Engel en JEC: Pabellón 5, Stand N79
Proceso termoplástico integrado para reducir los costes unitarios de los pesos ligeros de material compuesto
Con sus muchos años de experiencia en el moldeo por inyección y sus conocimientos en automatización, Engel desarrolla conceptos de producción altamente rentables para la fabricación de piezas de material compuesto en grandes cantidades. En la feria JEC World 2023, que se celebrará del 25 al 27 de abril en París, el fabricante de máquinas austríaco demostrará cómo se puede combinar una alta eficiencia de producción y rentabilidad con la sostenibilidad, tanto para la industria aeroespacial como para la automovilística.
En el proceso Engel organomelt, las preformas de compuestos de fibra termoplástica –por ejemplo, láminas termoplásticas y cintas UD– se conforman y funcionalizan en un único paso integrado. Por ejemplo, las nervaduras de refuerzo o los elementos de ensamblaje se moldean inmediatamente en el mismo molde tras el termoformado utilizando un termoplástico del mismo grupo de materiales de matriz que la lámina termoplástica. Esto no sólo permite un proceso de producción altamente eficiente y totalmente automatizado, sino que también contribuye a la economía circular. El enfoque monomaterial termoplástico consecuente facilita el posterior reciclaje de las piezas.
En su stand de la feria, Engel, firma representada por Roegele, muestra el gran potencial de la tecnología ligera organomelt con una exposición de máquinas en directo. Una máquina de inyección Engel victory 660/160 y un robot articulado Engel easix se están utilizando para automatizar la producción de aletas de inspección para el fuselaje de aviones de pasajeros. La célula de producción también incluye un horno IR, que también procede del desarrollo y la producción propios de Engel.
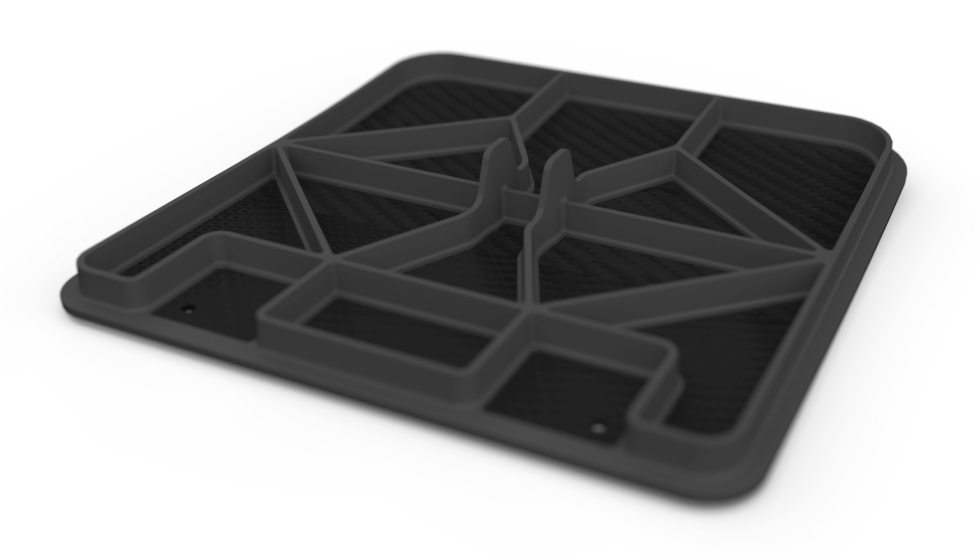
La alternativa termoplástica sostenible y rentable a la anterior solución termoestable con piezas de aluminio fresadas atornilladas: en la JEC World 2023, Engel produce flaps de inspección para aviones de pasajeros mediante el proceso Enge organomelt. (Imagen: Engel).
Para mostrar la amplia gama de aplicaciones tanto en el sector aeroespacial como en el de la automoción, durante los tres días de la feria se transformarán alternativamente dos sistemas de materiales diferentes. Por un lado, se están sobremoldean planchas termoplásticas con una matriz de PEEK, mientras que, por otro, se están procesan planchas termoplásticas basadas en PPA en combinación con PPA.
Las planchas termoplásticas se calientan en el horno IR, se introducen en el molde mediante el robot, se conforman en el molde y se sobremoldean inmediatamente. Se forman los nervios de refuerzo y un clip de montaje.
El calentamiento de la plancha de termoplástico es un paso del proceso que determina la duración del ciclo y también es relevante para la calidad. El grosor de la preforma define los tiempos de calentamiento y enfriamiento. Calentar el material rápidamente sin dañarlo es importante, al igual que los trayectos cortos para transportar la lámina termoplástica calentada hasta el molde, para evitar que la lámina vuelva a enfriarse de camino al molde y pierda su maleabilidad. Aquí es donde la tecnología sin columnas de la máquina victory juega a su favor. El acceso sin barreras a la zona del molde permite colocar el horno IR muy cerca del molde. Además, el robot puede tomar el camino más corto hasta el molde sin tener que rodear los contornos de interferencia. Ambos factores aceleran la manipulación en caliente y garantizan la consistencia del proceso y la alta calidad de los componentes.
En las soluciones integradas de Engel system, el robot y el horno IR están integrados en la unidad de control CC300 de la máquina de inyección. Esto permite manejar todo el proceso de forma centralizada a través de la pantalla de la máquina. Otra ventaja es que la inyectora, el robot y el horno IR acceden a la misma base de datos y coordinan con precisión sus secuencias de movimiento entre sí. Esto reduce el tiempo de ciclo en muchas aplicaciones.
Gran potencial en todos los ámbitos de la movilidad
Desarrollado para una producción eficiente a gran escala, el proceso Engel organomelt se ha establecido rápidamente en la industria automovilística, pero también está despertando un gran interés en otros sectores. “Cada vez recibimos más consultas de la industria aeroespacial”, informa Christian Wolfsberger, business development manager Composite Technologies de Engel. “En la industria aeroespacial, los materiales termoestables están siendo sustituidos cada vez más por termoplásticos”. Los motores de esta evolución son la presión de los costes y los objetivos de sostenibilidad. El uso consecuente de materiales termoplásticos permite un alto grado de integración del proceso para garantizar una funcionalización de las piezas totalmente libre de preocupaciones; esto, a su vez, reduce el tiempo empleado, el insumo de materias primas y los requisitos energéticos.
Donde normalmente se requieren diferentes sistemas de materiales y varios pasos de producción independientes, Engel organomelt sólo necesita una única célula de producción integrada. Las aletas de inspección para el fuselaje de los aviones son el mejor ejemplo de ello. Hasta ahora se fabricaban como piezas sándwich termoestables con piezas fresadas de aluminio atornilladas.
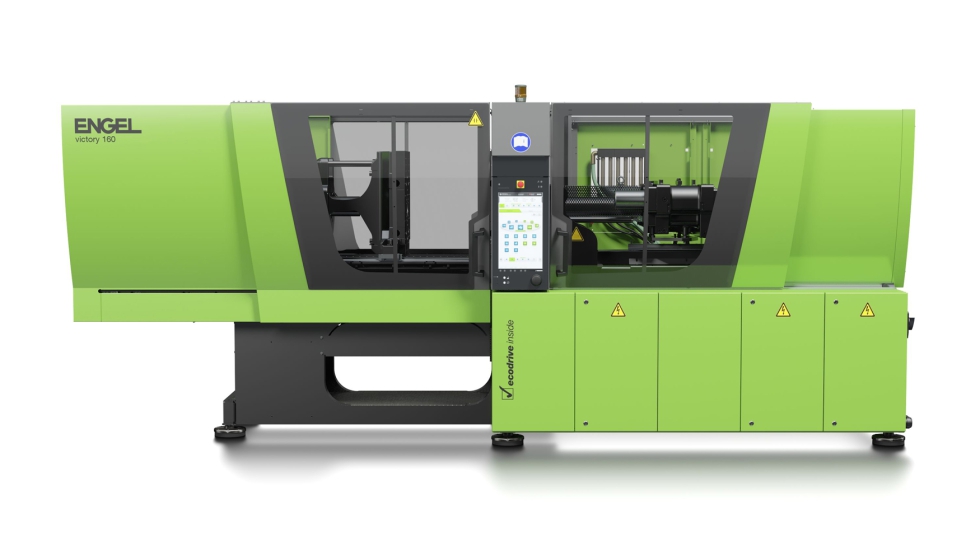
La integración del proceso es clave para reducir los costes de producción. La lámina termoplástica calentada se forma en la máquina de moldeo por inyección e inmediatamente se sobremoldea para crear los elementos de refuerzo y funcionales. (Imagen: Engel).
Reducir las emisiones de CO2 es un objetivo declarado de la industria aeronáutica, además de mejorar la rentabilidad. Un avión emite la mayor cantidad de CO2 durante su vida útil mientras está en el aire. Esto hace que el apalancamiento de tecnologías innovadoras de construcción ligera sea correspondientemente alto, especialmente si estas tecnologías también pueden ayudar a cerrar el ciclo de materiales al final de la vida útil de la pieza, y este es el caso del proceso Engel organomelt, que produce piezas puramente termoplásticas.
Engel ve un enorme potencial para el proceso organomelt en la producción aeronáutica. Las cantidades necesarias de elementos estructurales y piezas para la cabina de pasajeros aumentan continuamente. En todo el mundo se abren otras posibilidades en los ámbitos de la movilidad aérea urbana, que incluye las cabinas aéreas, y de la logística, donde se utilizan cada vez más drones de transporte.
Engel mostrará la producción de las aletas de inspección en JEC World 2023 en cooperación con su cliente FACC (Ried im Innkreis, Austria). Los otros socios del proyecto son Ensinger (Nufringen, Alemania), Victrex (Lancashire, Gran Bretaña) y Kuraray (Hattersheim am Main, Alemania) para las materias primas y Neue Materialien Fürth en Alemania para el diseño y simulación de piezas.
Otra empresa asociada expondrá en su propio Expert Corner en el stand de Engel. Voidsy, con sede en Wels (Austria), presenta un sistema ultracompacto para la comprobación sin contacto y no destructiva de materiales y componentes mediante termografía activa.
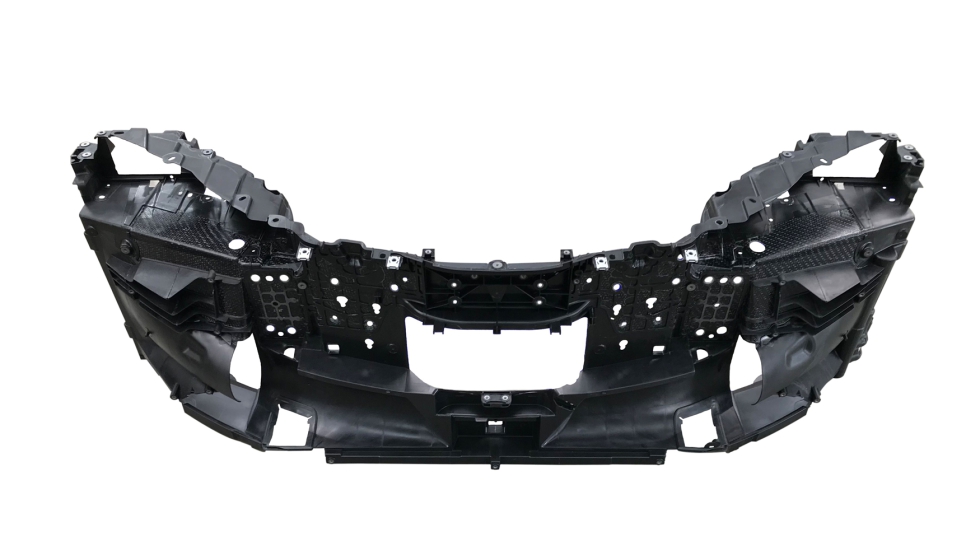
Producido mediante el proceso Engel organomelt: portamódulos frontal para los nuevos vehículos eléctricos 'Air' de Lucid Motors. (Foto: Elring Klinger)
Reducción de los costes de montaje y mano de obra
Otro Expert Corner está dedicado a las aplicaciones de automoción con Engel organomelt. Entre otras cosas, se muestra el portamódulos frontal de Lucid Motors, galardonado con el SPE Award. La producción en serie de esta pieza corre a cargo de la empresa ElringKlinger, con sede en Dettingen an der Erms (Alemania), y se basa en el procedimiento Engel organomelt. En función del tipo de vehículo, el portamódulos frontal sirve de soporte para el refrigerador del aire de sobrealimentación, los módulos de faros, el depósito de agua de lavado, la bocina, el módulo de radar de distancia o la toma de aire. También sirve de soporte para el capó mediante cierres de capó adicionales.
ElringKlinger ha logrado minimizar tanto el número de pasos previos y posteriores al mecanizado como los costes, a pesar de contar con un total de 37 insertos. El altísimo nivel de integración funcional en el proceso de moldeo por inyección se traduce en una menor sobrecarga de montaje, lo que, a su vez, reduce los costes de mano de obra. El portamódulos frontal se utiliza en el “Air”, el primer modelo de vehículo eléctrico del fabricante de automóviles estadounidense Lucid Motors.