Ford Werke apuesta por AutoForm para sus procesos de conformación de chapa
9 de noviembre de 2011
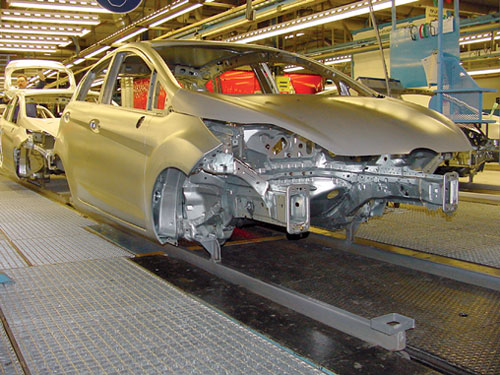
Ford comenzó la simulación de conformado de chapa metálica con su propio software. Debido al limitado potencial de desarrollo interno del mismo y los avances tecnológicos del mercado, Ford se vio obligado a buscar un software más eficiente. Se compararon varios programas y como resultado de este análisis, en 1997, Ford se decidió por el software de AutoForm Engineering. Desde entonces ha confiado en el programa y el uso de él no ha dejado de crecer. Aproximadamente la mitad de los especialistas en el equipo de Bernd Krömer trabajan actualmente con el software AutoForm. La introducción del software produjo, entre otras cosas, cambios en la organización. Hace cuatro años el departamento de Desarrollo de Chapa se fusionó con el de Procesos / FEM. Además actualmente hay miembros del equipo que se dedican sólo a estudiar, corregir y a afinar al detalle las conclusiones de los resultados de simulación de AutoForm-DieDesigner. Otros miembros del personal, a su vez, garantizan que los cambios en la herramienta se actualicen en el CAD. En total en los últimos años ha habido un aumento en el número de tareas que son responsabilidad directa del departamento de Bernd Krömer. Además el volumen de trabajo del departamento también ha aumentado como resultado del uso de nuevos módulos, ya que ahora tienen mayores exigencias de calidad a la vez que tiempos de desarrollo más cortos. Esto sólo se puede lograr de manera óptima con un software eficiente.
De la propuesta de diseño a la pieza final
Tanto si se está analizando la viabilidad de nuevas piezas como si se está en la fase de producción de las mismas, el personal en la central de Colonia no duda en utilizar AutoForm. Cuando la recuperación elástica es crítica, las superficies nominales se compensan de acuerdo con un cálculo previo de la robustez hecho con AutoForm-Sigma. Así es como Ford es capaz de asegurar una producción robusta de tal forma que sea totalmente fiable incluso con variaciones de condiciones del proceso, como por ejemplo, variaciones en las propiedades del material. Éstas no deben poner en riesgo dicha producción. Así Ford cubre con herramientas de simulación toda la cadena del proceso de conformado de chapa, desde casi la primera propuesta de diseño hasta la pieza terminada.
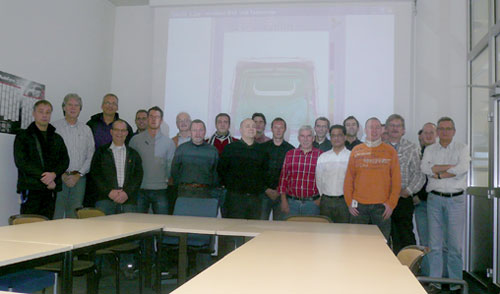
Más rápido y más económico
Como resultado de la cobertura total que ofrecen las herramientas de simulación, los tiempos de desarrollo se han reducido significativamente. Una mayor velocidad de cálculo junto a una optimización del hardware ayudan aún más a mejorar este punto. Las ventajas son evidentes ya que se necesitan una media de tres a cuatro modificaciones en piezas de materiales de ultra-alta resistencia (UHSS) hasta conseguir que la pieza sea factible.
Bernd Krömer remarca que el ahorro en tiempo y en costes fueron especialmente buenos con laterales fabricados con acero dual-phase y piezas complejas tales como tapamaletas o armazones de puerta. Basándose en su experiencia teniendo en cuenta el 90% de la producción de todas las piezas estampadas de la carrocería de un coche Ford, considera que el uso de AutoForm vale la pena en todas ellas.
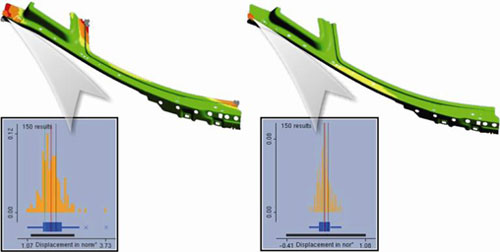
Ford compara constantemente los resultados de la simulación con los resultados de la producción e identifica zonas críticas en los análisis de FEM. El chequeo de los parámetros importantes de la producción, la documentación de mediciones, como por ejemplo de las curvas FLD, o simplemente el chequeo con variables de validación, hacen posible esta comparativa. La opinión de los especialistas de conformado de chapa del departamento de Die Systems Stamping Engineering Europe tiene una fuerte influencia sobre las cuestiones relacionadas con el método y como consecuencia también influye en la inversión de las herramientas y en el coste unitario de pieza. A través de simulaciones AutoForm les ayuda a decidir, por ejemplo, si un proceso sería factible con cuatro operaciones en lugar de con cinco, lo que permitiría ahorrar en costes.
Un mejor aprovechamiento del material ahorra costes adicionales
La utilización del material ha sido siempre un tema muy importante en Ford. El aumento del precio de las materias primas ha hecho que éste sea un tema todavía más importante. AutoForm-Nest permite a los especialistas en formato de chapa del equipo de Bernd Krömer aprovechar al máximo dicho formato o la banda de material. Como resultado, el aprovechamiento del material se ha incrementado en todos los modelos en aproximadamente un cuatro por ciento en los últimos cuatro años. Este nivel de aprovechamiento en los modelos actuales de Ford se encuentra por encima del nivel de otros fabricantes europeos, de tal forma que Ford consigue ahorrar una suma importante de dinero al año. Naturalmente, los especialistas en formato de chapa están interesados en aumentar aún más este aprovechamiento del material, por ejemplo, utilizando la zona de la ventana central de un portón para embutir piezas distintas.
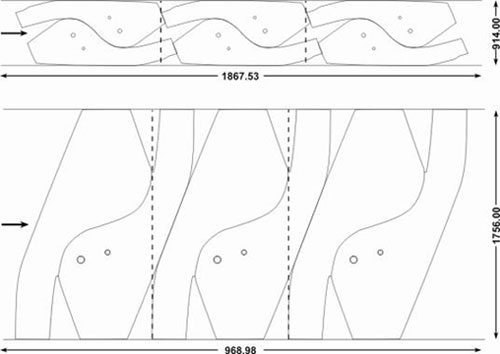
Revisión y previsión
En el pasado, los fabricantes de herramientas adquirieron cierto nivel de sus conocimientos técnicos de nuevos diseños de procesos basándose en la intuición de la experiencia práctica. Su amplio conocimiento, sin embargo, no era lo suficiente para abarcar los nuevos materiales de alta resistencia y de ultra-alta resistencia que aparecen continuamente en el mercado. Hace seis años, el acero fabricado por Ford de mayor resistencia era todavía de 600 MPa. Hoy en día este valor es 600 a 780 MPa en muchas piezas. Ford ya ha ganado algo de experiencia en la producción y ésta se ha integrado a su vez, y en cierta medida, en los nuevos cálculos FEM.
El valor de las soluciones de software que Ford utiliza desde hace años está creciendo. Sin embargo la aceptación de su uso en la fabricación de herramientas no fue inmediata tardando, según Bernd Krömer, entre dos y tres años. Unos resultados prácticamente iguales entre la simulación del proceso completo y la producción real de la pieza, ofrecían los argumentos más convincentes cuando, por ejemplo, la tendencia de arrugas de la pieza embutida y la de la pieza calculada se mostraban exactamente de la misma forma. Esta tan alta correlación entre las piezas reales embutidas y las previamente calculadas con el programa, es una de las principales razones por las que ahora Bernd Krömer no puede imaginar trabajar sin el software AutoForm.
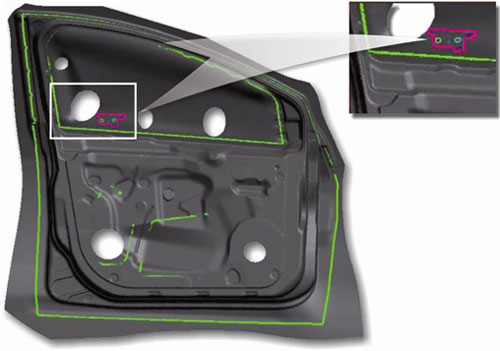