ASTI mejora la eficiencia de DHL con sus soluciones de picking por luz
Para la realización del picking de unidades sueltas, DHL contaba con un sistema de terminales de radiofrecuencia con los que no se encontraban plenamente satisfechos.
Por esto entraron en contacto con ASTI para la implantación de un sistema de pick to light, en busca de una mayor eficiencia. El número de ubicaciones de estantería que se pretendía cubrir con este nuevo sistema era de casi 800, con una referencia de producto asignada a cada una de ellas.
El picking por luz consiste en la utilización de displays como indicadores de referencia y cantidad de producto a incorporar en un pedido. Tras la identificación de un pedido, el sistema indica mediante señales luminosas el lugar donde se encuentra el primer producto que forma parte del mismo, indicándose en el display la cantidad exacta. Una vez que se ha recogido el material se confirma la acción mediante pulsación y el sistema procede a indicar el siguiente producto a añadir y así sucesivamente, hasta concluir el proceso, hecho que se indica en el display para darlo por terminado y proceder con su embalaje, dejando paso a uno nuevo. De este modo se eliminan las búsquedas de producto y se reducen los errores, agilizando el proceso.
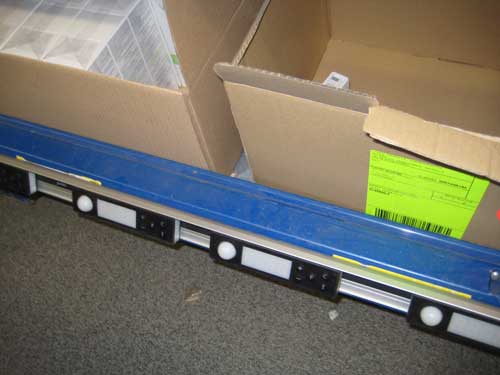
ASTI se encargó a partir de la necesidad concreta de DHL y del análisis de la misma, de diseñar una solución tanto a nivel hardware (seleccionando que dispositivos son necesarios para la solución), como a nivel software (analizando, diseñando y creando las aplicaciones, además de los interfaces necesarios con el software del cliente que van a formar parte de la solución) ocupándose totalmente de la implantación de la solución, llevando a cabo la instalación, configuración, documentación, formación y puesta en marcha del sistema.
A nivel hardware, ASTI buscó unos novedosos displays que le permiten ofrecer mayores funcionalidades del sistema al contar con la propiedad de poder emitir hasta ocho colores de luz distintos, lo que se traduce en la capacidad de preparar ocho pedidos simultáneamente por operario o bien la de poder trabajar hasta ocho operarios simultáneamente por display para la preparación de pedidos, contribuyendo a obtener mayores tasas de productividad.
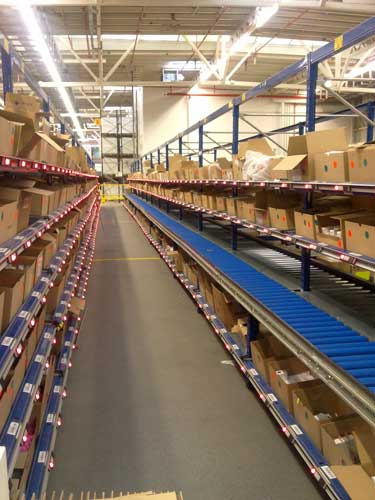
Gracias a esta propiedad de los displays, se diseñó un software multipicking, que le permite al operario ocuparse de un único tramo de picking a la vez que prepara hasta ocho pedidos simultáneamente, eliminando los desplazamientos entre ubicaciones y el tiempo que ello conlleva. Con el nuevo sistema desarrollado, los contenedores son los que se desplazan a lo largo de las líneas de picking. Cada contenedor se relaciona con el color de un pedido de manera que a su paso, el operario sólo incluye las unidades de producto que el display identifica con el color del contenedor.
Para un mejor funcionamiento, el sistemacuenta con un software de cálculo volumétrico, de tal manera que antes iniciar un pedido ya se sabe el tipo de contenedor que va a necesitar, evitándose tareas de intercambio por una mala elección del mismo.
Este sistema está en comunicación con el ERP de DHL, que es el que lanza los pedidos a realizar y las señales a emitir por los distintos displays. También comunica con elpuesto de final de línea, que en un proyecto anterior ASTI ya había instalado, en el cual se realiza el pesaje de los bultos preparados en el picking, rechazando aquellos cuyo peso no es correcto, evitando así que se envíen al cliente paquetes cuyo contenido no es el requerido, por falta de producto, por envío de producto no solicitado o por el envío de mayor cantidad de producto del solicitado.
Con todo esto, la adopción de este sistema se llevó a cabo de manera rápida, sin interferir en el desarrollo de sus operaciones.
La instalación fue muy sencilla ya que los displays no precisan tapas ni complicados cableados, lo que conlleva una ventaja adicional, un fallo en uno de los displays no implica la parada del resto de la línea, facilitando su reparación y en caso de ser necesaria su sustitución única.
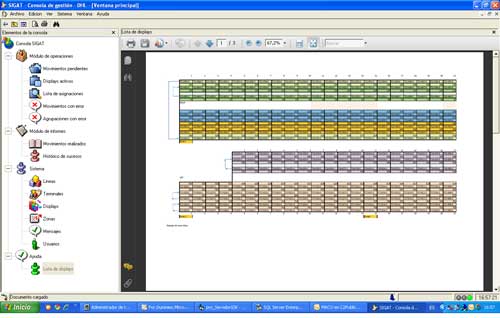
Según informan desde la compañía, los operarios han notado una gran mejora en su puesto de trabajo ya que el nuevo sistema es más sencillo de manejar, requiere muy poca formación, les deja las manos libres para dedicarse a la recogida de producto y les permite, debido a la operativa implantada, la preparación de varios bultos de forma simultánea. Cada operario sólo se encarga de su tramo de la línea de picking, permitiendo el sistema crear nuevos tramos es caso de ser necesario. Además, esta solución supone un significativo aumento en productividad ya que tras la implantación del sistema se preparan más bultos por hora, más del doble que con el sistema anterior, y con menos operarios por turno. Y gracias a las órdenes precisas del picking por luz, y al puesto de verificación con control de peso, los errores se han eliminado en su práctica totalidad.