Verne - Un centro de mecanizado de cinemática paralela de 5 ejes
Esta es la razón por la cual el IRCCyN [2] ha adquirido una máquina de cinemática paralela desarrollada por Fatronik [3]. El objetivo de este artículo es, en primer lugar, presentar la nueva máquina de Fatronik y, en segundo lugar, mostrar los primeros resultados en mecanizado, especialmente en el mecanizado de superficies libres de forma.
Verne una nueva máquina híbrida de mecanizado en 5 ejes
Verne es un centro de mecanizado de cinemática paralela de 5 ejes que ha sido desarrollado por el Centro Tecnológico Fatronik. Su característica principal es que combina cinemática paralela y serie, perteneciendo así a la familia de máquinas híbridas. El módulo paralelo proporciona las traslaciones X, Y y Z; el módulo serie es una mesa basculante (tilting) que proporciona los ángulos B y C tal y como se muestra en la Figura 1. El eje del cabezal está inclinado 30º respecto de la vertical y, el volumen de trabajo está libre de singularidades.
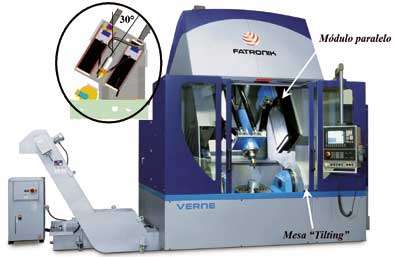
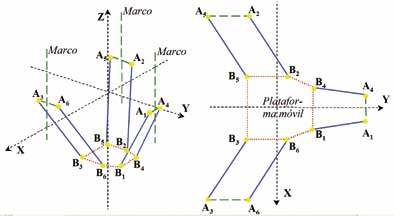
En esta sección, se explican las transformadas cinemáticas. Las coordenadas cartesianas (pieza) se denominan como [X, Y, Z, B, C] y las de la máquina como {V1, V2, V3, Ba, Ca}.
Con el fin de definir el movimiento de la máquina, se han utilizado tres conjuntos de sistemas de coordenadas, tal y como se muestra en la Figura 3. El primero es el sistema de coordenadas absoluto R0 , que está ligado a la estructura de la máquina. El segundo es el sistema de coordenadas de programación RM de 5 ejes, vinculado a la mesa basculante (tilting). El último es el sistema de coordenadas del cabezal RT.
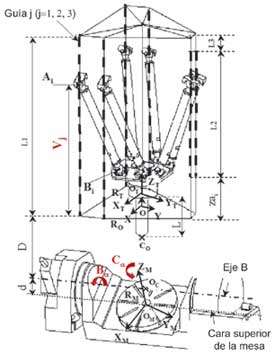




Las seis ecuaciones son:

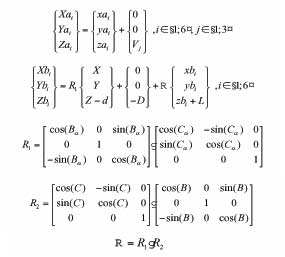
En estas ecuaciones, los vectores {xbi, ybi, zbi} y {xai, yai, zai} son parámetros de diseño conocidos.
Cuando el problema considerado es la transformada inversa, los valores conocidos son {X, Y, Z, B, C} y las incógnitas son {V1, V2, V3, Ba, Ca}. Sin embargo, en lo que a la transformada directa se refiere, los valores conocidos son {V1, V2, V3, Ba, Ca} y las incógnitas son {X, Y, Z, B, C}. Como el sistema es no lineal y, está compuesto por seis ecuaciones para solamente cinco incógnitas [X, Y, Z, B, C], se utiliza un método numérico (algoritmo de Newton-Raphson) para resolverlo. Por consiguiente, con esta transformada se puede controlar Verne.
Estos modelos cinemáticos (principalmente la transformada directa) son de gran importancia para la transformación de los datos de los encoders en coordenadas cartesianas, tal y como se explica en el apartado 3.3.
Los primeros resultados de mecanizado en Verne
Las primeras pruebas se han realizado con la pieza test de la Figura 4, que contiene las principales superficies libres de forma que pueden encontrarse en la industria del molde y matriz [1]
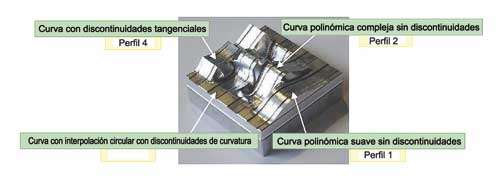
Las piezas se han mecanizado en bloques de aleación de aluminio. En un primer paso las mediciones se han realizado en una Máquina de Medir por Coordenadas (CMM), ya que la pieza test está compuesta por superficies libres de forma (Figura 5).
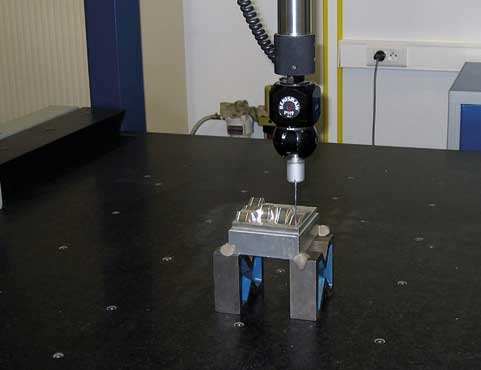
En un segundo paso, tal y como se explica en el apartado 3.3, se han realizado mediciones a partir de la lectura de los encoders.
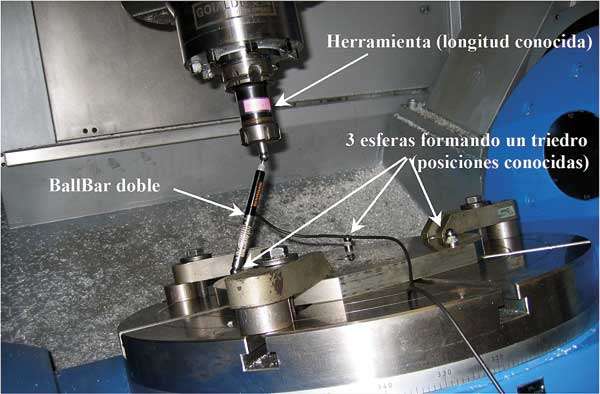
Con el fin de analizar la influencia de la calibración, se mecanizó una pieza antes de la primera calibración de la máquina (PKM I-a) y, otra justo después (PKM I-b). En la Figura 6 se representa la amplitud del error de contorno (expresado en porcentaje) para los cuatro perfiles y las dos configuraciones de máquina (antes y después de calibrar). El error de contorno es el error de componente, ortogonal a la trayectoria deseada (es decir, la desviación mínima de la trayectoria real respecto de la deseada, según la normal).
Nota: La amplitud del error de contorno se define como la diferencia entre el error de contorno máximo y el mínimo, medidos en la CMM (Figura 9).
La primera calibración permite reducir aproximadamente tres veces la amplitud del error de contorno. Por lo tanto, queda de manifiesto la gran importancia de la calibración para la precisión de la máquina. Verne volverá a ser calibrada de nuevo en unos meses, por lo que, probablemente, mejorará de nuevo su precisión.
Todos los resultados que se exponen en los siguientes párrafos corresponden a la configuración tras la calibración, PKM I-b.
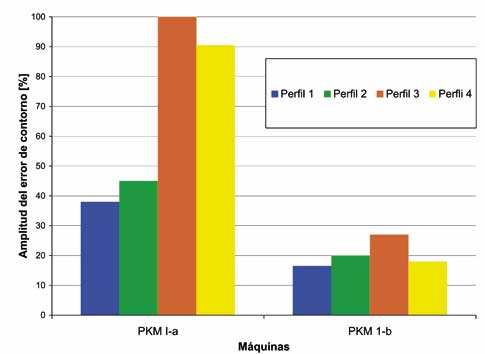
Las piezas PKM I-a y PKM I-b (también denominada en esta sección PKMI-b_0) se han colocado paralelamente al eje X (q=0°, ver Figura 8). Con el fin de determinar la influencia de la orientación de la pieza en la mesa, se han mecanizado dos piezas más; así, PKM I-b_90 corresponde a una colocación paralela al eje Y (q=90°), y PKM I-b_45 a un posicionamiento a 45° (q=45°).
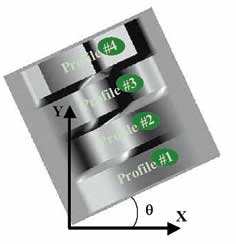
Se demuestra que la orientación de la pieza paralela al eje Y (PKM I-b_90) proporciona la mejor precisión, cualquiera que sea el perfil considerado. Este resultado puede explicarse por la cinemática de la propia máquina. En realidad, debido al diseño del modulo paralelo, existe un grado de libertad extra (además de las tres translaciones X, Y, Z)
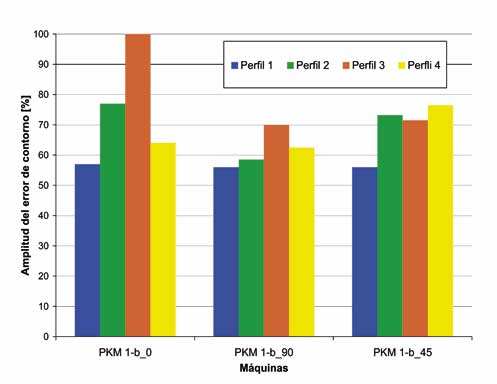
Sin embargo, para la velocidad de avance programada (6m/min) la diferencia entre las tres orientaciones es limitada. Se están realizando más ensayos con el fin de estudiar la influencia de la velocidad de avance en la orientación de la pieza sobre la mesa.
Todos los resultados que se dan en los siguientes párrafos corresponden a la configuración de orientación paralela al eje Y (q=90°).
Influencia del método de interpolación de la trayectoria de herramienta
Con el fin de analizar este parámetro CAM, se ha mecanizado una pieza (colocada paralela al eje Y) usando un método de interpolación B-Spline (PKM I-c).
La Figura 9 indica el error de contorno medido en la CMM para el perfil 1. La escala es la misma para los dos gráficos. Considerando el perfil 1, se tarda 2.24s en realizar una pasada con un método de interpolación lineal (G1) y, 2.2s con una interpolación tipo B-Spline. Por consiguiente, para la velocidad de avance programada de 6m/min, la interpolación con B-Spline permite reducir el tiempo de mecanizado, a la vez que mejora la precisión.
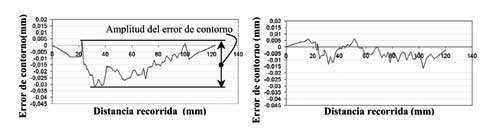
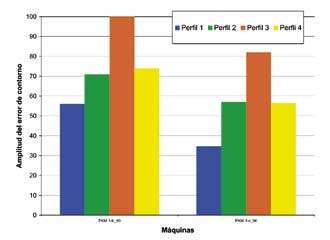
Los ensayos realizados hasta ahora se han llevado a cabo a una velocidad de avance programada de 6m/min, con una velocidad de cabezal de 18.000rpm (de PKM I-a a PKM I-c). Con el fin de estudiar el comportamiento de la máquina a diferentes velocidades de avance, en un primer paso se estableció una velocidad de avance de 7,7 m/min a 24.000 rpm (PKM I-d_90). En un segundo paso, la velocidad de avance programada se incrementó a 14.4m/min para una velocidad del cabezal de 24.000 rpm (PKM I-e_90). Como se ha mencionado anteriormente, la pieza se colocó paralela al eje Y (q=90°). En la Figura 11 se representa la amplitud del error de contorno medido en la CMM.
Es importante recordar que la máquina no se encuentra en su estado óptimo aún y que, por lo tanto, no se han optimizado todavía todos los parámetros de control. Este hecho puede explicar el distinto comportamiento a diferentes velocidades de avance programadas. Tan pronto como la máquina esté optimizada, se realizarán más pruebas y los datos obtenidos se compararán con los actuales. De cualquier forma, este análisis es de gran relevancia para mostrar la influencia de la velocidad de avance en la precisión, cuando la máquina no está bien ajustada.
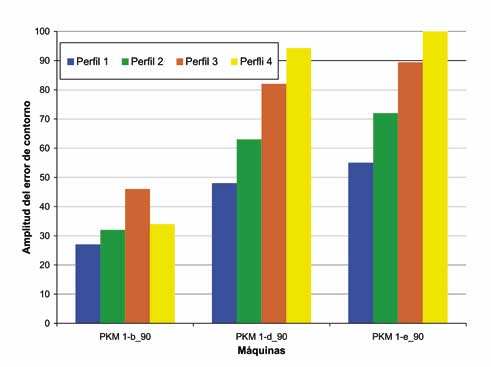
Estas primeras pruebas han demostrado la importancia de tener en cuenta todos los parámetros que influyen en el proceso de producción, con el objetivo de mejorar la precisión de las máquinas-herramienta (tanto de arquitectura serie como paralela). Comparando los resultados obtenidos en Verne con los del conjunto de máquinas-herramienta analizadas por el IRCCyN [1], se demuestra que esta máquina alcanza el mismo nivel de precisión que algunas SKM.
Sin embargo, debido al gran número de parámetros de mecanizado, su optimización no es lo suficientemente sencilla y rápida a la hora de mecanizar una pieza. Por consiguiente, una solución para ganar tiempo es analizar la lectura de los encoders, tal y como se explica en el próximo apartado.
Medidas con los encoders
En investigaciones previas en el IRCCyN, se ha desarrollado una nueva técnica para caracterizar una fresadora (es decir, para determinar la capacidad de una máquina para realizar una pieza con una tolerancia dada) [6], [7]. El objetivo principal es obtener las posiciones reales de la herramienta para cada eje, mediante la adquisición de la lectura de los encoders de los ejes durante el mecanizado, como se muestra en la Figura 13.
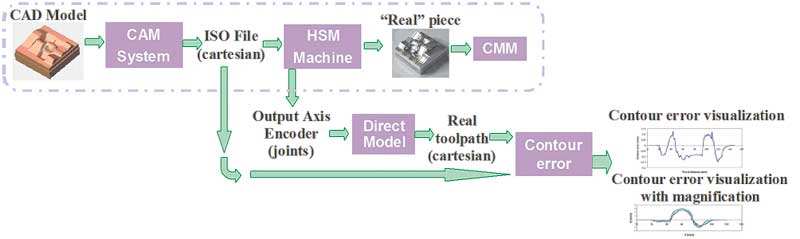
Nota: en lo que a la máquina Verne se refiere, el error máximo de transformada (directa o inversa) establecido en la pieza P1100 para los 4 perfiles (Figure 4) es de 3.5E-5mm. Así, estos errores son despreciables en la transformada directa, con la que se deduce la trayectoria real de la herramienta. (Figura 12).
Es importante tener en cuenta que para esta transformada se debe usar el modelo directo “real”. En realidad, en Verne se implementa un modelo en el Control Numérico para compensar los defectos de rectitud y paralelismo de los ejes. La Figure 13 muestra dos visualizaciones del error de contorno obtenidas a partir de los datos de los encoders.
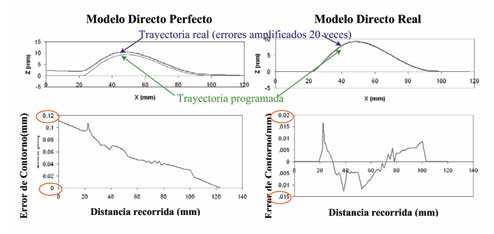
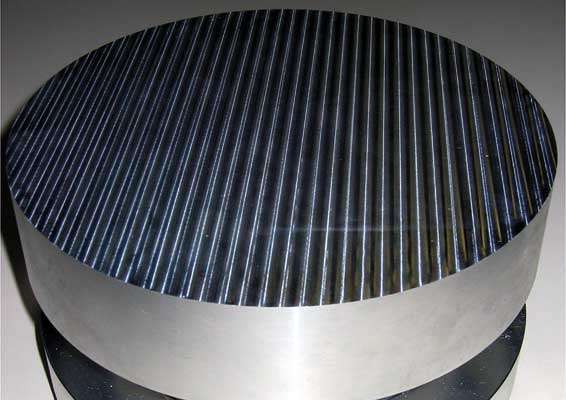
La visualización se ha realizado utilizando el interfaz de simulador de gráficos HSM [7] para obtener una visión realista de la pieza final. La Figura 15[a] corresponde a los datos de los encoders en el caso de Verne, mientras que la Figura 15[b] corresponde a los datos de los encoders en el caso de una máquina herramienta de arquitectura serie de 3 ejes.
Se constata la influencia de la arquitectura de la máquina en los resultados finales. Sin embargo, es importante recordar que la ventaja principal de las máquinas herramienta de cinemática paralela es su dinámica, que resulta más elevada que en las máquinas herramientas de arquitectura serie. Por lo tanto, se realizarán nuevas pruebas con el fin de determinar el campo de aplicación de las PKM.
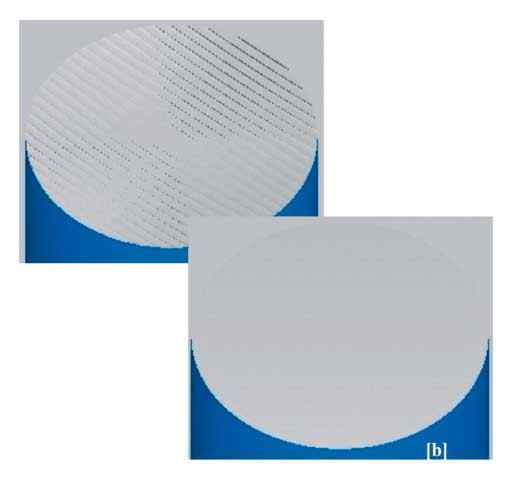
Conclusión
Por el momento, se concluye que Verne puede alcanzar el mismo nivel de productividad que algunas SKM.
Referencias
[2] Institut de Recherche en Communications et Cybernétiques de Nantes (IRCCyN), 1 rue de la Noë, BP 92101, 44321 Nantes Cedex03, France
[3] FATRONIK, Pol.Ind. Ibaitarte, 1, P.O.Box 160, 20870 Elgoibar (Gipuzkoa)-Spain, http://www.fatronik.com, Access July 2004
[4] RENISHAW, http://www.renishaw.com, Access July 2004
[5] MARTINEZ L., COLLADO V., Calibration of a Hybrid Serial/Parallel 5-Axes Milling Machine Using a Double BallBar Probe, 4th Chemnitz Parallel Kinematics Seminar, pp 137-150, Chemnitz, Germany, April 2004
[6] HASCOET J.Y., DUGAS A., LEE J.J., “Simulation des opérations d’usinage”, Rapport final du projet “Saut technologique UGV”, Institut de Recherche en Communications et Cybernétique de Nantes (IRCCyN), France, June, 2001, 161p
[7] DUGAS A., "CFAO et UGV - Simulation d’usinage de formes complexes", Thèse de Doctorat, Université de Nantes, Ecole Centrale de Nantes, France, 13 December, 2002