Automatización de una planta de poliamida
Emilio Fernández
Siemens15/09/2002
Siemens15/09/2002
Siemens Controlmatic se ha encargado de la automatización completa de la nueva planta de poliamida que Nurel ha abierto en Zaragoza. Para ello, Siemens ha optado por el concepto de automatización totalmente integrada y ha optado por un sistema totalmente descentralizado que transmisión y captación de datos.
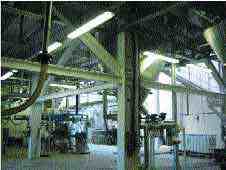
Vista de la nueva planta de Poliamida PA-6 en la fábrica de Nurel en Zaragoza
En la factoría que la empresa Nurel tiene en Zaragoza se ha construido una nueva planta de producción continua de poliamida PA-6, termoplástico industrial semicristalino de color blanco que técnicamente se llama policaprolactama y comercialmente nylon.
La poliamida PA-6 producida en Nurel se utiliza casi exclusivamente para la fabricación de diversos tejidos sintéticos. Esta nueva planta dispone de dos líneas de producción cada una con una capacidad de 23t/día de chips de PA-6.
Existen también otras unidades auxiliares y de preparación de aditivos que alimentan a las dos líneas de fabricación principales y que se encuentran localizadas en un edificio independiente.
La planta ha sido construida “llave en mano” por la ingeniería suiza EMS Inventa-Fischer y la puesta en marcha se ha realizado en abril de este año.
La automatización del proceso ha sido realizada por Siemens Controlmatic desde Barcelona y las líneas de transporte por Elinar empresa de ingeniería y servicios ubicada en Zaragoza.
Para la automatización de esta nueva planta se ha utilizado el concepto "Automatización totalmente integrada" de Siemens con el Sistema de Control Distribuido Simatic PCS7 como núcleo de la configuración de control global de la nueva planta. El concepto de automatización del proceso y del transporte de material se refleja en el diagrama adjunto (esquema 1).
La poliamida PA-6 producida en Nurel se utiliza casi exclusivamente para la fabricación de diversos tejidos sintéticos. Esta nueva planta dispone de dos líneas de producción cada una con una capacidad de 23t/día de chips de PA-6.
Existen también otras unidades auxiliares y de preparación de aditivos que alimentan a las dos líneas de fabricación principales y que se encuentran localizadas en un edificio independiente.
La planta ha sido construida “llave en mano” por la ingeniería suiza EMS Inventa-Fischer y la puesta en marcha se ha realizado en abril de este año.
La automatización del proceso ha sido realizada por Siemens Controlmatic desde Barcelona y las líneas de transporte por Elinar empresa de ingeniería y servicios ubicada en Zaragoza.
Para la automatización de esta nueva planta se ha utilizado el concepto "Automatización totalmente integrada" de Siemens con el Sistema de Control Distribuido Simatic PCS7 como núcleo de la configuración de control global de la nueva planta. El concepto de automatización del proceso y del transporte de material se refleja en el diagrama adjunto (esquema 1).
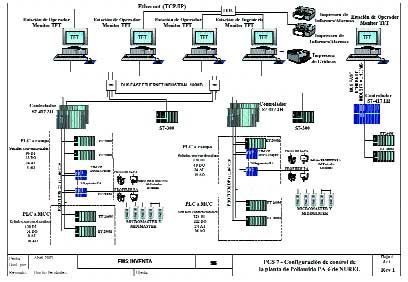
En él podemos ver el diseño cien por cien redundante tanto para las estaciones de operación como para los controladores de proceso y los buses de comunicaciones. En esta planta se ha utilizado con éxito el concepto de buses de campo:
Se utiliza Profibus DP redundante para la conexión descentralizada de las señales de E/S de campo y Profibus PA para conectar la instrumentación de proceso (transmisores de presión, caudal, nivel y temperatura…) y los posicionadores electroneumáticos para las válvulas de control.
Existen igualmente variadores de velocidad conectados al sistema de control a través del bus DP.
Con este procedimiento se optimiza la instalación e interconexión de los dispositivos de campo ya que las tarjetas de adquisición de información se instalan descentralizadamente en la planta en áreas cercanas al propio proceso y los trasmisores de campo que funcionan con tecnología de transmisión de información digital se conectan al Sistema de Control a través de un cable de bus.
Existen algunas señales de control muy críticas que requieren una alta velocidad de procesamiento y respuesta por parte del Sistema de Control cuya adquisición se realiza mediante instrumentos analógicos cableados directamente a entradas y señales analógicas.
El bus del sistema que interconecta los controladores de proceso con las estaciones de ingeniería y operación es del tipo Fast Ethernet Industrial trabajando a 100MB y utiliza la tecnología de “switches” configurados en redundancia que permite filtrar y optimizar las comunicaciones entre los controladores y las estaciones de operación.
Para el control del proceso se utilizan dos controladores del tipo AS417-2H que tienen redundancia total tanto de fuente de alimentación como de CPU y de procesadores de comunicaciones.
El sistema de transporte está controlado por otro controlador AS417-1H.
En la sala de control se encuentran dispuestas para el control del proceso cuatro estaciones de operación de las cuales una es también estación de ingeniería que centraliza todos los elementos que integran el control de la planta. Las cuatro estaciones disponibles permiten la visualización y operación de la planta completa. Cada una de ellas tiene la misma base de datos de la aplicación y realiza las mismas funciones de almacenamiento de datos, registro histórico de variables e informes de planta con lo que se evita la posibilidad de pérdida de datos.
El sistema de transporte se visualiza y maneja desde un puesto de control adicional.
También existen dos PLC que controlan las máquinas cortadoras suministradas como paquete y que se han conectado a la red Ethernet para poder así visualizar fácilmente la información de estos equipos desde las estaciones de la sala de control.
Empresas o entidades relacionadas
Siemens, S.A. - Smart Infrastructure