¿Qué puede aprender la logística de la producción Lean?
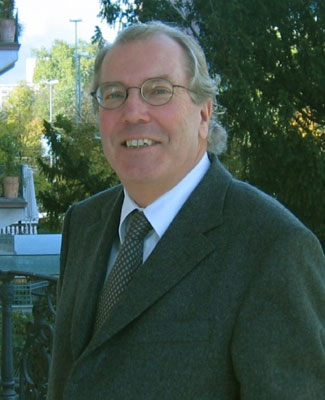
¿Qué hay detrás de la producción Lean?
En los últimos años la palabra ‘Lean’ ha experimentado un renacimiento considerable: producción Lean, procesos Lean, o inventarios Lean, por ejemplo, son conceptos que han adquirido relevancia en muchas discusiones como expresiones sinónimas de Gestión Total de la Calidad, Sistema de Producción Toyota, Kaizen o Cadena de Valor.
Considero que detrás de esta tendencia se encuentra el deseo de volver a las estructuras y a los procesos simples del pasado, para encontrar una respuesta a la complejidad creciente de la producción y la gestión de la cadena de suministros, donde los márgenes son cada vez más pequeños y la competencia cada vez más fuerte, y donde los algoritmos altamente sofisticados se han apoderado del control de los procesos.
Si nos remontamos a los orígenes de la filosofía ‘Lean’, su esencia puede reducirse a tres premisas:
- Son los trabajadores y empleados, con su inteligencia, quienes gobiernan las operaciones (y no unos complejos algoritmos).
- La lógica debe ser fácil de entender, simple y transparente.
- Salga a la planta de producción y observe: los ordenadores no pueden detectar los potenciales de mejora.
El poder del ‘Lean’ fue descrito ampliamente por primera vez en el libro ‘La máquina que cambió el mundo’, publicado en 1980 por un grupo de profesores del MIT. Compararon los procesos de producción de GM con el Sistema de Producción Toyota, conduciendo a los responsables de producción occidentales a cuestionarse los fundamentos de su filosofía de operaciones.
|
GM Framingham |
Toyota Takaoka |
Horas brutas de montaje por automóvil (tiempo total de trabajo / autos producidos) |
40,7 |
18,0 |
Defectos de montaje por cada 100 automóviles (en función a una encuesta a clientes) |
130 |
45 |
Espacio productivo, en m² por automóvil (espacio total/ automóviles producidos) |
0,75 |
0,45 |
Inventarios de piezas (promedio) |
2 semanas |
2 horas |
No existe una definición unánimemente aceptada de lo que es ‘producción Lean’, pero la siguiente definición puede funcionar como ‘descripción de trabajo’.
La producción Lean es la combinación de:
- El Sistema de Producción de Toyota, desarrollado por la empresa Toyota entre 1950 y 1980.
- El modelo ‘Six Sigma’ de Motorola (una metodología para lograr una calidad sobresaliente: ‘Sólo 3 defectos por 1 millón de oportunidades’).
- Hallazgos adicionales del MIT, como el abastecimiento modular y la ingeniería simultánea.
La siguiente tabla ofrece los ingredientes más importantes de cada uno de estos 3 métodos:
Sistema de Producción Toyota
|
+ |
Six Sigma |
+ |
Adiciones del estudio MIT |
= |
Sistema de Producción LEAN |
|
|
|
|
|
|
|
¿Qué puede aprender la Logística de la Producción?
O, más concretamente: ¿Existen elementos de la filosofía de producción Lean, obviamente poderosa, que puedan transferirse a la logística (refiriéndonos a los procesos de almacén y no tanto a los temas de transporte y distribución)?
A primera vista hay una serie de similitudes: problemas de automatización, flujo y gestión de colas, cuestiones de reposición, el proceso de picking tiene algunas similitudes con el trabajo de montaje, etc. Pero también hay grandes diferencias: en la producción, el flujo de trabajo puede ser nivelado, los mismos movimientos de montaje se repiten varios cientos de veces al día, las operaciones pueden planificarse perfectamente con unos días de antelación… En logística, sin embargo, vemos una enorme variación en las actividades diarias, no hay ni un solo proceso de preparación de pedidos idéntico al siguiente y la estructura de pedidos del turno de mañana es diferente a la del turno de tarde, por ejemplo.
Por lo tanto, vale la pena ilustrar estas similitudes y diferencias a través de distintos ejemplos.
Ejemplo 1: Puestos de trabajo
La optimización de los puestos de trabajo en plantas de producción y en almacenes es muy similar. Por consiguiente, los métodos Lean son muy aplicables: visibilidad, mejora continua, ir y ver, consenso en workshops, aprendizaje, formación… En muchos casos, estos aspectos aumentan la productividad en el almacén más de un 5% anual.
Ejemplo 2: Operaciones con cero defectos
La tasa de error en los almacenes (1 a 5 por mil) está muy lejos de la tasa que se puede llegar a alcanzar en producción (1 a 5 por millón), debido a las características de los procesos de picking y de embalaje. Sin embargo, la mayoría de los métodos de mejora de calidad de la metodología Lean puede aplicarse (círculo de calidad Six Sigma, mejora continua, ir y ver, etc.), siendo lo más importante el enfoque: evitar los errores y detectarlos y corregirlos dónde se producen es mucho más eficaz que utilizar los procedimientos de verificación posteriores.
Ejemplo 3: Automatización
Vemos una clara tendencia hacia una creciente automatización en las operaciones de almacenaje: sistemas ASRS, lanzaderas múltiples, AGV, sistemas de clasificación, robots para embalaje, etc. ¿Es esto una contradicción con los principios Lean? No, siempre y cuando estas ‘máquinas’ sean parte de un flujo de materiales optimizado bajo la filosofía Lean, por ejemplo incorporando principios como ‘pull’ en lugar de ‘push’, operaciones niveladas, bajo inventario, procedimientos de cero defectos, etc.
Es tarea de los ingenieros de flujo de materiales diseñar estas ‘máquinas’ de manera que se adapten a un entorno global Lean. Eso sí: una vez instalados, los métodos de mejora como el Kaizen, los workshops, el ir y ver, etc. tienen menor margen de aplicación, ya que la ‘máquina’ en cuestión se convierte en una parte fija dentro del flujo de materiales.
Ejemplo 4: Reposición y disposición
Hay una diferencia fundamental entre la reposición (disposición, gestión de inventario) en la producción y a lo largo de la cadena de suministros: la producción tiene que apoyarse en una disponibilidad total de las piezas a lo largo de la cadena de montaje. En la distribución de piezas de recambio, por ejemplo, o en la reposición de bienes de consumo de un almacén central hacia las tiendas al por menor, una disponibilidad del 100% de los artículos no puede garantizarse ni es deseable. Una disponibilidad alta se paga con unos costes de inventario también altos, y la gestión del inventario tiene que saber encontrar un equilibrio entre el nivel de inventario y el nivel de servicio:
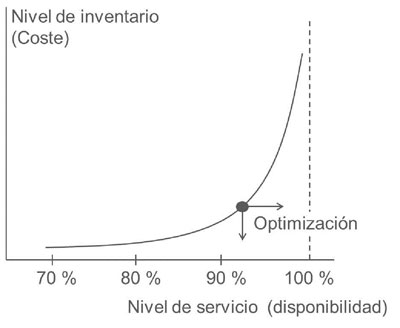
Esto no puede obtenerse sólo a través de métodos Kanban o de flujos continuos (‘one piece flow’). Cada orden de reposición de alguna manera influye en el equilibrio entre el desabastecimiento y la acumulación de excedentes. La siguiente tabla muestra los parámetros más importantes y las variables que deben tenerse en cuenta en cada actividad de reposición:
Parámetro |
Variables |
Demanda (ventas) |
Pronóstico, tendencias, variaciones, estable-caótico |
Tiempo de Reposición |
Características del proveedor, limites de producción, calidad, tiempo de guardado |
Cantidades estándar de reposición |
Contenedores / tamaño del contenedor, tipos de contenedores, aforo |
Coste del espacio del contenedor |
Dependiendo del área almacenada |
Coste de Almacenaje Coste de Proceso de reposición |
Dependiendo de la cantidad de reposición, el tipo de contenedor, el proveedor, el coste del transporte |
Suministro combinado |
Varios ítems de un proveedor, coste del transporte, costes de administración |
Coste de quiebre de stocks |
Coste de ventas, pérdida de ventas, pérdida de clientes |
Stock de Seguridad |
Variación de la demanda, variación de la fiabilidad del proveedor |
Valor del ítem Coste de capital |
Función de la cantidad de reposición, tasa de interés de mantener el inventario |
Estado de Inventarios |
Inventario en estanterías, canal de reposición, canal de ventas |
La solución es la ‘Disposición Dinámica’:
- Combinación de los métodos de reposición de la cantidad consumida, punto de reposición y frecuencia fija de reposición.
- Actualización continua de las características y parámetros del producto.
- Cada venta, cada cambio de parámetro, desencadena un nuevo cálculo de la reposición.
El resultado es un proceso de simulación: si la calidad de reposición es X y si hay un suministro combinado con otros productos, entonces el impacto probable de roturas de stock y los niveles de inventario es W.
Ejemplo 5: Programación de las operaciones
La programación de las operaciones de producción se ha desarrollado durante las últimas décadas más allá de los métodos simples de ‘pull’ o Kanban hacia sistemas avanzados de MRP, producción sincronizada JIT (especialmente en la producción masiva de automóviles) y programación de flujo orientada a cuellos de botella.
Y esto es lo que debería pasar con la programación de las operaciones de almacén. Lo que llamamos ‘Back Line Planning’ tiene las siguientes características:
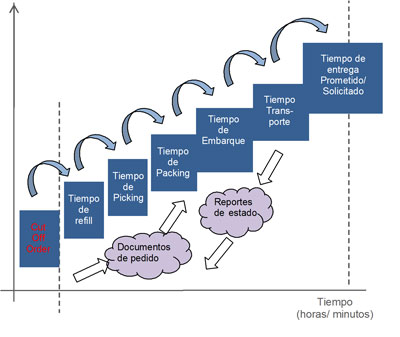
- Hay una monitorización en tiempo real de la utilización de los puestos de trabajo a lo largo del flujo de procesos a través del almacén.
- El sistema de gestión de almacenes simula la mejor combinación de inicio de pedidos individuales, permitiendo:
- Satisfacer la hora de entrega del pedido prometida al cliente.
- Una carga de trabajo equilibrada (en lo posible) sobre todos los puestos de trabajo.
- Reducir las colas a un mínimo.
De nuevo, este es un proceso de simulación continua, provocado por cada entrada de pedido.
Conclusiones
- Los métodos y los procedimientos Lean son aplicables en lo que respecta a la mejora continua de los puestos de trabajo, la introducción de técnicas de cero defectos o el diseño de subsistemas automáticos.
- Se requieren matemáticas, algoritmos y herramientas de simulación más avanzadas para la gestión de inventarios y la programación de operaciones.
Por todo ello, la esencia es lo que llamamos Logística Lean Avanzada, que es la combinación de una selección de elementos de producción Lean con algoritmos computarizados.