Efecto de la interacción diseño-fabricación en la modificación del contacto en engranajes cónicos-espirales
1. Resumen
Se ha comprobado que parte de los problemas de durabilidad y fiabilidad de los engranajes de tipo cónico-espiral radican en la focalización de la zona de contacto entre dientes correspondientes. Esta zona de contacto puede cambiar en función de la estrategia de diseño, máquina de fabricación e incluso el montaje final de los pares de ruedas. Así se demuestra en varios casos prácticos explicados en este trabajo. También se hace referencia a la medida sistemática de este tipo de engranajes tanto por técnicas simples como en MMC.
2. Introducción
El proceso de fabricación de un engranaje va a depender del tipo que se quiera conseguir [1]-[8]. En esta introducción se va a hacer un repaso a las tecnologías existentes en la fabricación de engranajes dependiendo de su tipo así como la evolución que han sufrido estas tecnologías a lo largo de los años.
2.1. Engranajes cilíndricos
Los engranajes se pueden fabricar según diferentes procesos, entre los cuales se pueden distinguir los métodos de reproducción y los de generación. Los primeros presentan una productividad muy elevada, pero requieren una elevada inversión en maquinaria o herramientas. Los segundos son menos productivos pero más universales.
Los métodos de reproducción [1] obtienen la superficie final del engranaje directamente, entre ellos se distinguen:
- Fundición: en caso de engranajes de grandes dimensiones
- Sinterizado a partir de polvos metálicos.
- Forja [8] y posterior acabado.
- Brochado: Para engranajes interiores de pequeño tamaño.
- Arranque de viruta:
- Tallado por fresa módulo. Se emplea un útil de corte que reproduce la forma exacta de los huecos que van a eliminarse, Estos métodos no plantean diferencias en cuanto al ciclo cerrado propuesto, y están fuera del ámbito de este trabajo.
- Tallado en máquina de 5 ejes[10]. Gracias a la precisión y a la repetitividad de los nuevos modelos de máquinas multitasking y maquinas de 5 ejes es posible fabricar engranajes en una máquina universal y no en una máquina talladora de engranajes como tradicionalmente. No es para producción en masa. Aporta flexibilidad no estando limitado sólo a engranajes. El problema es que este proceso no es válido cuando se habla de engranajes tallados de alta calidad (ISO 1-3).
En el caso de los métodos por generación[1] la idea es que la herramienta de corte genere precisamente el perfil conjugado de sus dientes, de la misma forma que existiría un contacto entre perfiles si la rueda fabricada engranase con ella. El 'punto de contacto' sería en el tallado el 'punto de perfil generado'. La cinemática del proceso la impone la máquina de tallado, equivalente al que sería el contacto entre perfiles. Existen dos tipos de proceso:
- Generación por fresa madre (hobbing): La herramienta gira sobre su eje y tiene forma de tornillo sinfín. Por tanto su sección longitudinal es similar a una cremallera.
- Mortajado con cremallera o piñón: el proceso de corte se produce debido a los bordes afilados de la herramienta, y a la existencia de un movimiento continuo y rápido de vaivén (denominado industrialmente mortajado). Existen dos modalidades, generación con cremallera y generación con piñón.
2.1.1. Evolución de las máquinas talladoras a lo largo de la historia
Antiguamente, la única manera de establecer una conexión entre el cortador y el engranaje a tallar era mecánicamente. Todo el movimiento de generación de los engranajes venía condicionado por la relación de transmisión que se introducía en la 'caja de cambios' de la máquina. Esta manera de trabajar condenaba la posibilidad de realizar variaciones de una manera ágil. En resumen, los engranajes eran generados por una máquina cuyo corazón era un sistema de engranajes. Actualmente todo este proceso ha sido sustituido por la electrónica (CNC) de tal manera que cualquier movimiento está controlado por un motor. De esta manera se tiene la posibilidad de realizar cualquier cambio y cualquier regulación para poder mejorar el proceso.
2.2 Engranajes cónicos
El concepto que se aplica para la fabricación de engranajes cónicos es exactamente el mismo que se utiliza para la realización de engranajes rectos. Conseguir que la herramienta genere el movimiento de engrane.
2.2.1. Engranaje cónico de dientes rectos
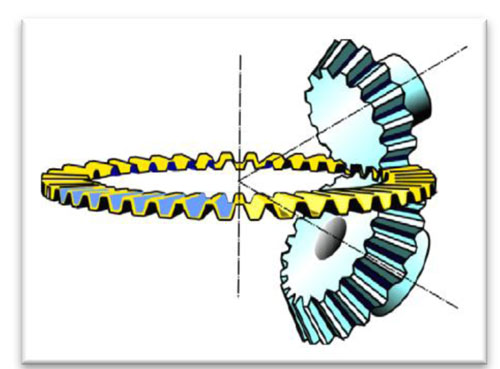
Existen diferentes metodologías para la generación de este tipo de engranajes:
a) Cortador de cuchillas. El tallado del diente se realiza mediante el vaivén de las cuchillas. Método en desuso, aunque en algunas piezas antiguas sin salida es la única manera de fabricación.
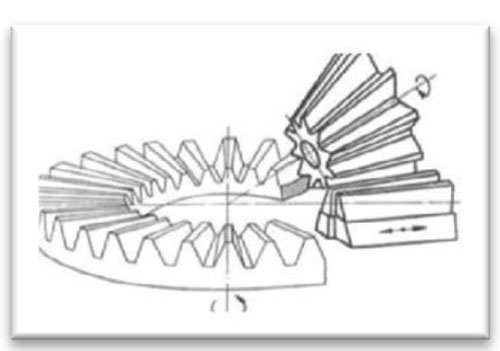
Figuras 2: a) Cortador de cuchillas.
b) Cortadores de disco. Esta metodología aprovecha el corte continuo de la herramienta. De esta forma se consigue un aumento en la producción. Las dos opciones más utilizadas actualmente son la de dos discos simultáneos o un disco independiente que hace ambos flancos.
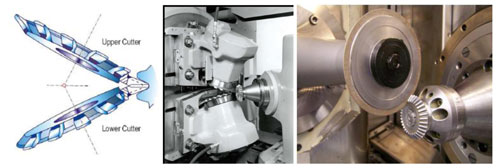
2.2.2. Engranajes espiro-cónicos
Aunque a priori la fabricación de este tipo de engranaje pueda parecer mucho más complicada, la realización de estos engranajes tiene el mismo principio que los anteriores tipos mencionados, que la herramienta sustituya en su movimiento aquel perfil con el que va a entrar en contacto el engranaje.
Existen dos corrientes totalmente diferenciadas para fabricar estos engranajes.
a) Face Hobbing [11]: En este método existe una continua interpolación entre la pieza y la herramienta. Todo está indexando. El diente generado de esta forma tiene un fondo de diente y cabeza que van paralelas.
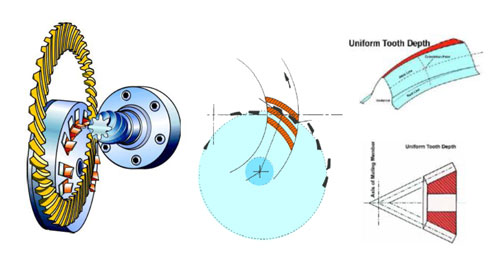
b) Face Milling: En este caso, la ley de movimiento que genera el diente es un círculo ya que las cuchillas en el cortador realizan un movimiento circular mientras el engranaje se mantiene fijo en una determinada posición angular.
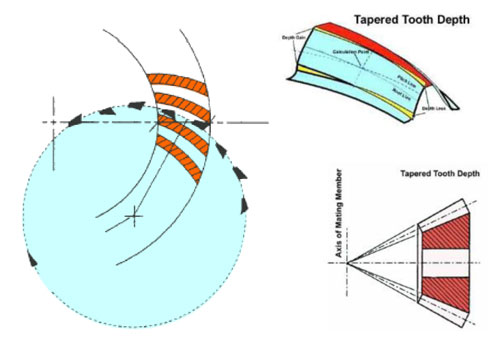
2.3. Evolución de las máquinas para engranajes espiro-cónicos
Los cambios sufridos en las máquinas a lo largo de los años ha sido producida por un continuo interés en poder controlar cada vez más cada parámetro del proceso y no depender de un movimiento mecánico y cerrado. Una modificación en la superficie de la pieza suponía un 'rediseño' en toda la cadena cinemática que genera el perfil del diente.
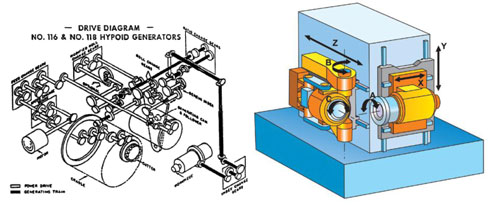
Las nuevas tecnologías introducidas en los últimos años han propiciado una mayor posibilidad de regulación de todos los parámetros que afectan al engranaje. En un engranaje espiro-cónico esto es de gran importancia ya que una pequeña modificación puede hacer que el contacto entre superficies mejore ostensiblemente. En las figura 6 se muestra la complejidad del mecanismo necesario para generar un engranaje espiro-cónico así como la última tecnología para la generación de estos engranajes.
3. Casos de estudio: engranajes espiro-cónicos
La manera de trabajar con este tipo de engranajes difiere totalmente de lo que sería con un engranaje cilíndrico de dientes rectos. Así, cuando se quiere trabajar con engranajes de dientes rectos, todas las fases que intervienen desde su diseño hasta su montaje pueden ser independientes entre ellas. El control de estos engranajes está perfectamente definido en las normas internacionales por lo que medir y corregir los fallos es relativamente sencillo. Además todas las correcciones a realizar son por norma general, muy intuitivas. El montaje de una pareja de engranajes no influye demasiado en la zona de contacto ya que lo parámetros a modificar son escasos. La intercambiabilidad entre ruedas es uno de los puntos a lograr en su producción y montaje.
En los engranajes espiro-cónicos los conceptos utilizados hasta ahora se desvanecen. Las fases que engloban el ciclo de la pieza desde el diseño hasta el montaje de la misma se convierten en una sola. En este caso, no se puede trabajar de manera independiente entre unas y otras. Todas las fases van a estar unidas dentro de un ciclo global.
En este artículo se plantea un método de trabajo para reducir al máximo el número de iteraciones necesarias, mediante un método de trabajo realimentado entre las primeras etapas de diseño-fabricación-control de calidad. Además, se introduce la fabricación de la pieza mediante el proceso de rectificado desde sólido, que es un proceso muy dirigido a series cortas. El rectificado además induce el problema añadido de quemado y control del proceso.
3.1. Tipología de pieza a estudiar
El sector al que van a ir dirigidas las piezas de este caso de estudio, es el sector aeronáutico. Este sector tiene una serie de requerimientos que no tienen el resto de sectores. Los pares de engranajes espiro-cónicos utilizados en aeronáutica tienen que tener la mejor calidad en cuanto a error de paso se refiere llegando a ser necesario cumplir la calidad DIN 1 a DIN 3. Por su puesto la fiabilidad de los componentes es un factor crítico en cualquier componente introducido dentro de un avión. Las piezas tratadas son piezas conocidas como críticas, estas son las que en caso de fallar el avión no podría seguir volando.
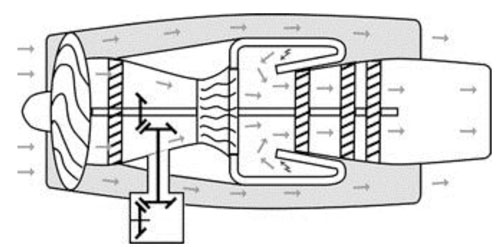
Igualmente importante son otros aspectos como acabado superficial, radio de fondo del diente, conseguir un error de transmisión bajo, alta resistencia mecánica y bajo peso. El principal reto a conseguir, es conseguir un 'ease-off' en la fase de diseño que sea aceptable y tratar de plasmarlo en la realidad. Para este propósito y los requisitos de calidad mencionados anteriormente, es necesario disponer de las máquinas viables para conseguirlo.
Para poder superar los requisitos de desgaste y resistencia mecánica, estas piezas como normal general deberán ir con un tratamiento superficial que les de dureza. En este caso, el tratamiento superficial es un cementado. El material de partida es un E16NCD13. El estado previo al tratamiento es recocido. Se le pedirá una capa de cementado entre 0,65 y 0,8 mm. Tras el cementado será necesaria una operación de temple y revenido. La dureza superficial a conseguir es de 58-62 HRC. También es necesario mencionar que el número de piezas a fabricar no son elevadas. No más de 20 piezas.
4. Metodología de trabajo. Ciclo cerrado
En la figura 8, se muestra la secuencia de trabajo a seguir para conseguir realizar un set de engranajes con las características de calidad definidas previamente.
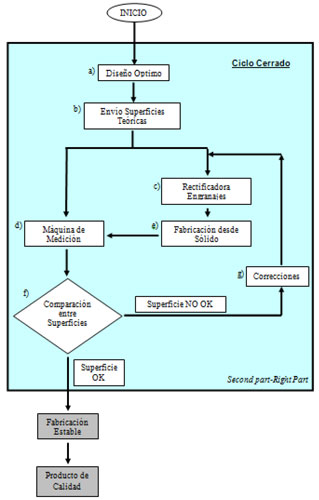
La primera fase del ciclo, es la de diseño (8a). En esta fase es donde nace la concepción de las superficies del engranaje, aquí se decidirá cómo deberá ser el contacto entre superficies para un correcto funcionamiento. Una vez terminada esta fase, las superficies serán enviadas (8b) a la máquina para su fabricación (8c) y a la máquina de control (8d) para su medición posterior. Tras recibir las superficies en la rectificadora, se mecanizarán las superficies (e). Esta primera fabricación generará unas superficies que no serán las ideales, por esto, las piezas se han de medir para indicar las diferencias entre las superficies teóricas y las reales conseguidas en la rectificadora (8f). Tras analizar las diferencias existentes, el departamento de ingeniería realizará las correcciones necesarias para llegar a la superficie ideal diseñada (8g). Con estas nuevas correcciones, se vuelve a la máquina para volver a rectificar las superficies. Tras este ciclo cerrado, las piezas que salen tras estas operaciones son piezas cuyas superficies entran dentro de los límites de calidad exigidos. Trabajando de esta manera, involucrando a todas las fases (diseño-fabricación- control) se consigue una producción estable desde la primera pieza. Una vez que se consigue la primera pieza, el proceso de fabricación puede continuar sin depender de los demás departamentos ya que la calidad de la pieza ya está asegurada gracias a la metodología de trabajo explicada.
En los apartados siguientes se muestra más detalladamente cada fase del proceso.
5. Etapa 1. Diseño engranaje espiro-cónico
Como primera fase, se trata de buscar un set de engranajes espiro-cónicos que sean capaces de proporcionar unas características de durabilidad y resistencia elevadas. Por lo tanto, se ha de buscar en todo momento que la zona de contacto sea aquella que proporcione el menor error de transmisión [12], además de que las tensiones de contacto no superen valores críticos para el material.
Para realizar el estudio y la mejora se ha de partir del diseño inicial para ver si este es válido o si por el contrario se puede mejorar. [13] En este caso, el análisis de la pareja de engranajes proporciona los siguientes resultados.
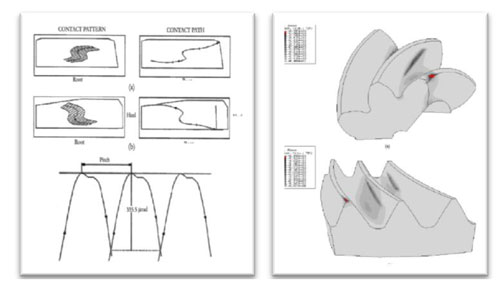
El resultado obtenido en esta primera fase de diseño no es el deseado. La zona de contacto no sigue una línea teórica ideal, de hecho ni se acerca. En cuanto al error de transmisión, los valores son demasiado elevados para que durante el funcionamiento no exista ningún problema, por lo tanto tampoco es válido. Por último, se ve que existen zonas donde la tensión de contacto es demasiado elevada.
El primer paso en la optimización está dirigido en la búsqueda de la mejor dirección de contacto que sea capaz del mayor error de posicionamiento. Como se puede ver en la figura 10, la nueva dirección de contacto ofrece una mejor distribución del área de contacto mejorando ostensiblemente el funcionamiento de dicho par de engranajes. Añadiendo ligeras modificaciones en los parámetros de máquina se consigue un perfil del flanco mejorado.
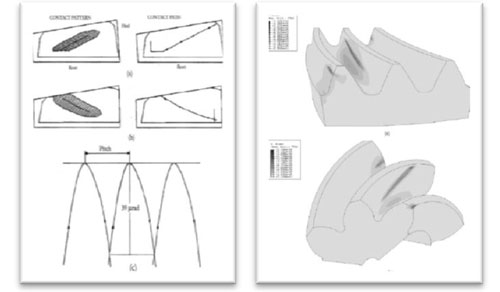
Debido a la gran complejidad del problema, y debido al tipo de pieza al que se hace frente. El mejor método para conseguir lograr los requisitos de calidad, es el método de rectificado por flanco independiente. En este formato de fabricación, cada flanco se fabrica sin tener en cuenta el contrario. Se consigue que cualquier modificación que se realice en un flanco cóncavo por ejemplo, no sea copia al flanco convexo, ya que la herramienta no estará nunca en contacto con los dos flancos a la vez.
6. Etapa 2. Fabricación por rectificado desde sólido
En este caso, se utilizarán dos muelas idénticas pero que a posteriori una irá dirigida al flanco convexo y la otra al flanco cóncavo. Debido a las calidades que se quieren conseguir, se ha de asegurar que las piezas en el momento en el que llegan a la máquina, tengan unas características muy específicas de calidad. Normalmente, se necesita una cara de apoyo y un diámetro de referencia para poder centrar la pieza en la máquina. Es evidente que si antes de empezar a tallar el engranaje, esta ya trae intrínsecamente un error previo, este error será añadido al engranaje. Es por tanto que esto es un punto clave.
Otra parte, igual de importante, es el diseño del utillaje. Se está pensando en conseguir piezas en calidad DIN 1-2 por lo tanto, la forma en la que va a ir la pieza amarrada y apoyada en la máquina conlleva una gran importancia. Este artículo no es objeto de estudio de toda la diferente tipología de utillajes que son necesarios, por lo tanto no se va a entrar en detalle en este tema. En definitiva, el error total que se obtenga en el engranaje será la suma de todos los errores inherentes provocados por divergencias en el proceso de fabricación.
Por último queda definir en qué máquina se van a realizar las operaciones de fabricación (Etapa 2) y de control (Etapa 3).
La máquina de la que se dispone para realizar estos ensayos es la máquina Phoenix 275G con cabezal de alta velocidad de la compañía Gleason, una máquina de rectificado compacta y versátil que ayudará a conseguir dicho propósito siempre y cuando se tenga en cuenta las restricciones que impone esta máquina:
- Diámetro de muela. 69 mm ≤ Ø ≤ 230 mm
- Anchura máxima del diente = 58 mm
- Revoluciones máximas del spindle = 12.000 rpm.
- Diámetro primitivo máximo de la corona = 275 mm
Esta máquina también brinda la posibilidad de hacer el rectificado desde sólido. Con este proceso, se evita tener que comprar nuevas herramientas para realizar un previo desbaste de la pieza, se gana tiempo (puesta a punto de nuevas herramientas) y dinero (no hay que invertir en diferentes herramientas).
7. Etapa 3. Medida y reajuste de parámetros
Cuando uno se va a poner a fabricar, no dispone de los mismos datos de control que en cualquier otra tipología de engranajes (Error individual de paso (fp), error total de división (Fp), error total de hélice (Fβ), error total de perfil (Fα), etc.) es por ello, que lo único que se puede hacer es tratar de fabricar la superficie más parecida a la diseñada previamente. Para poder ver las diferencias existentes entre lo que se fabrique y lo que se ha diseñado se pone a disposición de los ensayos la máquina de medición de engranajes 350 GMS de la compañía Gleason.
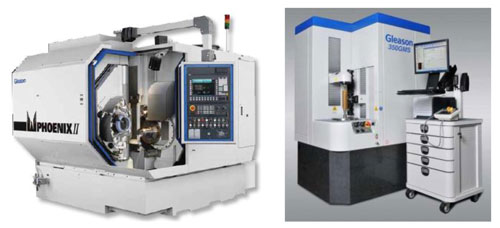
Una vez definidos los utillajes, herramientas y máquinas es el momento de empezar a fabricar. En este instante se necesita que la fase de diseño, fabricación y control estén unidas. A continuación se procede a introducir una metodología de trabajo mediante un ciclo cerrado entre ellas para poder realizar una fabricación estable.
Tras haber realizado el conveniente diseño buscando el óptimo contacto entre las superficies, se deberán mandar estas superficies generadas a la máquina mediante un post-procesado. Al mismo tiempo, para un posterior control en la máquina de medición, también se enviarán dichas superficies teóricas a la máquina de control. Como se ha comentado anteriormente, el método de fabricación que se va a utilizar es el de flancos independientes. El proceso de fabricación necesario para poder realizar correctamente las piezas se ha determinado que sea:
- Desbaste del lado convexo.
- Desbaste del lado cóncavo.
- Cementado.
- Acabado lado convexo.
- Acabado lado cóncavo.
- Ataque nital.
Es evidente que realizar el proceso en tantas fases puede llegar a parecer excesivo pero debido a la gran complejidad del problema, es la manera más fiable de asegurar la calidad del producto.
Es hora de comenzar con el primer paso el desbaste previo al cementado. Una vez montada la muela y la pieza en la máquina se puede empezar a realizar el ciclo de trabajo en la máquina definido en la fase de diseño previo. Una vez terminada la operación, se comprobará qué tipo de superficie se ha generado. Para poder ver que se ha obtenido, se procederá a la medición mediante puntos de la superficie. En este caso, la malla elegida es una malla de 9 columnas y 5 filas. Es decir, la superficie quedará determinada por 45 puntos.
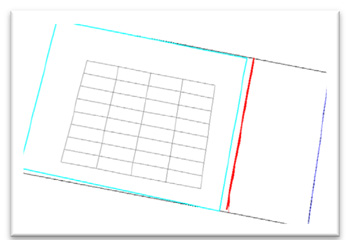
Como se ha comentado no se dispone de parámetros de control para saber si está bien o mal, únicamente existe una superficie teórica que se deberá contrastar con la superficie generada. En la figura 13 se muestra la comparación entre la superficie teórica y la superficie mecanizada.
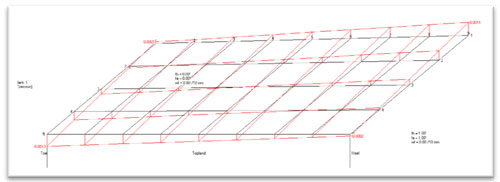
La malla negra representa la superficie teórica previamente diseñada. La roja muestra cual es la distorsión actual con respecto a la teórica. Para poder corregir estas desviaciones, vuelve a entrar en juego la fase de diseño. Tras recibir la información de los errores, pueden hacer las modificaciones necesarias para corregir dicho error. Puede suceder que el error sea tan elevado que no haya manera de corregirlo. En este punto siempre hay que tratar de hacer las correcciones más simples que sean posibles ya que cuanto más complicadas sean, mayor será la complejidad del movimiento a realizar por la máquina. Si el error es demasiado elevado, puede que aunque se realicen las correcciones pertinentes, no se pueda llegar a la malla teórica.
Una vez que se tienen los parámetros necesarios para corregir los errores, se han de volver a mandar la máquina, para que en el próximo ciclo realice las correcciones. Como se puede observar, tras mecanizar y volver a medir se obtienen los siguientes resultados:
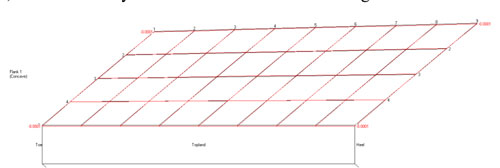
Una vez conseguido uno de los flancos, es el momento de continuar con el siguiente. El proceso a seguir sería exactamente el mismo que para el anterior. Mandar la superficie del flanco a la máquina 275G y a la máquina de medición 350GMS. Realizar el ciclo de mecanizado y posteriormente medir. Tras la medición, sacar las diferencias entre la malla teórica y real para poder de nuevo en la fase de diseño, corregir dichos errores. De nuevo necesitan estar relacionadas la fase de diseño, con la de medición y la de fabricación ya que para hacer los cambios pertinentes, la máquina necesitará recibir los cambios a realizar.
Como se puede apreciar, el concepto típico de los talleres, intentando ser independientes de ingeniería no funciona en este tipo de piezas. Ambos grupos deben trabajar juntos si quieren conseguir un producto con unos requisitos tan especiales.
Para complicar aún más la fabricación de este engranaje, se comento anteriormente que debería de llevar un cementado [15]. Este cementado se realiza tras el desbaste explicado anteriormente. Aquí puede haber diversidad de opiniones, ¿por qué perder el tiempo en sacar una superficie tan buena si es un desbaste? La respuesta es clara, tras la operación de cementado, el engranaje sufre una severa deformación por lo que no se podría acabar el engranaje y posteriormente tratarlo ya que sería imposible cumplir con los requisitos de calidad. Otra razón por la que se ajusta tanto la superficie en el desbaste, es porque de esta manera ya se tiene la mejor configuración de máquina para conseguir la superficie del flanco teórica. Y para finalizar, es necesario tener una capa de cementado perfectamente distribuida a lo largo de todo el engranaje y de ahí que se necesite que la superficie desbastada sea lo más parecida a la superficie final acabada.
Tras realizar el cementado, todas las caras y diámetros que se habían utilizado previamente para apoyar y centrar la pieza en el utillaje quedan inútiles. La pieza necesita volver a ser mecanizada para conseguir unos registros donde poder apoyar de nuevo la pieza.
Una vez que se tiene una zona limpia se puede volver a montar la pieza en el utillaje para comenzar con la operación de acabado. La operación de desbaste se realizó con el método de rectificado desde sólido, por lo tanto en cada pasada existía la misma cantidad de material. Ahora, tras el cementado y con la deformación sufrida no se tiene el mismo material en todo el flanco lo que va a complicar aún más la puesta a punto para finalizar el engranaje. La situación actual es que se tiene un diente cementado con diferente material a lo largo del diente. Si a la hora de rectificar, se excede con la potencia aplicada, puede suceder que se sobrepase la temperatura de revenido, se tenga un cambio estructural en la pieza y por tanto la pieza sufra quemados. Si esto sucede, la pieza queda directamente rechazada.
El proceso a seguir para acabar la pieza, es el mismo que se ha utilizado para el desbaste. Se tiene que volver a utilizar la interacción entre fabricación-diseño-control para tener la superficie deseada.
Para poder validar el proceso, como se ha rectificado sobre zona cementada, se ha de realizar un ataque nital a la pieza para ver que en ningún momento esta pieza ha sufrido quemaduras en su superficie. El proceso de nital a realizar es el siguiente:
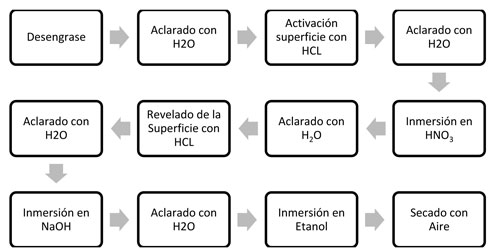
Figura 15: Proceso para ataque nital.
8. Montaje final
Que la pieza haya superado los previos requisitos de calidad, no supone que la pieza esté perfectamente lista para la fabricación en serie. Para ver si realmente lo fabricado es lo que se diseñó, hay que realizar una última operación manual. En esta operación se harán funcionar los engranajes en su posición de montaje para ver dónde queda la zona de contacto.
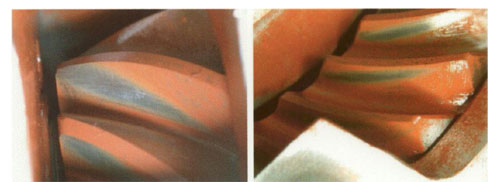
Si este contacto queda en la zona deseada se podrá dar por válido el diseño, la fabricación y el montaje. Si no es así, existen varias posibilidades para poder modificar ligeramente el contacto a lo largo del flanco que se muestran a continuación:
- Subir y bajar el contacto si se introduce o se saca el piñón dentro de la corona.
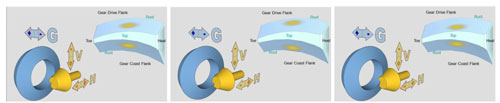
- Desplazar el contacto a lo largo del flanco, hacia un lado o hacia el otro, subiendo y bajando el piñón en la dirección V.
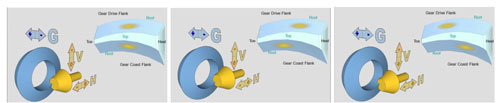
Estas modificaciones en el montaje tienen la desventaja de que a partir de este momento, para mantener las propiedades en la zona de contacto que se han conseguido este par de engranajes, no se podrán intercambiar con otros engranajes. Estos dos, estarían unidos de por vida.
9. Conclusiones
En este trabajo se ha presentado un método de trabajo que minimiza el tiempo de producción de engranajes complejos, y además se han presentado líneas de desarrollo que permitan entrar en proyectos de diseño y optimización de trasmisiones complejas y de alta responsabilidad. De esta forma es posible fabricar engranajes que aseguren al menos 'second part- rigth part', en el complejo problema de los cónicos espirales. Donde desde el inicio hasta su fabricación, todas y cada una de las partes tiene una importancia determinante en el producto.
El trabajo además ha permitido generar y actualizar nuevo know how que está ya integrado en los planes formativos del grado de Ing Mecánica y una Master, y un grupo consolidado en nuestro entorno que pueda integrarse en proyectos complejos.
De esta forma se rompe una realidad que hasta la fecha ha ocurrido, que se fabrican engranajes pero con la debilidad de que todas las fases del engranaje no estaban interrelacionadas entre ellas.
Se soluciona el problema de los rechazos de piezas como consecuencia de la realización de los engranajes mediante prueba y error.
10. Agradecimientos
El autor quiere agradecer la financiación recibida de Mimeco dentro del Proyecto Innpacto Enngrana que ha hecho posible la consecución de este trabajo.
Referencias
[1] K.-D. Bouzakis, E. Lili, N. Michailidis, O. Friderikos. Manufacturing of cylindrical gears by generating cutting processes: A critical synthesis of analysis methods. CIRP Annals - Manufacturing Technology, Volume 57, Issue 2, 2008, Pages 676-696
[2] R.Endoy, Gear Hobbing, Shaping, and Shaving: A Guide to Cycle Time Estimating and Process Planning, SME, 1990
[3] Prem H. Daryani, The Art of Gear Fabrication, Industrial Press Inc., 2001
[4] Franklin Day Jones, Henry H. Ryffel. Machinery's Hadbook. Industrial Press Inc., 1961
[5] Joseph R. Davis, Gear Materials, Properties, and Manufacture, ASM International, 2005
[6] Angulo, C.; López de Lacalle, L.N.; Agirrebeitia, J.; Pinto, Ch.; ELEMENTOS DE MÁQUINAS. ISBN: 978-84-95809-27-8. Sección de Publicaciones de la E. T. S. Ingeniería de Bilbao, 2007
[7] B. Karpuschewski, H.-J. Knoche, M. Hipke. Gear finishing by abrasive processes. CIRP Annals - Manufacturing Technology, Volume 57, Issue 2, 2008, Pages 621-640
[8] G.G. Baránov. Curso de la Teoría de Mecanismos y Máquinas. EDITORIAL MIR, 1980. Pages 209-326.
[9] E. Doege, H. Nägele. FE Simulation of the Precision Forging Process of Bevel Gears. CIRP Annals - Manufacturing Technology, Volume 43, Issue 1, 1994, Pages 241-244
[10] S.H. Suh, W.S. Jih, H.D. Hong, D.H. Chung. Sculptured surface machining of spiral bevel gears with CNC milling. International Journal of Machine Tools and Manufacture, Volume 41, Issue 6, May 2001, Pages 833-850
[11] Vilmos V. Simon. Influence of tooth modifications on tooth contact in face-hobbed spiral bevel gears. Mechanism and Machine Theory, Volume 46, Issue 12, December 2011, Pages 1980-1998
[12] Chung-Yunn Lin, Chung-Biau Tsay, Zhang-Hua Fong, Computer-aided manufacturing of spiral bevel and hypoid gears by applying optimization techniques, Journal of Materials Processing Technology, Volume 114, Issue 1, 4 July 2001, Pages 22-35
[13] Faydor L. Litvin, Alfonso Fuentes, Kenichi Hayasaka. Design, manufacture, stress analysis, and experimental tests of low-noise high endurance spiral bevel gears. Mechanism and Machine Theory, Volume 41, Issue 1, January 2006, Pages 83-118.
[14] Guenther. Interpretation of bevel gear topography measurements. CIRP Annals - Manufacturing Technology, Volume 60, Issue 1, 2011, Pages 551-554.
[15] K.-D Bouzakis, N Michailidis, J Anastopoulos, S Kompogiannis, G Erkens, P.J Roudnik. Geometry and coating parameters effect on cemented carbide sticks cutting performance used in bevel gear manufacturing, Surface and Coatings Technology, Volume 153, Issues 2–3, 15 April 2002, Pages 148-154
[16] Ying-Chien Tsai, Wei-Yi Hsu. The study on the design of spiral bevel gear sets with circular-arc contact paths and tooth profiles. Mechanism and Machine Theory, Volume 43, Issue 9, September 2008, Pages 1158-1174
[17] Cao Xuemei, Fang Zongde, Xu Hao, Su Jinzhan. Design of Pinion Machine Tool-settings for Spiral Bevel Gears by Controlling Contact Path and Transmission Errors Original Research Article. Chinese Journal of Aeronautics, Volume 21, Issue 2, April 2008, Pages 179-186
[18] Vilmos Simon. Head-cutter for optimal tooth modifications in spiral bevel gears. Mechanism and Machine Theory, Volume 44, Issue 7, July 2009, Pages 1420-1435
[19] Alessio Artoni, Marco Gabiccini, Mohsen Kolivand. Ease-off based compensation of tooth surface deviations for spiral bevel and hypoid gears: Only the pinion needs corrections. Mechanism and Machine Theory, Volume 61, March 2013, Pages 84-101