Grinsel, el nuevo software de selección óptima de muelas abrasivas convencionales
El rectificado es un proceso de mecanizado en el cual el arranque de viruta se realiza gracias a la acción, sobre la pieza, de duras partículas abrasivas fijadas mediante un aglomerante. Dichas partículas abrasivas conforman la muela abrasiva como herramienta de corte del proceso y disponen de minúsculas aristas de corte, agudas y de forma irregular. El mecanizado abrasivo se caracteriza por la acción simultánea de una buena cantidad de granos abrasivos sobre la pieza. Con el objeto de optimizar el rendimiento para cualquier muela abrasiva que forme parte de un proceso de rectificado, se ha desarrollado una metodología que permite realizar la comparación del rendimiento de diferentes muelas abrasivas para una aplicación en concreto. Esta metodología, unida al know-how adquirido por el personal técnico del fabricante de muelas Abrasivos Unesa S.L., ha permitido volcar todo ese conocimiento generado en un software de selección de muela abrasiva óptima, denominado Grinsel. Dicho software permite, de una manera rápida y concisa, la selección de la muela abrasiva óptima para una aplicación concreta, según las referencias del catálogo de productos de Abrasivos Unesa S.L.
1. Introducción
A pesar del gran desarrollo realizado en los últimos tiempos, el rectificado es uno de los procesos más complejos y menos conocidos existentes debido, sobre todo, al gran número de variables que intervienen durante el mismo. sin embargo, este desarrollo ha sido mínimo en relación a las investigaciones relativas al comportamiento de las muelas abrasivas.
La explicación a la falta de desarrollo científico en torno a las muelas abrasivas, obviando el desarrollo tecnológico de nuevos abrasivos y formulaciones capaces de rectificar nuevas aleaciones, además de determinada por la complejidad inherente a las mismas muelas, viene determinada por el principal objetivo de la industria de rectificado. es necesario recordar que el rectificado se utiliza en la transformación de materiales difíciles de mecanizar mediante otros procesos, generalmente en base a su elevada dureza y la exigencia de tolerancias estrechas. siempre se ha considerado que la obtención de dichas características era suficiente para la supervivencia del sector, sin considerar otros aspectos claves en la industria manufacturera de la actualidad como el aumento de productividad y la reducción de costes.
La aparición y desarrollo de diferentes procesos que pudieran ser sustitutivos del rectificado hacen que este proceso necesite de un desarrollo tecnológico en todos sus aspectos, es decir, máquina rectificadora, muelas abrasivas y mejora del proceso. Durante la última década se han impulsado sobremanera las actividades investigadoras en torno al rectificado, abarcando mejoras en las máquinas (motores lineales, medición on-line, multifuncionalidad, etc.) así como mejoras en el proceso; desarrollo de nuevas técnicas de simulación del proceso (predicción de la rugosidad a obtener en la pieza, predicción de dañado térmico, etc.), rectificado en seco, rectificado con temple, etc.
Sin embargo, dichas actividades investigadoras son reducidas cuando se trata de la muela abrasiva, habiéndose centrado sobre todo en el desgaste que sufre una muela abrasiva durante el rectificado y la determinación del ratio g, para cuya definición es necesario determinar el volumen de muela desgastada.
En relación a la selección o recomendación de muela abrasiva, diversos métodos han sido desarrollados en función de la aplicación de rectificado a realizar durante las últimas décadas. Estos métodos contemplan desde sistemas expertos, tales como la utilización de redes neuronales [3] y software del tipo denominado como wsexpert [4], hasta un método basado en el valor de un coeficiente que se calcula para la operación de rectificado a realizar [5]. Por otro lado, diversos fabricantes de muelas rectificadoras disponen de aplicaciones web de consulta [6], en las que se recomienda el uso de una muela en concreto de entre las muelas de su catálogo, para el rectificado de un material en concreto.
Sin embargo, el método más utilizado por los fabricantes de muelas abrasivas es un sistema de selección que utiliza ciertas reglas definidas en base al conocimiento del proceso. Existen diferentes consideraciones sobre la forma de selección de cada una de las características de la muela abrasiva, en base al material a rectificar y las características del proceso. Existen reglas y consideraciones a la hora de seleccionar el tipo de abrasivo [2, 7, 14, 15,16, 17, 18, 19, 20], el tamaño de grano [14, 16, 17, 24], la estructura [16], el grado [14, 16, 17, 21, 22, 24] y el aglomerante [2, 7, 14, 16, 17, 20, 22, 23].
La tabla 1 muestra una tabla resumen con las variables a considerar en la recomendación de cada una de las características que conforman una muela abrasiva, según el estudio bibliográfico realizado. esta recopilación permite discernir las variables más importantes a considerar en la definición de la muela abrasiva. Estas variables son las relativas a la pieza a rectificar, el tipo de rectificado y el tipo de operación a realizar.
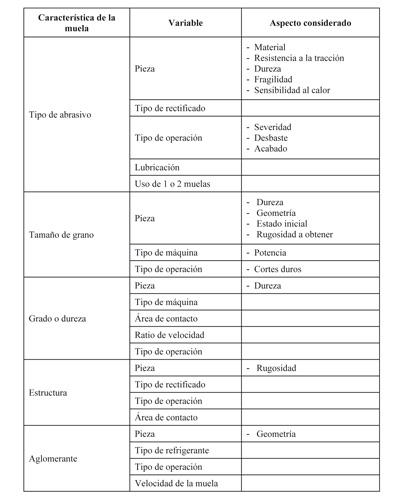
Tabla 1. Parámetros considerados en la definición de una muela abrasiva.
2. Objetivos
En el ámbito del comportamiento de la muela no se conoce ninguna metodología que analice el rendimiento de las muelas abrasivas y aporte una recomendación de muela óptima desde el enfoque de la mejora optimización del proceso. Se pretende desarrollar una metodología de análisis del comportamiento/rendimiento para cualquier muela abrasiva, de modo que sea posible realizar una comparativa entre muelas diferentes que permitan concluir cuál de esas muelas es la óptima para una aplicación en concreto. Por otra parte se desea desarrollar un software de selección óptima de muela abrasiva basado, además de en la experiencia acumulada en la industria del rectificado por el fabricante de muelas abrasivas Unesa S.L., en los resultados obtenidos debido a la aplicación de esta metodología.
3. Metodología
El trabajo planteado para poder dar respuesta a la recomendación de muela abrasiva óptima se muestra en el diagrama esquemático de la Figura 1. Se ha definido un ensayo tipo con un tiempo de rectificado suficiente como para poder evaluar el rendimiento de la muela abrasiva. Se ha procedido a definir las variables que se consideran necesarias para proceder a la evaluación del rendimiento en profundidad de las mismas. Se ha optado por analizar las consideradas como imprescindibles desde un punto de vista más industrial y menos científico. Para ello se ha realizado un set-up experimental que permita medir dichas variables [1].
Sobre la pieza se analizarán la rugosidad obtenida, los cambios de dureza superficial y la obtención de las tolerancias dimensionales y geométricas. Sobre la muela se analiza principalmente su desgaste, determinándolo en función de la reducción radial sufrida por la muela tras el ensayo. La particular estructura y topografía de las muelas abrasivas hace que realizar las medidas sobre las propias muelas sea la forma más complicada de obtener el desgaste. La falta de precisión en las medidas obtenidas mediante los métodos utilizados en bibliografía hace que se descarte realizar medidas sobre la propia muela utilizando medios como la cámara CCD [25, 26] o el láser [27].
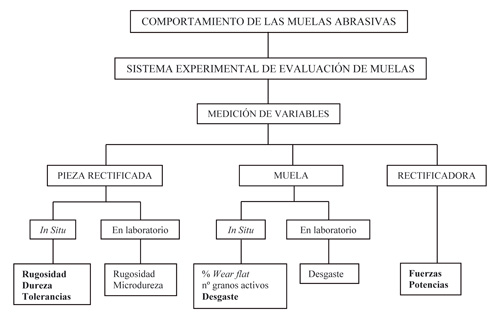
Figura 1. Diagrama esquemático para determinar el comportamiento de muelas abrasivas.
Se ha optado por determinar el desgaste mediante el método de impresión. Este método consiste en copiar el perfil desgastado de la muela sobre un cuerpo (lámina o chapa) de espesor reducido o recrear dicho perfil utilizando un molde con material utilizado para el moldeo dental por una parte, bien sea alginato o silicato, o utilizando pasta de carrocero [28].
La medición de la huella del perfil se puede realizar de diferentes maneras; mediante perfilometría confocal [2, 29], microscopio óptico [30] o cámara CCD [31]. Con objeto de poder realizar la medición del desgaste en la propia máquina, se ha diseñado un utillaje donde poder realizar la copia del perfil en una chapa de espesor reducido, midiendo el escalón que representa el perfil desgastado mediante un láser.
3.1. Condiciones del ensayo
A continuación se muestran en la Tabla 2 las principales condiciones del ensayo realizado para una misma aplicación de rectificado por 2 muelas abrasivas diferentes aunque similares. La única diferencia entre ambas muelas reside en el tipo de abrasivo. Se trata de muelas con tamaño de grano, dureza y estructura medias donde la muela 5MBA 46 G 12 V489P24P (en adelante Muela 1) contiene alúmina blanca y monocristalina a partes iguales y la muela MBA 46 G 12 V489P24P (en adelante Muela 2) contiene alúmina blanca en su totalidad.
El ensayo consiste en un ciclo estándar de rectificado, que consta de pasadas de desbaste, acabado y chispeo y es repetido 15 veces.
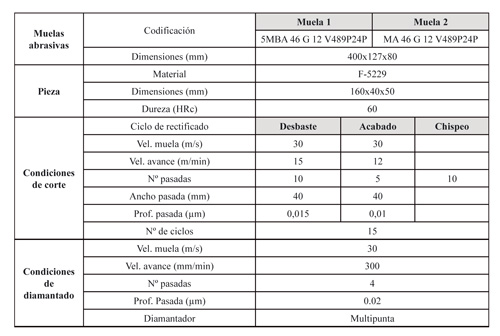
Las condiciones de corte utilizadas son las recomendadas por el fabricante de las muelas abrasivas utilizadas durante el ensayo.
3.2 Resultados
A continuación se procede al análisis de las variables de salida especificadas anteriormente.
En cuanto a la rugosidad, (ver Figura 2 (a)), con la Muela 1 se obtiene mejor rugosidad cuanto más se utiliza la muela realizando mayor número de ciclos de rectificado. Los valores de rugosidad representan la media aritmética obtenida de la toma de 6 medidas sobre la superficie rectificada a la finalización de cada ciclo de rectificado.
Por otra parte, la diferencia entre las tolerancias de planitud obtenidas a lo largo del uso de las muelas es mínima, tal y como se muestra en la Figura 2 (b). Se percibe un deterioro de la planitud de alrededor de 5 μm a la finalización del ensayo en la Muela 1. La medida se ha realizado mediante láser, realizando un barrido en diagonal de la superficie rectificada.
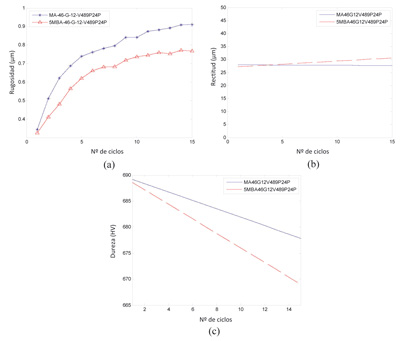
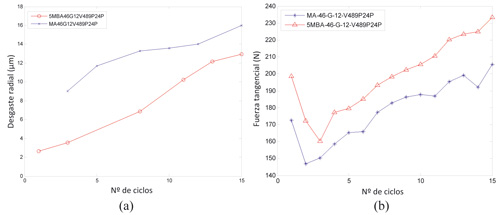
Respecto a la dureza superficial, se observa una ligera caída según se realizan los ciclos de rectificado (ver Figura 2 (c)). La pequeña variación de dureza, unida a la ausencia de zonas ennegrecidas confirmada mediante inspección visual, permiten concluir la inexistencia de dañado térmico sobre la pieza tras el rectificado con ambas muelas. Los valores representados responden, al igual que en el caso de la rugosidad, a la media aritmética obtenida sobre 6 medidas realizadas.
En cuanto a la medición de variables realizadas sobre la muela, se ha determinado el desgaste radial sufrido por la muela abrasiva al final del ensayo. Tal y como muestra la Figura 3 (a), la Muela 2 se desgasta en menor cantidad que la Muela 1. Es necesario resaltar que la diferencia corresponde a unas pocas micras. Siendo el tamaño de grano de ambas muelas igual a 46, el diámetro del grano abrasivo es igual a 0,33 mm [2]. Debido a que el desgaste radial producido es sensiblemente al diámetro de los granos, es posible asegurar que las muelas no han sufrido un reafilado por rotura del aglomerante.
Por último, se ha realizado el análisis de las fuerzas de corte obtenidas durante los ensayos. Se observa (ver Figura 3 (b)) que la fuerza de corte es mayor en el rectificado con la Muela 1. Las fuerzas son obtenidas a partir de la potencia consumida por la máquina y representan la media de las fuerzas de corte generadas durante las 5 últimas pasadas de las 10 pasadas que conforman la operación de desbaste. Ello es debido a que durante este tramo se concentran las mayores fuerzas de corte generadas durante el ciclo y se encuentran relativamente estabilizadas.
3.3. Conclusiones y líneas futuras
La lectura de los datos obtenidos en las variables de salida analizadas permite determinar el mejor rendimiento de la Muela 1 sobre la Muela 2. De forma resumida, se puede asegurar que ofrece mejores resultados en la rugosidad obtenida sobre la pieza y la evolución de su desgaste es menor. A pesar de que se produce una ligera mayor caída de la dureza superficial, no es para nada significativa ni indica riesgo de dañado térmico inmediato. Sin embargo, y considerando que las medidas de fuerzas proceden de la potencia consumida durante el rectificado, sería conveniente un análisis más exhaustivo del efecto del desgaste sobre la potencia consumida, de forma que no se alcance el umbral de la potencia límite de quemado según los modelos predictivos de dañado térmico existentes, tales como el Modelo de Malkin [2].
En cuanto a las líneas futuras y a pesar de que la metodología descrita permite comparar el rendimiento de cualquier muela que sea sometida al plan de ensayos detallado, se cree necesario profundizar en cómo se produce el desgaste de las muelas abrasivas. Este hecho, además de permitir conocer su rendimiento y duración de vida, permitirá realizar un análisis del coste que supone utilizar una u otra muela, con todo lo que conlleva en términos de productividad.
4. Software de recomendación de muela
La posibilidad de determinar el rendimiento de una muela abrasiva para una aplicación de rectificado y el poder compararlo con cualquier otra muela ha permitido el desarrollo de una herramienta de recomendación de muelas. Esta metodología, unida al conocimiento adquirido por el personal técnico del fabricante de muelas Abrasivos Unesa S.L. debido al desarrollo de su propia actividad, ha supuesto el germen del software de selección de muela óptima Grinsel.
La estructura seguida en el desarrollo del software se muestra en la Tabla 3 y se basa en el siguiente principio; partiendo de una aplicación de rectificado concreta se definen las variables de entradas que servirán para definir los requerimientos a obtener en dicha aplicación. En función de los requerimientos demandados, se han definido reglas de recomendación combinando tanto la experiencia de Abrasivos Unesa S.L. como los resultados obtenidos utilizando la metodología descrita en el apartado 3. La recomendación de muela se obtiene de la selección de cada una de las características de muela de manera individual.
Dotado de una interface amigable, según se muestra en la Figura 4, que facilite su uso, permite la recomendación rápida y sencilla de la muela que mejor se ajusta a las especificaciones de la aplicación de rectificado definida.
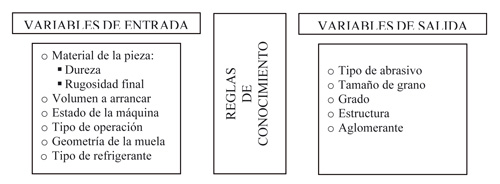
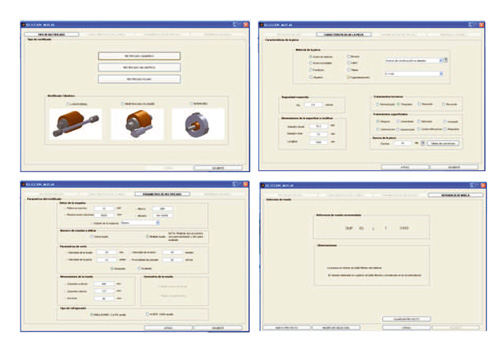
Con el objeto de definir el algoritmo de funcionamiento del software se han definido por cada una de las variables de salida las tablas correspondientes que la relacionan con las variables de entrada a considerar. Estas tablas conforman la base de datos del software, sobre las cuales se ha definido su código de actuación mediante el software Matlab.
Agradecimientos
Los autores agradecen al Gobierno Vasco la ayuda ofrecida al proyecto Abrasel (IG- 2011-0000011), así como a la empresa Abrasivos Unesa S.L. su participación e implicación en el desarrollo del proyecto.
Referencias
[1] Fernández, R. & Iriarte, A. & Puerto, P. & Gallego, I. & Arrazola, P.J., Analysis of the behavior of grinding wheels in surface grinding, 4th Manufacturing Engineering Society International Conference, 2011, Cadiz. [
2] Malkin S. & Guo C., Grinding Technology: Theory and Applications of Machining with Abrasives, Industrial Press, 2008, New York (USA).
[3] Li, Y. & Mills B. & Rowe W. B., An intelligent system for selection of grinding wheels, Proceedings of the Institution of Mechanical Engineers, v 211, n 8, p 635-641, 1997.
[4] Zhu, C. B. & Midha, P. S. & Trmal, G. J. Development of Knowledge Based Abrasive Wheel Selection System using a Proprietary Expert System Shell, Proceedings of 4th International Congress on Condition Monitoring and Diagnostic Engineering Manufacturing, p 318-325, 1992.
[5] Nakajima, T., A New Standard for Proper Selection of Grinding Wheels in Plunge Grinding Operation, Annals of the CIRP, v 27, n 1, p 249-253, 1978.
[6] http://www.cumi-murugappa.com/abrasives/gws.php
[7] Anon., Grinding Wheel Selection, Metalworking Production, v 141, n 6, p 53-58, 1997.
[8] Hodges, K., Selecting Abrasive Wheels for Cylindrical Grinding, Foundry Trade Journal, v 160, n 3332, p 150-152, 1986.
[9] Practical method of selecting grinding wheels for tool steels, 1970.
[10] Li, Y. & Mills B. & Rowe W. B., An intelligent system for selection of grinding wheels, Proceedings of the Institution of Mechanical Engineers, v 211, n 8, p 635-641, 1997.
[11] Fukuda, T., Correct Selection of Superabrasive Wheels, Industrial Diamond Review, v 63, n2, p 19-23, 2003.
[12] Malm, B., A Technical Approach to Grinding Wheel Selection, Iron and Steel International, v 54, n 3, p 149-156, 1981.
[13] Anon., Practical method of selecting grinding wheels for tool steels, Norton Company, Grits and Grinds, v 61, n 6, p 3-11, 1970.
[14] Anon., Tips for Selecting Abrasive Wheels, Metabo Corporation, Welding Journal, v 81, n5, p 33-34, 2002.
[15] Jackson, M. J. & Wakefield, R. T., Materials Selection Applied to Vitrified Corundum Grinding Wheels, British Ceramic Transactions, v 100, n 5, p 229-236, 2001.
[16] Wilson, J. V., What You Should Know About Grinding Wheels, Manufacturing Engineering, v 78, n 6, p 40-44, 1997.
[17] Krar, S., Grinding Technology, Delmar Publishers, 1995, Albany (USA).
[18] Pelaez, J., Maquinas Herramienta Auxiliares, Cedel, 1993, Barcelona (España).
[19] East, W. R., Developments in Abrasive Products, Foundry Management and Technology, v 116, n 8, p 58-64, 1988.
[20] Rooney, G. G., Selection of Wheels for Modern JIG Grinding, The Carbide and Tool Journal, v 17, n2, p 2-4, 1985.
[21] Información técnica, http://www.nortonabrasivos.es/documentos/ biblioteca/archivo_54.pdf, Abrasivos Norton.
[22] Sepúlveda, E., Propiedades Mecánicas de los Materiales de Muelas Abrasivas Convencionales, 7th Inter-American Conference on Materials, p 439-445, 1981.
[23] Smits, C., A Grinding Principles and Practice (A Machining Xcellence TM Course), TechSolve, 2003, Cincinnati (USA).
[24] Hodges, K., Selecting Abrasive Wheels for Cylindrical Grinding, Foundry Trade Journal, v 160, n 3332, p 150-152, 1986.
[25] Fan, K.C. & Lee, M.Z. & Mou, J.I., On-Line Non-Contact System for Grinding Wheel Wear Measurement, The International Journal of Advanced Manufacturing Technology, v 19, n 1, p 14-22, 2002.
[26] Young, H. & Chen, D., Online Dressing of Profile Grinding Wheels, The International Journal of Advanced Manufacturing Technology, v 27, n 9-10, p 883-888, 2006.
[27] Brinksmeier, E. & Werner F., Monitoring of Grinding Wheel Wear, Annals of the CIRP, v 41, n 1, p 373-376, 1992.
[28] Handigund, P.B. & Miller, M.H., Abrasive Wear and Forces in Grinding of Silicon Carbide, Proceedings of the American Society for Precision Engineering (ASPE) Annual Meeting, p 413-416, 2001.
[29] Marinescu I.D. & Rowe W.B., Tribology of Abrasive Machining Processes, William Andrew Publishing, 2004, Norwich (USA).
[30] Badger, J. A., The Book of Grinding, 2010, Texas (USA). [31] [Su06] Su, J. C. & Tarng, Y.S., Measuring Wear of the Grinding Wheel Using Machine Vision, The International Journal of Advanced Manufacturing Technology, v 31, p50-60, 2006.
[31] [Su06] Su, J. C. & Tarng, Y.S., Measuring Wear of the Grinding Wheel Using Machine Vision, The International Journal of Advanced Manufacturing Technology, v 31, p50-60, 2006.