicas respetuosas con el medioambiente, los ensayos se realizaron en seco. Para ello se ha hecho uso de un centro de torneado CNC, modelo Emco Turn 242, Figura 2(a). Con el objetivo de analizar la influencia de la velocidad de corte (v) y el avance (a) sobre la morfología de la viruta y sus características geométricas, se ha procedido a la realización de distintos ensayos con diversos valores de v y a, Tabla 2. Se trata de valores habitualmente utilizados en el mecanizado de este tipo de aleaciones en aplicaciones aeronáuticas. La profundidad de corte (p) se mantuvo constante, tomando un valor de 1 mm. Todos los ensayos se ejecutaron para un tiempo de mecanizado de t = 10 s.
Como herramientas de corte se emplearon plaquitas de Carburo de Wolframio (WC-Co) sin recubrimiento, con referencia DCMT11T308-F2HX, cuya geometría se muestra en la Figura 2(b). Para cada ensayo se utilizó un filo nuevo, con el objetivo de mantener las mismas condiciones iniciales en todos ellos.
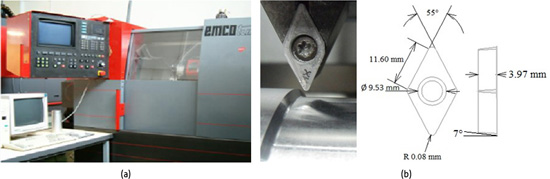

- Fase 3. Ejecución de los ensayos de mecanizado
Una vez seleccionadas las variables de entrada al proceso, se procedió a la ejecución de los ensayos de mecanizado. La combinación de los distintos valores de v y a seleccionados dio lugar a una resultante de 20 ensayos posibles. Los ensayos de mecanizado fueron grabados en vídeo, con el objetivo de registrar la forma en la que la viruta se desprende de la zona de corte, así como cualquier tipo de incidencia. Una vez finalizado el proceso de corte, se procedió a recoger la viruta generada y a etiquetarla mediante un código identificativo, -siguiendo metodologías aplicadas en otros estudios- código recoge la información relativa a los valores de los parámetros de corte empleados y del filo y la herramienta utilizada en el ensayo. Tras el etiquetado, los fragmentos de viruta de cada ensayo fueron clasificados según su morfología, aplicando los criterios establecidos en la norma ISO 3685.
- Fase 4. Selección y preparación de la muestra
Tras finalizar los ensayos de mecanizado, se procedió a la elaboración de probetas metalográficas para facilitar la manipulación de la viruta, y proceder a su observación haciendo uso de técnicas de microscopia óptica. Con ello se pretende comprender su mecanismo de formación y su comportamiento durante el proceso de corte. Se aplica una serie de procedimientos normalizados en la rama de ciencias de materiales, con la finalidad de comprobar las características y propiedades de la muestra o posibles fallas efectuadas por el proceso. Es importante resaltar que el éxito en esta etapa depende, en gran medida, del método utilizado en la preparación de la muestra así como del equipamiento básico para realizarlo. Se consideraron los siguientes pasos para preparar las muestras metalográficas de la viruta:
- Selección de viruta
- Corte transversal de viruta
- Inclusión de viruta
- Esmerilado y pulido de probeta metalúrgica
- Ataque químico
- Medición y análisis de viruta
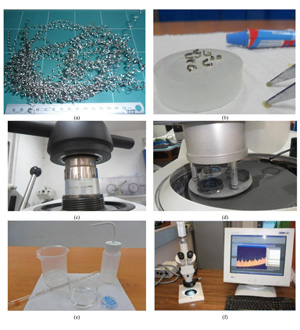
El proceso de selección de muestra es un paso importante, ya que debe satisfacer las condiciones de estadísticas en una sección limitada de forma aleatoria. En este caso se recomienda seleccionar diversos fragmentos de viruta previamente identificados de acuerdo a los parámetros en las que fueron expuestas, Figura 4.
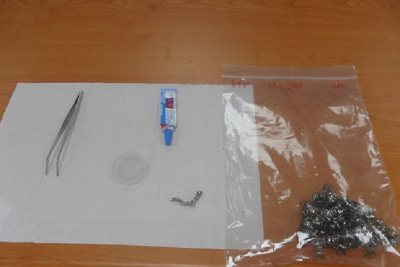
Una vez identificada la viruta con respecto a su proceso, se realizó un corte transversal a los fragmentos de viruta, Figura 5(a). El corte se realizó de forma manual (evitando el calentamiento de la muestra), permitiendo obtener la homogeneidad del material durante el proceso de fabricación en la que fue ejecutada.
Posteriormente, se llevó a cabo la inclusión de la viruta, con el objetivo facilitar un mecanismo que permita manipularla y visualizar sus características geométricas. Para ello se procedió al montaje de viruta (inclusión) en una probeta de resina 20x20x10 mm, haciendo uso de resina termoplástica de monje en caliente, con nombre comercial ClaroFast de la marca Struers, adecuada para el análisis del material a estudiar. Para el montaje de la viruta fue necesario realizar previamente un molde de plástico (resina), Figura 5(b). Posteriormente se aplicaron presión y calor para lograr suavizar y densificar el plástico. Los parámetros utilizados en su fabricación, en base a las recomendaciones del proveedor de resina, fueron los siguientes: Fuerza 35 N, tiempo de calentamiento 7 min, tiempo de enfriamiento 8 min, temperatura constante a 180 °C (para una proporción equivalente a 25 ml de resina). Una vez realizada la probeta base, se adhirieron los fragmentos de viruta y se procedió a colocar la probeta en la embutidora. Esta operación se repitió bajo los siguientes parámetros: 10 ml de resina sobre la probeta con viruta, reducir el tiempo de calentamiento y enfriamiento a un 10% de los parámetros propuestos con anterioridad.
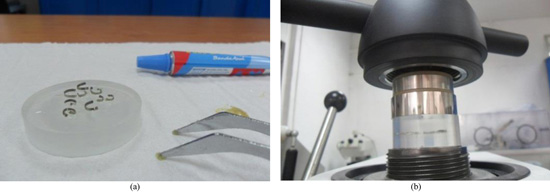
Finalizado el montaje de la viruta se procedió al desbaste y acabado. Para ello se hizo uso de una pulidora modelo Tegrasystem, Figura 6(a), con el objetivo de obtener una superficie ideal y libre de toda huella de marcas de herramientas, brindando un aspecto de la superficie igual al de un espejo. Para lograr dicho objetivo fue necesario realizar un desbaste agresivo para eliminar material excedente de la probeta, utilizando un disco abrasivo MD-Primo™ 320 con H2O, a una velocidad de 150 rpm, tiempo de 5 min y fuerza de 30N. Para un desbaste medio fue necesario utilizar un disco MD-Largo™ a una velocidad 150 rpm, con un tiempo de 7 min y fuerza de 30 N. Para el acabado final se utilizó un disco MD-DAC a una velocidad de 150 rpm a un tiempo de 3 min aplicando una fuerza de 25N. La selección del abrasivo se realizó teniendo en cuenta el material a pulir y el propósito del estudio metalográfico, Figura 6(b).
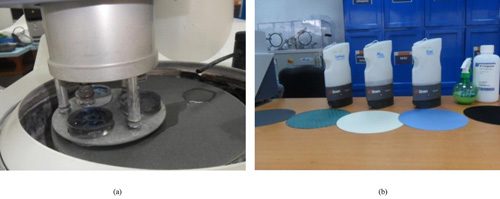
Una vez finalizado el pulido se realizó un enjuague general a la probeta con agua destilada y secado con aire comprimido, con el fin de eliminar impurezas en la probeta. A continuación, se procede a realizar una inspección previa a la superficie de estudio antes de realizar el ataque químico. En el caso de que el resultado no sea el deseado, es posible realizar un desbaste fino adicional para mejorar el acabado de la probeta. En la Figura7 se puede observar la diferencia entre una superficie con un pulido incorrecto, Figura 7(a) y correcto Figura 7(b).
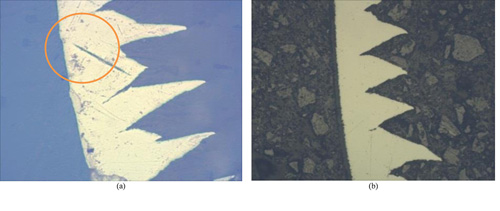
Tras el pulido, se procedió al ataque químico de las probetas haciendo uso de un reactivo adecuado al material objeto de estudio. Este ataque químico permite revelar la microestructura del material a estudiar. La preparación del reactivo se realizó bajo los siguientes parámetros: 100 ml de H2O, 1-3 ml de Ácido fluorhídrico (HF) y 2-6 ml de Ácido nítrico (HNO3). Para su preparación se utilizó una bureta de vidrio, 2 vasos precipitados de plástico (uno para colocar el reactivo y el otro para agua destilada). El tiempo empleado para el ataque químico fue de 15 segundos de exposición al reactivo, Figura 8 (a). Una vez pasado el tiempo estipulado se realizó un lavado con agua destilada con su respectivo secado. Para el almacenaje de las probetas se utilizó un desecador, con el fin de mantener una atmosfera interna libre de humedad, Figura 8(b).
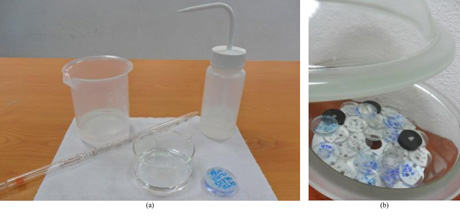
- Fase 5. Selección Análisis y medición de muestra
Una vez preparadas las probetas se procedió a su observación mediante el uso de técnicas de Microscopía Óptica Estereoscópica (SOM, Stereoscopic Optical Microscopy). Para ello se utilizó un microscopio estereoscópico modelo Nikon modelo SMZ 2T con un máximo de 63X, con cámara Kappa Image Base mod. CF11 DSP, tarjeta capturadora PCI SC module, con fuente emisora de luz Intralux 400 marca Volpi, con adaptadores para emisión anular y dos focos puntuales de fibra óptica, Figura 9.
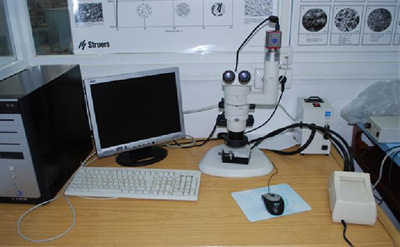
La captura de imagen y las mediciones se realizaron haciendo uso del software Kappa Image Base-Control y Perfect Image V7. Una vez obtenida la imagen se procedió al trazado de una serie de líneas tangenciales sobre la zona de interés de la viruta, las cuales facilitaron la monitorización OFF-LINE y la medida de los parámetros geométricos característicos de la viruta. En la Figura 10 se muestran los parámetros objeto de medición, donde hc es la altura de cresta, hv la altura de valle, S la sección de viruta, ø el ángulo de deslizamiento o cizalla y b el ancho de la viruta. Los valores de estos parámetros se han obtenido como el valor medio de las mediciones realizadas en distintos puntos de la viruta. A partir de estos parámetros se han obtenido de forma indirecta otros parámetros geométricos de interés, como el espesor de la viruta (tc), o el factor de recalcado (ξ).
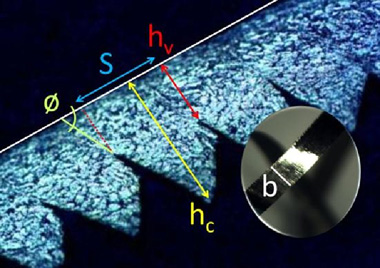
Resultados
Una vez finalizada la monitorización offline, se procedió al tratamiento, análisis e interpretación de los resultados experimentales obtenidos. En la Figura 11 se muestra una comparativa macroscópica de la morfología de la viruta adquirida a ciertas velocidades de corte: 75 y 50 m/min en función a los valores de a aplicados. En ellas se pueden apreciar diferentes efectos en su forma, teniendo en cuenta los criterios de clasificación de la morfología de la viruta de la norma ISO 3685 se puede decir que la tipología de viruta obtenida es, en general, de tipo helicoidal cónica enredada.
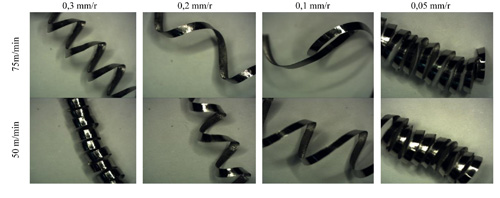
En la Figura 11 se puede observar la evolución geométrica de la viruta a distintas v, estando asociada al incremento del avance. Se puede apreciar que la alta plasticidad de esta aleación da lugar a que la viruta se deforme plásticamente sin llegar a fragmentarse, obteniéndose una viruta continua con elevada tendencia a formar nidos de viruta que dificultan la evacuación de la misma de la zona de corte. Se observa además una escasa influencia del valor de v en dicha morfología, siendo algo mayor la influencia de a. Continuando con la evaluación, se observa cómo, debido al bajo módulo elástico de la aleación, se origina una deformación de la viruta por su plano de deslizamiento, dando lugar una viruta de tipo segmentada.
Así, para valores de a de 0,3 mm/r a v de 50 m/min —como es el caso— la viruta obtenida es de tipo helicoidal cónica corta, presentando una menor tendencia a formar nidos de viruta. Todo parece indicar que los mayores esfuerzos originados a altos avances y bajas velocidades de corte dan lugar a que se supere el límite de rotura del material, existiendo una mayor tendencia a la fragmentación. Sin embargo al incrementar su v, como es el caso a v 75 m/min, se logra distinguir un cambio significativo, dado que aumenta el espesor de la viruta y por lo tanto se vuelve más rígida, por lo que las fuerzas necesarias para originar su corte deberán ser altas, debido a su baja deformación. Por consiguiente podría afectar la vida útil de la herramienta.
En la Figura 12 se puede observar la presencia de brillo en la superficie exterior de la viruta -la cara de contacto con la herramienta-, lo cual es debido a la carga de tensión que sufre en la zona de corte, sin embargo en la cara interior se puede identificar el efecto de sierra, característica de la viruta de titanio, debido a su compresión durante el proceso. Esto se puede observar con detalle durante el estudio SOM.
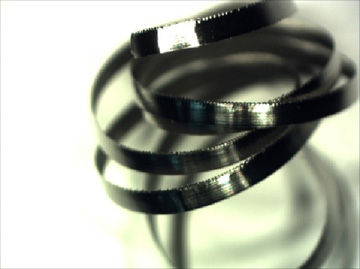
Para lograr la caracterización de la morfología de la viruta en el proceso de corte es necesario recurrir a una evaluación más detallada, justificando el uso de técnicas microscópicas en el área trasversal de la viruta. Conellas se puede observar con claridad la formación del efecto dietes de sierra en la viruta, así como también la segmentación de ella, que aumenta de forma significativa frente al valor de a y de forma leve con el valor de v (Figura 13). El comportamiento de este efecto es el resultado obtenido de las diferencias de altura entre las crestas y los valles, presentando una mayor tendencia a la fragmentación. Por lo tanto, la sección de la viruta está directamente relacionada con el comportamiento del material.
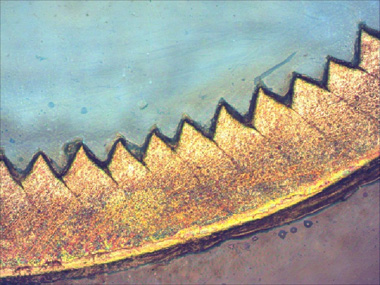
Considerando lo anterior, se observa que la viruta de titanio tiende a incrementar su espesor conforme avanza en su mecanizado. De igual forma, se puede decir que para v = 75 m/min se encuentra el valor más favorable desde el punto de vista de la fuerza de corte necesaria, con independencia del valor de a aplicado.
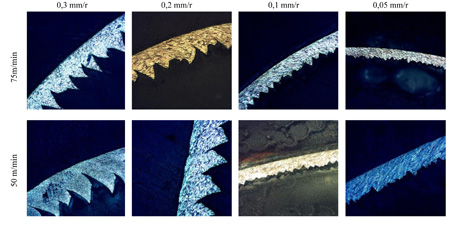
En la figura 14 se identifican imágenes SOM a distintas v, logrando identificar que el a es el parámetro de mayor influencia en la segmentación de la viruta, visualizados durante el incremento de alturas entre la cresta y sus valles. Por lo tanto, si aumenta su sección respecto al a, podría afectar a la calidad superficial de la superficie mecanizada. Finalmente, a partir de los datos obtenidos experimentalmente, se ha procedido a la obtención de un modelo paramétrico que permita predecir el valor de S en función de v y a, visualizados en la Figura 15. Para ello se ha procedido a realizar un ajuste con distintos modelos, siendo el modelo potencial el que ha dado lugar a un mejor resultado.

Considerando K, x e y como parámetros de ajuste. Se puede observar que el valor del exponente para a es superior al exponencial asignado como v, lo cual significa que la sección de la viruta se ve notablemente influenciada por el a y levemente con v.
En la Figura 15 (a) se pueden comprobar las teorías expuestas en los párrafos anteriores, donde la sección de la viruta tiende a incrementarse conforme avanza el corte. A su vez se observa que efectivamente el parámetro de la v tiene poca influencia en ella, ya que su afectación es ligeramente significativa en comparativa a su a, Figura 15(b). Es importante indicar que los límites de confianza utilizados para este modelo fueron a un 95%.
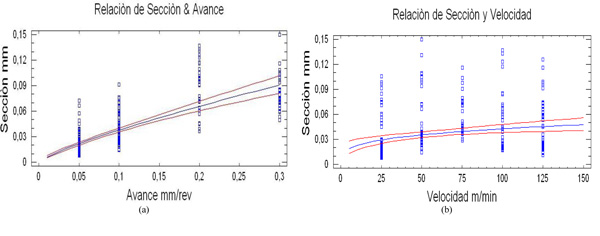
Conclusiones
Una vez finalizado la experimentación y análisis de los datos obtenidos de ellos es posible extraer las siguientes conclusiones:
- Se propone una metodología experimental para la caracterización morfológica y geométrica de la viruta en procesos de torneado en seco de aleaciones ligeras de uso aeronáutico, particularizado el estudio para la aleación UNS R56400 (Ti6Al4V), teniendo en cuenta su relación con parámetros y variables de entrada y/o salida asociados a la misma y al proceso.
- Se ha analizado y considerado el uso de técnicas metalográficas como instrumento fundamental para la caracterización de la viruta en el proceso de torneado, en particular bajo la ejecución de ensayos con microscopia óptica, así como los recursos materiales e instrumentales empleados.
- Se logra determinar que, para la aleación estudiada, el análisis de la viruta manifiesta que el avance es uno de los parámetros de mayor influencia en el proceso de corte, cuya combinación con altos valores de velocidad de corte puede lograr el incremento en la sección de la viruta y, por tanto, mayor uso energético requerido para corte.
- La metodología propuesta puede ser aplicada para el análisis de otros materiales metálicos, adaptando ciertos aspectos a las características propias de la viruta obtenida en el mecanizado de esas aleaciones.