CT Ingenieros, Titania y Eurecat estudiarán cómo aumentar y optimizar la fabricación de materiales compuestos
CT Ingenieros, Titania y el centro tecnológico Eurecat trabajan en un proyecto de I+D sobre pultrusión de materiales compuestos. El proyecto, denominado Pultrubeam, pretende mejorar la tecnología de pultrusión para la fabricación en forma continua y fuera de autoclave. Este método debe permitir conseguir una óptima cadena de producción para fabricar piezas de material compuesto (fibra de carbono o fibra de vidrio) disminuyendo el coste y, en consecuencia, aumentar el uso de materiales compuestos en estructuras aeronáuticas, ferroviarias y automovilísticas. José Manuel Bayo (JMB), responsable del proyecto Pultrubeam e ingeniero sénior en CT Ingenieros; Miguel A. Rodríguez (MAR) director de Titania; y María Eugenia Rodríguez (MER), directora de la Unidad de Composites de Eurecat, nos dan más detalles del proyectos.
De entrada, ¿podrían explicarnos brevemente en qué consiste en proyecto y cuáles son los objetivos?
José Manuel Bayo (JMB): CT Ingenieros lidera el proyecto de innovación Pultrubeam que consiste en el desarrollo y optimización del proceso de fabricación de pultrusión de elementos para componentes aeronáuticos. La principal característica del proyecto reside en el proceso de fabricación y en el material compuesto utilizado. Con este proyecto atacamos el proceso de fabricación tanto de materiales como de procesos desde la técnica de pultrusión. Tradicionalmente, los procesos de fabricación de piezas de material compuesto en aeronáutica necesitan de un autoclave para poder transformar la fibra y el polímero en un material con las propiedades mecánicas necesarias, aplicando presión y temperatura. Esta operación hace que el método de fabricación sea discontinuo, incrementándose los costes, el uso de materiales auxiliares, utillaje y el consumo energético. La pultrusión es un proceso continuo que no depende de un autoclave. Por tanto, este proyecto permitirá simplificar el proceso de fabricación y optimizará la cadena de producción.
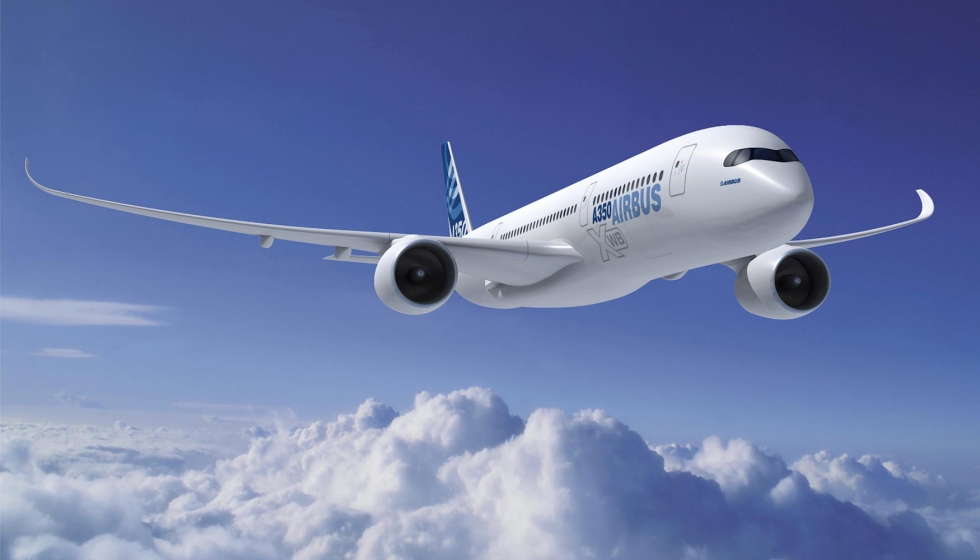
Pultrubeam incide el proceso de fabricación desde la técnica de pultrusión, simplificando el proceso y optimizando la cadena de producción al ser un método en continuo y no requerir de paros.
María Eugenia Rodríguez (MER): El proyecto Pultrubeam tiene por objetivo madurar la tecnología de pultrusión, para la fabricación de forma continua y fuera de autoclave de perfiles estructurales en material compuesto. Pultrubeam busca incrementar el conocimiento de este proceso de fabricación para su aplicación en sectores como el aeronáutico, la automoción y el ferroviario, entre otros. Actualmente, existen diversas geometrías de piezas y seguirán existiendo en nuevos programas, con dos características adecuadas para la pultrusión, ya que se trata de perfiles con diversas longitudes y que tienen secciones transversales complejas.
¿Pueden detallarnos en qué consiste la técnica de la pultrusión? ¿En qué otros procesos se utiliza?
JMB: Tradicionalmente, la técnica de pultrusión se ha utilizado en la fabricación de perfiles de plásticos reforzados con fibra de vidrio, donde está muy desarrollada. Sin embargo, en otros materiales compuestos está aún en fase de investigación. La pultrusión consiste en tirar del material en bruto, haciéndolo pasar por una matriz que le da forma mediante la aplicación de presión y temperatura. De esta forma se consigue que, cuando el material sale de la cadena de producción continua, se encuentre ya curado, obteniéndose un producto similar o de mejores propiedades al generado mediante autoclave.
MER: La pultrusión es un proceso de fabricación que permite obtener piezas de forma continua. Al ser un proceso continuo y especialmente diseñado para altos volúmenes de producción, permite desarrollar perfiles económicamente muy rentables con respecto a otros procesos de fabricación de composites. Básicamente, consiste en tirar de los refuerzos impregnados con resina, a través de un molde a alta temperatura, de manera que se produce el curado de la resina en su interior y se obtienen perfiles de sección constante con la geometría del molde.
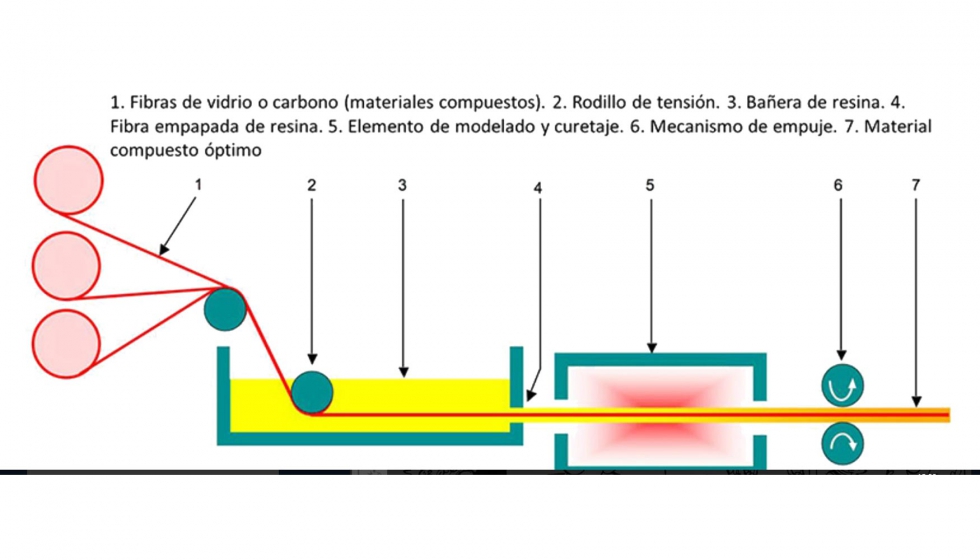
La pultrusión permite ahorrar energía y costes al no usar autoclave, reducir el espacio necesario y optimizar la producción.
El proyecto Pultrubeam tendrá una duración de 3 años. ¿En qué fase se encuentra actualmente? ¿Cuáles son los pasos a seguir en los próximos meses?
Miguel A. Rodríguez (MAR): La pultrusión como proceso novedoso se encuentra en un estado donde se requiere el estudio de las propiedades que se obtienen de la combinación de usar un nuevo proceso con nuevos materiales. En este sentido Titania, como especialista en Materiales y Procesos para el sector aeronáutico, desarrollará el protocolo de caracterización adecuado que permita determinar las propiedades críticas de las piezas que se obtienen por este proceso y su grado de cumplimiento con las expectativas del sector aeronáutico. Es decir, el conocimiento que ha acumulado Titania durante su trayectoria en el sector aeronáutico trabajando en la calidad de elementos que se procesan en la industria mediante procesos de curado clásicos como autoclave o RTM, se utilizará para establecer los valores de referencia que permitan determinar la viabilidad técnica de su sustitución por el proceso de Pultrusión, lo cual conllevaría todas las ventajas que se acaban de comentar.
JMB: Actualmente estamos en la fase de puesta a punto de fabricación y el abordaje tanto de los materiales como de la producción.
MER: En Eurecat tenemos una amplia experiencia en transformación de composites. Esto nos ha permitido plantear este proyecto tan ambicioso del que no partimos de cero, si bien tenemos un largo recorrido por delante. Durante los tres primeros meses, nos centraremos en la planificación detallada de las actividades de ingeniería.
Entrando más en detalle, uno de los beneficios que apuntan es la reducción de costes en la producción de composites. ¿Cuál es el proceso actual para obtener materiales compuestos y qué diferencias supone este proyecto?
JMB: El proceso de pultrusión es totalmente continuo y evita procesos intermedios asociados al autoclave o el encintado automático por nombrar algún ejemplo. Estos procesos intermedios suelen requerir de materiales que sustenten los procesos e infraestructuras. En la pultrusión se evita alterar accidentalmente la materia prima antes de su entrada en la cadena de producción. La pultrusión permite ahorrar energía y costes al no usar autoclave, reducir el espacio necesario y optimizar la producción.
MER: Actualmente, existen muchos procesos para la fabricación de piezas en material compuesto. La elección de uno u otro dependerá del tamaño, geometría, requerimientos, etc. Es importante subrayar que no con todos los procesos podemos fabricar las mismas piezas. Existen procesos manuales para piezas con bajas necesidades mecánicas o procesos más automáticos cuando se busca productividad y piezas estructurales. Las ventajas principales de la pultrusión con respecto a la mayoría de los procesos de fabricación en composites son, por una parte, la productividad, ya que es un proceso que trabaja en continuo y automático, y que el perfil obtenido no suele requerir de procesos posteriores.
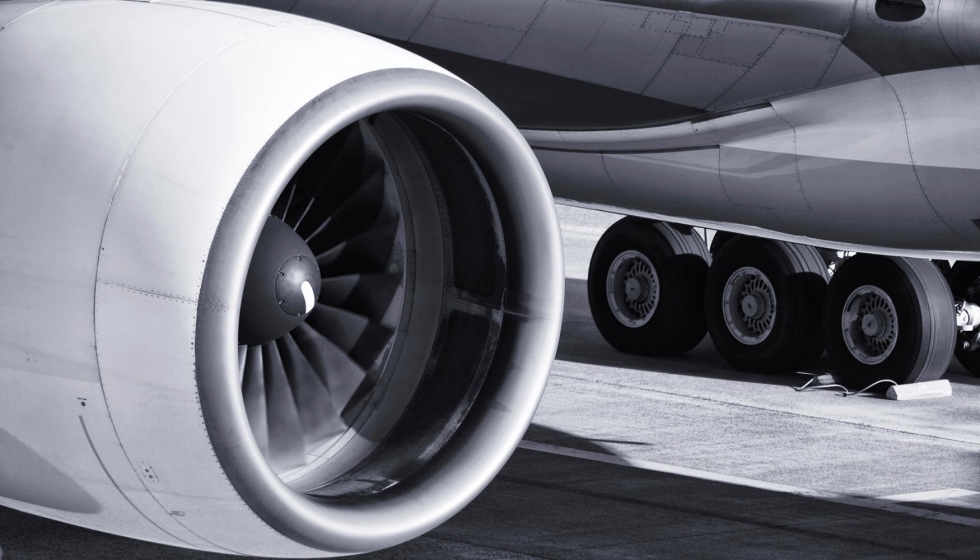
Actualmente, ¿cuáles son los materiales compuestos más habituales? Simplificar el proceso de obtención… ¿permitiría obtener otros composites?
JMB: Composites o materiales compuestos hay muchos. Pultrubeam se centra en los composites que aportan soluciones para las necesidades del sector aeronáutico.
MER: Los materiales compuestos dependen mucho del sector y de los requerimientos de la aplicación. Actualmente, se pueden encontrar matrices termoestables (poliésteres, epoxi o fenólicas) y matrices termoplásticas (polipropilenos, poliamidas, Polieteretercetona, etc.) combinadas con fibras y tejidos de vidrio, kevlar, carbono, fibras termoplásticas e incluso fibras naturales.
Pensando en sus aplicaciones, ¿qué sectores serían los más beneficiados de este nuevo sistema de producción? ¿Qué beneficios les reportaría en cada caso?
JMB: Queremos que este proyecto innovador tenga utilidad en la industria aeronáutica. Los beneficios asociados podemos enfocarlos en la mejora de las propiedades de los materiales y en la simplificación del proceso de fabricación.
MER: Los sectores más beneficiados serían la aeronáutica y el sector de la automoción e incluso el ferroviario. Del proyecto Pultrubeam queremos que tenga utilidad para estos sectores tan competitivos porque las piezas cumplirán los requerimientos de calidad.
En 2018 cuando finalice el proyecto, ¿cuáles son los resultados esperados?
JMB: Cuando termine el proyecto queremos haber conseguido la validación a nivel de planta piloto (laboratorio) del proceso de fabricación mediante pultrusión y la obtención de una pieza de material compuesto.
MER: El objetivo de Pultrubeam quiere avanzar en la tecnología de pultrusión y que tenga aplicabilidad en el sector aeronáutico, ferroviario y el vehículo eléctrico.
Como empresa dedicada a proporcionar servicios de ingeniería, ¿qué aporta CT Ingenieros al proyecto?
José Manuel Bayo, responsable del proyecto Pultrubeam e ingeniero sénior en CT Ingenieros: "CT Ingenieros lidera Pultrubeam y aporta el conocimiento de la industria aeronáutica, la experiencia en el análisis y diseño integral de componentes aeronáuticos y a nivel de materiales incorporando nuevos usos y funcionalidades. Como líderes del proyecto Pultrubeam en todas sus fases (fase de preparación, metodológica, de puesta a punto de laboratorio, de desarrollo y de validación) aportaremos todo nuestra trayectoria y experiencia en el diseño de estructuras así como en la definición, diseño y control del proceso de fabricación durante el proceso de pultrusión".
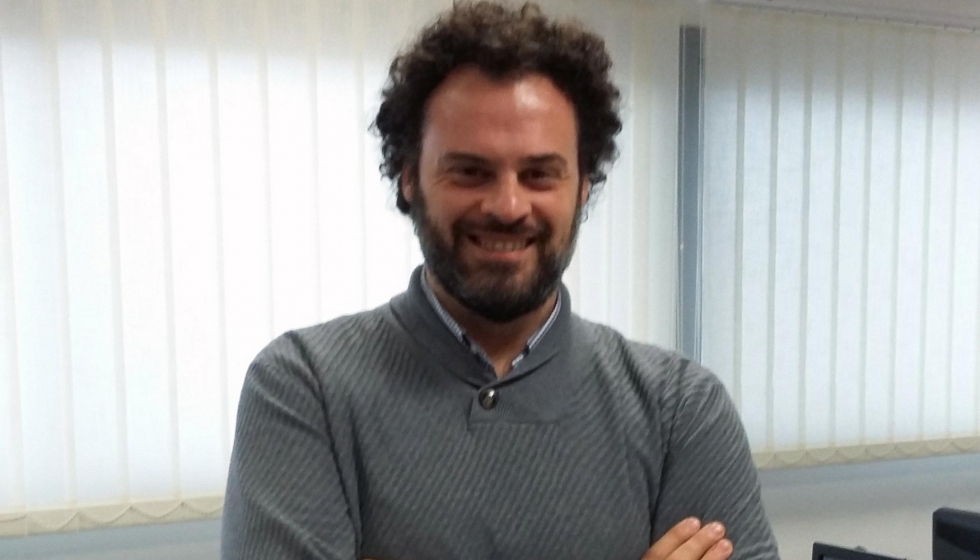
José Manuel Bayo, responsable del proyecto Pultrubeam e ingeniero sénior en CT Ingenieros.
Como empresa especialista en los ensayos y tests para la industria, ¿cuál es el cometido de Titania en el proyecto?
Miguel A. Rodríguez, director de Titania: "Titania es responsable en Pultrubeam de la evaluación de la calidad de las fabricaciones realizadas por el proceso de Pultrusión. Para ello diseñará y ejecutará un plan de ensayos que evalúe las propiedades físicas, mecánicas y microestructurales de los nuevos materiales elegidos para este proceso fuera de autoclave. Además, integrará en su centro de I+D de fabricación en Composite, las piezas pultrusionadas para abordar desarrollos posteriores. El proyecto Pultrubeam se suma a la cartera de proyectos de I+D (Apolo, Air-Union o Sealant) que realiza Titania relacionados con nuevos desarrollos en fabricación en materiales compuestos dentro de nuestra estrategia de dar soporte a la industria en sus procesos especiales críticos".
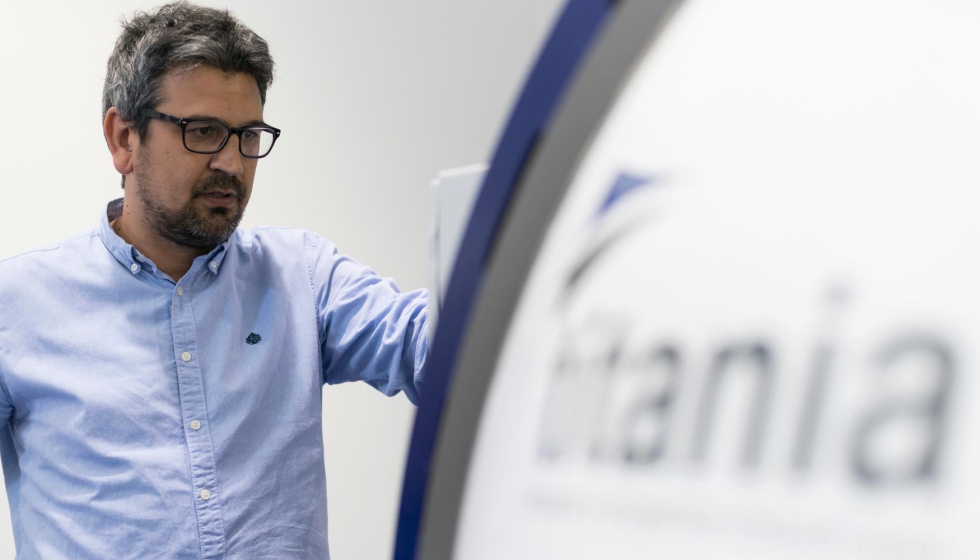
Miguel A. Rodríguez, director de Titania.
Como centro tecnológico, ¿cuál es el trabajo que realizará Eurecat dentro del proyecto Pultrubeam?
María Eugenia Rodríguez, directora de la Unidad de Composites de Eurecat: "En el caso de Eurecat, es fundamental el conocimiento que aporta, además del equipamiento que ha generado mediante su participación y su liderazgo en varios proyectos centrados en este proceso de pultrusión como Industrusió e Hypermembrane para mejorar el proceso de pultrusión termoplástica o para la producción de perfiles ondulados respectivamente".
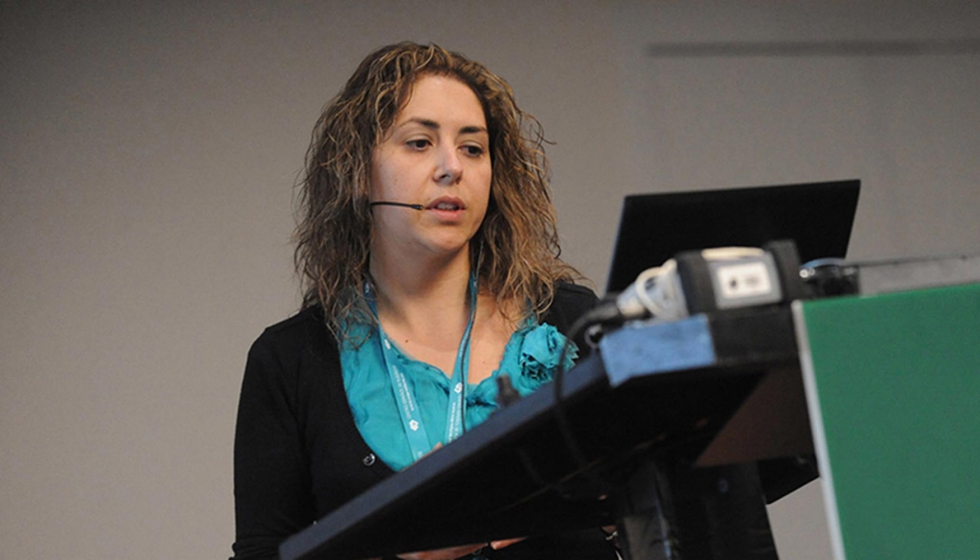